Energy and production efficiency both help manufacturers become more sustainable. In this article, we share how ISO 50001 works and why it’s worth considering merging your energy consumption data with OEE.
What is ISO 50001?
The International Organization for Standardization, commonly known as ISO, is an independent, non-governmental organization that develops standards for companies. These standards ensure a common and globally recognized level of best practices as well as guidelines for meeting them.
The ISO 50001 standard is developed to help organizations continuously improve energy efficiency, save costs on energy and reduce greenhouse gas emissions. Like other ISO management system standards, ISO 50001 follows the “Plan-Do-Check-Act ” process for continuous improvement.
Why Do Manufacturers Implement ISO 50001?
This framework is used by many manufacturers. Hence, in this article, we want to offer valuable insights on the ISO 50001 benefits, and how Evocon can help you reach the goals you’ve set out as part of your energy consumption reduction plan.
With energy prices continuing to rise, it’s more important than ever for manufacturers to find ways to reduce the amount of energy consumed. Some companies work with ISO 50001 standard solely for the cost-saving benefits this framework offers, while some take it to the next level and proceed with getting ISO 50001 certification for their progress. For them, certification serves as a “stamp of approval” of their operations and contributes to creating a positive brand image.
ISO 50001 standard, regardless of whether the company proceeds with certification, helps create and implement energy efficiency policies, set goals, and measure the results. The main idea behind this framework is to use data to understand energy use better and continually improve energy management.
ISO50001 Implementation
For each company, the energy efficiency journey looks a bit different. Companies working with ISO 50001 often start with developing an energy efficiency policy to get everyone internally on the same page.
Next comes the gathering of data on current energy usage trends and setting achievable targets for reducing energy consumption. An essential part of the process is designing action plans to reach those goals.
The final part of the process is to measure and evaluate the results obtained.
ISO 50001 implementation examples
Below we’ve listed some of the most common steps companies take as part of the ISO 50001 energy management process. This is in no way an exhaustive list and the impact of each activity differs from company to company.
Implement new energy-efficient technologies
- Upgrade to LED lights offers manufacturers as much as 90% energy savings compared to HPS lights.
- Update the heating and cooling devices to ones that are no more than 10 years old and are using more modern technologies provides significant energy savings as heating and cooling consume half of the EU’s energy and much of it is wasted.
- Use software tools to capture the data on which machines or devices consume the most energy and when.
Track energy consumption and OEE
Evocon helps monitor your OEE and energy consumption in real-time.
Reduce energy waste
- Adjust the heating and cooling device thermostat, ensure premises are sufficiently insulated and windows and walls have the necessary shading. This can offer significant savings as heating and cooling devices are consuming a lot of energy and often provide the best results.
- Check the air compressor for leakages or reduce its operating pressure. Compressed air alone accounts for 10 percent of industrial power usage across Australia’s industrial sectors so this simple activity can provide significant energy savings.
- Regular cleaning and planned maintenance of your electrical and mechanical equipment improve its performance and consecutively increases energy efficiency.
Improve current processes
- Switch off machines and devices during break time and holidays. Some companies also introduce a device labeling system (red: do not power off; yellow: power off after confirming that there is no problem in shutting off; green: turn off the power).
- Limit the frequency of cool room access as far as practical as every time the doors are opened, the cool air escapes triggering the cooling mechanisms to work again.
- Regularly check current high-consuming devices – clean heat transfer surfaces, and check for any steam leaks in steam generator systems.
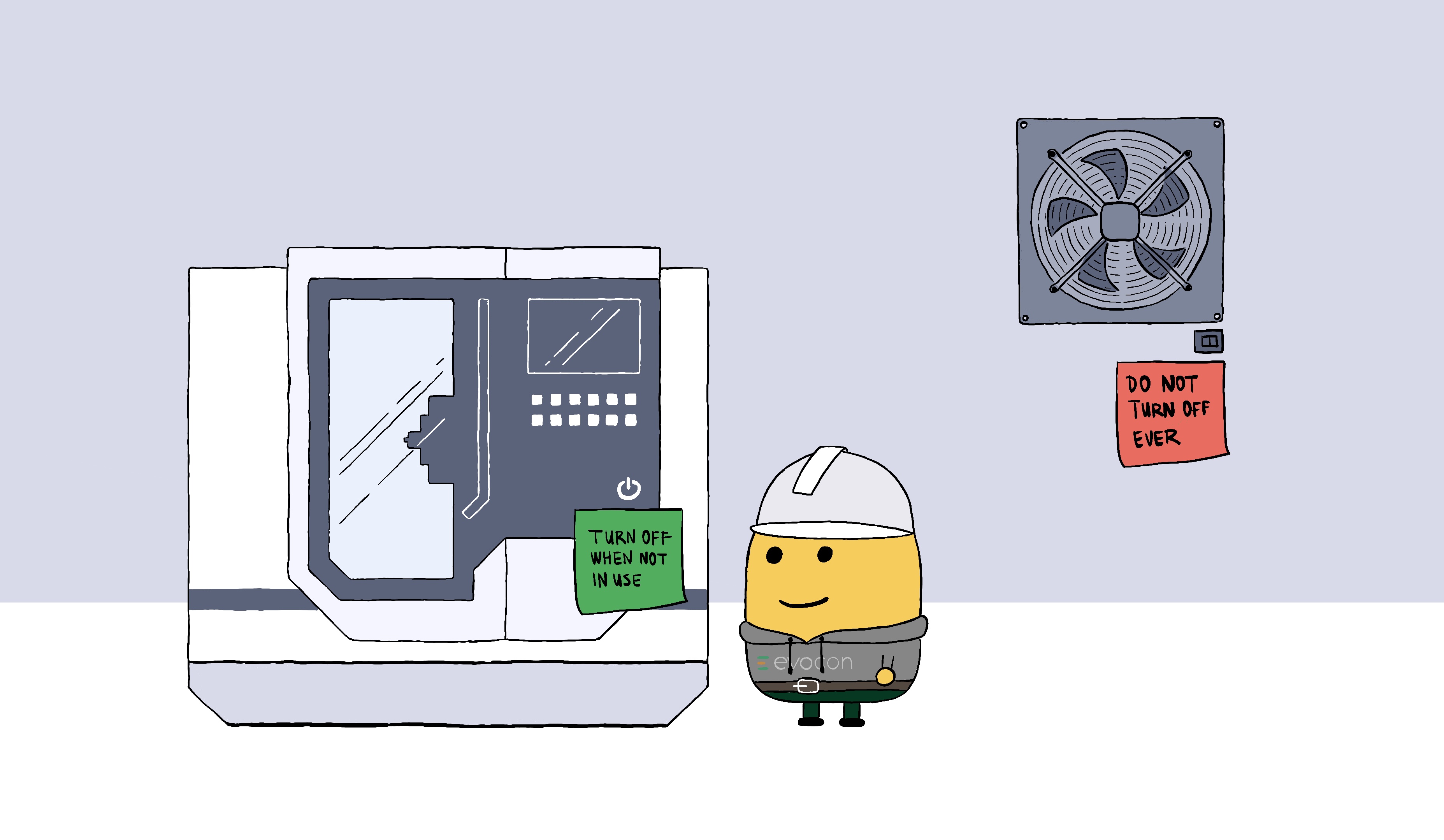
How OEE supports ISO 50001
It is increasingly common to meet production teams who have prioritized gathering data and real-time insights on what’s happening on their manufacturing floor. But some Evocon customers are taking it one step further by combining real-time energy and OEE data.
In cases where the energy used in production is responsible for a significant part of the company’s monthly costs and/or GHG emissions, this approach can pay off in a matter of a few months’ time.
For this to be executed, the company needs:
- energy consumption sensors (commonly used for ISO 50001 process);
- Evocon’s OEE and production monitoring software;
- integrate energy data with efficiency data.
This offers manufacturers a real-time view of how energy consumption correlates to the efficiency of the production (or any other production-related KPI), allowing them to quickly iterate and improve the process on the go. It can also serve as a tool to notice any issues with the machinery early on.
Example: Combining production output with kWh monitoring
One of the latest implementation examples in regards to ISO50001 is a Danish furniture manufacturer. As part of their energy goal, we set up a real-time widget that shows energy (kWh) consumption together with minute-by-minute production output.
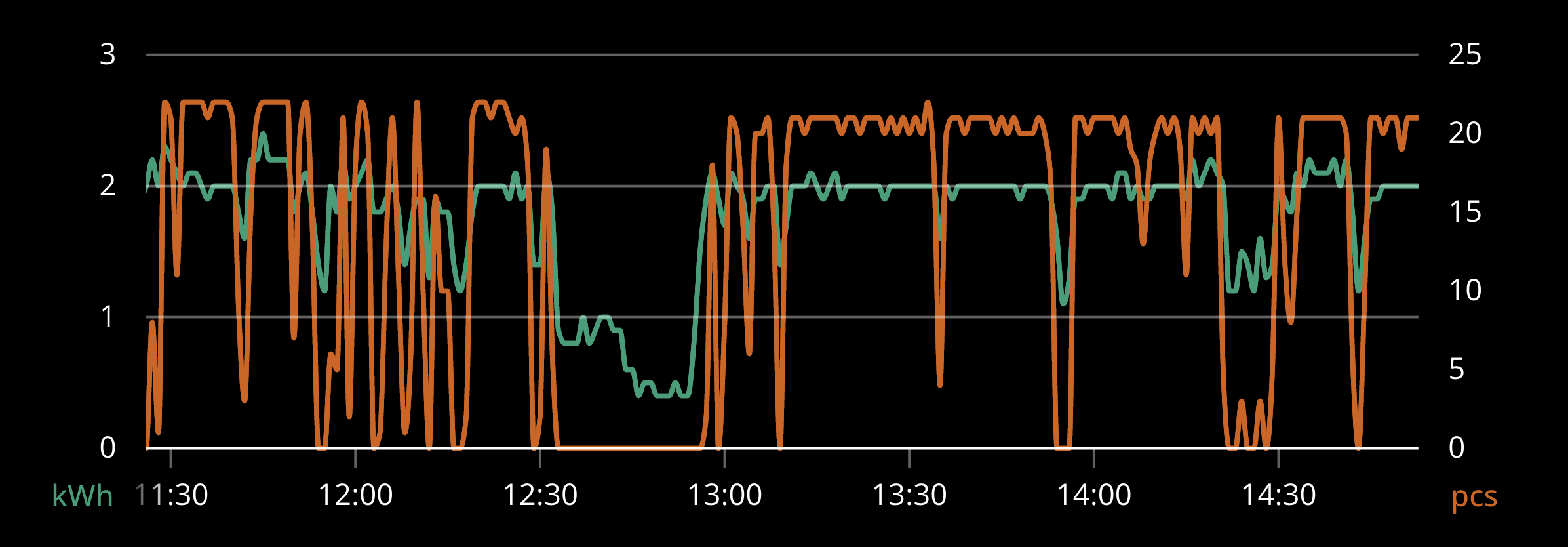
In the example above, we can see why it’s important to keep production running as smoothly as possible (in other words achieving a high OEE) because whenever a machine stops (is idle) then energy is still being consumed.
Having a visual overview of energy consumption helps operators notice when energy is wasted and take steps to mitigate that.
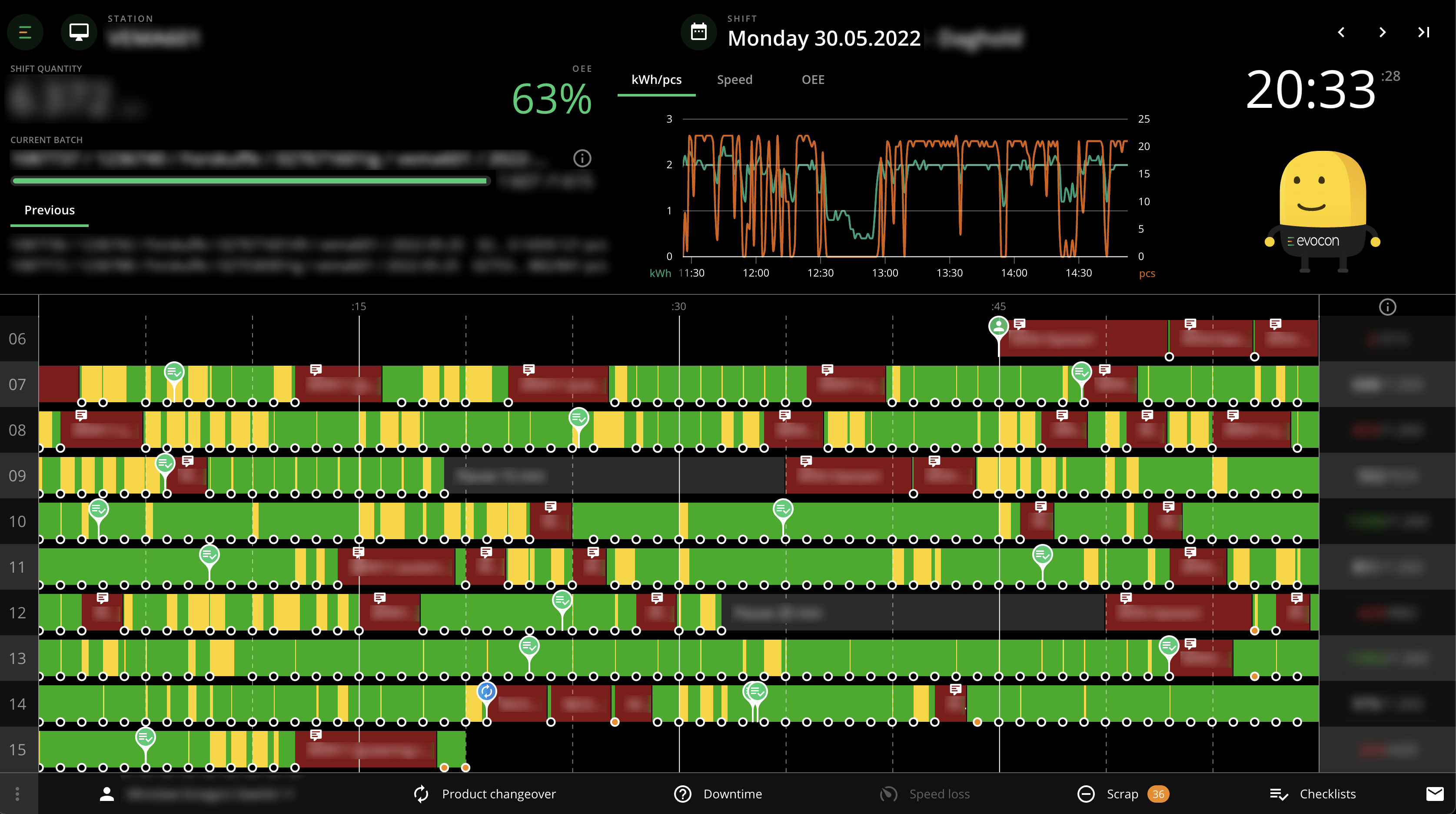