Nova Packaging is a paper packaging producer based in Thessaloniki, Greece. It is part of Eren Holding, an organization with over 50 years of experience and operations spanning energy, paper, packaging, cement, retail, and textiles. The group is known for its large-scale operations, including being Turkey’s largest producer of corrugated cardboard, with an annual production capacity exceeding 1 million tons.
Over the past nine years, Nova Packaging has developed a world-class facility for producing packaging products, using state-of-the-art machinery and ensuring high-quality, sustainable production. They focus on continuous improvement and bring this to every aspect of their work, aiming to get better every day.
Since early 2024, they’ve implemented Evocon to visualize production and monitor OEE. We spoke with Fotis Fotiadis (Quality and Operational Excellence Deputy Manager) and Vasilis Anastasiadis (Deputy Production Manager), two of the visionaries behind Nova Packaging’s digitalization journey.
A Cutting-Edge Facility Built for Innovation
Nova Packaging’s facility is a testament to its vision of building a world-class production process with a modern approach to sustainable production. Along with new machinery and a clear vision for success, the company takes a particularly innovative approach to automation. For example, it implements the latest machines to facilitate seamless pallet movement from the corrugator to converting stations.
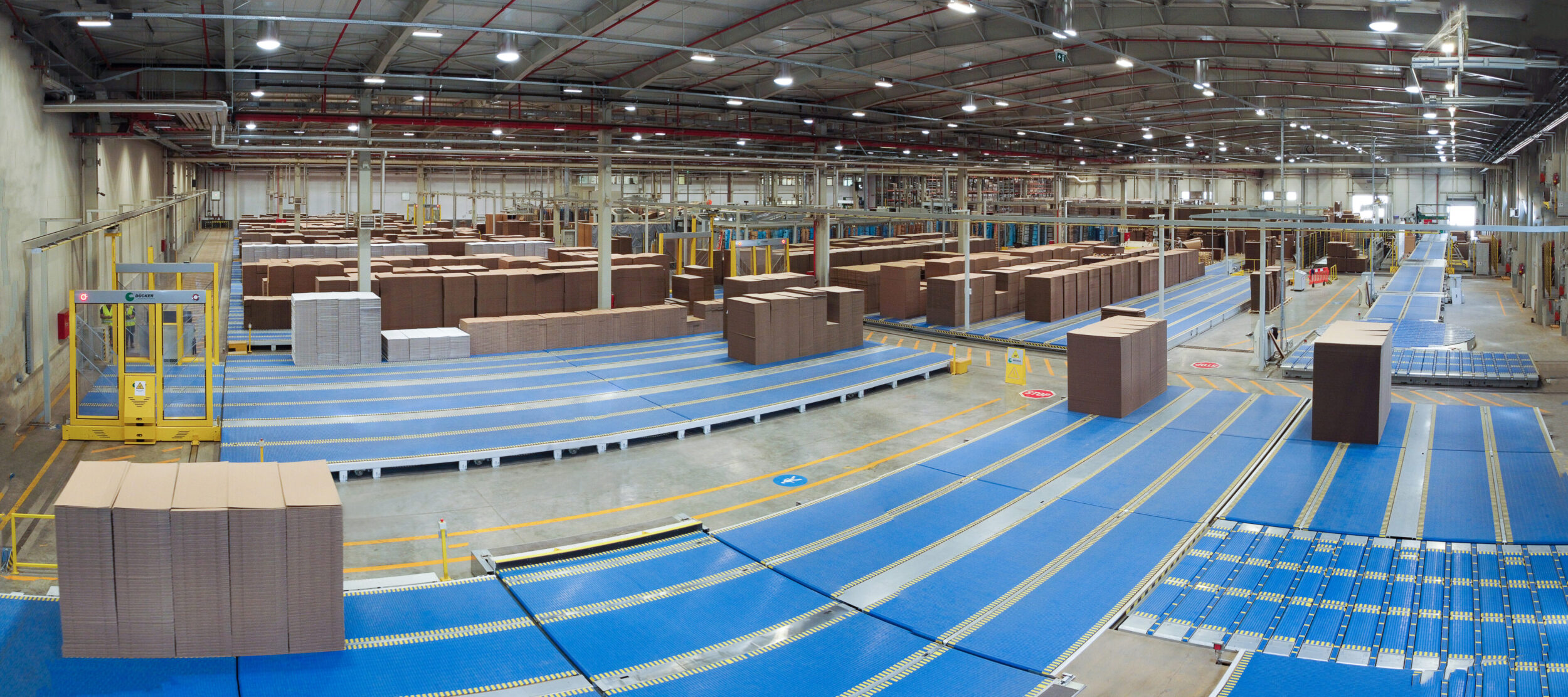
Their facility is equipped to produce custom orders in large volumes and change production orders as quickly and efficiently as possible. With all of this machinery in place, they also have a lot to track, and ensuring the machines are running smoothly is extremely important.
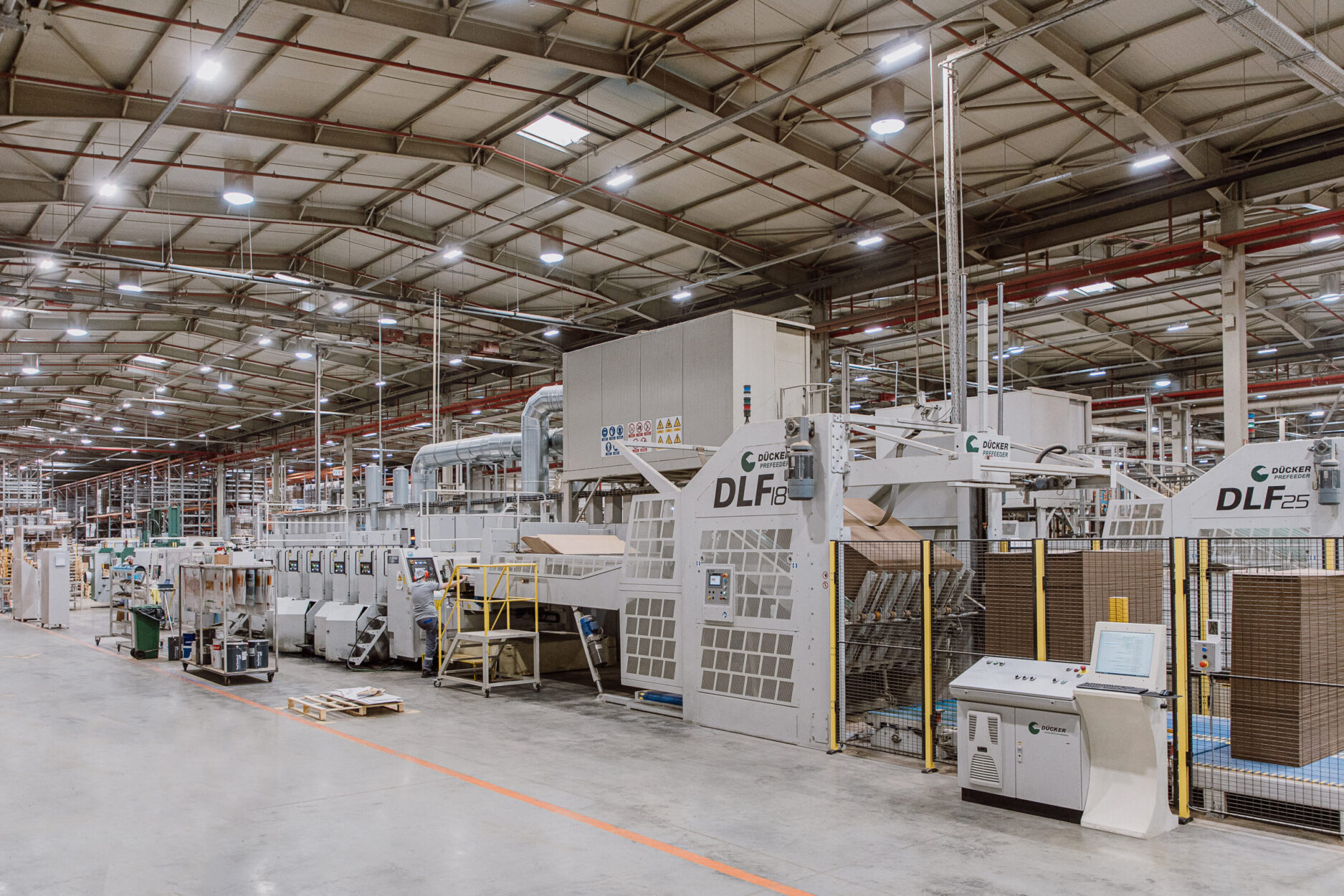
Overcoming Challenges in Data and Collaboration
After joining Nova Packaging in 2023, Fotis instantly found some areas for improvement. One of the first challenges he noticed was the need for a neutral reporting platform across departments. In their daily standup meetings, each team lead presented reports with diverse data in various formats, making it difficult to fully grasp what each department was discussing. This challenge highlighted the need for a unified platform where every department could display its reports in a standardized manner, ensuring that everyone could understand the information presented.
“Every department and every chief had their own reports. We didn’t have something neutral, something common to speak the same language, and that’s one of the huge benefits of Evocon.”
Vasilis Anastadiasis, Deputy Production Manager, Nova Packaging
Before implementing Evocon, they had already developed an in-house ERP and MES system. While these systems provided access to extensive production data, they lacked the capability to present it in a clear and actionable way. Vasilis explained that although the ERP collected vast amounts of data, including information needed for calculating OEE, the team struggled to visualize performance effectively. This gap highlighted the need for a user-friendly, visual solution to unlock the full value of their data.
This would lead to another challenge — resistance. With data monitoring already in place, the operators wondered why a new tool was needed. Fotis and Vasilis knew that understanding the “why” was the most important factor in smoothly transitioning to a new digital tool. OEE was not just another metric to add to their process — it was a tool that affected and could help everyone on the team.
Defining Success: Finding the Right KPI
The first step was to define KPIs for the team to work towards. From his experience, Fotis identified OEE (Overall Equipment Effectiveness) as the primary KPI to focus on, given its strong connection to continuous improvement. While they also considered metrics like production volume, these figures alone weren’t as effective in driving overall improvement.
“Let’s define what makes a good day a good day, and what makes a bad day a bad day”
Fotis Fotiadis, Quality and Operational Excellence Deputy Manager, Nova Packaging
The next step was deciding on an OEE software solution and implementing it in their factory.
As Fotis had used Evocon at a previous company, he knew it was easy to use and implement and had excellent visualization capabilities, so it was the clear choice for their needs.
From Data Overload to Clarity: Implementing Evocon at Nova Packaging
Evocon was selected as the OEE system of choice because it addressed the two key areas identified by Fotis and Vasilis:
- Visualization was one of the most important aspects Fotis and Vasilis picked out, as they knew how important it is to have engaging, accurate, understandable ways to display their data.
- They also needed more specific data. With their in-house solution, they could collect the duration of the shift and mark downtime, but they couldn’t mark the specific reasons for stoppages, such as product setup.
With the support of Evocon’s authorized partners in Greece, Spiros Vamvakas and John Lelis, they implemented Evocon. Since April 2024, it has been implemented on three machines, aiming for a full-scale implementation on all machines in 2025.
Cultural Change: Boosting Engagement on the Shop Floor
The Nova Packaging team took an interesting approach to education on OEE. In addition to running OEE training sessions, their operators calculated OEE manually for the first couple of months. They first calculated OEE scores by hand and then added the data to Excel. This was purposely done to give the operators a complete understanding of how OEE works and how its three components — availability, performance, and quality — together create clear targets for improvement.
It was essential to make it clear that OEE is a tool to be used, not just a number on a screen.
From Resistance to Engagement: Operators Embrace Transparency
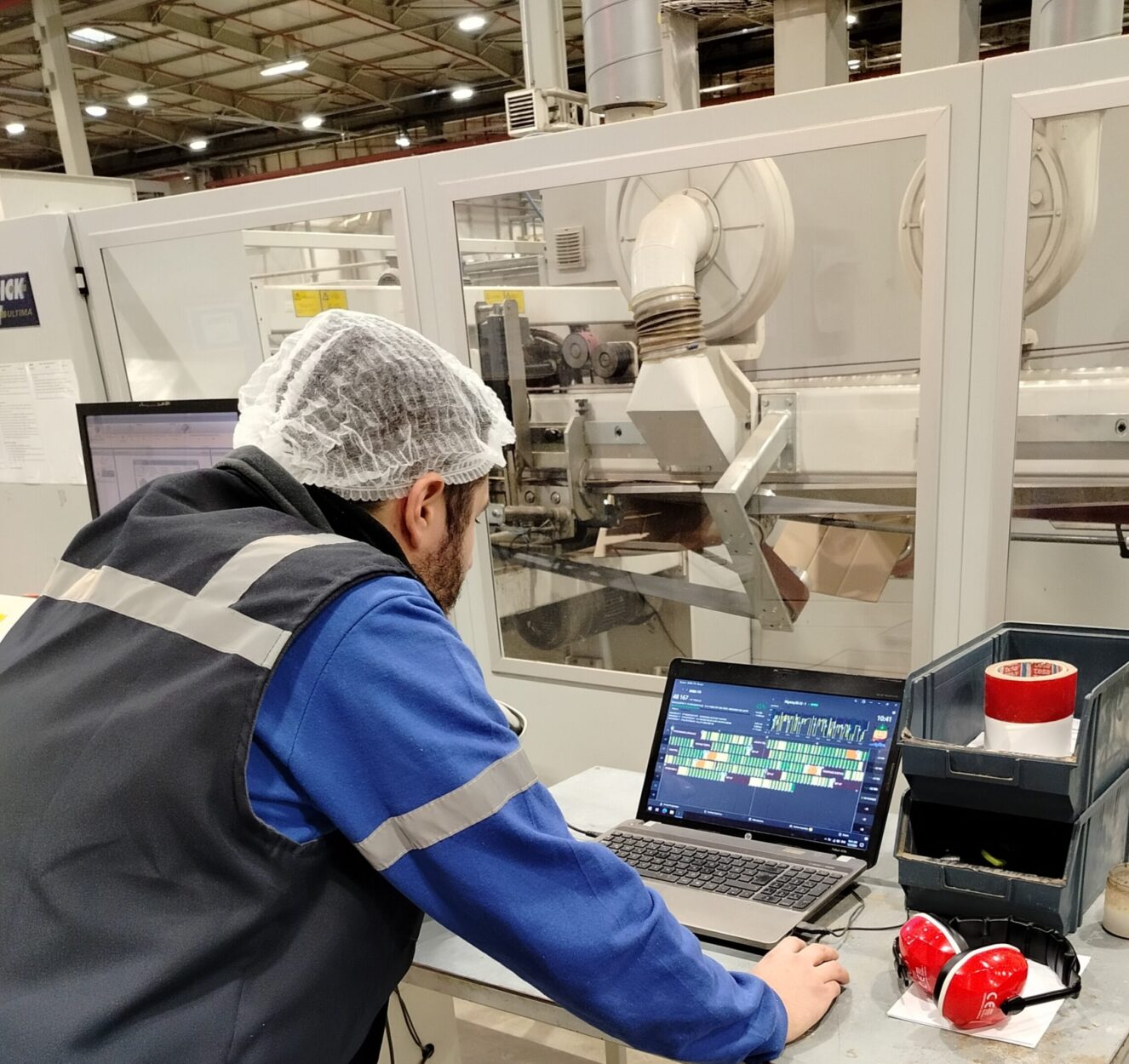
The Operators Perspective
Evocon made an instant impact on the shop floor, with operators appreciating the new tool’s visualization. The training on OEE they received in the months prior helped put any reservations they initially had at ease, and they were ready to start using the solution with a strong understanding of OEE philosophy.
The clear, transparent data it provided was one of the main reasons the operators engaged with Evocon. They now had access to and understanding of the data used by each department in the organization. This transparency made the operators feel like they had a say.
“The operators engage with Evocon because of two main reasons. First, they appreciate this transparent and data-driven approach. And second, they see that Evocon makes their contribution measurable, valuable, and visualized.”
Vasilis Anastadiasis, Deputy Production Manager, Nova Packaging
One moment that Fotis was particularly proud of was when operators brought new ideas to him. An example of this was when, after introducing a new product, some operators realized that a different process was involved in the setup, leading to a different setup time. They asked if they could add a new stop reason to the system to track and improve the setup times for that product. The operators’ initiative directly resulted from implementing a visual, transparent solution on the shop floor.
The ease of use of Evocon and the simple color coding of machine uptime also increased operator engagement. When everything was green and running smoothly, the operators felt good, and when it was red, they knew something needed to be done — a simple but effective benefit of having such intuitive software.
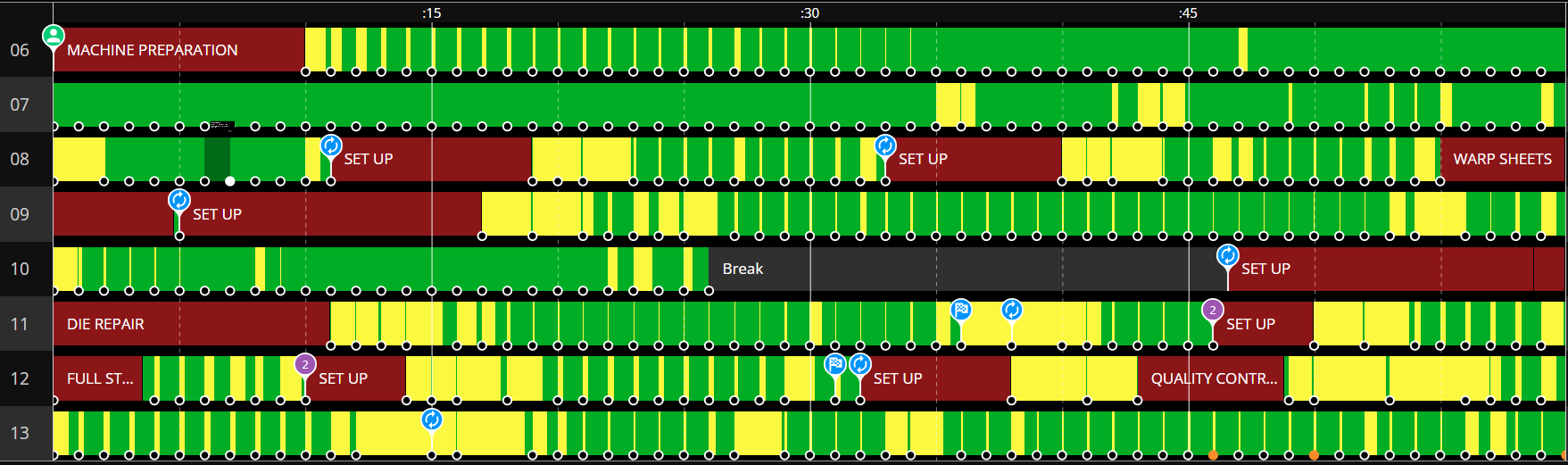
The Management Perspective
Since its implementation, the management team at Nova Packaging has been impressed by their team’s adaptation to Evocon, and two particular benefits of the system. The first point they picked out is the ability to access accurate, real-time information online. In the past, they would have data from the previous 24 hours, meaning that any solution they needed was implemented after an issue had been found rather than on the spot.
The second considerable benefit they found was the possibility of viewing the data on the go. With Evocon available on mobile devices, they could check how the factory operates when traveling or if they needed to check how machines run during a shift when they aren’t at the facility.
The Window into Production – How Evocon Powers Daily Operations
Collaborating in Daily Meetings
Evocon is used daily at Nova Packaging in several ways. Every morning, they have a team meeting during which each department updates the rest of the team. Evocon reports have become a staple of these meetings, with teams using them and understanding how OEE impacts other departments, from sales and success to production and accounting.
This has led to a more cohesive understanding across departments, meaning they are on the same page when deciding on improvement projects or developments in the facility.
Before and After: Evocon in the Office
The factory has an open office where technical, production, quality control, and excellence managers collaborate, fostering cross-departmental communication and synergy. This is extremely valuable because everyone knows what is happening with the other teams and can help each other out when necessary.
Before implementing Evocon, management oversaw the production from the office through the large windows looking directly out onto the shop floor. They saw this as their “window to the production process.”
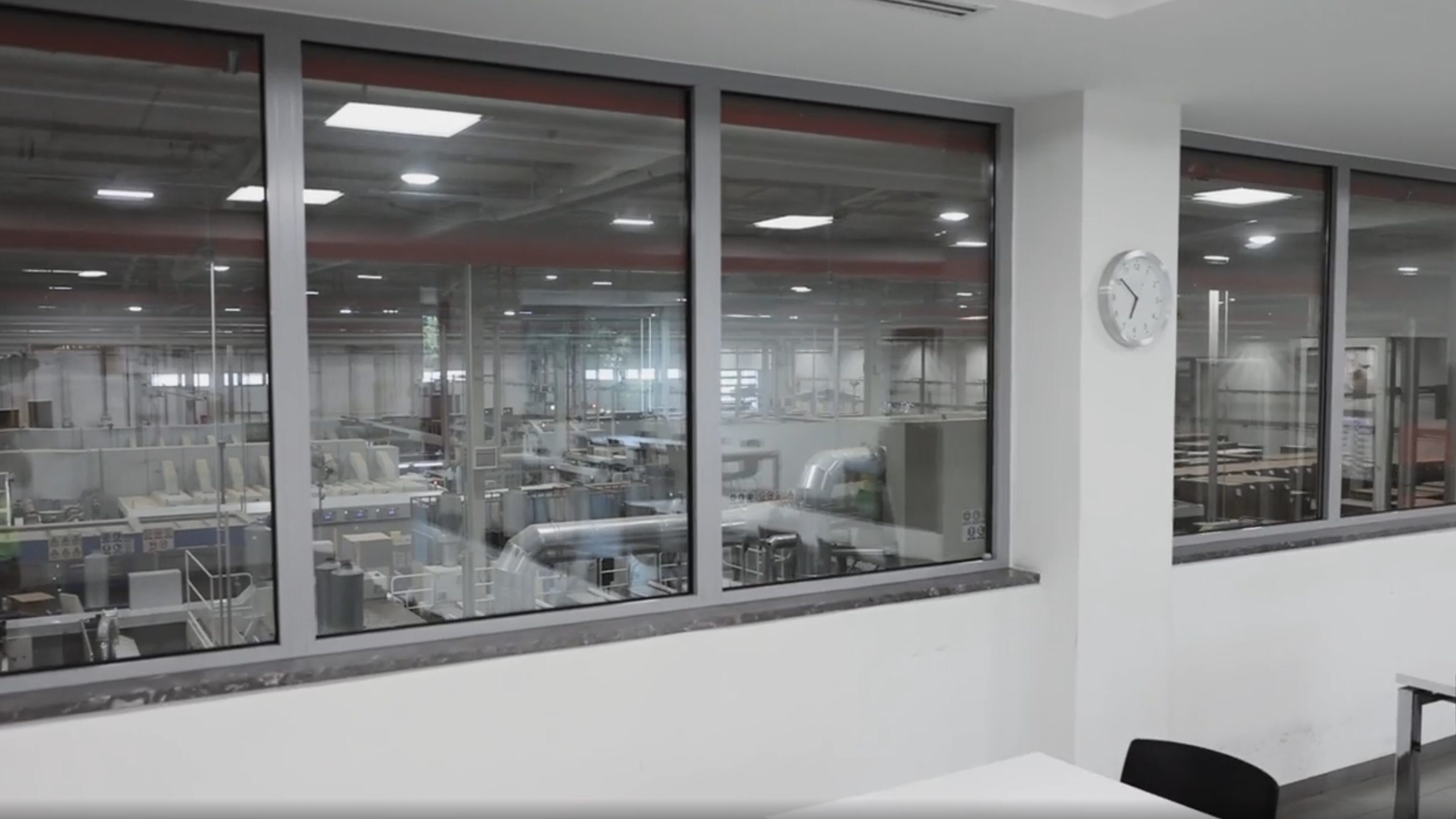
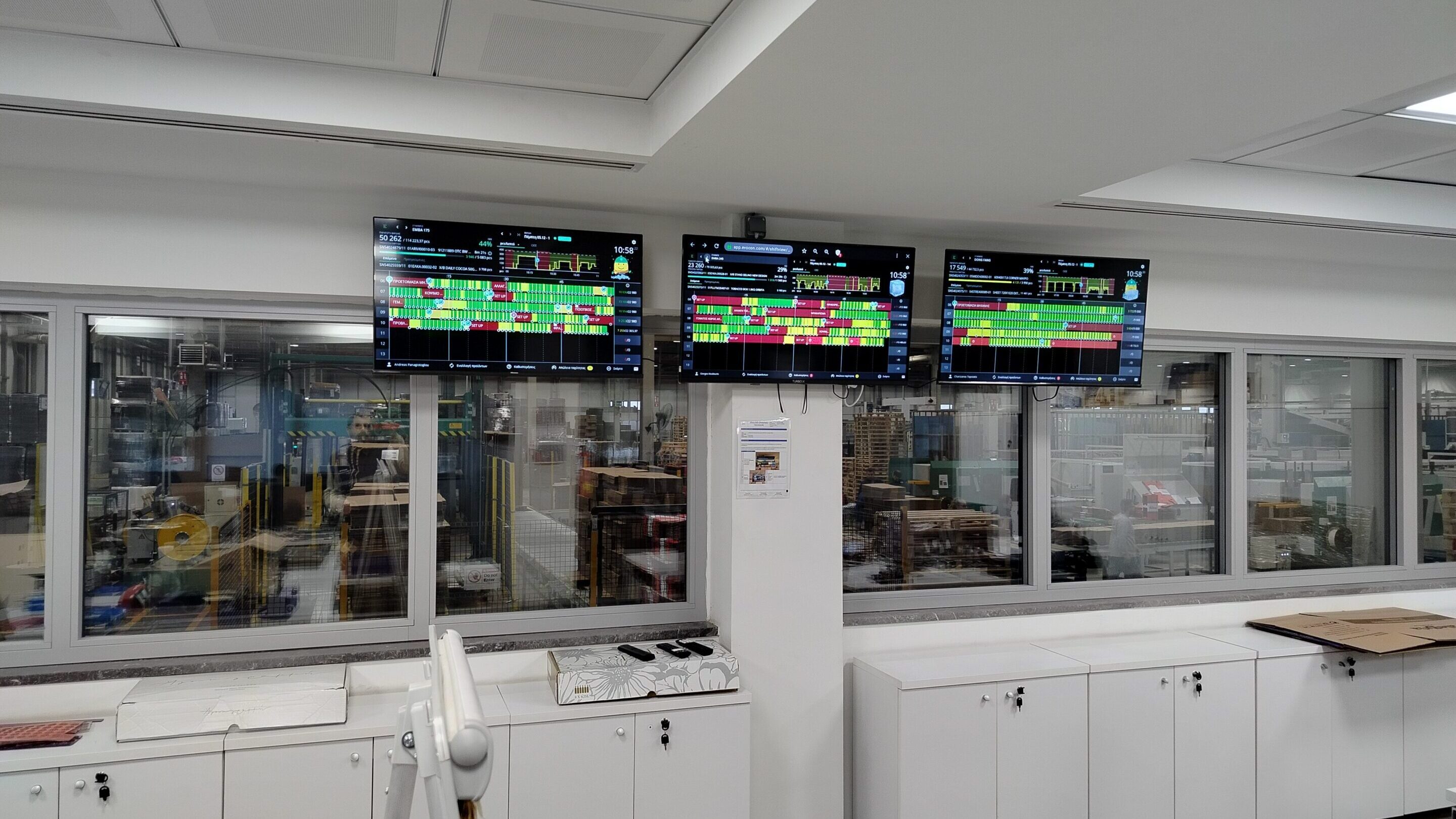
Now, monitors have been installed in the office and are visible to everyone, with Evocon always on display. As Evocon has become an integral part of Nova Packaging’s working processes, they say they have “replaced these windows with Evocon” as it provides the data clarity and accuracy needed to act effectively.
“Until now, we saw our production through the windows. But we didn’t understand it. Now, Evocon’s TV screens are our real windows into the production.”
Fotis Fotiadis, Quality and Operational Excellence Deputy Manager, Nova Packaging
Continuous Improvement: Building a Future of Operational Excellence
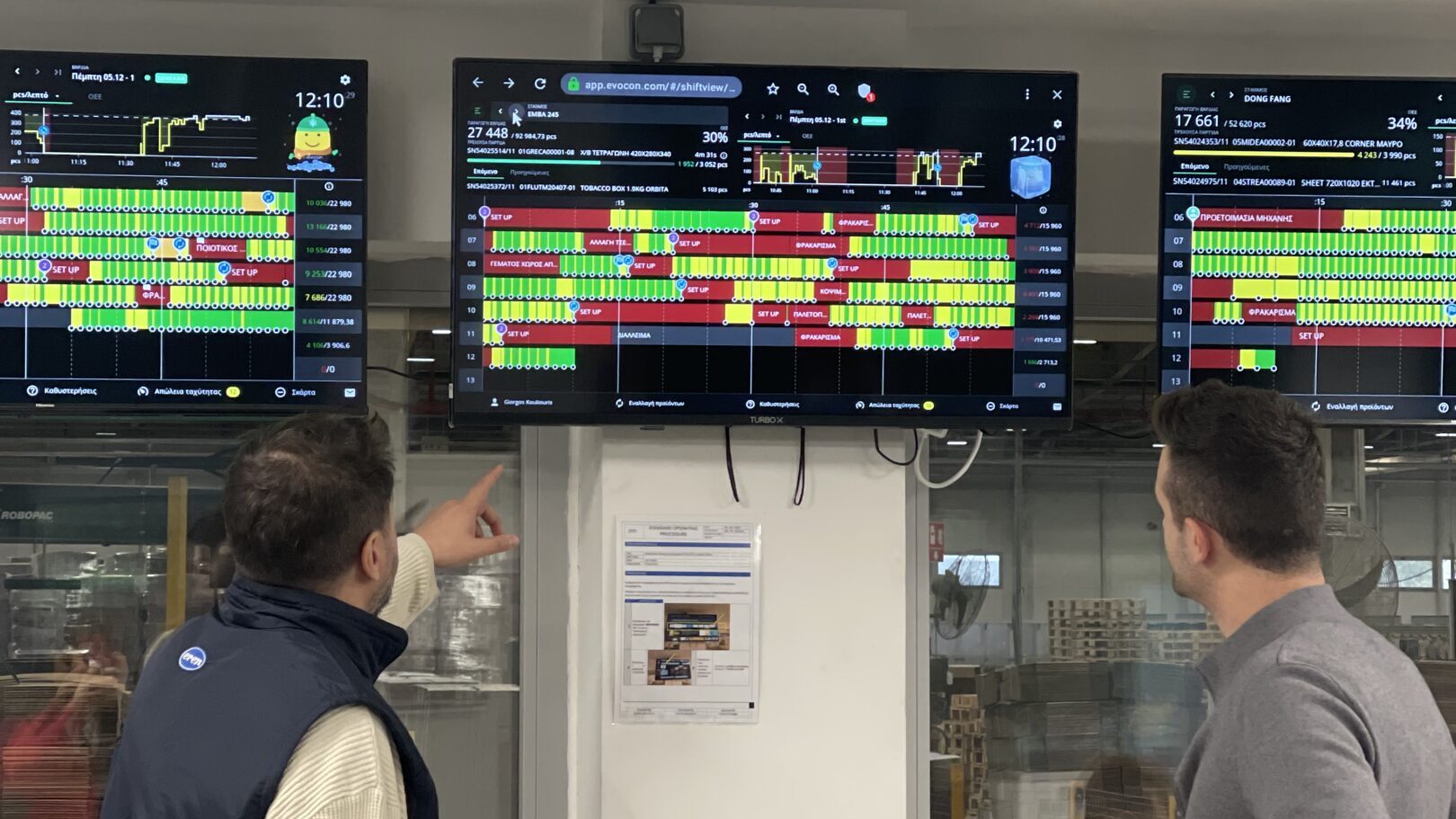
Fotis and Vasilis have implemented modern, innovative tactics to take Nova Packaging to a new level of production. By focusing on data visualization, educating operators, and OEE, they have an excellent opportunity to continue to improve.
Continuous improvement in all aspects is integral to their work. With OEE, rather than targeting a specific percentage, they focus on ensuring steady progress, even in small increments. When it comes to production, they want to maximize efficiency wherever possible.
“This is the philosophy that I want to implement here. Just a small increase regardless of what percentage our OEE is; let’s improve it a little bit.”
Fotis Fotiadis, Quality and Operational Excellence Deputy Manager, Nova Packaging
Nova Packaging inspires modernization, digitalization, innovation, and a culture of continuous improvement. By using tools like Evocon, they have made their operations more efficient and encouraged teamwork and transparency across the company. Their focus on clear data and involving operators has enabled them to make real progress. Looking to the future, Nova Packaging aims to keep improving and setting new standards for sustainable and efficient production.
We’d like to thank Fotis and Vasilis for sharing their experiences with us, as well as Spiros and John, our authorized Evocon Partners in Greece.
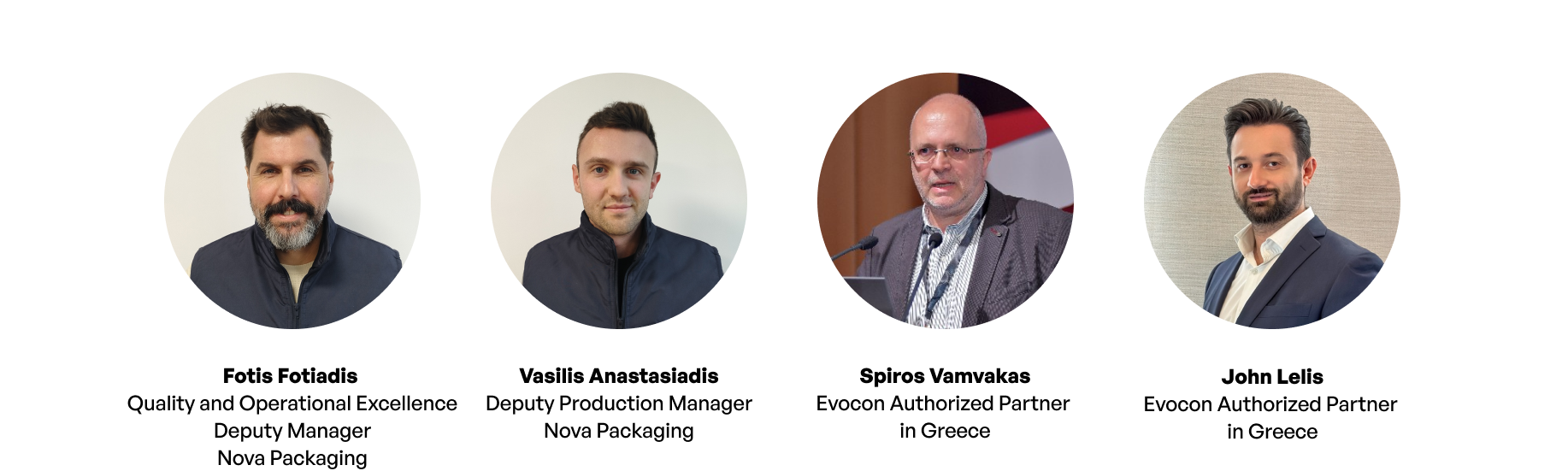