Torm Metall, a manufacturer with 130 employees in Estonia, specializes in creating parts and assemblies from aluminum and stainless steel. More than 90% of their sales are custom-made according to customer drawings and specifications. Moreover, since they export 30% of their products, production efficiency is always in focus.
What Necessitated a Change?
Today, rapid advances in digital technology are transforming the manufacturing landscape faster than ever before. To avoid losing ground to agile competitors, manufacturers are under constant pressure to identify bottlenecks in production and find innovative solutions to make every process better, faster, and more efficient. But the first challenge is figuring out exactly where to start. Production digitalization is one possible answer.
In 2016, a production manager at Torm noticed that one of their machines was operating at only 35% of capacity. It spent the majority of its time sitting idle, causing a worrisome drag on productivity. The manager then started asking questions to find out why the equipment wasn’t working up to capacity. Unfortunately, nobody really knew the answer.
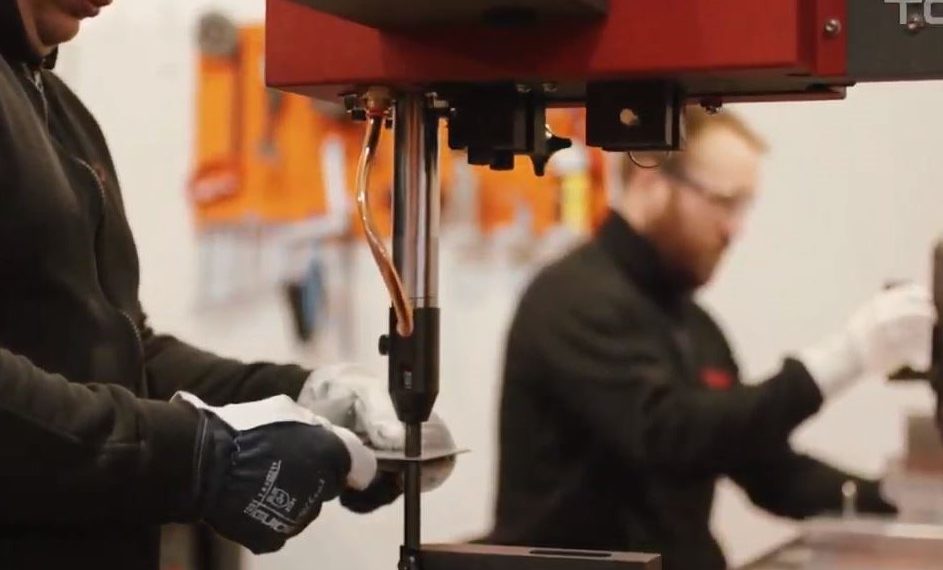
Without data on OEE on how the machines were actually being used on a day-to-day basis, there was no way to know how to fix the problem.
So Torm Metall set out to analyze machine downtime, identify machine breakdown causes, and find ways to eliminate inefficiencies wherever they could.
Production Digitalization Provides Much-Needed Transparency
To make the first step in production digitalization, Torm Metall turned to another Estonian company, Evocon. The OEE software designed by Evocon offered them the ability to:
- automate the process of data collection from each workstation,
- track machine downtime,
- and gain real-time information about their entire line of production equipment.
With that knowledge in hand, they would be able to analyze the efficiency of every operational step and system, find problems, and use the collected production data to reduce stoppages and make their business more competitive.
Data is the key to production optimization
The company started by connecting a water jet cutter and two laser cutting tables via PLC to Evocon to measure the exact time usage of the tables. By comparing those numbers to the amount of work time originally planned, they could improve their planning to streamline the workflow.
The company also installed separate computers or touchscreens near each workstation. Now, whenever there was an unexpected stop, operators could simply select the machine breakdown cause from a predefined list. Whether it was a technical fault or something else that interrupted the production at that station.
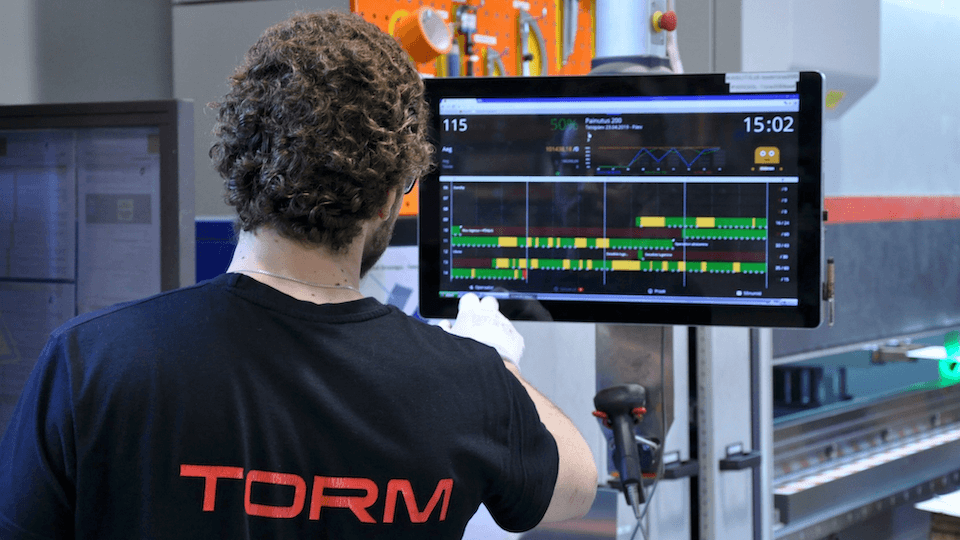
Once they began collecting data, the company was able to analyze it and develop a clear overview of how the production equipment was actually being used throughout the day. The transparency they gained from tracking their equipment downtime and OEE gave them a better idea of where the problems were occurring. It also led to new insights about how to solve them.
Depending on where and why a problem occurred, the solution sometimes involved changing the setup of a particular unit. In other cases, it required making a broader organizational change to the process, such as rearranging the order of operations or moving tools across the floor to a different location. With this, they started to realize the benefits that production digitalization would give them.
Digitalize your production
Gain the visibility required to drive improvements and boost performance. Free for 30 days.
One simple change can double production efficiency
In the case of the idle machine that the manager noticed at the start of it all, the problem turned out to be simple. After performing root cause analysis on the issue, they discovered that after the unit had completed a job, it was stalled until someone came along to take away the finished products. Once the operator unloaded the material, the workstation could resume operation. Otherwise, it would sit idle for several hours a day.
The solution involved a simple logistical change. The team added a worker to assist the machine operators. He would help with offline tasks, unloading the finished parts, and loading of new materials. The results were striking. Before, the machine had been operating at only 35% of capacity. But with the added worker, uptime quickly jumped to 70%, doubling the output.
Production Digitalization Offers a Competitive Edge
Today, manufacturing processes at Torm Metall run smoother than ever before. They now have 12 individual stations set up with OEE tracking and displays with Evocon to continuously track the efficiency of the workflow. Monitors on every unit display key indicators, enabling real-time monitoring of the production process. That helps the company make improvements on the fly and track their effectiveness.
In the near future, the company plans to integrate its production data with its ERP system.
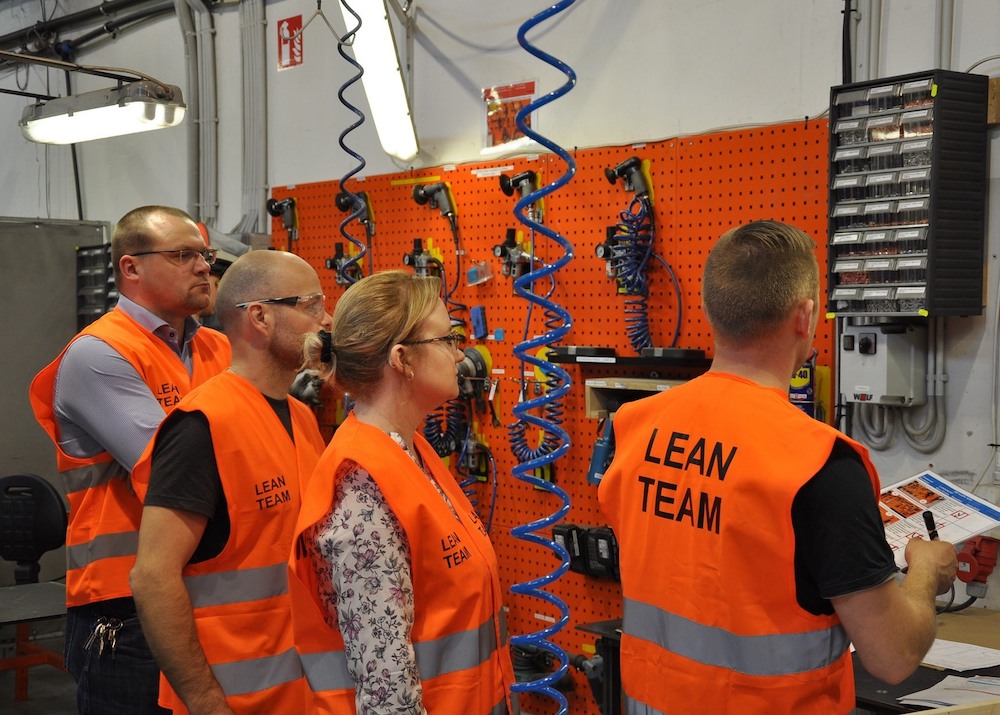
As Torm Metall discovered, production digitalization is the key to much-needed innovation in a rapidly evolving marketplace. Thanks to Evocon’s OEE software, they can now analyze their workflow and have the transparency they need to truly understand what are the various problems they have. And find innovative ways to address them. It also helped them measure the effectiveness of each change they made. So they knew exactly whether or not they were making progress.
“Digital technologies are advancing rapidly. If businesses do not take advantage of their opportunities and keep their finger on the pulse, then they’ll already be left behind tomorrow.”
Torm Metall
Encouraging transparency and sharing of knowledge between IT and manufacturing is the best way to increase productivity and achieve business goals. It also helps become more competitive in a constantly changing manufacturing landscape.