The environmental impact of manufacturing has been on top of mind for many business leaders globally, even Bill Gates. This article aims to show examples of how you can become greener in simple, achievable ways.
What Are the 10 Simple Steps That Every Manufacturer Can Take to Become More Green?
In one of the previous articles, we were exploring what it would take to run a genuinely sustainable manufacturing site (read it here). In short, it’s far from easy.
However, sustainability is here to stay. It helps your business to outperform your competition thanks to resource savings and boosted innovation. Also, it will help your company to resonate with what customers value nowadays.
Keep reading to get inspired to reach for some of the low-hanging fruit in your manufacturing plant and save resources (and money).
The list is not organized by the impact of the activity, as it depends on the case-by-case situation.
1. Switch to renewable electricity
When looking at statistics at the European level, energy is responsible for a quarter of Europe’s total GHG gasses. A similar percentage usually is found when looking into carbon footprint reports of large organizations.
A simple low-hanging fruit here is to look into who your energy provider is, your current energy mix (% of the energy that is renewable), and what options you have. The best thing is – usually, all it takes is a quick web search and getting a new contract for a greener electricity provider or plan.
2. Establish a Green Team
Opening up the conversation with employees is actually one of the most impactful things you can do to speed up your environmental and social efforts. Green Team is a cross-functional team that is collaborating on identifying current sustainability issues in the company and finding realistic and practical solutions.
Cost savings is one of the key benefits for companies as Green Team offers solutions to make your business more sustainable.
Some teams work on implementing recycling schemes, some on eliminating unnecessary packaging, and some on hosting employee training to educate team members on why sustainable business practices matter.
By the end of the day, having a Green Team helps you to integrate sustainability in business operations across several departments, fosters innovation, and boosts engagement.
3. Start recycling
Although this might seem like a trivial task, it’s actually one of the first activities any company should start with. There are two main benefits (among others) of launching a recycling program in your company:
- it helps you reduce costs by reducing the garbage collection costs (like in the case of Retmeier) that are charged by the kg of waste you produce;
- and it boosts employee engagement and satisfaction.
If you’re looking at your current or future carbon footprint, the amount of waste you send to landfills contributes to your company’s carbon footprint. So, there’s another benefit for you.
4. Encourage virtual meetings and remote work
Employee business travel is one of the largest contributors to a company’s carbon footprint. For some perspective, when the pandemic hit and commuting and travel dropped, so did carbon emissions globally (by 7%). So the impact is real, and it’s significant.
The pandemic also showed that many manufacturing processes could take place remotely – as long as there’s a way to track what’s happening in real-time. This is where Evocon came to benefit many customers, as we could provide real-time data on what’s happening on the production floor.
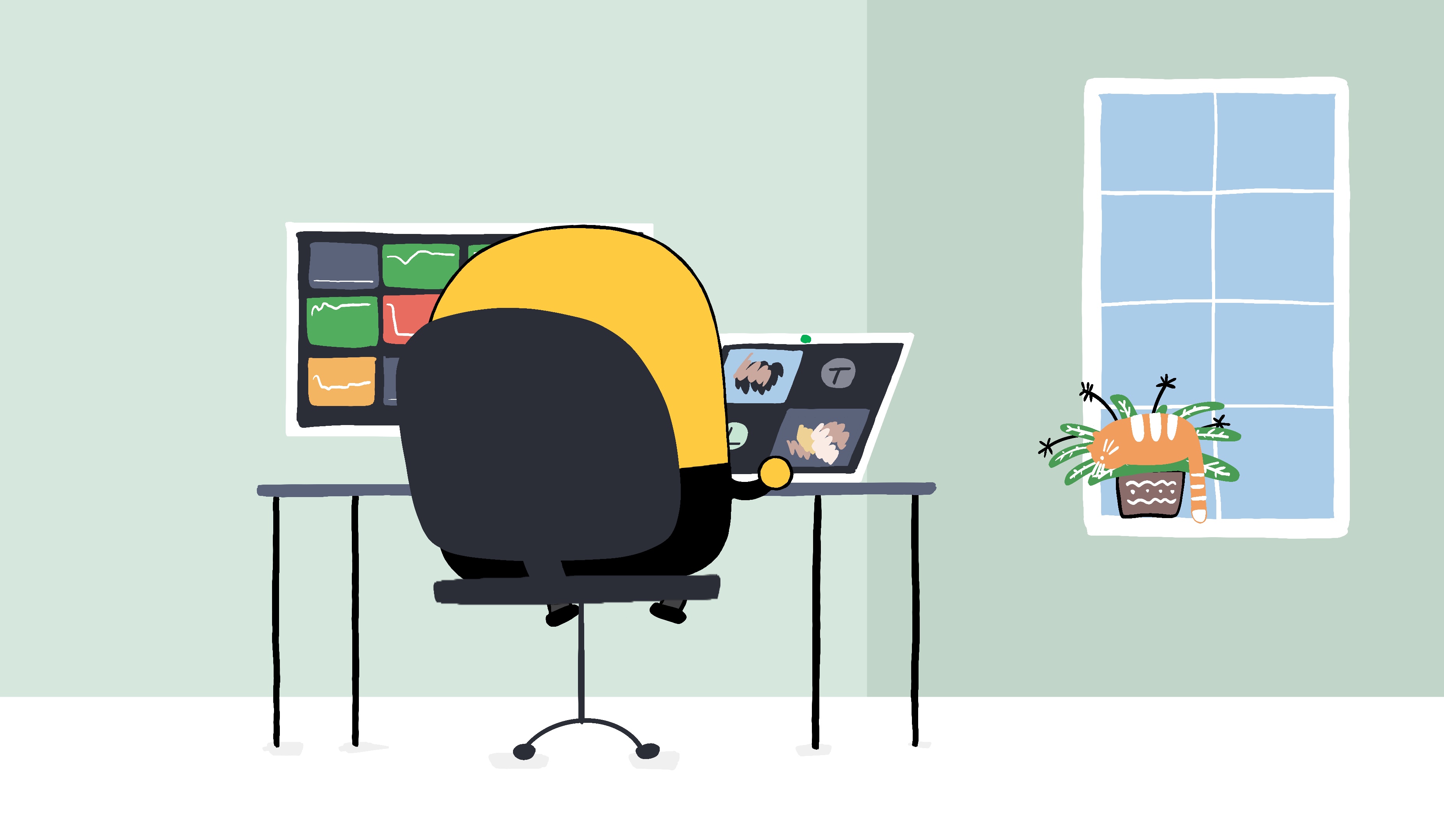
5. Eliminate unnecessary packaging
Regulatory and public concerns are driving major changes in what’s considered the norm in consumer packaging. With the increased adoption of the zero-waste movement, consumers are increasingly preferring biodegradable, recyclable, or reusable packaging. Any non-essential packaging ingredient is more commonly seen as unnecessary and excessive.
This puts pressure on manufacturers to change, especially in consumer-facing industries. The good thing is that in many companies, packaging elimination projects offer cost and time savings. Consider this: every “thank you” note in the box, every extra bag, and marketing leaflet costs you money and takes up fulfillment time.
Even small improvements in the manufacturing process can add up to huge material, time, and environmental benefits. Take, for example, the Guayaki mate tea company. They have recently reduced their annual packaging use by almost 20 tons (44,000 pounds) just by eliminating the overwrap and tea string from its single-use mate bags.
However, you don’t have to stop at the packaging. Removing unnecessary paper use in your factory can also be accomplished by switching to a paperless manufacturing system.
Paperless Manufacturing System
Get all the tools you need to eliminate waste and increase efficiency in your factory.
6. Watch out for snakes!
This time, we don’t mean the reptiles. We mean – look out for the hissing sound when passing by the devices that use compressed air for cleaning, painting, power drills, hammers, etc. You can make it part of your regular maintenance check, as it’s easier to hear issues when the machinery is turned off. Even better, set up those regular maintenance check reminders on Evocon, so you never forget them.
This is an impactful practice as an air compressor is often one of the highest energy-consuming devices on the production floor. On top of that, air leaks can waste up to 30% of the energy and reduce air compressor performance.
7. Switch to LED lights & install motion sensors
Another solution that will benefit the environment and your bottom line is energy efficiency. If you can’t start with a full-on energy audit and fancy solutions but want to get started – consider the following two simple solutions.
LED lighting is a bit of an investment, but it pays off quickly. Depending on the price of energy and the price of light bulbs you choose, the savings can add up to 80%.
On top of that, you should consider motion sensors for some areas where you often leave the light on or use them infrequently. Depending on the space you’re thinking of, a simple motion sensor’s energy savings varies greatly. For warehouses, this simple gadget can save up to 75% of energy, corridors – up to 40%, and storage rooms – up to 65%.
8. Ensure your equipment is in a good working condition
Many factors contribute to manufacturing efficiency, and most firms generally operate at 60-80% efficiency. This leaves a lot of room for improvements which help you save costs and reduce waste and fulfillment time.
Working with Evocon can help you gather real-time data and insights to understand how your equipment is utilized and if there’s any spare capacity. We can also help you track maintenance checks to avoid any unscheduled production stops.
9. Optimize your HVAC
Stricter environmental regulations and the increasing energy costs have changed how many companies work with Heating, ventilation, and air condition systems (HVAC). Two main issues with HVAC systems are:
- the refrigerant used for air conditioning (Freon has been banned due to its impact on Ozone layer depletion);
- and the use of electricity (which often is produced from non-renewable sources such as burning fossil fuels),
The best practice for this area is to upgrade HVAC systems. It is an investment, but it pays off quickly. For example, replacing an air conditioner that’s 10 years old with a new and efficient model can result in up to 40% of energy savings.
10. Track the quality of your production output
Product quality control is one of the most important areas any manufacturer can and should focus on to improve the profitability and sustainability of the business. The easiest thing to start with is tracking your quality in real-time.
By capturing quality data and visualizing it, you make it more noticeable to operators. And everything that is monitored, usually gets more attention. For example, we helped one our clients reduce potential scrap by 3x.
The next step would be to gather information on why there are quality losses and implement quality checks that ensure non-conformities are discovered in due time.
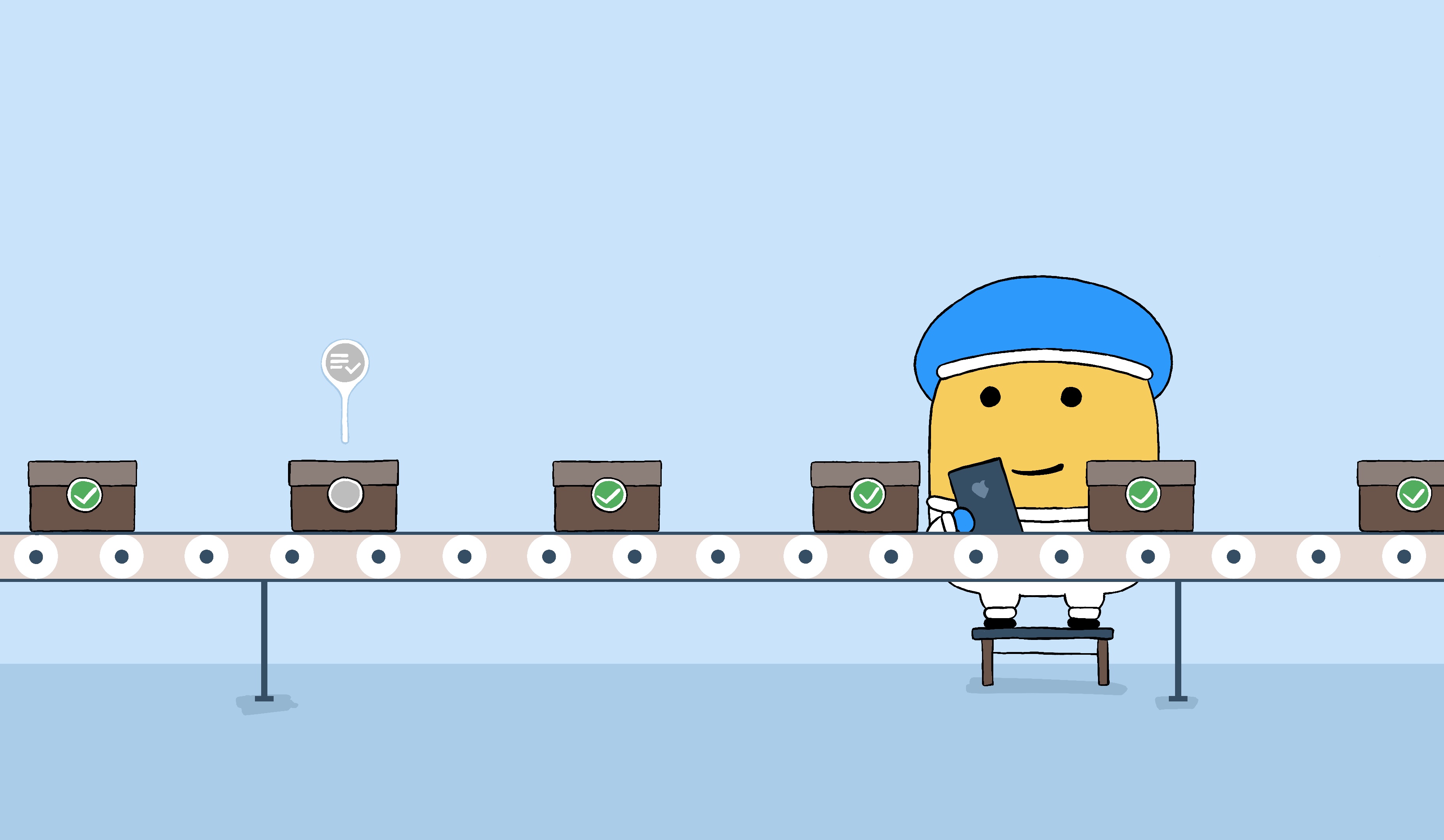
Start By Taking The First Step
Found this article useful? Share it with your colleagues and get started taking your first step.
If you would like to work on improving your production efficiency, measuring output quality, or other key performance indicators, reach out, and we can help you digitize your operations.