In this brief case study, we feature a company from Greece that is not just a leader in their industry and in their country, but a leader in Europe. Like many, Papoutsanis’s journey with Evocon started from the basic need to digitize its data collection process.
Company Profile: Papoutsanis SA
Papoutsanis SA was founded in 1870, when Dimitris Papoutsanis created a successful business of olive oil soap on the Greek island of Lesvos, by committing to delivering innovative, high-quality personal care products at competitive prices.
Today, the company, listed on the Athens Stock Exchange, is one of the largest manufacturers of soap, and liquid cosmetics in Europe, with over a hundred million products made per year.
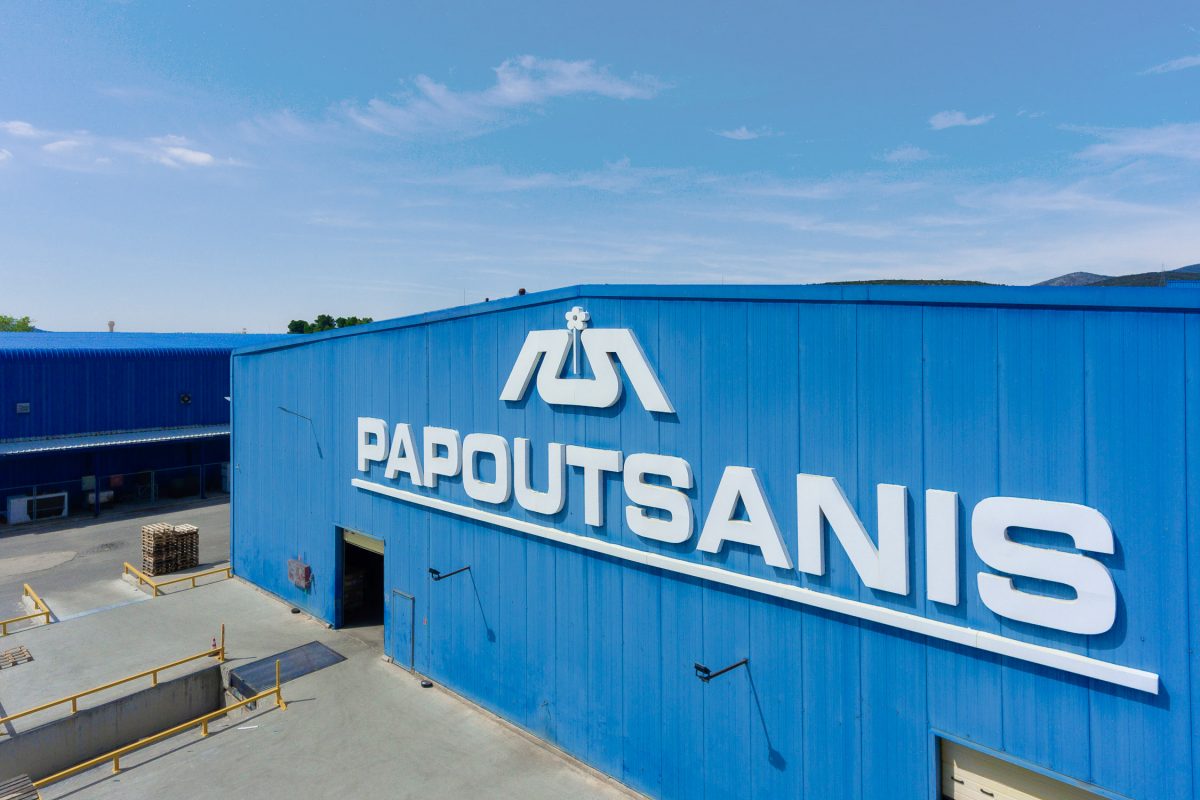
Among the varied line of products that they have, there are shower gels, shampoos, hand washes, face cleansers, hand and body lotions, and more. And in addition to liquid cosmetics, they also have a line of accessories, such as dental and shaving kits, shower caps, sewing kits, vanity sets, combs, amenity trays.
Inspired by 150 years of history and empowered by innovative thinking and vigor, Papoutsanis is constantly enriching its product portfolio for customers and consumers worldwide. Their innovative approach and a focus on quality have earned them a presence in more than 25 countries globally, with exports including to Europe, America, Asia, and Oceania.
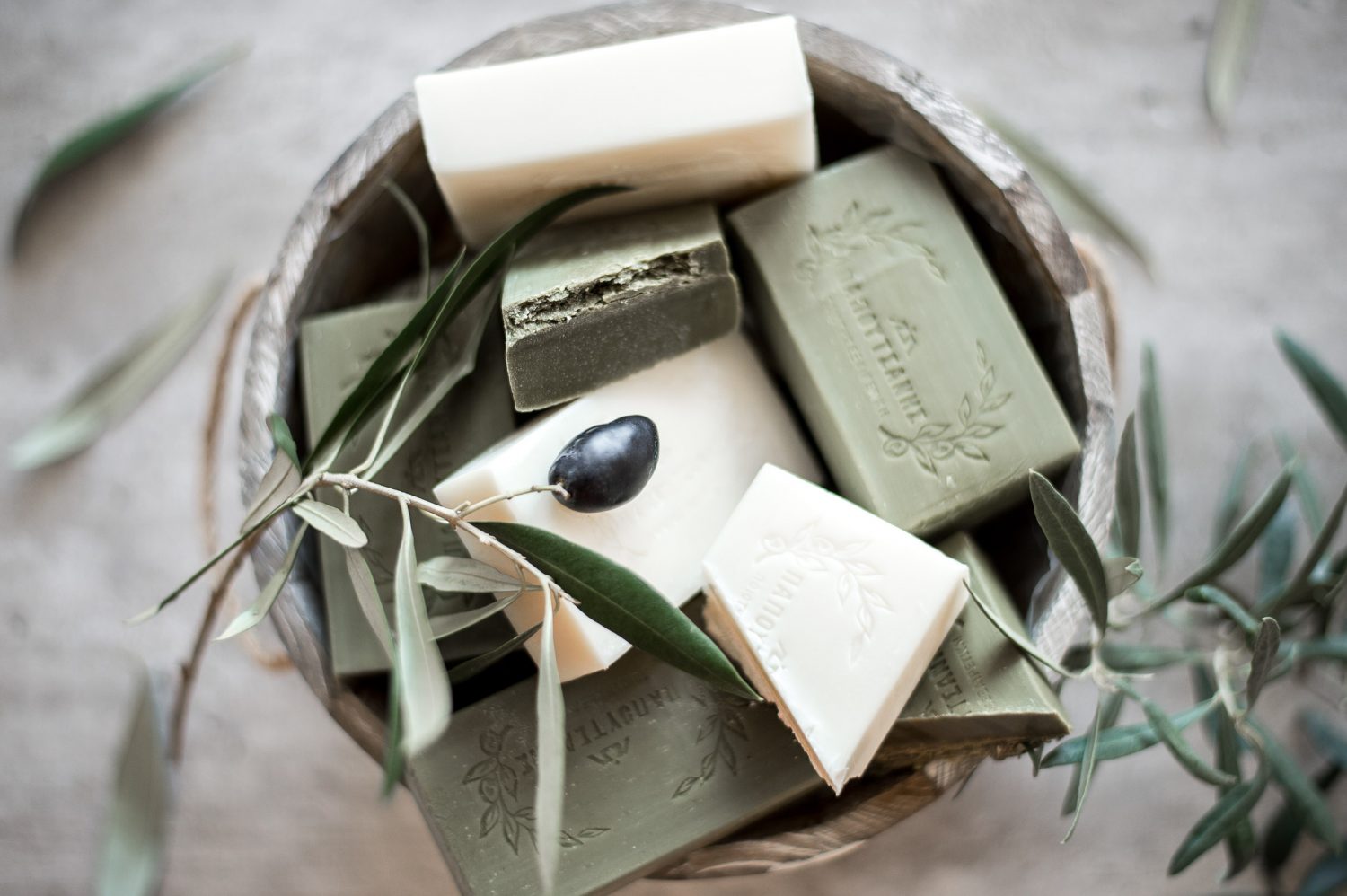
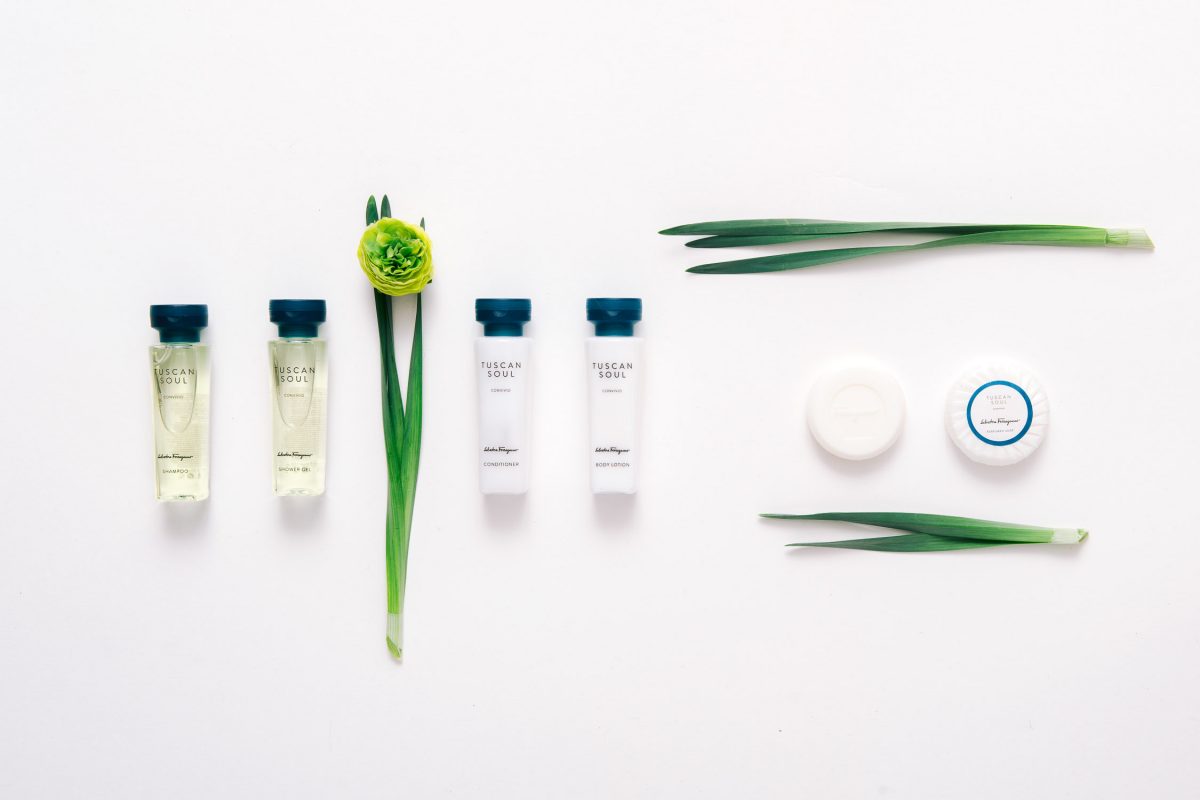
Production overview – diverse & complex
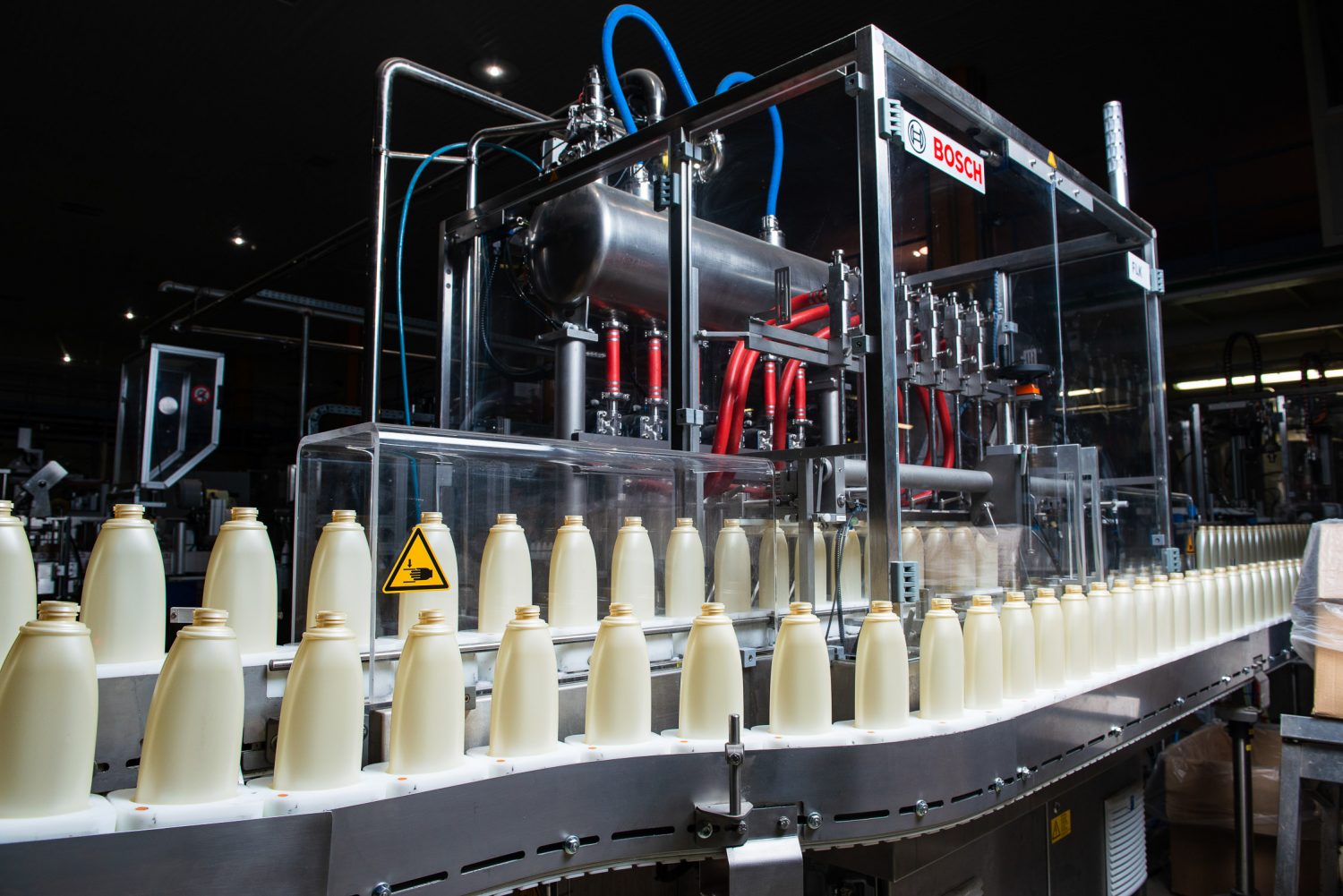
Papoutsanis operates a fully integrated, state-of-the-art production plant in central Greece, close to Thiva, which also functions as an export hub.
The company has four main production areas:
- Own Brands (such as KARAVAKI, Natura, and Aromatics) and Selective Distribution Products (OLIVIA).
- Hotel Amenities that hold a leading share in the Greek market and existing collaborations with international hotel chains and the biggest multinational hotel-supply industries.
- Third-Party and Private Label Manufacturing for international suppliers and retailers.
- Specialized Soap Noodles for its industrial clientele.
In addition to the variety of products it produces, the company also manufactures plastic packaging (bottles and caps) for its cosmetics. The in-house production includes processes such as injection, stretch blow molding and extrusion blow molding.
All of the above showcases the diversity and complexity of their production and that any technological solution implemented to improve their production has to be able to take this into account.
Going Smart with Evocon
Papoutsanis, to be able to respond to today’s challenges that require flexibility, quick response, total customer and consumer satisfaction, full cost control, and productivity improvement set out to modernize their factory.
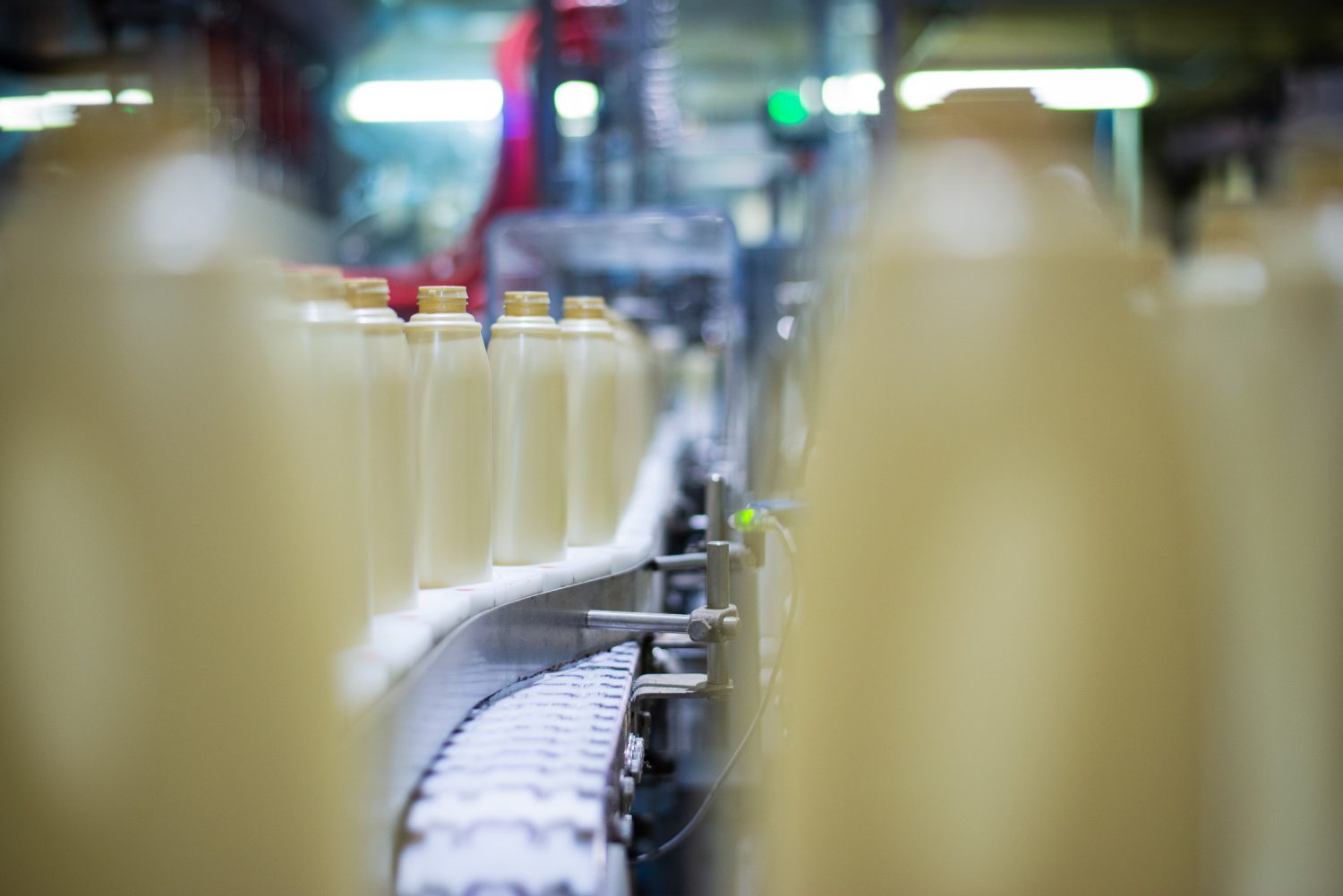
Taking advantage of available technological solutions on the market, they started to look for ways to convert their factory into a Smart Factory.
💡 A smart factory is a digitized manufacturing facility that uses connected devices, machinery, and production systems to continuously collect and share data. This data is then used to inform decisions to improve processes as well as address any issues that may arise. – TWI Global
Since this process consists of many steps and increases in complexity, they wanted to start by digitizing their data collection process and getting information on what is most important to them – real-time overview of production, OEE, and main losses.
Start your digitization journey
Get the tools you need to track and analyze the performance of all your production shifts across different stations, factories and countries. Free for 30 days.
Reasons for choosing Evocon
Because of their profile, Papoutsanis had many criteria that would have to be met when implementing an OEE solution. Finally, after running a free trial of Evocon, they outlined the following reasons for choosing to continue with Evocon:
- The possibility to try the solution for free before committing any investments.
- The OEE system of Evocon is easy to set up and can monitor any production process.
- The initial investment was minimal.
- It is cloud-based and has a subscription service (SaaS).
- It captures OEE in real time with accuracy, transparency, and clarity.
- It is user-friendly and, due to its engaging nature, motivates staff for continuous improvement.
- The solution helps evaluate maintenance effectiveness, through the use of different features.
- It provides different reporting capabilities and supports in-depth analysis of each identified problem.
- The system can be integrated with other IT systems (ERP, CMMS, etc.)
- It has support documentation that users can easily access and a professional and fast support team to help with issues and questions.
39% change in OEE in 12 months
After a year of working with Evocon, the Production Manager of Papoutsanis, Mr. Vassilis Mavroidis, summarizes their experience as follows:
“With the installation of Evocon and after total factory implementation, we review all losses of the equipment every day, and we know every minute what is happening in our factories. The upward trend of OEE is steady, and the improvement versus last year is over 30%.”
Production Manager of PAPOUTSANIS SA, Mr. Vassilis Mavroidis
From their OEE dashboard, we can see how the first 4 months (12.2021-03.2021) of the whole factory averaged 45%, and then in the last 4 months (7.2022-10.2022 – excluding November of 2022, which is still ongoing), it has been averaging at 62.5%. Which is actually a 39% change and an increase of 17.5% in absolute numbers.
This is a remarkable increase in only a year for the whole factory.
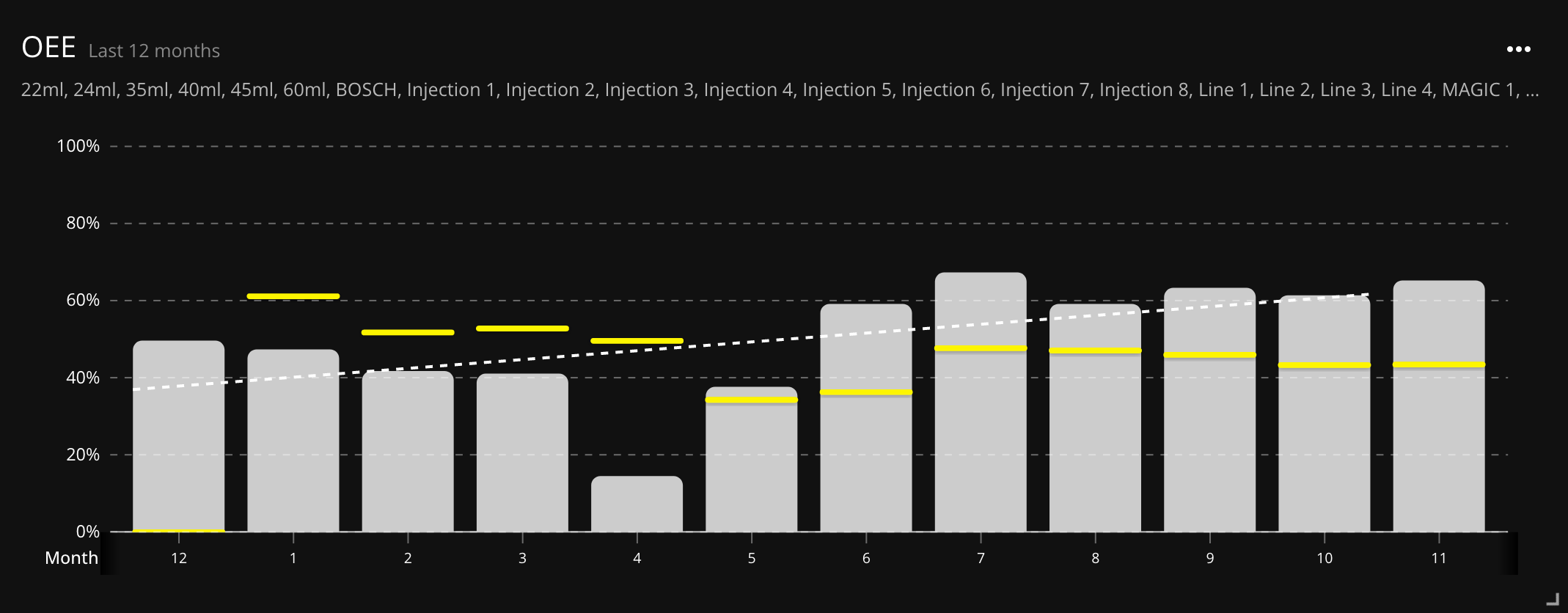