TMI has made a business of quick response, fast-to-market, prototype to production, and low volume / high mix offerings. As anyone in manufacturing will tell you, this is difficult terrain to master.
As one might expect from a company that makes such difficulties its core business, TMI believes in integrating emerging technologies. This is in service of their never-ending drive to improve and streamline processes. Which is exactly what led them to Evocon.
About TMI Automotive Products
TMI Automotive Products is a family-owned manufacturer of industry-leading automotive interior components. Based in Corona, California, the SoCal born company has carved out a niche over the past 35 years by providing the industry with innovative products for restoration and resto-mod project vehicles.
TMI Products was founded in 1982, when the Tuccinardi brothers began making Volkswagen® door panels by hand in their family garage in Torrance, CA. TMI quickly became the market leader of classic Volkswagen interiors, and after years of delivering high-quality products, TMI expanded its offering to include new applications such as Chevrolet®, Ford®, and MOPAR® to meet market demand. Being an industry leader, TMI branched out to offer a blended style of classic and modern and created the Pro-Touring line. All the while remaining true to the Restomod Sport Series product line.
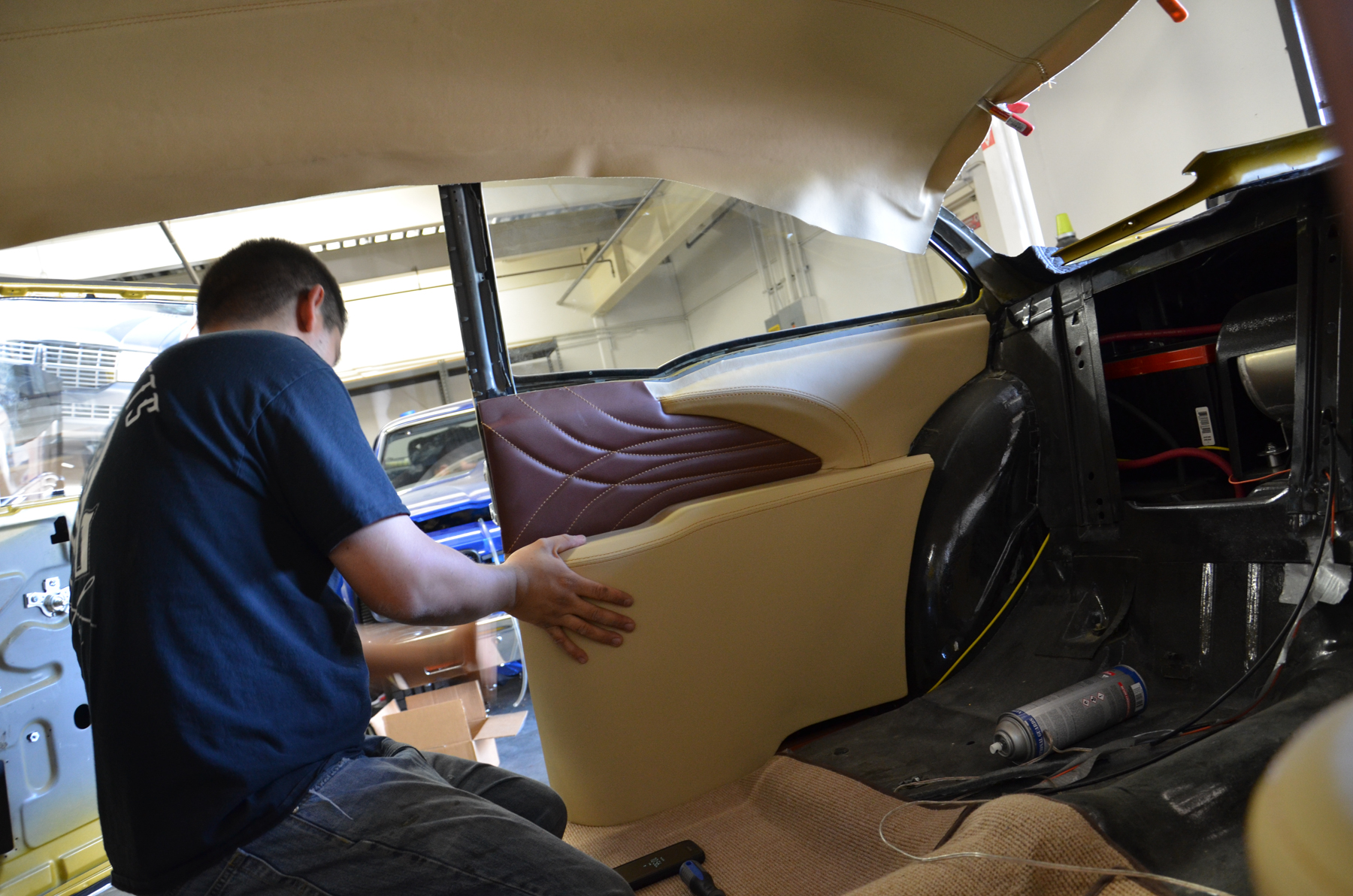
Production Monitoring Challenges
TMI had two related challenges that they faced. Both of which came about as part of the decision process to invest in some new equipment (Kuris cutting machines and additional sewing machines).
Data accuracy
“Our production manager didn’t believe the efficiency we were getting was as low as it was.”
Gene Tuccinardi, CEO for TMI Automotive Products, Inc.
What Gene’s quote comes down to is essentially an issue of data accuracy. This is a common problem with paper-based production monitoring in general. It is usually experienced as a lack of trust in what the true numbers are. For a team to be effective, there needs to be a single source of truth. One number that the team can agree on and trust. Without it, problems can surface in a variety of areas.
This was the problem when TMI was trying to decide if they should invest $500k in a new machine for their cutting line. In fact, TMI correctly decided, not being able to know for certain how efficient you were was a problem any way you look at it.
So, TMI chose to solve this problem as part of the investment process. After all, if you are going to invest in a new machine, shouldn’t you be able to see if it improves the efficiency of the line once it is operational?
Timely data to visualize production
TMI also realized that in addition to not having data they could trust, there were other problems. How they visualized and used production data to understand efficiency could also be improved.
In particular, was the fact that TMI was always looking into the past when they reviewed production reports. This is another common problem with paper-based production monitoring. By the time you get the data in your reports, it’s too late to act on it.
“We had reports, but they were only numbers. Also, we couldn’t see moment-to-moment how we were actually doing. We had to wait till the end of the day or the end of the week.” said Tuccinardi
Historical data is useful to management, where time can be taken to analyze the raw data. However, the situation is less than ideal for the machine operators responsible for getting things done on the floor. In that case, as Gene points out, numbers are not enough to allow operators on the floor to react in real-time. For this to be possible, operators need to be able to visualize production.
All of this resulted in a general rethink of how TMI used production data. They realized that it was not enough to simply get accurate data on efficiency. To really change the game, they needed to be able to visualize production in real-time. The challenge here was that when they came to this realization, they were completely new to the idea of real-time OEE monitoring.
New technologies
TMI had learned a few things from its history of integrating new technologies into its production processes. One key learning is that you never know if something will work until you try it yourself. TMI also possessed the frugality that comes naturally to entrepreneurial family-owned businesses. These two facts combined made the possibility to try Evocon’s OEE software for free very attractive.
The Solution for TMI Came from Evocon
When TMI reached out to Evocon to begin the free trial, they were unsure if the solution would work. Evocon worked closely with them to understand the situation and stayed in close contact while they worked through a few unique challenges during the hardware implementation.
“We had a few challenges getting the hardware setup and the team at Evocon were very responsive. They quickly helped us through the process to get us online,” said Tuccinardi
Once Evocon’s IIoT devices and sensors were installed and operational, TMI was able to see that the solution would indeed work. In fact, Evocon has fundamentally changed the way that the company operates its production facility.
Start Your Improvement Journey
Automatically collect the production data needed to transform your operations. Free for 30 days.
Change management
The transformation of the production process does take time though. One hurdle that companies usually encounter at first with production monitoring is one of human nature. Try as we may, all of us are susceptible to resist change at times. So, no one can blame operators on the floor when they at first find production monitoring to be intrusive. Admittedly, it can seem Orwellian.
However, as TMI can attest, there are tried and true ways of working through the resistance to change. Mainly this comes down to demonstrating in words and actions that the purpose of monitoring production is not to play “gotcha” and punish operators. Instead, production monitoring is the way we can see clearly and accurately what is happening. Once we can visualize production accurately, the challenge becomes to work as a team to improve the results.
Automated data collection and reporting
It is natural to see that when a company struggles with the limitations of manual data collection, in this case, data accuracy, that the solution is to automate the collection of data and take the human variable out of the equation.
It’s only in the last decade that the cost of such solutions has become affordable to the average company. And it is Evocon that is at the forefront of making this possible. From the free trial to the incorporation of new improvements and updates based on user feedback at no increased cost to the end-user. All the way to the cost savings that can be realized by eliminating paper-based production monitoring, reducing machine downtime, and improving OEE, the value in Evocon’s cloud-based production monitoring and reporting is clear.
For TMI, the benefits of visualizing production moment-to-moment for operators and managers on the production floor began to take shape after a couple of months. Particularly when TMI decided to implement Evocon on its foam line. To date, OEE has improved by 30% on the foam line.
“The biggest problem now is that we are too efficient and it’s hard to make improvements. But we keep trying… mainly through the Evocon Meeting.”
Zach Tuccinardi, Electrical Engineer for TMI Automotive Products, Inc.
The “Evocon Meeting” at TMI
Once TMI had Evocon operational they began to visualize production data and results. Shortly after that, it was natural to incorporate the results into their daily and weekly production meetings. Which they affectionately came to call “The Evocon Meeting”. These meetings have become and remain, to this day, the cornerstone of how TMI manages production.
The form and content of the meeting continue to evolve from where it began over a year ago. Part of this routine is to pull downtime reports and discuss top reasons on the Pareto charts during productive problem solving sessions. TMI has also incorporated Quality Assurance and Maintenance personnel into the meetings, which we highly recommend and consider a best practice in its own right.
Conclusion
From the story of TMI, we have learned that when a company struggles with the limitations of manual collection of production data, in particular data accuracy and timeliness, that Evocon’s automated production monitoring and live OEE tracking is a viable solution. In the months and years ahead, TMI plans to continue to explore and leverage the benefits of data automation and production monitoring.