Chala SAS is one of the leading producers of fasteners and straps for bras, girdles, and other garments in the Latin-American region. In its home country of Columbia, Chala is the biggest producer of such products, supplying well-established local brands that operate globally such as Leonisa. Chala’s products also feature in American fashion producers such as Hanes.
Despite its success, Chala recognized the need to modernize its manufacturing operations and take advantage of the latest innovations to drive improvements. This case study outlines how by partnering with Evocon, Chala has realized significant improvements across many areas of its operations.
Background: Manual Processes & Missed Opportunities
Chala CEO, Werner Eberl, knew that the manufacturer could afford a number of benefits if it implemented a bespoke OEE monitoring solution. But the OEE solutions available from local suppliers still required a lot of manual input, making them non-starters for Chala.
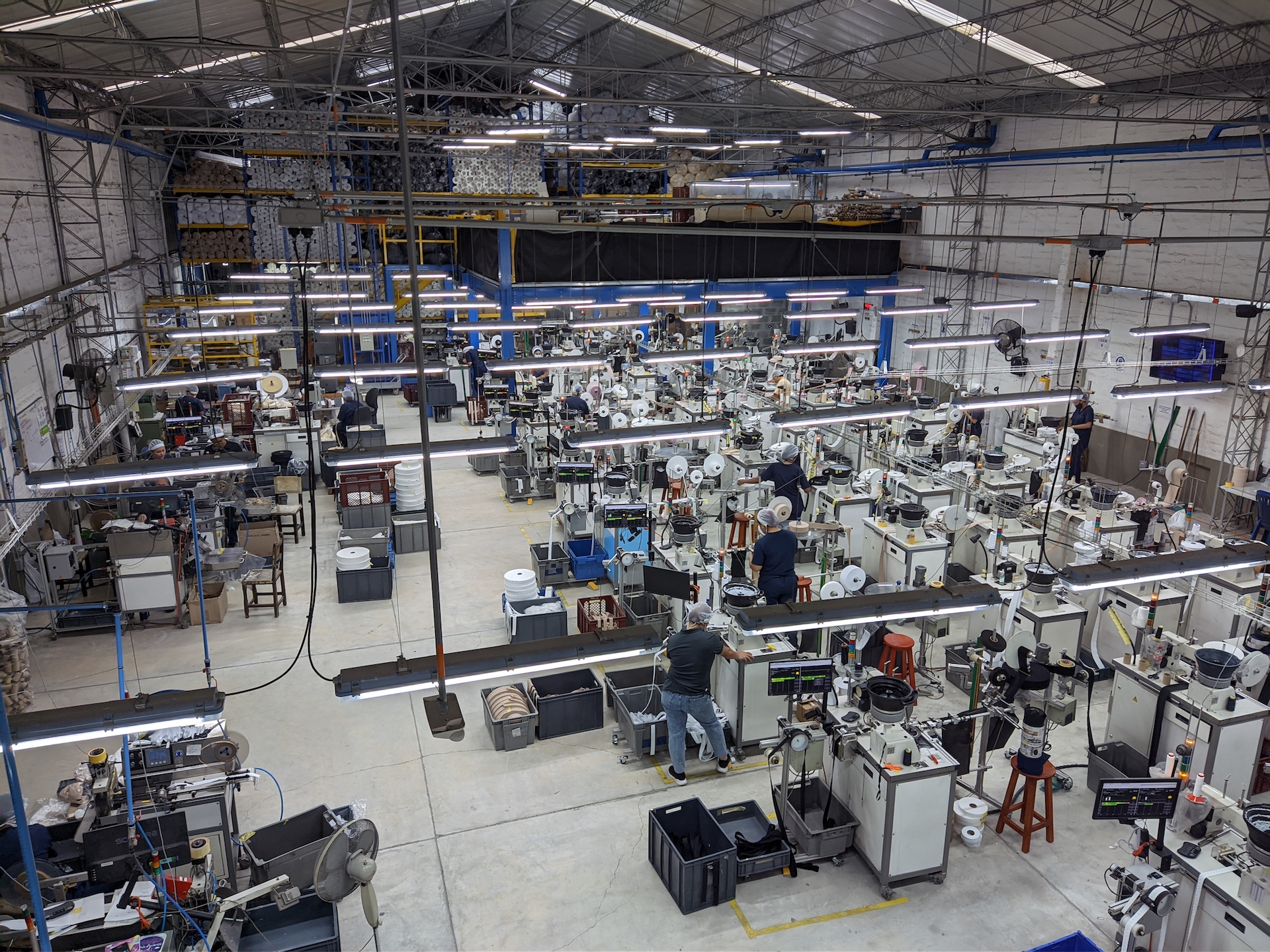
As a result, Chala continued using its traditional manual processes, which were outdated, inefficient, and inaccurate. For example, production stops were recorded on paper by a person who went from line to line. These stops were then uploaded to a spreadsheet every few hours, consuming around two hours of the individual’s time — time that would be better spent focusing on other areas.
While this process worked, it meant that issues impacting production were often discovered too late and no immediate action could be taken to fix them. Furthermore, Chala had little insight into the downtime and production processes, meaning there was no way to determine the root causes behind production goals not being met, nor identify potential improvement opportunities.
A Digital Transformation For The Better
After 20 successful years in business, Chala moved closer to embracing a new era by embarking on a digital transformation project. The first step of Chala’s journey was to partner with Evocon to implement its visual and user-friendly OEE monitoring solution. The Evocon implementation’s first goal was to record production stops in real-time, thus enabling better insights and faster decision making.
Sebastián Cardona Gómez, Continuous Improvement Manager at Chala, who joined the company at the start of its digitalization journey at the end of 2019, shares his insights.
“We need to keep the lines working at all times,” says Sebastián. “Even just a 10-minute stop is a huge loss for Chala.”
Quality At The Forefront
Another area where Chala has realized significant improvements is production quality. At the end of 2021, Chala became one of Evocon’s first Checklists BETA testers. This latest addition to Evocon’s product offering aims to improve quality controls and it’s helped Chala do exactly that.
Since implementation, Checklists has helped Chala reduce potential scrap by 3x, compared to its previous quality control process.
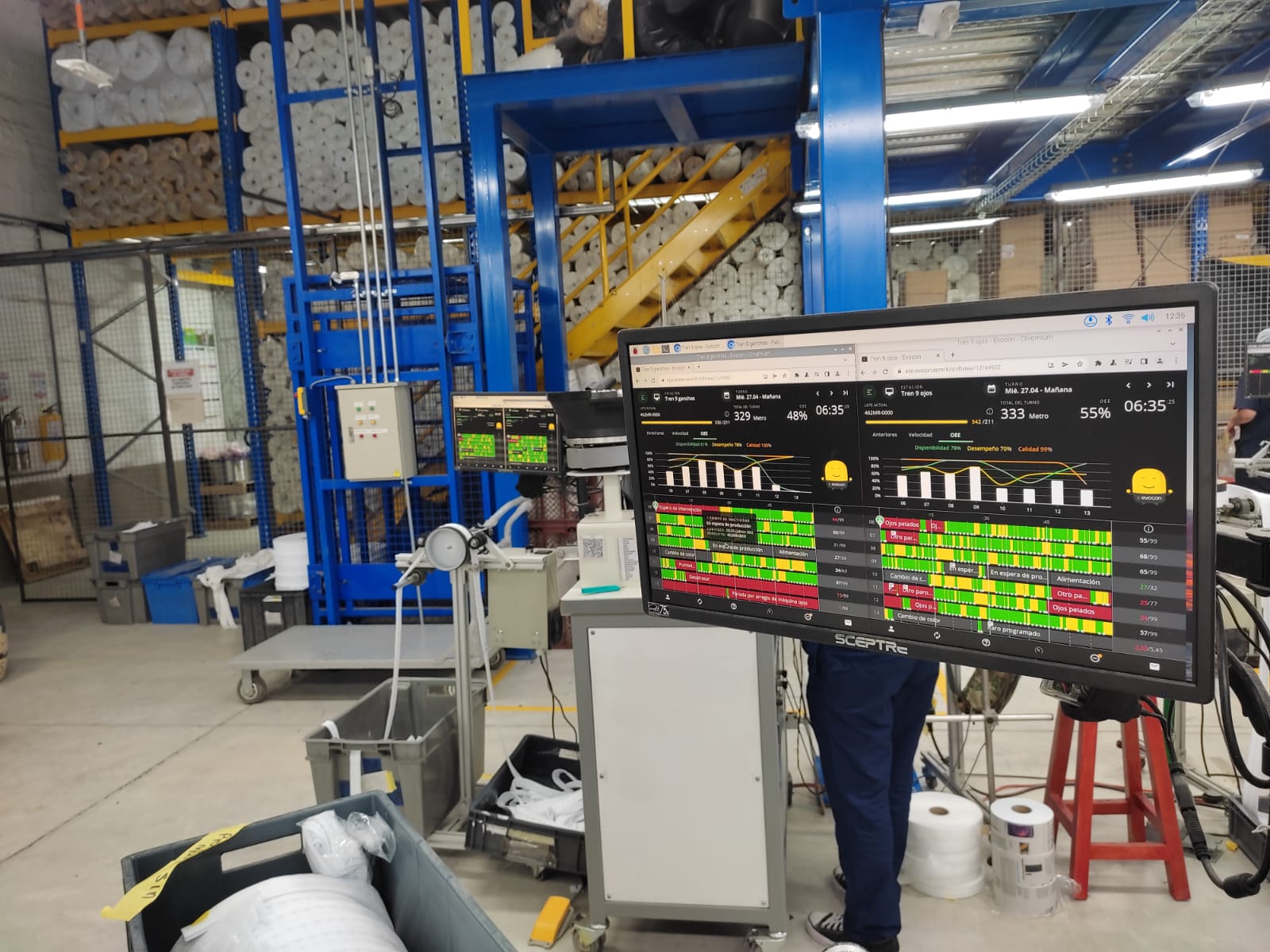
Previous quality checks were done in an old-school fashion using a pen and paper. Moreover (and rather wastefully), because Chala had no automated tracking in place, said checks were completed approximately after every 150 meters of product produced. The problem with this setup was that if a defect was detected, 150 meters of product needed to be scrapped.
With Evocon’s new Checklists feature, Chala now performs quality controls on every sewing machine after every 50 meters of product produced. Furthermore, since Evocon tracks production in real-time, the quality checks are triggered and displayed to operators only when the actual quantity is produced. This means that if a defect is detected, Chala only has to scrap 50 meters, instead of the 150 meters previously, resulting in three times less product being wasted.
“Scrap is not just product lost, it’s also valuable time lost on the line. At CHALA we promise the best quality for our customers – Checklists makes that possible,” says Sebastián.
Operators perform product changeover, interval, and cycle time checks which make it possible to have greater control over the product quality and the machine’s health. The operators are motivated to do the checks as they do not want to see red pins on the visual displays. When everything is green or orange, it not only indicates that everything is up to date, but further highlights a job well done.
Data-Driven Maintenance Operations
With Evocon’s intuitive, visual displays outputting real-time information, Chala’s maintenance engineers are able to keep a close eye on the current state of the factory. Should a line stop for more than the agreed time, maintenance goes and addresses the problem. Prior to Evocon being implemented, operators would have to leave their station to alert maintenance of the issue. In some circumstances, it was a long time before they asked for help to resume production.
As a result, Chala’s:
- Availability has increased between 20-25% across lines that have been subject to improvement projects
- Performance has grown on average from 30% to 70%
Chala’s next goal is to reduce the load of the maintenance personnel by handing the first-hand maintenance controls over to the operators. Here, Checklists is able to provide all the reminders they need at exactly the right times.
Start your digitalization journey
Gain the visibility needed to drive improvements and boost performance. Free for 30 days.
A Positive Cultural Shift
Chala implemented Evocon on one production line in the beginning; now it is implemented across 95% of the machines. Each of the lines has several data points that give Chala very accurate data about the efficiency of the workflow (end of line output is affected by start of the line input).
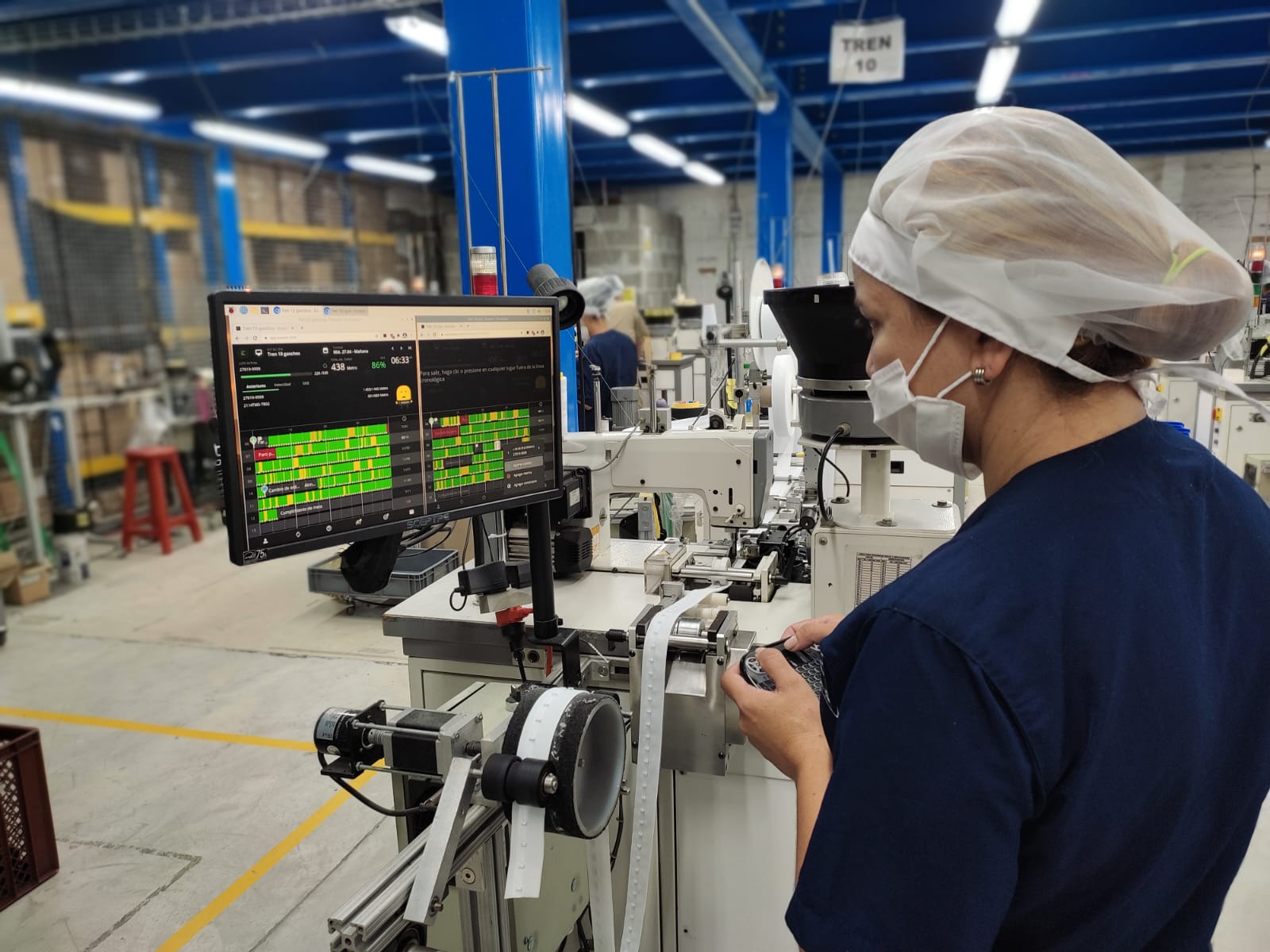
However, Sebastián admits that Chala’s operators took a short while to get used to Evocon. Suddenly their work was visible and they were not used to keeping track of downtime in such detail.
But Chala overcame this through its continuous improvements team, which was excellent in finding great ways to motivate operators.
“We all want to be recognized, so simple acknowledgments and appreciation, like having your name on the factory board for your good performance, can go a long way,” says Sebastián.
After this simple change, operators became more attentive to their tasks and felt a healthy competition between each other, which resulted in even smoother workflows and further decreased downtime.
Sebastián says: “Checklists have changed our company’s culture for the better. Operators want to make sure that all quality checks are done on time and according to expectations.”
Since implementing Evocon, Chala has:
- Grown its orders
- Increased production output capacity by 10% (from 176,000m in 2020 per line to 195,000m in 2022 per line)
- Expanded its asset park
- Improved its internal working culture
Another benefit reaped through its Evocon implementation is that Chala now has greater visibility into what its operators are doing. Previously, there was no accurate way to measure their day-to-day performance.
Now, when an operator is not performing to the required level on the production line, it is flagged as a training opportunity. The operator receives focused training, the result of which can be as much as a 15% performance improvement.
The Future Of Change
Chala’s initial goal was to keep machines running as much as possible and to rectify production stops as soon as they occurred. With Evocon, it has significantly reduced the duration and occurrence of longer stops, resulting in an increase in uptime of up to 25%.
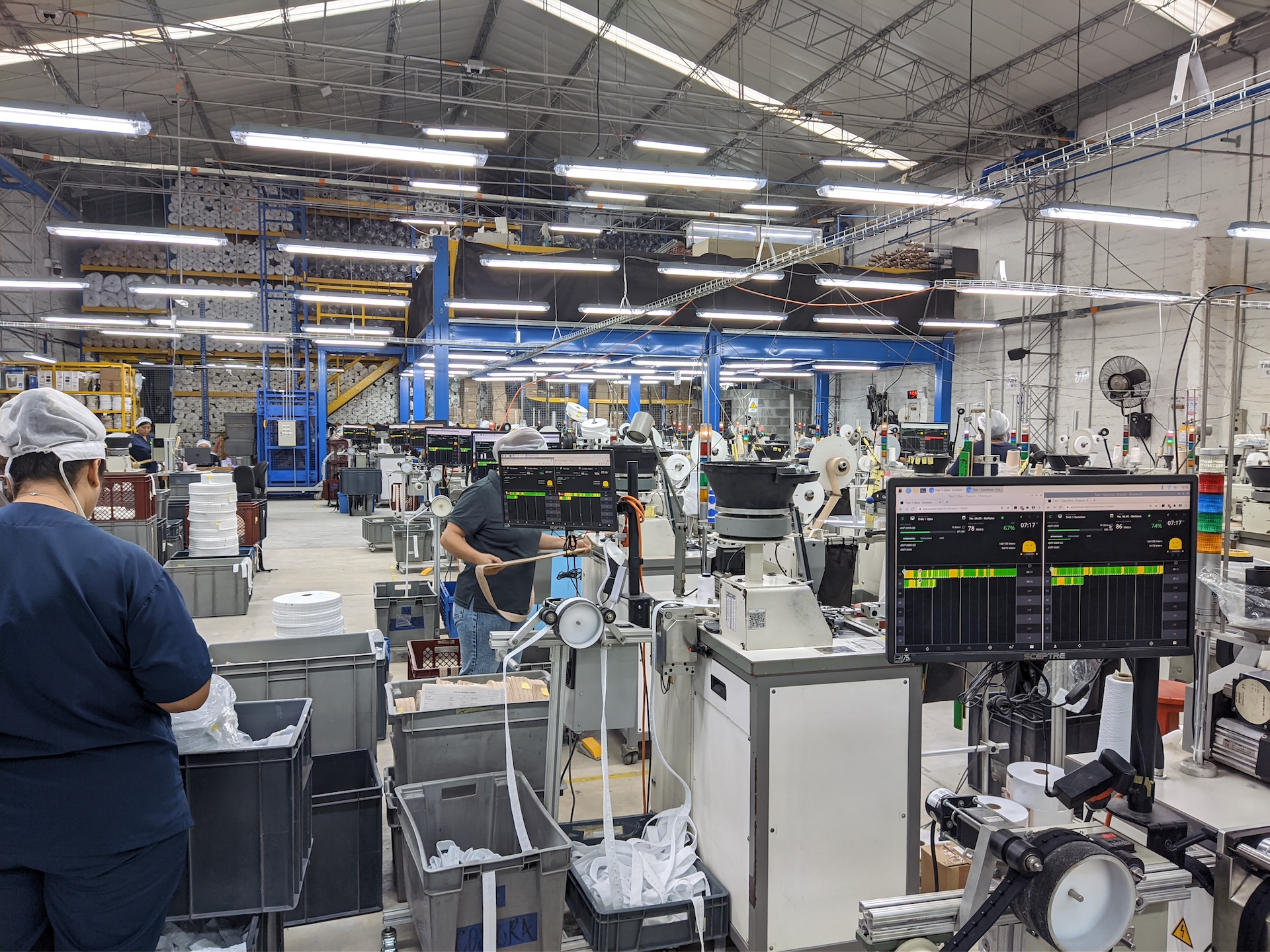
Now Chala has arrived at a place where it can start analyzing and improving the shorter, trickier stops (speed losses and micro stops), one by one, a week at a time. For that Sebastián and his team use Dashboards to compare stations and product performance. They try to establish the root cause so an action plan can be drawn up to resolve it permanently.
In terms of culture, the next step for Chala is to push operators out of their comfort zone a little further by encouraging them to take ownership and initiate problem solving on their own. It is a change that will take some time but they are sure that Evocon’s visualized and intuitive interface will guide operators on their journey.