H+H is a leading provider of solutions and materials for wall building. In recent years, they have expanded and leaned into technology to digitalize their work streams. With the introduction of Evocon, they discovered the importance of having an easy-to-use tool that provides relevant, accurate data across the company. In this case study, we gain insight into H+H’s factories in Central Western Europe (CWE), Poland, and the UK, thanks to the participation of Elke Heidenreich (H+H CWE), Karol Sokołowski and Łukasz Biłas (H+H Poland), and Leyton Austin (H+H UK).
Introducing Evocon: A New OEE Software Program for H+H
Karol Sokołowski, the Production Director for CSU at H+H Poland, played a key role in bringing Evocon to the company. With firsthand experience using Evocon at Saint-Gobain Weber, Karol was already familiar with its benefits and knew it could address many of the challenges H+H was facing. He was confident that implementing Evocon would make a significant impact on the company’s operations.
Like many manufacturers, H+H Poland relied heavily on paper reports and spreadsheets which made it much more difficult to easily create reports and analyze daily data. This led to many inconsistencies due to human error, as well as taking a long time to process. Karol knew that to solve this issue, they would need to find an easy-to-start data collection and reporting system. Though he was aware of Evocon, he asked around the different sites to see what solutions they were using. He found that there had been attempts to implement automated systems, but they proved to be particularly complicated and expensive to set up and run. They were often far too complex, offering too many features that would likely never be used. That’s why he turned to Evocon – “Evocon is the best product to start reporting in an automated way and to teach operators the connection between data collection and reporting.”
H+H Poland pilot program
Karol planned a pilot program at H+H Poland, starting with one machine in a single factory. This method of introducing Evocon has proven successful, as the system’s value and trust are built with results before expanding to more machines and locations. After starting the pilot, it took a few months to collect and analyze the data and see the initial improvements. Karol then presented the results to the management board in Poland. Along with the data and results, the board was impressed with the feedback from operators and factory managers. The decision was then made to roll out Evocon to one other location in Poland.
About a year later, he presented the results from the two factories to the board at the group level—the board managing H+H’s operations across borders. Initially, the intention of the presentation was not to show Evocon as a solution for the whole group, but just to provide data from the Polish factories.
So, how did Karol’s presentation make the board decide that Evocon should be implemented throughout the entire organization?
“It was the Wow-Effect – they (the board) could see the data in a very nice way, and it was data they could believe in.”
– Karol Sokołowski, Production Director for CSU, H+H Poland
The board appreciated the clear and concise graphs and how Karol was able to extract and present the data quickly. The ease and depth of the presentation, along with the straightforward and inexpensive implementation, customizability, and simple onboarding, made the board consider implementing Evocon across the company. This was when they decided to introduce Evocon to H+H factories in the rest of Poland, as well as other countries.
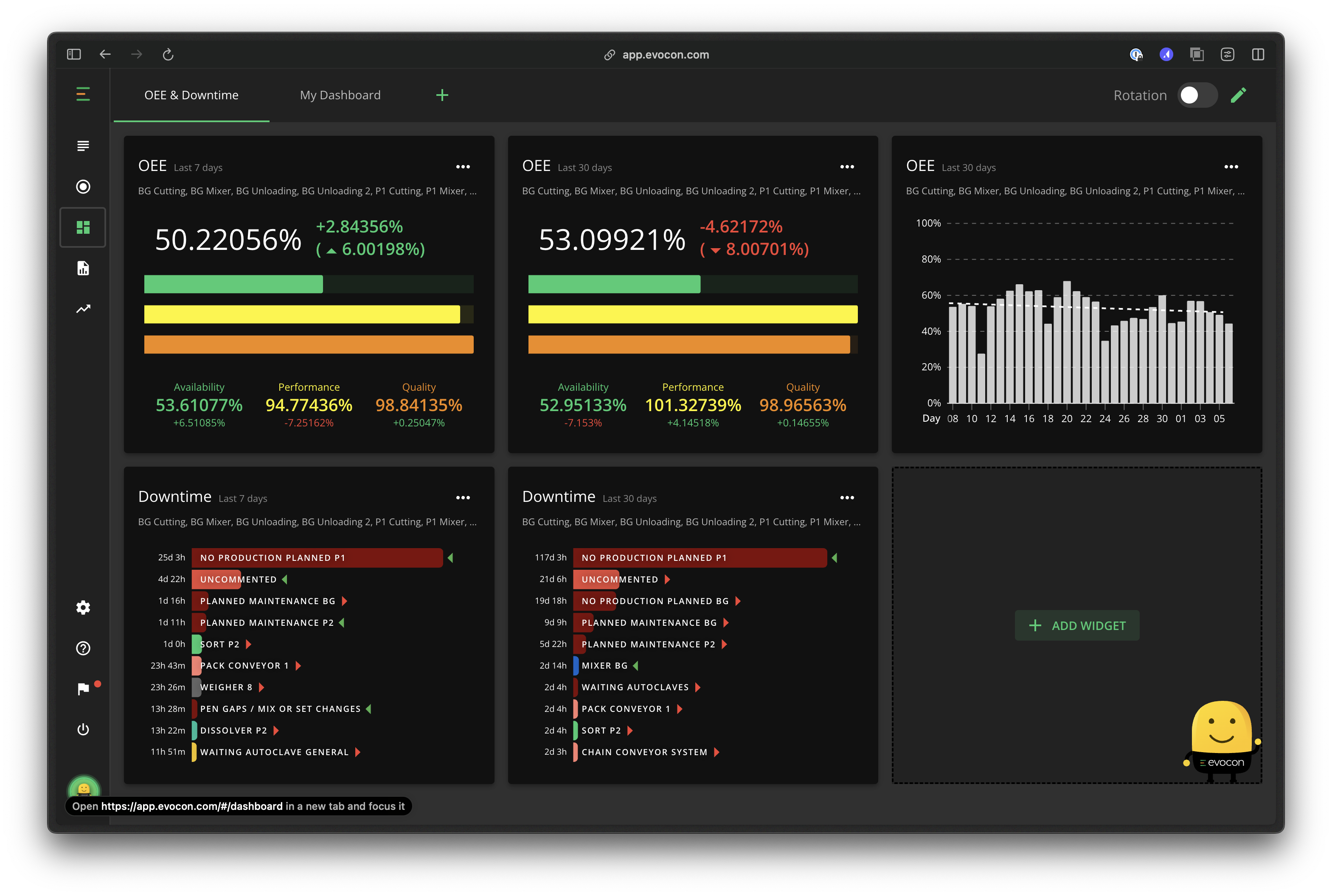
Evocon’s International Implementation
Expanding Evocon at H+H Poland
Soon after the pilot program was completed, and the decision was made to implement Evocon across borders, Łukasz Biłas joined H+H. Łukasz helped them introduce Evocon to the remaining factories in Poland.
When he joined, Łukasz found that H+H previously had the same issues as many companies without a production monitoring system in place have. All reporting was on paper, and if you needed to find the reasons for problems with machines or production, you had to ask the operators and hope they remembered what happened accurately. Now with Evocon, they have the data in the system ready to extract.
One of the main benefits he sees is when it comes to prioritizing improvement projects. Previously, if they wanted to select a project to work on, they would have to collect feedback on paper forms, manually upload all of that information to Excel, and then create charts to understand which problems they should tackle next. This workflow has been improved and simplified using Evocon.
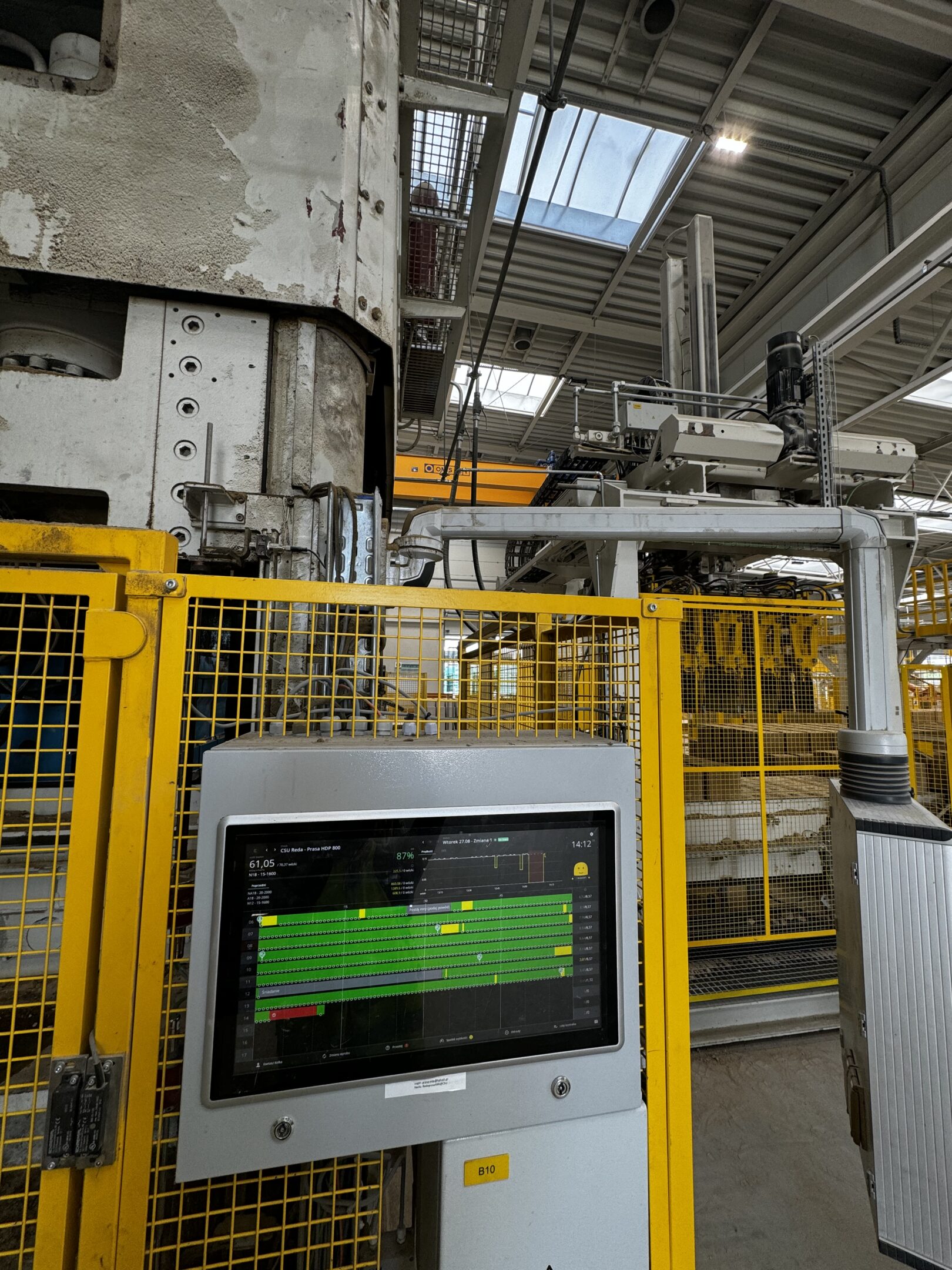
With Evocon proving successful in Poland, it was time to broaden the scope and introduce it to more H+H factories. It was then introduced at H+H facilities in CWE and the UK.
Evocon at H+H CWE (Central Western Europe)
In CWE, they began the implementation with a pilot program at four of their German sites simultaneously. They first installed Evocon on their main machines focusing on production and packaging.
The pilot sites appreciated the new tool, and found it “easy to handle, with very good involvement and acceptance by the operators, and very good analysis”. Building on this success, they soon introduced Checklists, another Evocon tool, which proved to be one of the best solutions for performing routine checks, shift handovers, and maintenance activities in their daily and weekly routines.
After the successful implementation at the four pilot sites, they decided to roll out Evocon in all other CWE sites in Germany and Switzerland. The feedback from site managers was overwhelmingly positive, highlighting the tool’s ease of use, reduction in paperwork, and the fast overview it provides of machine-specific issues.
Elke believes it exceeded all their expectations. In addition to Evocon as a system and its features, the site managers have all been pleased with the speed of support they receive.
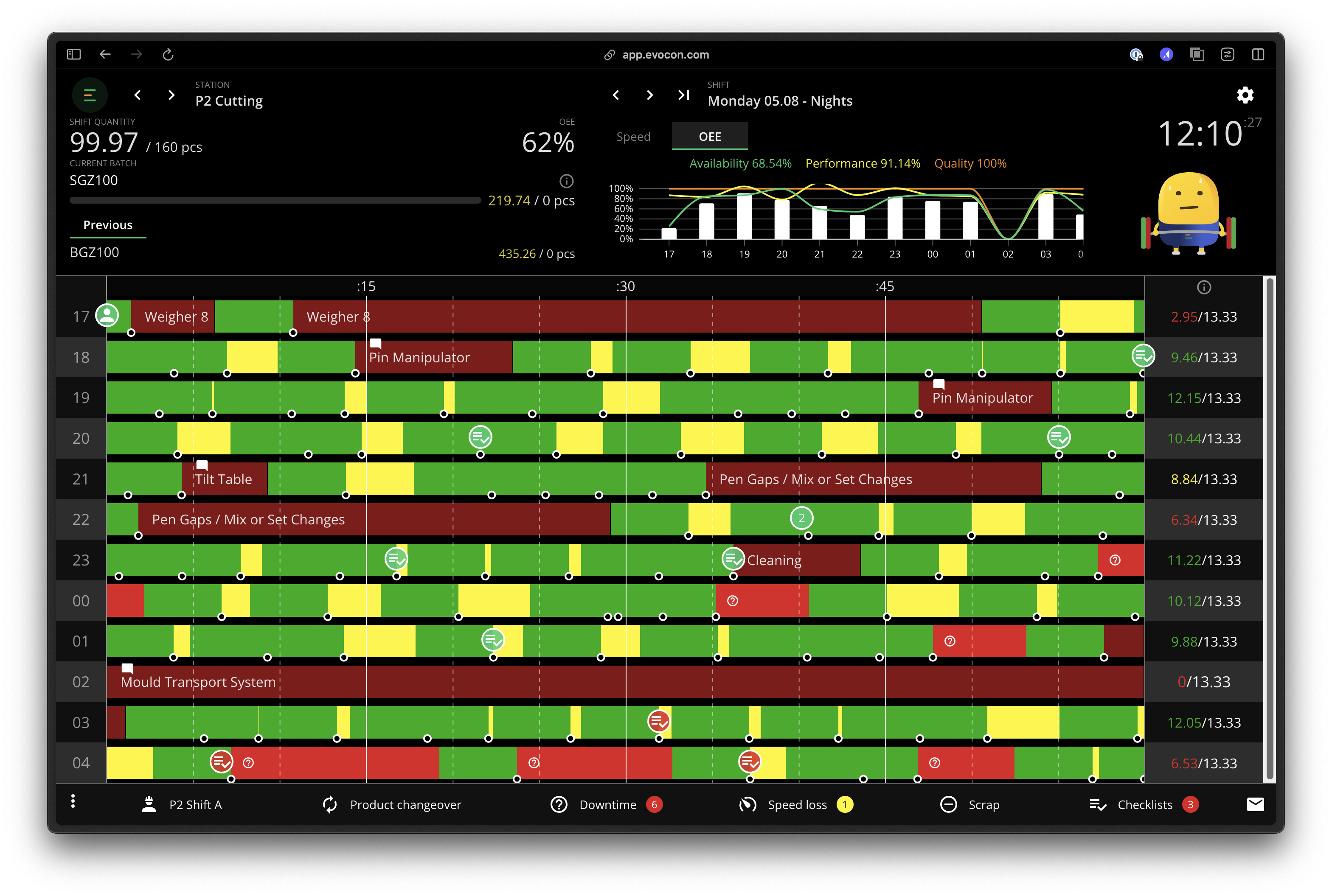
Evocon at H+H UK
H+H UK considered Evocon a potential solution as a result of Karol’s presentation. In Leyton and the UK team’s initial experience, they saw that it was “intuitive, very easy to use, and very engaging.” They looked at how the system was rolled out in Poland and CWE, learned some lessons from their pilot programs, and began developing their implementation plan.
“Right from the start, Evocon has been great! The support from Evocon has always been absolutely fantastic.”
— Leyton Austin, Continuous Improvement Manager, H+H UK
They noticed how Evocon provided fast and easy data access for factory and continuous improvement managers, and improved efficiency for operators. This ease of access saves time and simplifies the decision-making process.
“You just have to simply log in instead of going to the plant floor to see what is going on.”
— Leyton Austin, Continuous Improvement Manager, H+H UK
Since then, it has been an integral part of their organization. Today, H+H has implemented Evocon at 23 factories across Poland, Germany, Switzerland, and the UK. Elke mentioned that since it’s been implemented, she always recommends Evocon “because of the setup, because of the reaction time,” and for her, it’s “one of the best tools I’ve ever worked with.”
The Key to Change Management – Operators
Change management is vitally important when implementing any new system in the workplace. Employees are used to their working methods and can be skeptical about how valuable a new tool might be. Factories are the same, with skepticism and distrust in new systems and technologies.
The ability to use Evocon from the shop floor operators to the executives in the boardroom was essential in implementing Evocon across H+H. For operators, there are various reasons that Evocon is beneficial:
- Easy to use: Evocon is built with the end-user in mind. Many systems can appear complicated, instantly making them less favorable for new users. This first hurdle is cleared instantly with Evocon’s visual, easy-to-read interface and simple functionality. The system is intuitive and displays the information the operator needs in real time. As Leyton found it in the UK, “The user-friendliness from the shop floor’s point of view is fantastic. The development of the product is fantastic.”
- Less paperwork: Using Evocon to track downtime, speed loss, and scrap means less manual work for operators and shift leaders, who would otherwise have to record everything manually. With Evocon, users quickly learn how much of their old manual workload is covered automatically. This means more time can be spent improving systems and workflows rather than manually tracking production.
- The human touch: Time and again, we have found that Mr. Evocon, our favored mascot and the heartbeat of your factory, makes a substantial difference to the factory workers’ day. Humanizing the feedback process in this way improves the adoption of Evocon and positively impacts people’s engagement on the shop floor. This was the case in CWE, as the operators have said: “It’s really nice that the guy is smiling.”
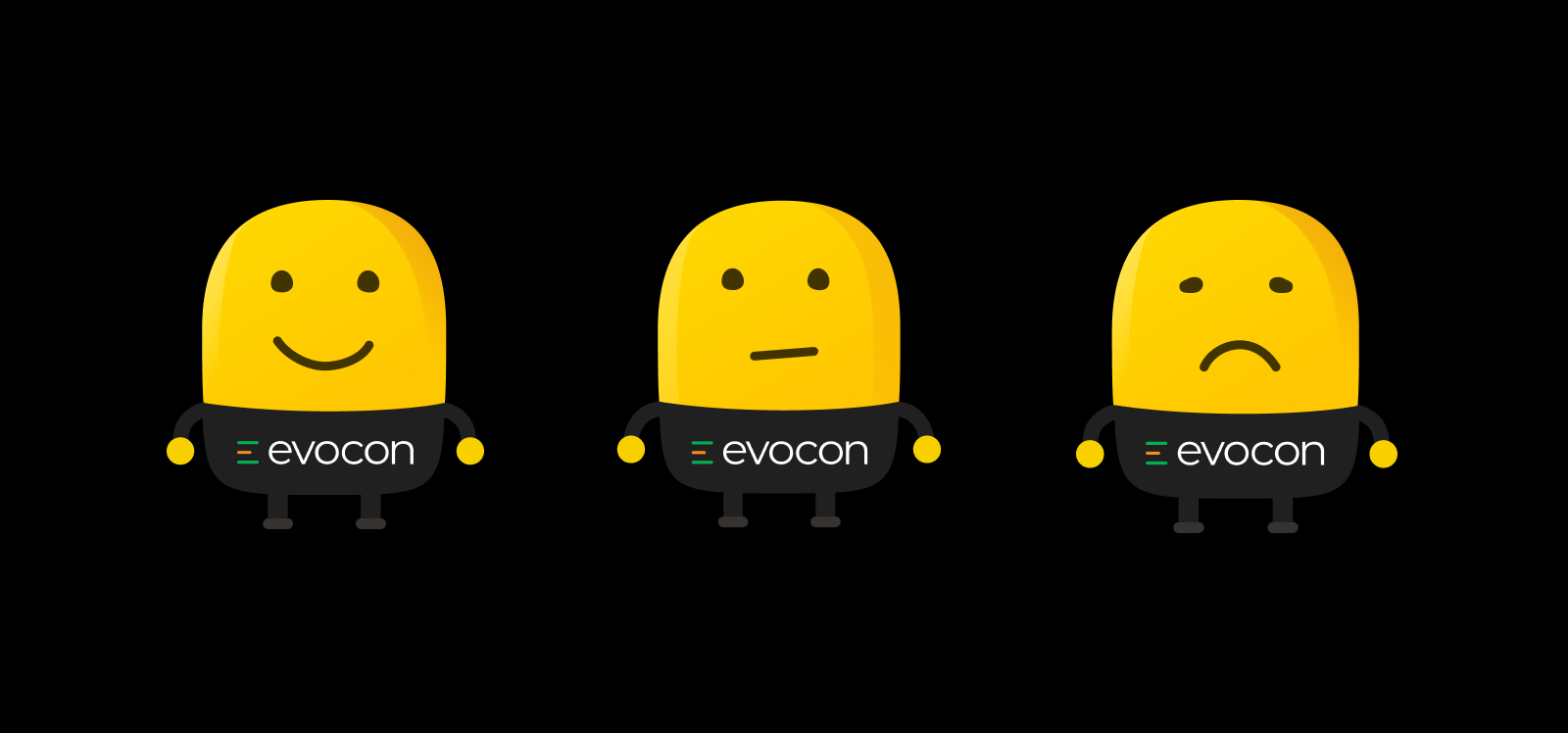
In the case of H+H, the operators played a crucial role in the smooth implementation of Evocon across multiple locations. As they experienced the system’s benefits in one factory before expansion was decided, their positive feedback and increased efficiency were instrumental in driving the adoption of Evocon at other sites. This bottom-up approach, where operators could see the immediate impact on their daily tasks, made it easier for teams across the company to adjust to the new system. With a proven track record and evidence that the software worked, the decision to expand its use was based on tangible results rather than introducing an unknown system across all locations at once.
Uniting the Shop Floor and Management
By engaging operators in the production monitoring process and discovery of actual issues, operators started to see how their efforts contributed to the decision making process. Having access to the data also meant they could display and prove any issues. For example, in CWE, they have found this to be one of the most significant benefits.
“We can use them (downtime reasons) as reasons to get money for investments. That is the biggest benefit that they see. Not only do they say, ‘I know my problem, I can tell you that I have a problem,’ now they can prove that they have a problem.”
— Elke Heidenreich, Continuous Improvement Manager, H+H CWE
Through the operators’ input, big and small changes are made. The board uses the data added to Evocon on the shop floor to make decisions affecting the entire company. This, in turn, gives the workers at H+H a sense of togetherness, as they know that their work and feedback are being taken seriously and making a significant impact.
The implementation and adaptation to Evocon we have seen in H+H is remarkable. They are the perfect example of how traditional manufacturing companies can evolve and improve their processes through digitalization. By using Evocon, the operators feel more included in the decision making process, and involved in company decisions. At the same time, management has access to fast, accurate data. This collaborative approach is why H+H has been able to become more efficient and effective in what they do.
And to leave you with one of our favorite quotes from Łukasz – “Tell me if you ever find something easier to use than Evocon.”