For decades the manufacturing industry has relied on paper for everything from engineering drawings and blueprints, to shipping labels, inventory lists, and production orders. And while paper has played a hugely important role in manufacturing over the years, technology has advanced to the point where it can completely replace paper in many areas of manufacturing. The good news for manufacturers is that switching to predominantly paperless operations affords numerous benefits, many of which we are going to cover in this guide.
What Is Paperless Manufacturing?
In a nutshell, paperless manufacturing is when firms replace their traditional paper-based shop floor processes with electronic alternatives, enabling access to information whenever and wherever it is needed. In the process, manufacturers significantly reduce the amount of paper they use and, in turn, the amount of paper they waste.
The Benefits Of Paperless Manufacturing
With paperless manufacturing, information is stored digitally, allowing it to be electronically transmitted and displayed in real time on the factory floor – all of which, as you’ll learn, provides a number of benefits for firms.
Realize your sustainability ambitions
First and foremost, paper-based factory documentation is wasteful. Consider how much paper a factory uses in a single day. While it’s hard to calculate, research shows that the global production volume of paper and paperboard was approximately 401 million metric tons in 2020 alone. While that figure represents a slight decrease over the previous year, global paper production volumes have remained relatively stable around the 400 million metric tons per year mark since 2010.
If we didn’t use so much paper, less would be needed to be produced each year. And while a large proportion of paper is recycled each year – just over 65% in 2020, according to the American Forest and Paper Association – recycling still has an impact on the environment.
The bottom line is that while recycling paper is absolutely better than throwing it away, reducing the amount we use or not using it at all is even better. Furthermore, we’ve only considered the impact of the physical paper waste. What about the time and effort it takes someone in the factory to actually deal with it on a daily, weekly and monthly basis?
Stop wasting paper and enjoy the cost benefits
An obvious benefit of going paperless is that it removes the vast majority of the costs associated with paper. In addition to the actual cost of the paper, associated savings can also be realized by not having to store, handle, print, and recycle, too.
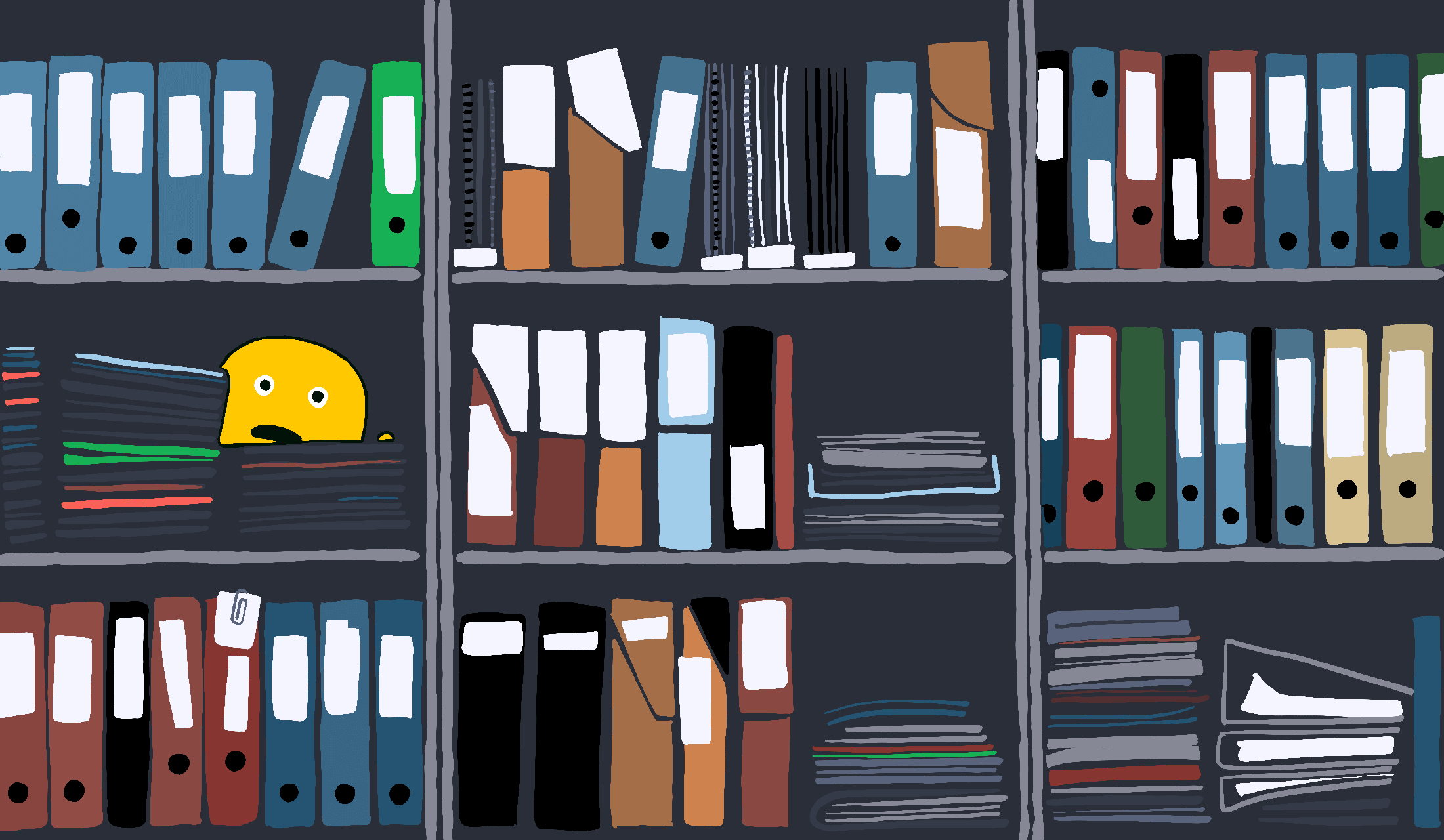
Have you ever considered how much your filing space costs you on an annual basis? How much is your printing service costing you? These potential savings could go straight onto your balance sheet.
Then there is the cost of inefficiency caused by paper-based documentation. While it is difficult to place a figure on a firm-by-firm basis, research by McKinsey (albeit dated) reveals that employees spend 1.8 hours every day just searching and gathering information.
Greater accuracy and visibility from start to end
Despite being used for decades, paper-based manufacturing documentation is prone to inaccuracies. Whether it’s a factory worker recording some wrong information, or one of their colleagues misinterpreting it, paper-based manufacturing is fraught with potential errors waiting to happen.
Consider also scenarios where changes to approved orders are needed. The initial order will have been printed and inevitably made its way to the factory floor to be produced. Amending any aspect after the order has made its way this far involves physically finding the job order and replacing it with an updated version. Even then there could be several copies of the job order and unless all of them are found and replaced, mistakes can happen.
All of this represents wasted time and effort for all involved. With paperless manufacturing though, any changes are made directly into the system and are displayed in real-time for everyone who needs to know.
Related reading: Manual vs Automated Machine Data Collection in Manufacturing
Digitalize production with Evocon
Monitor production automatically in real-time and boost efficiency with Evocon’s 30 day free trial.
Empower your workforce and encourage more collaboration
With information being seamlessly shared across multiple departments, the opportunities for collaboration are naturally increased. So, too, is the communication between different departments, bringing them closer together.
Manufacturing employees can work on documents simultaneously and in real time, further boosting productivity, improving outcomes, and encouraging a culture of collaboration across the organization.
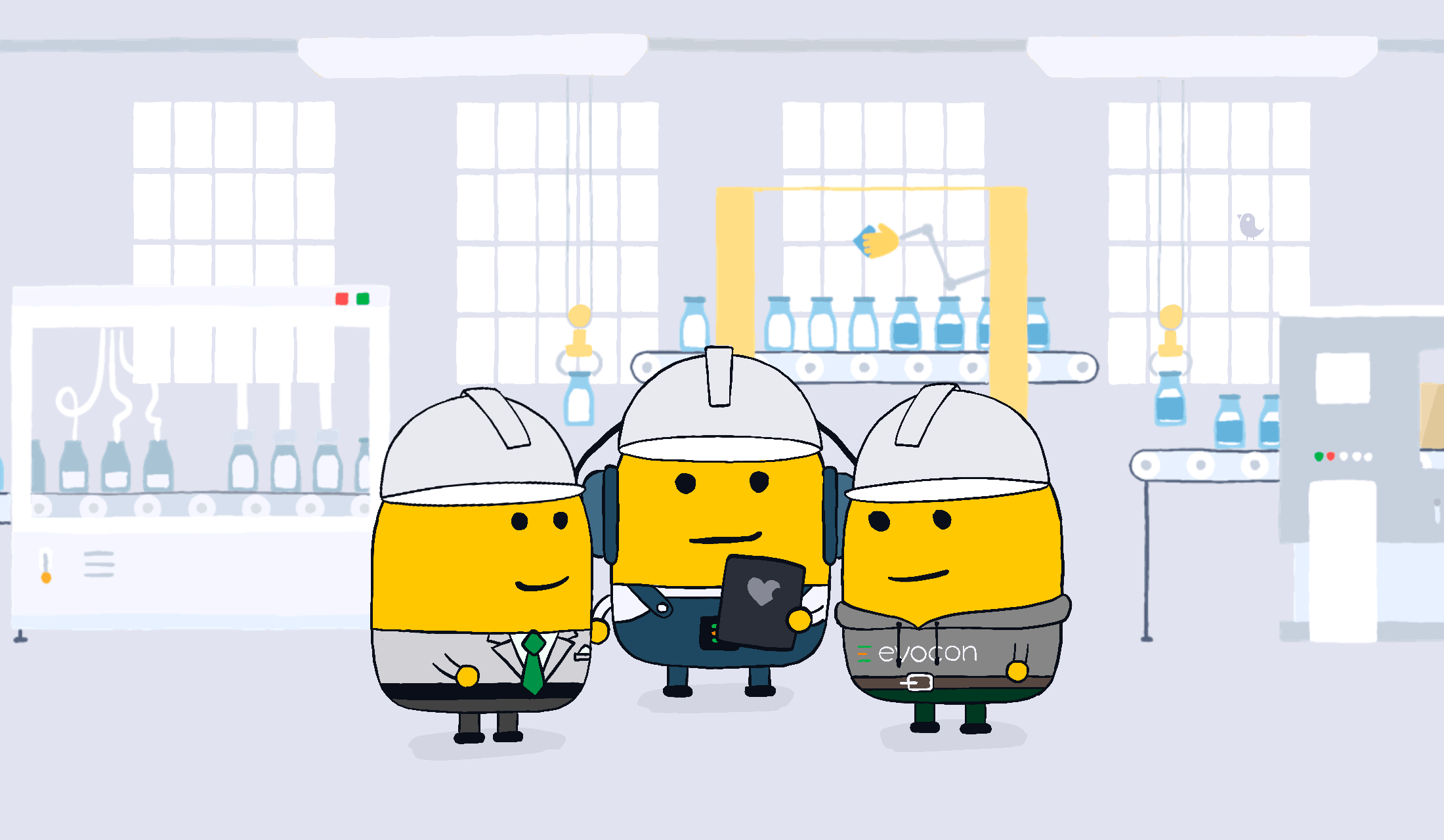
Moreover, a modern workforce wants to feel empowered to take advantage of the latest tools and technologies. If no viable alternatives to paper existed, then manufacturers would have a solid argument as to why they are persisting with traditional processes. By not utilizing paperless manufacturing solutions, companies also stand to see their employees’ morale impacted – especially if competitors have implemented such systems. That’s because workers might feel undervalued in their roles, which could lead to them searching for positions elsewhere.
Mitigate risk and boost your business continuity
One of the biggest pitfalls with paper is that it lacks security. Should a fire break out in a factory, there is significant risk associated with keeping paper-based files. Floods and even insects also pose a threat to paper documentation. A manufacturer could lose years worth of information in a single event.
Paperless manufacturing eliminates risk in this respect and everything is stored electronically and backed up for business continuity purposes. Even in the event of a natural disaster, a firm’s files will be safe, making recovering significantly easier and cost effective.
Go into audits with the utmost confidence
For manufacturers, professional accreditations and industry compliance are paramount. They not only boost a firm’s image and underline its commitment to quality, but also help embolden its workforce.
Take ISO 9001. It outlines the specific requirements manufacturers need to meet in terms of quality. To maintain ISO 9001 accreditation, firms must undergo a rigorous compliance audit every three years.
For the ISO 50001 Energy Management accreditation – a data driven ISO standard focuses on energy performance improvement – manufacturers must have their energy data validated digitally. Traditional paper-based processes simply cannot achieve this, so companies that are not utilizing paperless manufacturing stand to miss out on attaining this important sustainability-related accreditation.
With paperless manufacturing solutions, firms can go into such audits with the complete confidence that their records are accurate and up to date. Having quick and easy access to documentation, such as certificates and production data, means manufacturers can efficiently prove their quality standards during audits. Furthermore, such paperless solutions can also help with the management of calibration and non-conformance, making reporting on both significantly more intuitive and efficient.
Consistently delight your customers with your quality
Having switched to a paperless solution and acquired complete confidence in its manufacturing processes and quality standards, a company can reduce the amount of rework it has to perform.
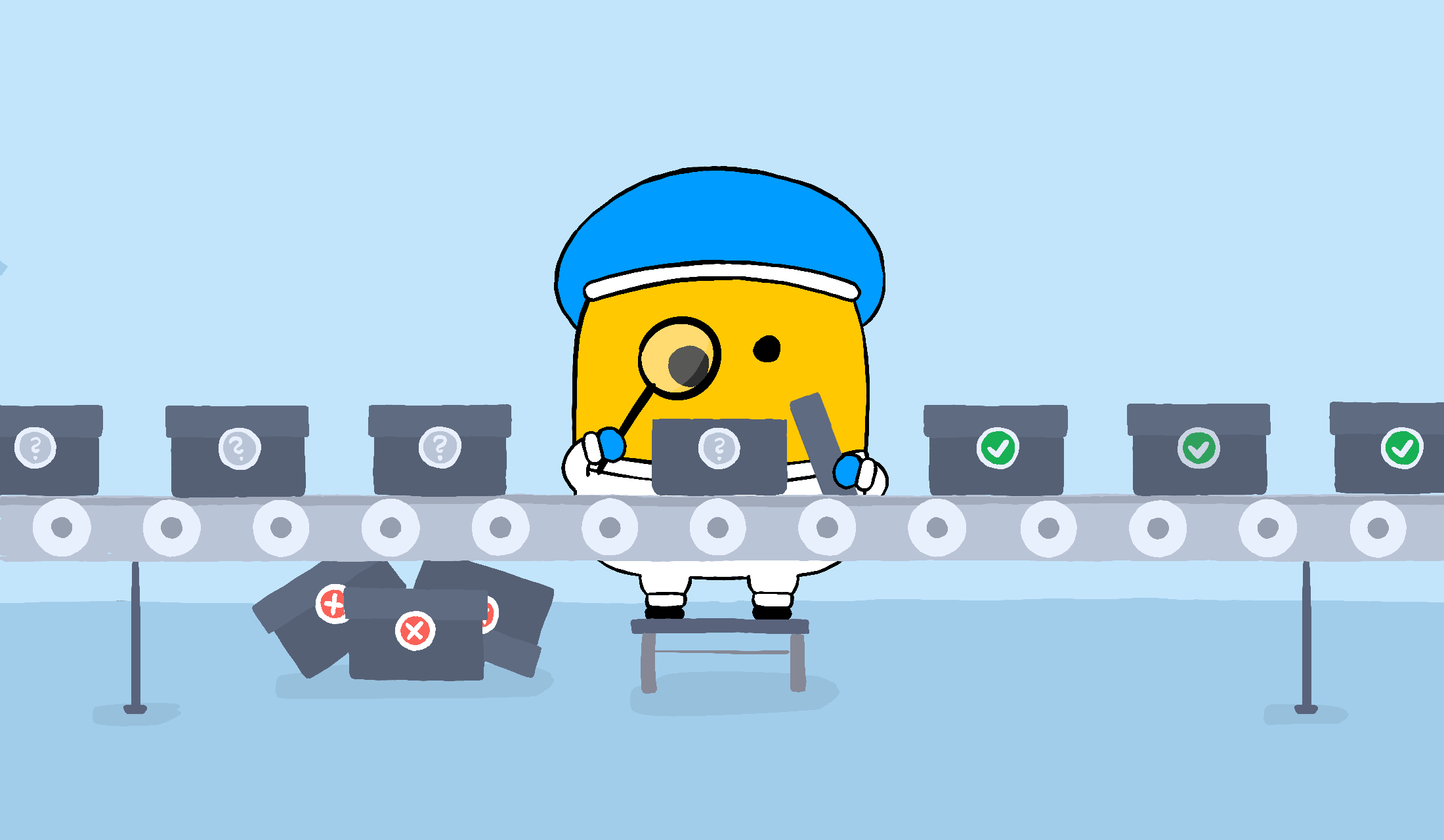
SixSigma defines rework as “an action performed upon a non-conforming product or service that, when completed, makes it conform to its requirements.” In other words, fixing products that don’t quite make the cut for whatever reason.
Furthermore, there are solutions that can digitize shop floor quality and maintenance checks. By going paperless in these areas, manufacturers can not only increase product quality and free up their workers to perform more value-add activities, but also enjoy better equipment longevity and the associated cost benefits.
Manufacturers can promote their commitment to quality standards to their customers, who will also notice it in the consistently high quality products they receive. This is great for building and maintaining brand loyalty and also highlights to the wider industry just how seriously a firm takes its work.
Start making data-driven decisions
Digital manufacturing solutions can also afford powerful insights for manufacturers. With data stored electronically, trend analysis can be performed at the touch of a button. Detailed reports can also be produced to outline any pertinent insights that are uncovered. This is all but impossible with paper-based documentation.
Firms can then use these insights as the basis for their continuous improvement programs. Examples might include identifying training deficiencies/opportunities, equipment utilization issues, and quality lapses. Because all of these insights can be gathered quickly and easy, there is no impact on a firm’s efficiency.
One of the most common complaints we hear from manufacturers is how they lack transparency when it comes to their shop floor production. This is often a result of persisting with paper-based processes because they simply do not visualize what is going on at any one time.
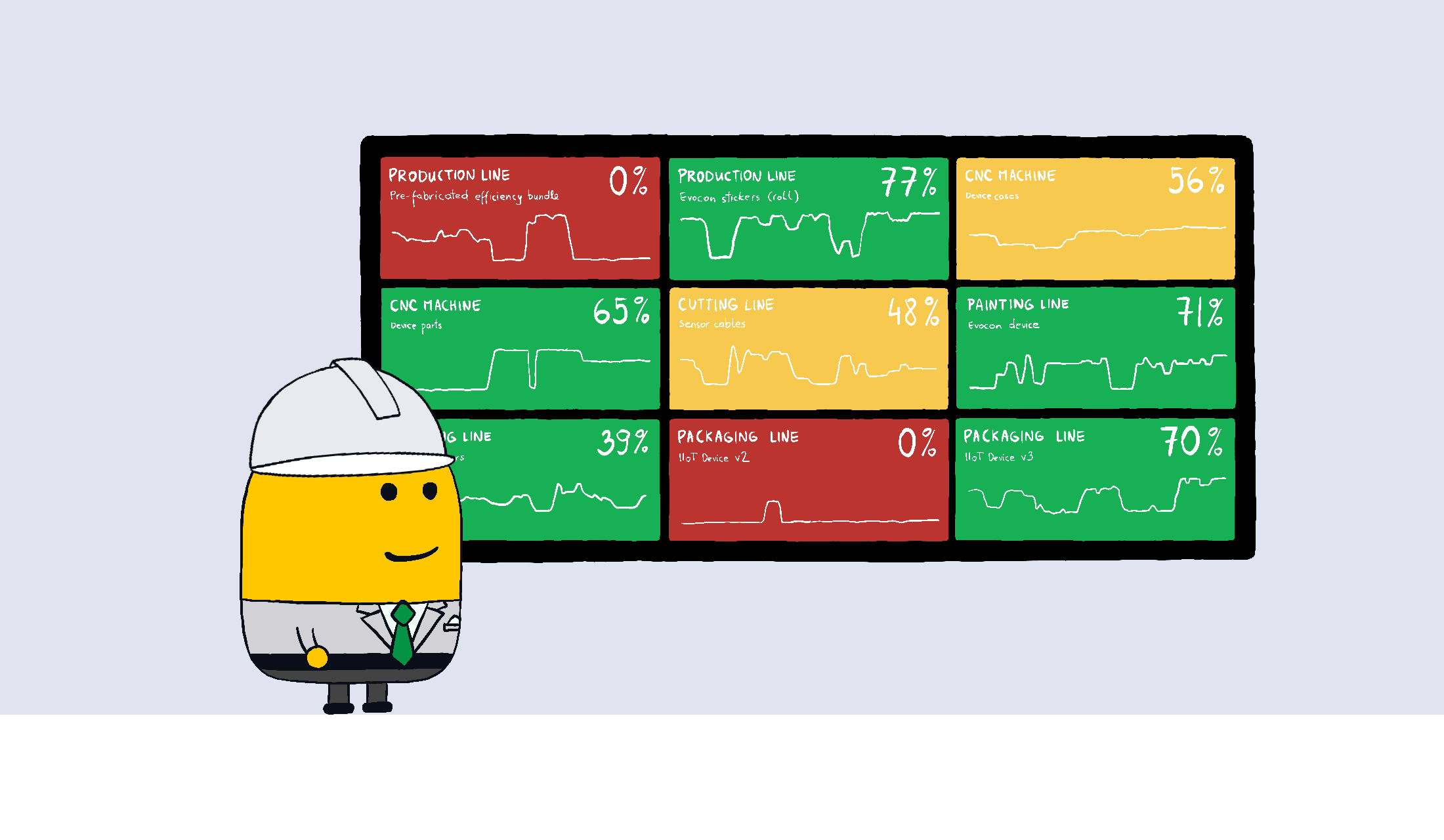
Be the best version of your organization
Let’s revisit the waste and sustainability angle for a second. Were you aware that consumers actually want manufacturers to help them be more sustainable?
According to the Mintel Sustainability Barometer 2021, consumers predominantly hold companies most responsible for “a host of environmental and social targets and standards.” In fact, almost half (48 percent) of consumers believe companies should be primarily responsible for boosting recycling; compared to just a quarter that believe the responsibility lies with themselves, and a fifth with governments.
By implementing paperless ways of working and massively reducing the amount of paper they use, manufacturers can promote themselves in the eyes of consumers as companies that not only care about the environment, but are proactively doing their bit to help.
Take Your First Step to Paperless Manufacturing
Having used paper for such a long time, it’s understandable that the switch to paperless manufacturing could be daunting for many firms. The good news is beginning your paperless manufacturing journey does not need to cause you headaches or represent a large capital investment.
Start small and simple – digitize downtime tracking
By starting small and starting simple, you can begin replacing many of your traditional manufacturing processes and systems one by one with modern alternatives that will help you realize the benefits outlined above.
Evocon can help you begin your paperless manufacturing journey (and do so with minimal effort, disruption and investment) so you can see first hand just how valuable making the switch can be.
By replacing their downtime tracking processes with Evocon, manufacturers can eliminate the need for operators to manually mark downtime and the reasons behind it on paper. Not only is manual downtime tracking highly inaccurate and inefficient, but it also does not allow for the tracking of speed losses and micro stops. In other words, if you’re tracking downtime manually using paper, you are not seeing the full picture.
While this is just the first step to paperless manufacturing, it is an important one as it allows you to see just how easy and cost effective the change process can be.
It’s our experience that once our manufacturing customers have seen the benefits they can afford by using our production reporting software, they want to take more steps on their paperless manufacturing journeys.
Next up: production orders & quality monitoring
One of the next areas they then often focus on is digitizing their production orders. By integrating Evocon with their ERP systems, these manufacturers eliminate the need to physically print orders. Any changes to the job are made centrally and updated automatically on the shop floor in real time, reducing the chances of errors and subsequent rework.
The next step is usually to digitize quality monitoring, freeing up valuable resources to focus on value-add activities.
Continuing Step-By-Step
With various paperless manufacturing initiatives implemented, manufacturers usually have a taste for the benefits of digitization and don’t want to stop there. Fortunately, there are numerous opportunities to eliminate paper on the shop floor and all it takes is for manufacturers to experience the benefits by taking a step-by-step approach to realize how simple this journey can be.