In our article, the importance of lean continuous improvement you learned about the origins and benefits of continuous improvement and that PDCA is the core of Kaizen. But what specific steps are involved in using PDCA? In this one, we answer this question by giving a thorough introduction to the popular process improvement methodology known as PDCA.
What is PDCA?
While working with W. Edwards Deming in the 1950s, the Japanese adopted a process improvement methodology they referred to as the “Deming Cycle”. Today it is the fundamental core of “Kaizen”.
It was Deming that introduced the Japanese to the method, but the method itself was actually developed by his colleague Walter Shewhart.
Shewhart called his method PDCA.
PDCA is an acronym for the four stages of an improvement cycle: plan, do, check, and act.
In the 1990s Deming changed the name for the method that he used with clients from PDCA to PDSA. The new name reflected his preference for a change from “check” to “study” because with a “check”, one might miss something. However, PDCA has remained the most commonly used term in practice today.
Let’s now take a closer look at each step in the improvement cycle.
The Four Stages of PDCA
Plan
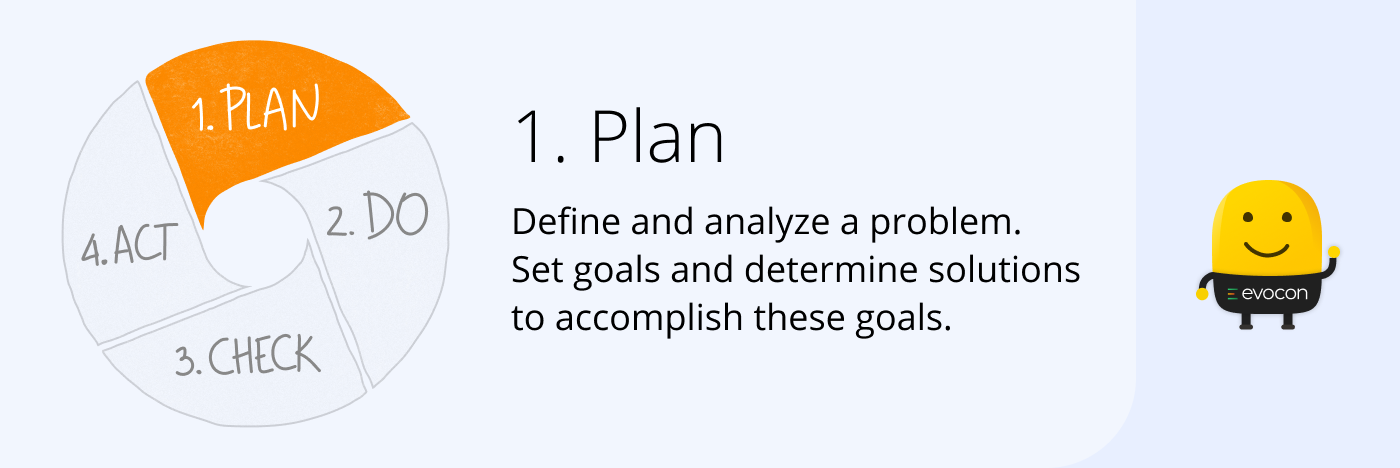
The key aim in the first step of PDCA (planning stage) is to develop an intimate familiarity with the current state.
Learning about the process can take many forms, including conducting research and gathering data on various factors of the current situation: suppliers, inputs, process, outputs, and customers (SIPOC). You will need to determine, agree, and define issues and to evaluate potential strategies and actions that can overcome process issues.
Specific steps in the Plan stage
- Define what the process does and identify the start and endpoints.
- Describe the process: list the critical tasks performed and sequence of steps, people involved, equipment used, environmental conditions, work methods, and materials used.
- Identify everyone involved, such as operators, suppliers, and any external and internal customers.
- Understand and document customer expectations: what the customer wants, when, and where.
- Understand the process better by gathering any historical process performance data available or collecting current state data. If you have not already implemented machine monitoring, Evocon can save you considerable time with this step as it automates data collection and visualization.
- Learn and document any perceived problems associated with the process.
- Identify the root causes of problems and describe the impact on performance.
- Develop solutions that correct the root cause of the problems and prevent a recurrence.
- Select the best solution.
Do
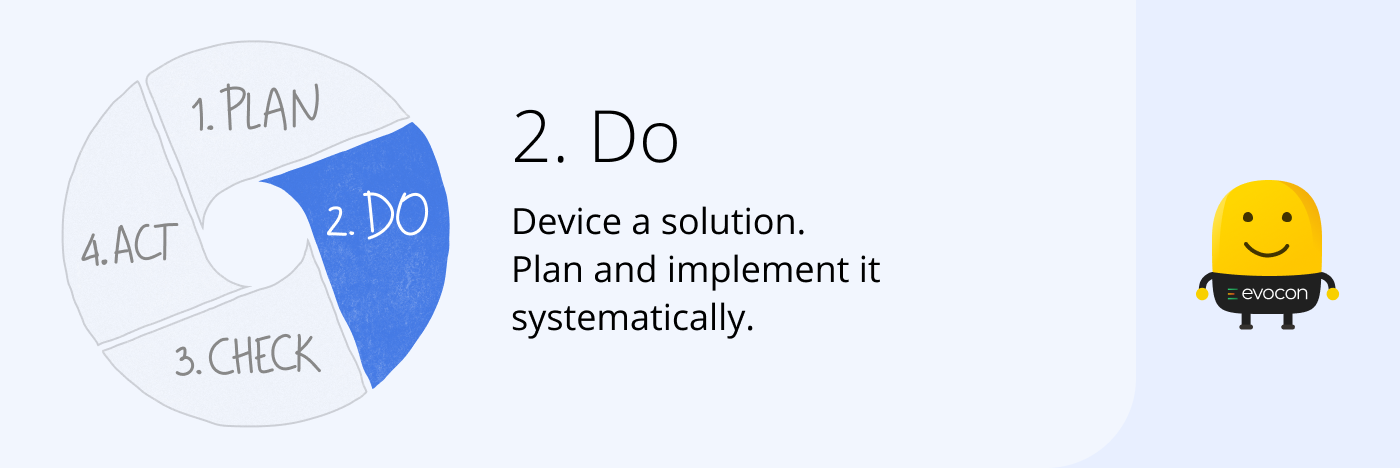
The “Do” stage is when implementation begins on a small scale.
Small scale implementations can take the form of a limited pilot within a more extensive production process, or perhaps with a targeted group of clients. The point is to test the effectiveness of solutions by gathering and evaluated objective data.
Specific steps in the Do stage
- Conduct a pilot study or experiment to evaluate the possible solution(s) effect.
- Identify steps to measure the effectiveness of the improvements or solutions tested.
Start improving your production process
Get the tools needed to reduce costs and improve productivity. Free for 30 days.
Check
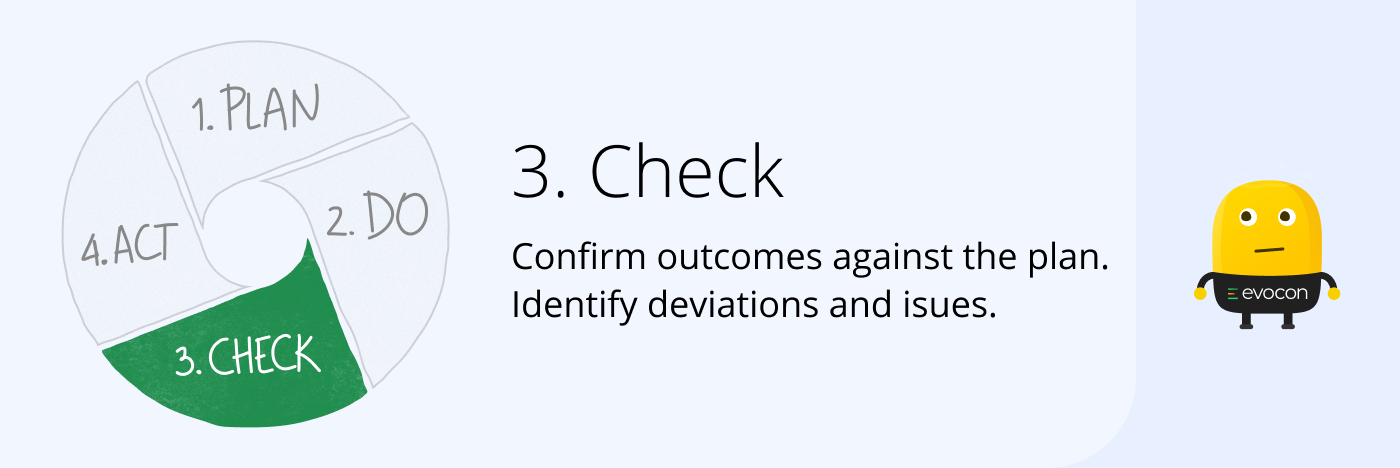
The “Check” stage in PDCA determines whether the solution is working by assessing the outcomes, documenting learning, and determining whether additional problems or opportunities are required to be addressed.
Specific steps in the Check stage
- Examine the results of an experiment or pilot.
- Determine if the effectiveness of the process has increased.
- Decide if further testing is necessary.
Act
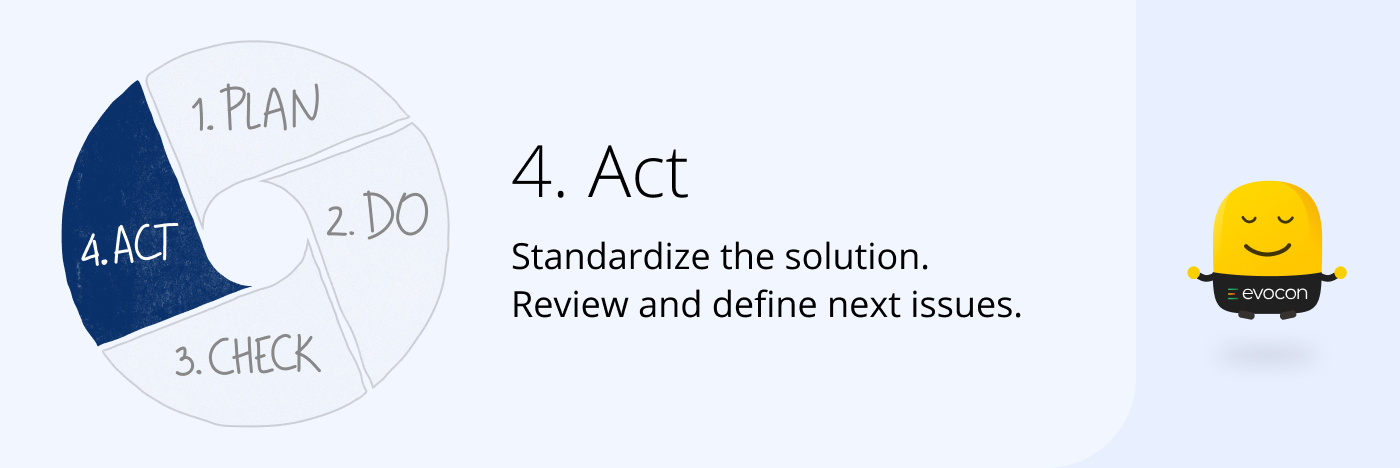
The “Act” stage is the last step in the PDCA cycle. The key focus here is to refine and finalize the changes that will be introduced.
Once standardized, the improvement must be established as the new “best practice” within the company.
Specific steps in the Act stage
- Select the best change or solution.
- Develop an implementation plan that explains who needs to do what and when.
- Formalize the solution, for example, by revising work instructions.
- Set up a method to track and monitor the performance of the process.
Conclusion
In this article, you have learned about the four stages of PDCA: plan, do, check, and act. You should now have an understanding of what specific steps you can take to get started with each stage.
Once you are comfortable with using PDCA a next step for you to consider is a free trial of Evocon. Evocon digitizes your production with machine monitoring and harnesses your process data through automation and visualisation. The result is a shorter improvement cycle time. This means more improvements can be realised without adding additional resources and in the same amount of time.
Sources
- Specific steps adapted from Small Business Guidebook to Quality Management, Office of the Secretary of Defense, Quality Management Office, Washington, D.C. (1998)