5S is a lean manufacturing methodology designed to optimize workplace organization and efficiency. It helps manufacturers create clean, organized work environments that minimize waste and maximize productivity. In a well-run factory, everything is arranged logically, workstations are tidy, and tools are easily accessible.
As a structured five-step process for sorting, organizing, and optimizing a workspace, 5S in manufacturing ensures an efficient, obstacle-free production process that encourages operational excellence. This foundational lean tool supports broader initiatives aimed at optimizing production.
In this article, we explore what 5S is, its benefits, and how to implement it effectively.
What is 5S Methodology?

What is 5S in Manufacturing?
When introducing a culture of improvement, 5S is one of the first systems manufacturers can implement. The five steps guide you to run an organized, clean, and clutter-free workplace. If employees are working in a poor-quality environment, this can lead to poor-quality end products. 5S sets a higher standard for operations and changes their mentality and view of the factory.
It works in harmony with other lean principles like Kaizen (continuous improvement), Just-in-Time (JIT) production, value stream mapping, and methodologies like Six Sigma. By implementing 5S, organizations lay the groundwork for a culture of efficiency, safety, and continuous improvement, creating an environment where lean practices can thrive.
The Origins of 5S Methodology
Initially developed in Japan as a part of the Toyota Production System (TPS) in the 1950s. The aim was to help Toyota become more agile, removing any part of the automotive production process that led to waste and delays.
The term “5S” comes from five Japanese words — Seiri, Seiton, Seiso, Seiketsu, and Shitsuke — commonly translated into English as Sort, Set in Order, Shine, Standardize, and Sustain.
This may sound complicated, but the process is straightforward in practice. It’s important to remember that the goal is a clearer, distraction-free working environment, which is achieved by following these five steps.
The Benefits of 5S in Manufacturing
Cultural change is the most significant impact that 5S has on a working environment. It sets the standard for your entire operation and your end product. It’s the perfect way to begin your continuous improvement journey, as it’s hard to disagree with — a well-organized and clean working environment leads to more efficient production. Here are some of the benefits observed through 5S in manufacturing.
- Improved Efficiency
Organizing tools and materials reduces search time and streamlines processes. One simple solution is to install a tool holder to quickly access the most frequently used tools. A clutter-free environment reduces workers’ time spent searching for tools and materials and allows them to work faster.
- Enhanced Safety
A clean, clutter-free workplace minimizes the risks of accidents and injuries.
- Quality Improvement
Standardized practices help reduce errors and maintain consistent product quality. Additionally, problems with quality are easier to spot if the working environment is clean.
- Employee Involvement
5S promotes employee collaboration and ownership of the work environment. Creating a workspace where workers are responsible for their environment leads to higher expectations from themselves and others. In particular, when new employees join a company, they are more likely to live up to these standards if they see high standards of organizing and cleaning.
- Improved Conditions
A well-organized environment helps to create the ideal conditions for operational excellence. A cluttered environment often leads to a cluttered mind. By clearing your workspace with 5S, you can focus on the job without distractions.
When gauging the success of 5S implementation, manufacturers often look at several key metrics, including:
- Reduced lead time
- Improved inventory turnover
- Decreased accident rates
Real-time OEE Software
Gain visibility and increase your production efficiency.
How to Implement 5S in Manufacturing
Preparing for 5S Implementation
5S is often one of the first steps in the journey toward continuous improvement. To implement it successfully, keep these key tips in mind:
- Assign a person responsible
Each area should have one person responsible for overseeing the 5S project — ideally, this should not be an operator but someone who ensures that tasks are completed and standards are maintained. Based on our experience, production engineers or production managers are well-suited for this role. Operators, on the other hand, will be responsible for executing the actionable steps.
- Take photos for reference
Take photos to document the workspace before and after each step to highlight improvements. Once the ideal standard is achieved, take a final photo and place it somewhere visible. This is a visual reference for maintaining organization and can also be used during audits.
- Give it time
5S is not just a project — it’s a culture shift. Changing habits takes time; in our experience, workers usually take about a month to fully adapt. During this period, monitoring progress and reinforcing new standards is crucial to ensure long-term success.
- Involve everyone
Successful 5S implementation requires full participation from operators, managers, and leadership. Clearly assign roles and communicate expectations to ensure everyone understands their responsibilities. When employees are actively engaged, they are more likely to take ownership of the process.
Once you have prepared your team, you can start with the 5 steps.
Step 1: Seiri (Sort)
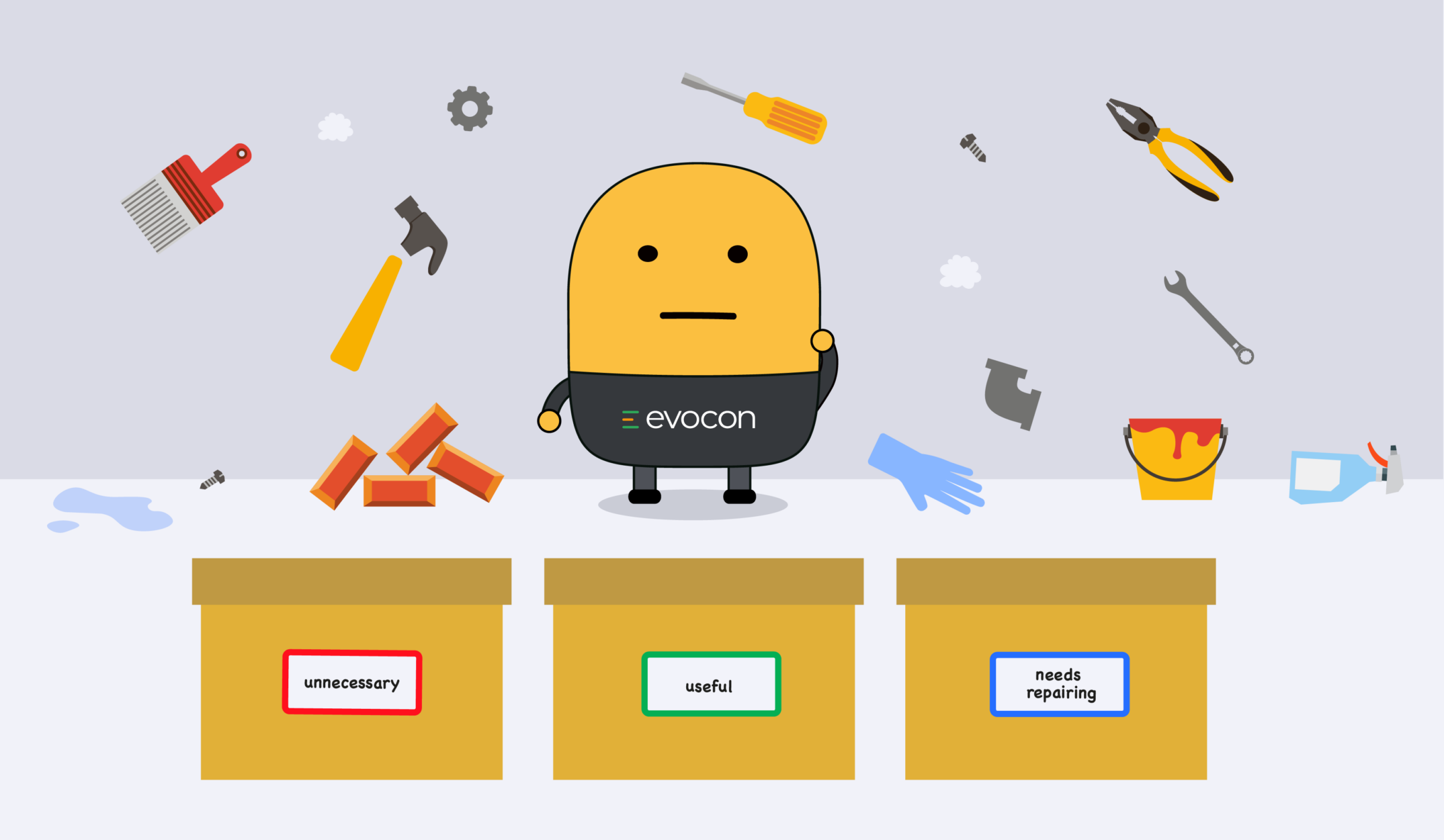
The first step of the 5S methodology focuses on eliminating unnecessary items from the workplace that are not currently needed for production. This includes old samples, scrap, and stock left lying around.
Start with a comprehensive inspection of all areas, including tools, shelves, and storage spaces. Identify and categorize items based on their necessity. For example, use colored tags:
- 🔴 Red Tag: Unnecessary items to be scrapped.
- 🟢 Green Tag: Useful materials and tools to be located in the right place.
- 🔵 Blue Tag: Materials or items to be repaired, such as electrical boxes, dismantled assemblies, and other repairable components.
Example: In a bottling plant, the team inspected their workspace and tagged items. They discarded old tools with red tags, organized essential items like spare nozzles with green tags, and set aside damaged components for repair with blue tags. Clearing out unnecessary items freed up space and improved workflow around the bottling line.
Step 2: Seiton (Set in Order)
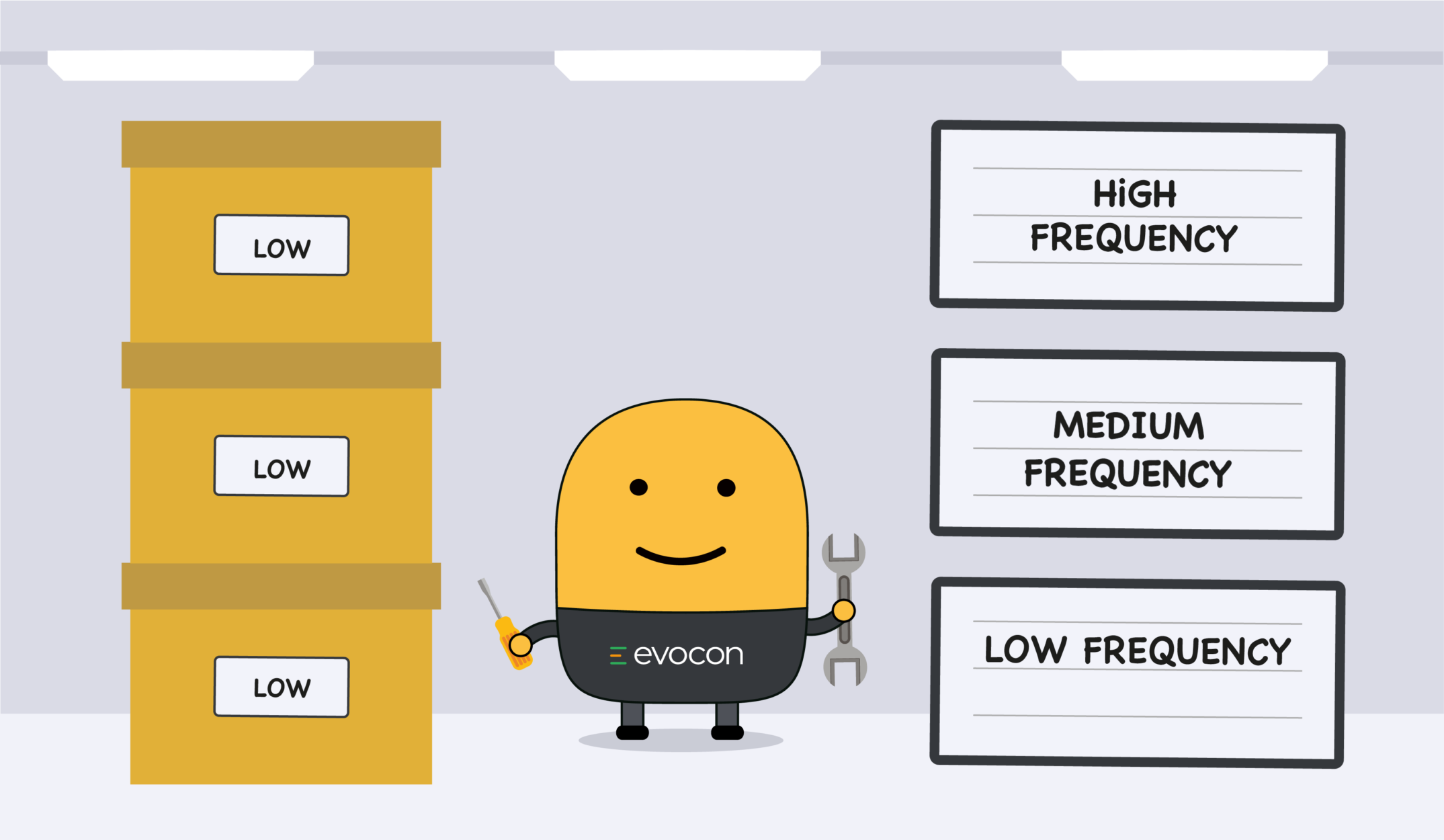
In the second step, arrange the remaining necessary items according to well-defined criteria in order to cut search time. You should classify your items by frequency of use to understand their necessity and where they will be best located. Follow these guidelines to begin organizing:
1) Classify items by frequency of use:
- For each item, you should provide a short description (key, screwdriver, etc).
- Asses the frequency of use and create a set classification criteria like this:
Frequency of use | Guidelines | |
Low | Once a month | Does not have to be close to the line |
Medium | At least once a week | Arrange within area, in an accessible location |
High | At least once a day/shift | Keep next to workstation |
2) Find a suitable location for tools, equipment, and materials:
- Put the most frequently used items next to the locations where they are needed.
- Store frequently used items at a height between your elbows and shoulders.
- Place tool holders where needed, with clearly assigned spaces for each tool.
- Put less frequently used objects elsewhere.
3) Clearly identify each location:
- Label storage areas and use color coding for quick identification.
- Place photos of an area’s appearance and where tools and equipment are kept.
- In more complex setups, assign codes to each tool and area. Keep the codes simple and easily related to respective locations:
Area | Area Code |
1st cabinet | A01 |
1st shelf of first cabinet | A0101 |
2nd cabinet | A02 |
4) Document storage locations:
Document all storage locations and items. Photos clearly demonstrating where tools should be placed can also support this. It should be easy for anyone to walk in and understand where items are kept.
You can also create a table with details for each item, including the description, frequency, location, and a unique code for easy tracking.
Object description | Frequency of use | Best stocking location | Item code | Area code |
Screw driver | High | Accessible height | C01 | A0103 |
This ensures workers can find tools and materials quickly, reducing wasted time.
Example: The team organized tools by usage. High-use items, like cleaning supplies, were placed near the bottling line, while less-used items were moved to labeled cabinets. Clear signage and color-coded zones helped workers locate tools quickly, cutting downtime during shifts.
Step 3: Seiso (Shine)
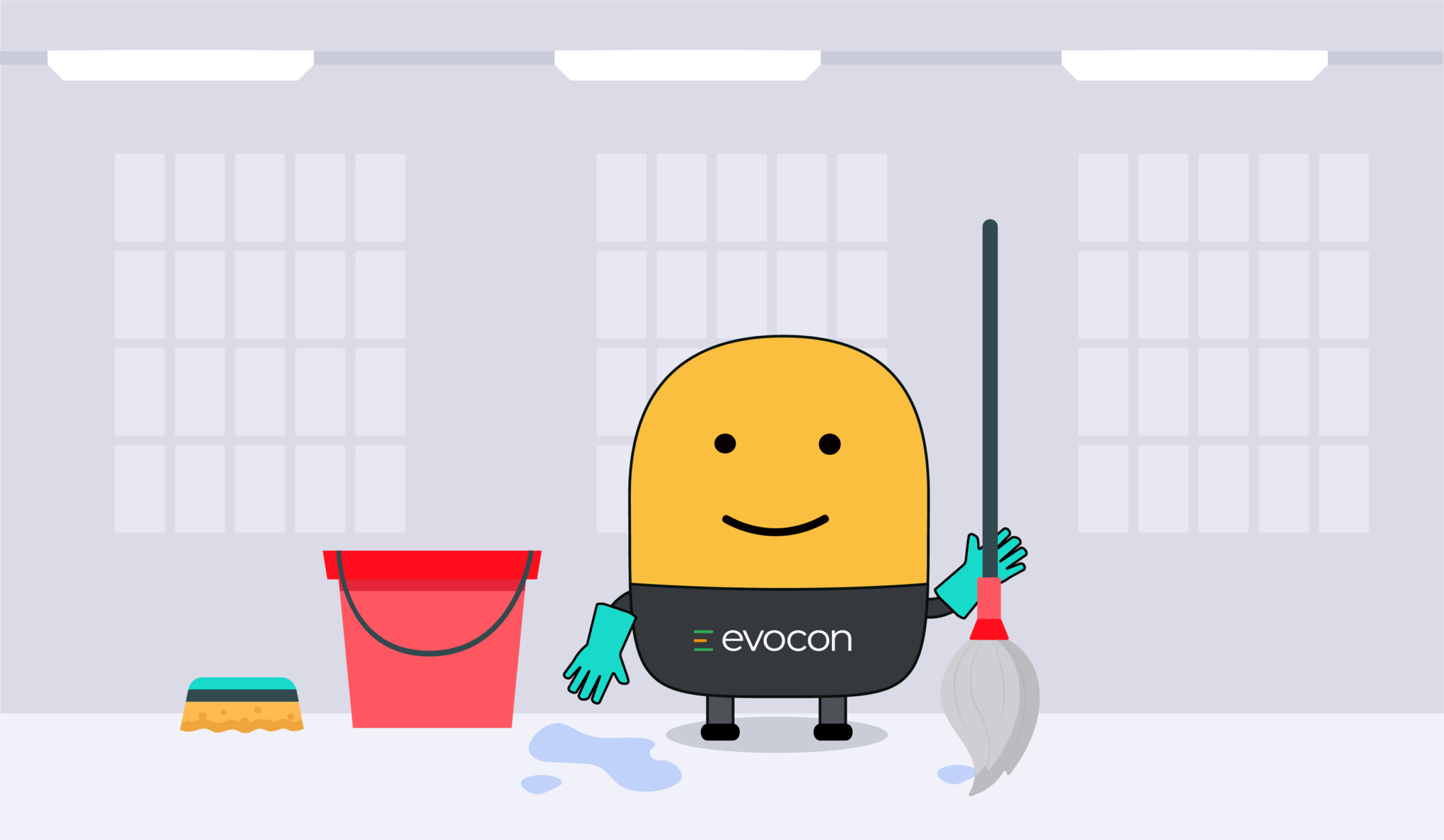
Shine focuses on cleaning the workspace and identifying potential issues. During this process, check for and record issues such as safety hazards, dirt buildup, or hard-to-clean areas. Here are the steps to shine your workspace:
- Deep Clean:
Thoroughly clean all equipment, tools, and work areas.
- Inspect While Cleaning:
Identify issues such as wear and tear, safety hazards, or areas prone to dirt buildup.
- Address Anomalies:
Document problems, assign countermeasures, and set deadlines and a person responsible for resolution.
Regular cleaning ensures the workspace stays functional and prevents minor issues from becoming more significant problems.
Example: Workers deep-cleaned the bottling line, identified buildup under conveyors, and flagged worn rollers for replacement. Residue near the filling machine was addressed with improved cleaning schedules. Regular cleaning reduced contamination risks and kept production running smoothly.
Step 4: Seiketsu (Standardize)
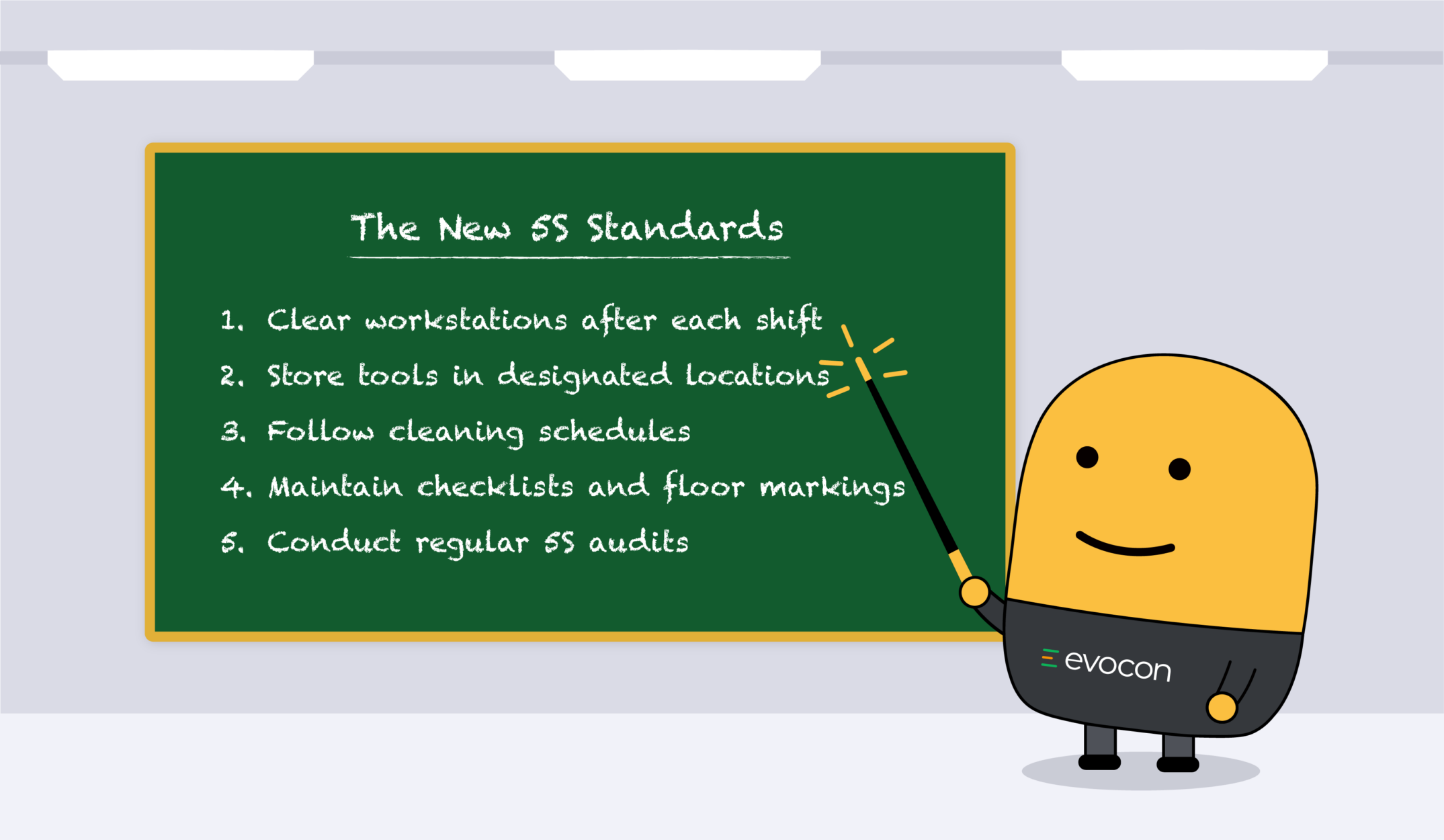
The first three steps help establish optimal working conditions. Now, the focus switches to standardizing and sustaining these levels. This is why 5S in manufacturing is so important — it sets standards to ensure the workplace is optimal for operational excellence.
The goal of step four is to define, write down, and make visible the new standard for cleaning, order, and stock levels. To do this, you will need to make sure:
- The new standards are visible and applicable.
- Anyone can see what should be done and how. Use visual management tools like photos, screens, charts, diagrams, and labeled zones.
- To monitor progress, ensure key metrics are visible (e.g., waste reduction and improved efficiency).
The key here is visibility. Clear visual tools, like checklists, help maintain order and save time.
Example: The plant implemented a checklist for daily cleaning tasks like wiping nozzles and weekly maintenance like roller checks. Diagrams showing tool storage zones were posted, and progress metrics were displayed. These standards kept everyone aligned and maintained consistency across shifts.
Step 5: Shitsuke (Sustain)
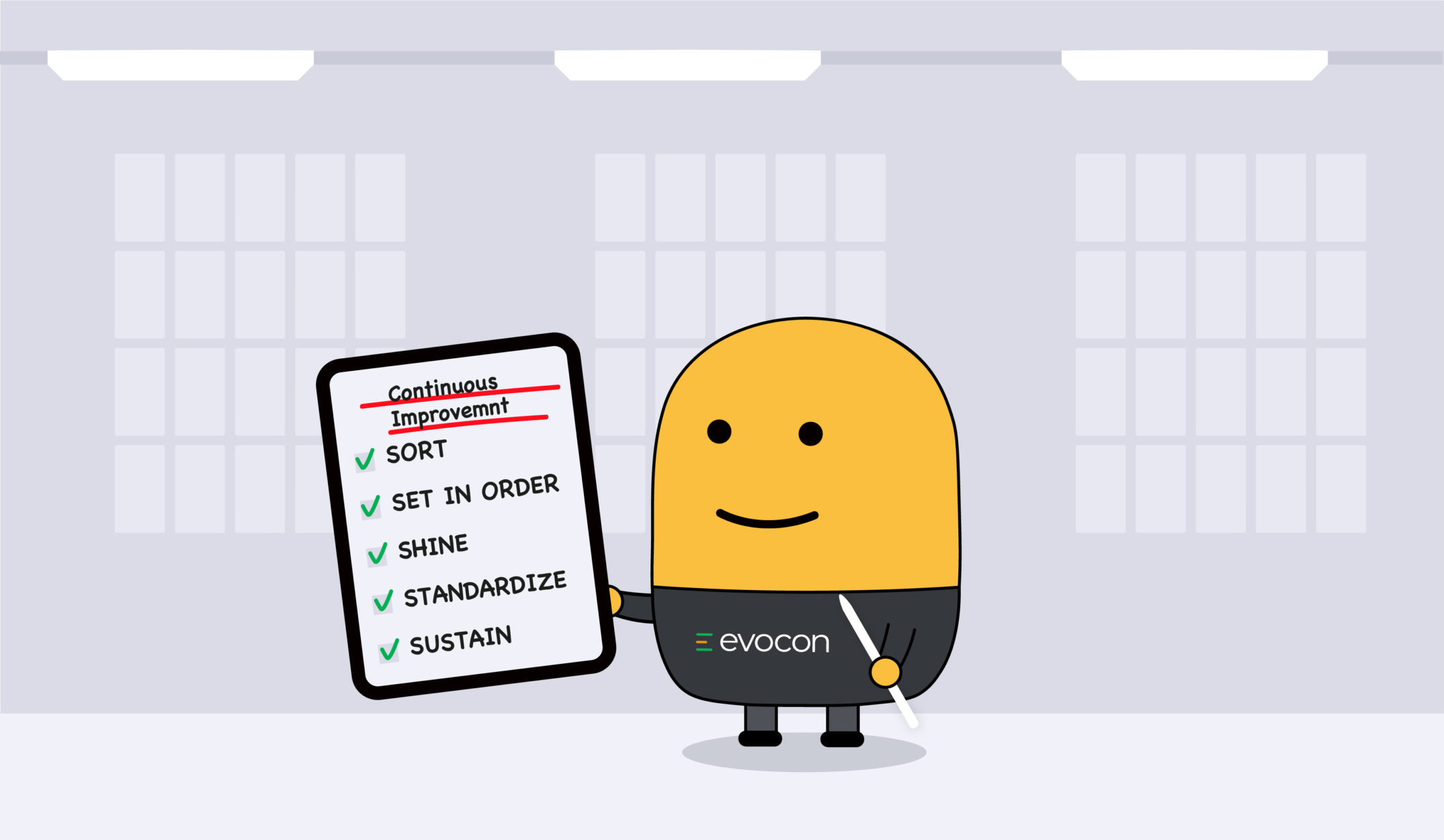
Now that the first four steps have been completed, we move on to step five, where the goal is to support continuous improvement. Here, we have four main aims:
- Make sure standards are observed.
- Highlight issues and take countermeasures.
- Restore standards.
- Standardize continuous improvement.
Leadership plays a crucial role in maintaining the standards established through 5S. This can be achieved by:
- Including 5S standards in performance reviews.
- Aligning 5S practices with KPIs.
- Holding yourself and your team accountable to sustain the organization.
Planned audits are also essential, as they ensure that the new standards are consistently followed and reviewed. Some manufacturers find it beneficial to conduct cross-team audits instead of relying solely on managers. This approach encourages knowledge-sharing and collaboration between teams.
Audits don’t have to be complicated. The person assigned can check each area using photos and a simple checklist to ensure 5S standards are maintained. In the beginning, audits should be conducted weekly to reinforce new habits. Once positive changes are seen, the frequency can be adjusted to monthly to sustain improvements.
Additionally, incorporating other elements of Kaizen, such as the PDCA (plan, do, check, act.) cycle, can help keep your organization aligned with 5S principles and on track for long-term success.
By embracing the principles of 5S continuous improvement, manufacturers can ensure their systems remain efficient and adaptable to future challenges.
Example: To maintain their progress, the company conducted monthly audits with rotating focus areas, such as removing unnecessary items or refining tool organization. Teams reviewed different areas, identified gaps, and proposed new solutions. These activities reinforced accountability, encouraged collaboration, and kept the workplace consistently organized and efficient.
Key Takeaways
The 5S lean manufacturing methodology is not just about organization — it’s a process improvement tool that helps create a culture of continuous improvement across the workplace.
Manufacturers can improve efficiency, safety, and product quality by systematically sorting, organizing, and maintaining workspaces.
The success of 5S relies on employee involvement and leadership support. Every member of the organization plays a role in sustaining these standards and working towards continuous improvement. Everyone, from the board to plant managers to operators on the floor, has a role in making its implementation and continued use successful.
To track the entire process, use a 5S audit checklist such as this one to assess the success of your implementation. Tracking the process and ensuring accountability are vital to making 5S a long-term success.