For many manufacturing problems, but particularly for simple ones, 5 Whys Analysis is an easy-to-use and effective method for uncovering root causes. Moreover, you can apply the concept immediately and get a lot of people involved.
What Is the 5 Whys Analysis?
The point of the 5 Whys Analysis is to get to the root cause of the problem that for example, undermines productivity, and to explore potential solutions. You do this by asking “why” questions recursively about the issues until you identify a possible root cause.
To better understand the process and benefits of root cause analysis, we recommend exploring the articles below:
Learn More: Benefits of Root Cause Analysis in Manufacturing
Learn more: How to Perform Root Cause Analysis in 6 Steps
Start improving your productivity
Track and analyze the performance of all your production shifts across different stations, factories and countries. Free for 30 days.
How to Put the 5 Whys into Practice?
Since the method is really simple, we will use an example to illustrate how the concept works and how you can start using it today.
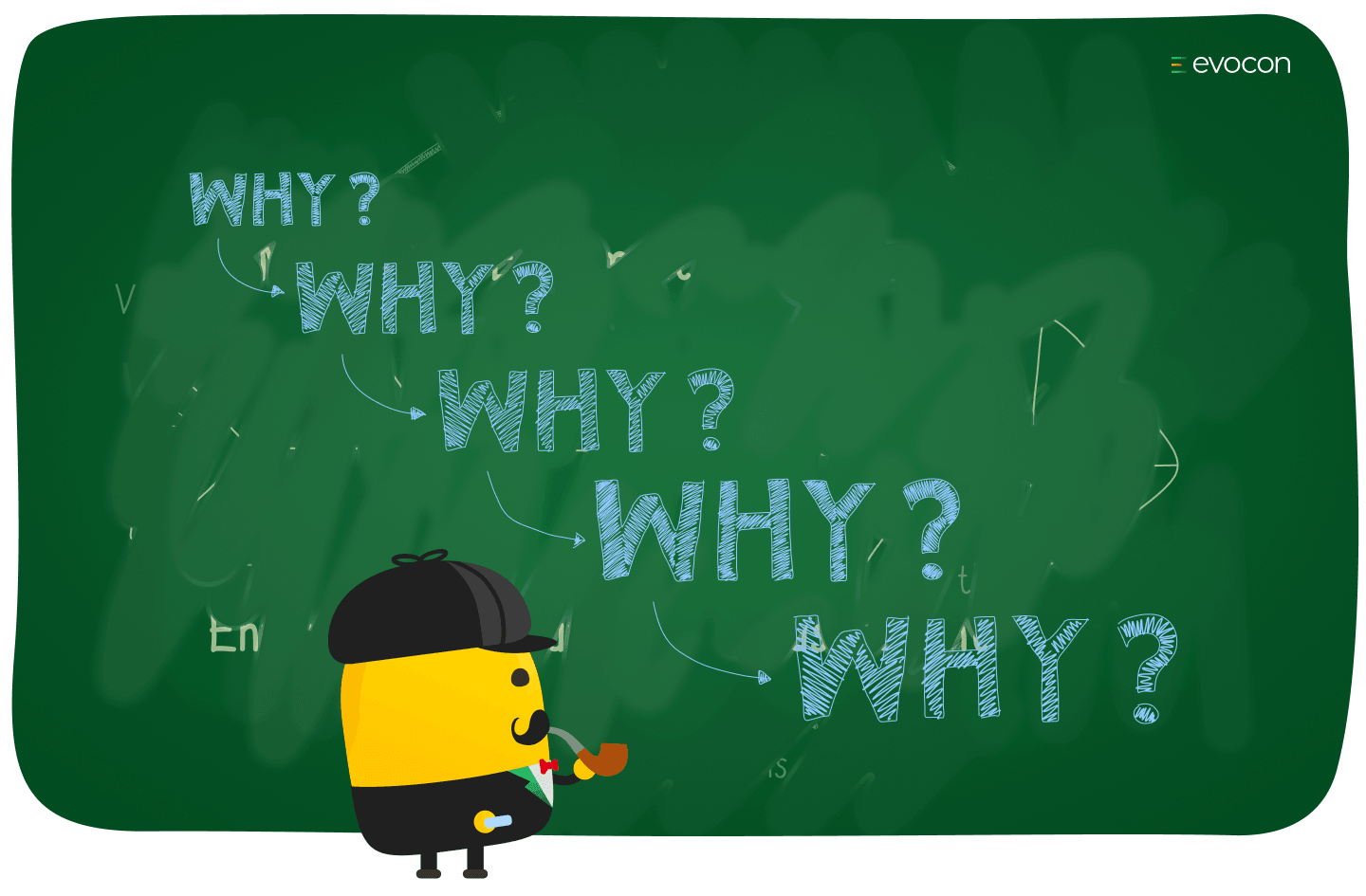
Example – Finding the root cause of “Waiting on parts / Material missing”
The following example best illustrates the concept for a common problem in production: Waiting on parts /material missing.
- Why 1 – Why is the material missing? Raw material stock is empty in the warehouse.
- Why 2 – Why did the warehouse run out? The buyer in purchasing did not purchase enough.
- Why 3 – Why didn’t the buyer buy more? The buyer purchased enough stock to cover the demand forecast, and it was wrong.
- Why 4 – Why was the demand forecast wrong? Forecasts, by definition, are inherently not accurate.
- Why 5 – Why can’t the forecast accuracy be improved? It can with investment in new technology and training.
Solution: In this case, the machine might not sit idle if the plant invests in new technology and training.
It is important to note that you may not always have to ask why five times to uncover the root cause. Usually, it is evident when you reach it by using good judgment.
Main Takeaway
In this post, we have explored the concept of the 5 Whys. We have demonstrated how to apply it by walking through a simple example. Further, you can combine the method with Fishbone Diagrams to discover potential causes that reduce productivity.