A manufacturing plant’s Quality Assurance Manager (QAM) is responsible for product consistency and production compliance with the Quality Management System (QMS). This article examines how a Quality Assurance Manager benefits from Evocon’s production monitoring and OEE tracking software.
Evocon Automates Monitoring of Production Quality
As a Quality Assurance Manager with overall responsibility for product consistency and QMS compliance, your tasks include:
- monitoring and advising on production quality,
- collecting production data on quality,
- implementing and monitoring the results of quality checks,
- and producing reports on performance measured against a standard.
You will also likely play a key role in process improvement (PI) initiatives. The nature of a process improvement project requires that you collect data on production quality. Data, for example, on scrap rates and first-pass yield. Often, it is your analysis of trends in the production data or attempts to understand the root cause of a problem, which will lead to the formation of a PI project.
While the responsibilities of the position are easy to write in a few short sentences succinctly, the amount of effort necessary to accomplish these tasks is significant.
A fundamental reason has long been the time required to capture and collect sufficient production data on various shop floor processes. Indeed, in many companies, armies of employees work in Quality Control, whose sole purpose is the manual collection of process data by pen and paper or by Excel.
Learn more: The disadvantages of manual data collection
As we will see, Evocon’s quality control software significantly reduces the time and resources a Quality Assurance Manager will need for these efforts.
Daily Challenges of Quality Assurance Managers
As a Quality Assurance Manager in manufacturing, there is always a lot going on and a wide variety of tasks to accomplish. This can find you doing everything from auditing a process for QMS compliance to problem-solving on the shop floor.
That said, there are common areas that most QAMs will concern themselves with daily:
- reducing non-conforming products (defects, scrap, etc.),
- a search for process improvement opportunities,
- and administration of a continual process for collecting production data for analysis and reporting.
Non-conforming products and scrap
As a QAM, you understand that it is essential to monitor and track production non-conformance and scrap closely. Moreover, you know that you have to put in a lot of effort to collect data for this analysis manually.

With manual data collection, this effort is unavoidable. After all, you need to know that your processes can consistently produce output that meets standards as specified by the Quality Management System. To do that, you need data on production quality that is:
- easily accessible,
- accurate,
- and free of bias.
This task is not logistically feasible when done manually without an automated OEE system to collect the massive amount of data generated by production processes.
Automated OEE Software
Start collecting production and quality data automatically. Free for 30 days.
Process improvement opportunities
A Quality Assurance Manager must also lead the effort to reduce the cost of poor quality. One way that QAM’s ensure that they will see improvement in the metric is to make sure that all resources at their disposal, for example, Process Improvement Teams and Quality Engineers, focus on solving the problems which have the most significant effect on quality once eliminated.
This was a big challenge in the past as it required comparing data from across the facility. Data that likely did not exist. This meant relying on subject matter experts’ informed judgment or even a guess.
Reporting on production quality
Most Quality Assurance Managers will have some form of a monthly plant management meeting where they will report on production quality for a period. Not only is this a requirement of ISO 9001, but it is also a standard business practice for most manufacturers. To prepare for the meeting, it is not uncommon to have several technicians gather data to give to a Quality Engineer. The Quality Engineer will then perform a preliminary analysis before sending a report to your desk. This could involve 5-10 staff hours per week by itself.
Then, once you have the data, you will likely still need to create charts and a slide deck. And this, too, takes valuable time that could be spent more effectively on taking care of the company.
Ways Evocon Benefits Quality Assurance Managers
Now that we have looked at some of the main daily concerns of a Quality Assurance Manager, let’s look at the benefits which Evocon’s manufacturing data collection software provides together with its quality control product.
Eliminating Manual Data Collection
The process of gathering production data on scrap rejects and non-conforming products often requires a Quality Assurance Manager to task Quality Technicians and control personnel with pen and paper data collection. In other words, applying a paper-based manual system to monitor data on production quality. Not only is this process time-consuming, but it’s also prone to errors.
With Evocon, you can quickly pull up data on your entire production process. And because data collection is automated and is substantially more accurate and reliable.
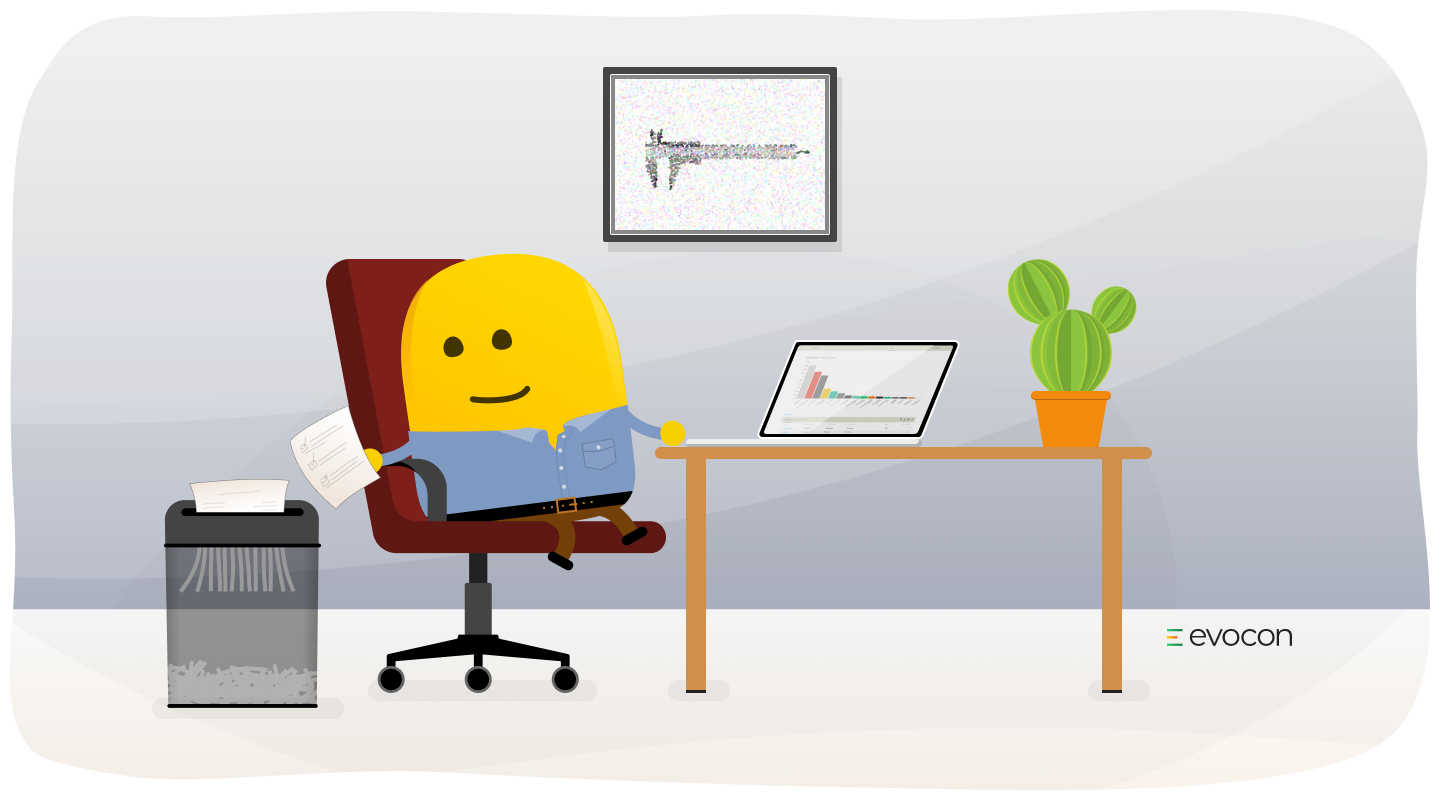
The need and use of data are not going to end. So the only option that can reduce a QAMs workload is to become more efficient at managing the collection and dissemination of data. This is what Evocon’s production monitoring software does for QAMs. The result is not only saving thousands of hours annually, but also the quality of the data itself is improved substantially.
See Where your Production Losses are in the Plant
Typically, Quality Assurance Managers tend to be heavily involved in Process Improvement. Mainly when it comes to identifying and selecting the production processes that the project teams should focus on.
Less than a decade ago, relying on historical, incomplete, and manually collected production data was common. It was simply not practical in any other way. This meant that the first task of a project team would be to collect as much data as possible. The data would then be used to verify that the problem justified the deployment of a team in the first place.
Evocon changes this situation. Now, a few mouse clicks will show OEE data by work center, including quality losses detailed for each. Such detailed information results in projects starting in the areas that guarantee results.
The Bottom Line
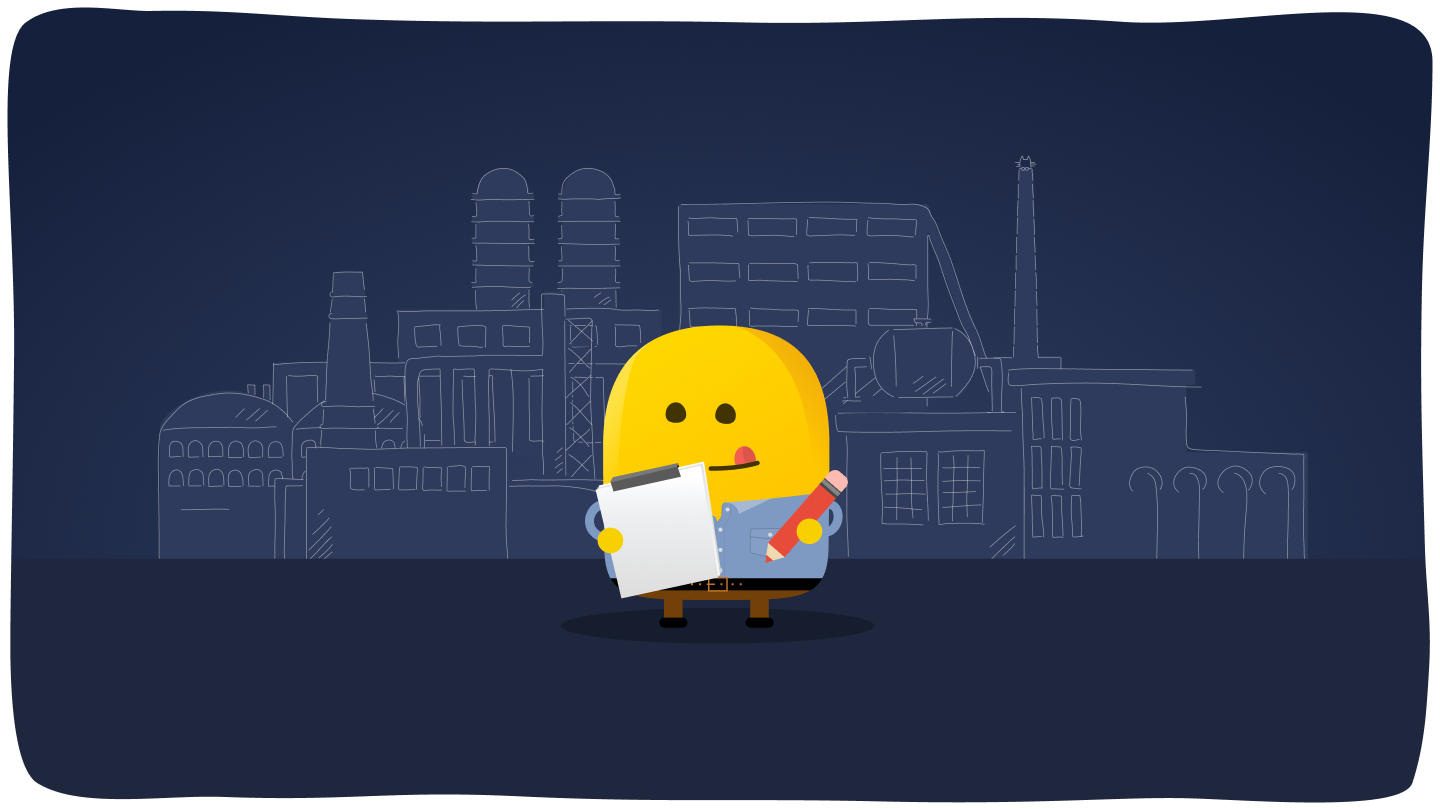
We have seen that the role of a Quality Assurance Manager is one in which data serves a primary function. We also looked at how the time required to collect data manually for analysis and reporting is significant and, worse, is a low value add.
Evocon’s manufacturing quality control software can help fundamentally change this situation by automating the tasks of data collection and reporting.
Why Start With Evocon Today?
Having user-friendly access to reliable quality data makes it easier to see the results of improvement efforts visually. It also gives you more time to focus on other essential functions of your role. Such as leading internal audits, evaluating production process compliance, or implementing new solutions to ensure no customer ever receives a non-conforming product.
This is what Evocon is all about. Freeing you from the time-consuming and error-prone process of manual data collection. So that you can add value by doing what you do best.
You can get started today with our free trial and begin to save time on automated data collection immediately. In several weeks, you can realize just how far having additional resources to assign can do for your efforts to reduce cost and improve production quality.