Downtime in the manufacturing industry is a costly affair. By implementing strategic measures, you can not only reduce machine downtime but also elevate your Overall Equipment Effectiveness (OEE), resulting in enhanced productivity and profitability. Here’s our short guide on best practices to achieve this goal.
1. Ensure Accuracy of Data
Without reliable data, we’re only guessing about the extent and impact of downtime. Accurate data helps manufacturing organizations identify the true frequency, duration, and reasons behind these disruptions, allowing for targeted, evidence-based problem-solving.
By understanding what’s causing downtime, you can create strategies to minimize future disruptions, leading to increased operational efficiency and productivity.
If you have no process in place for collecting data, you can learn about the different options to track machine downtime. In essence, though, the least you can do is start collecting it on paper and then transferring it to Excel. However, based on our experience working with manufacturers around the globe, this will just push forward the inevitable – if you want to ensure data accuracy you need to implement an automated solution to capture data.
Once you’ve ensured data is accurate, you can turn to enhancing visibility of data.
2. Make OEE Visible on the Shop Floor
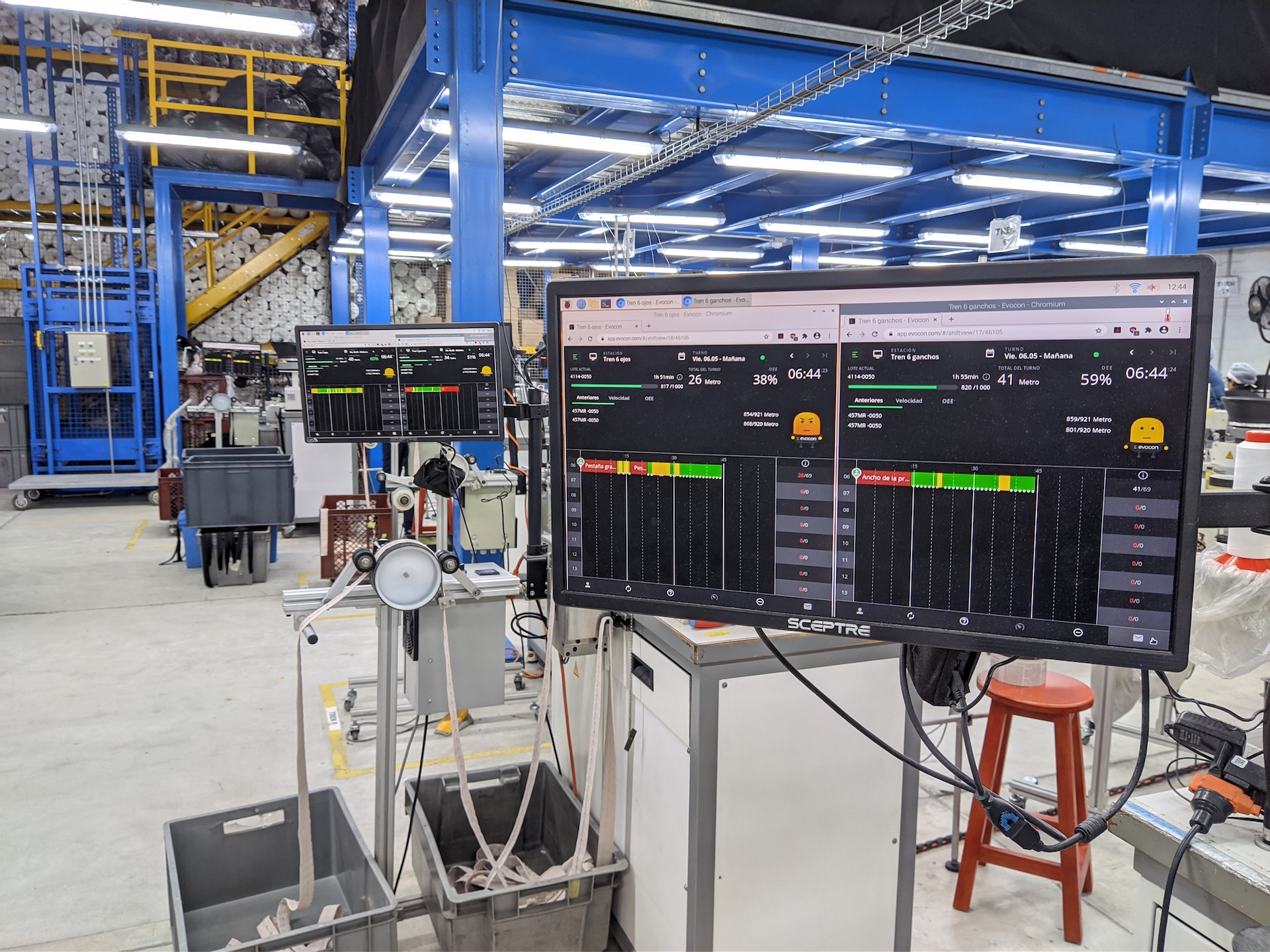
The power of visibility cannot be understated in your quest to minimize downtime. Start by displaying your OEE data, gathered via a reliable downtime tracking software, on the shop floor. This enhances awareness, fosters motivation, and empowers your team to tackle downtime as it arises.
Overall Equipment Effectiveness (OEE) is a comprehensive metric comprising Availability, Performance, and Quality, each of which can be visualized separately and compared over periods for trend analysis. This will help you keep an eye on your most critical KPIs and promote a culture of continuous improvement.
Tip: It’s very common to experience an increase in OEE of around 10-15% just by visualizing downtime and OEE data on the shop floor.
Downtime tracking software
Start measuring and optimizing your downtime with Evocon’s 30-day free trial.
3. Prioritize and Tackle the Low-Hanging Fruits
Once you have collected a substantial amount of data, usually over a couple of weeks or months, you can start identifying the most common causes of downtime. The crucial part here is how you choose to categorize your downtime groups and reasons. Think about this as early as possible and talk to your shop floor so that everyone understands how reporting is done the same way.
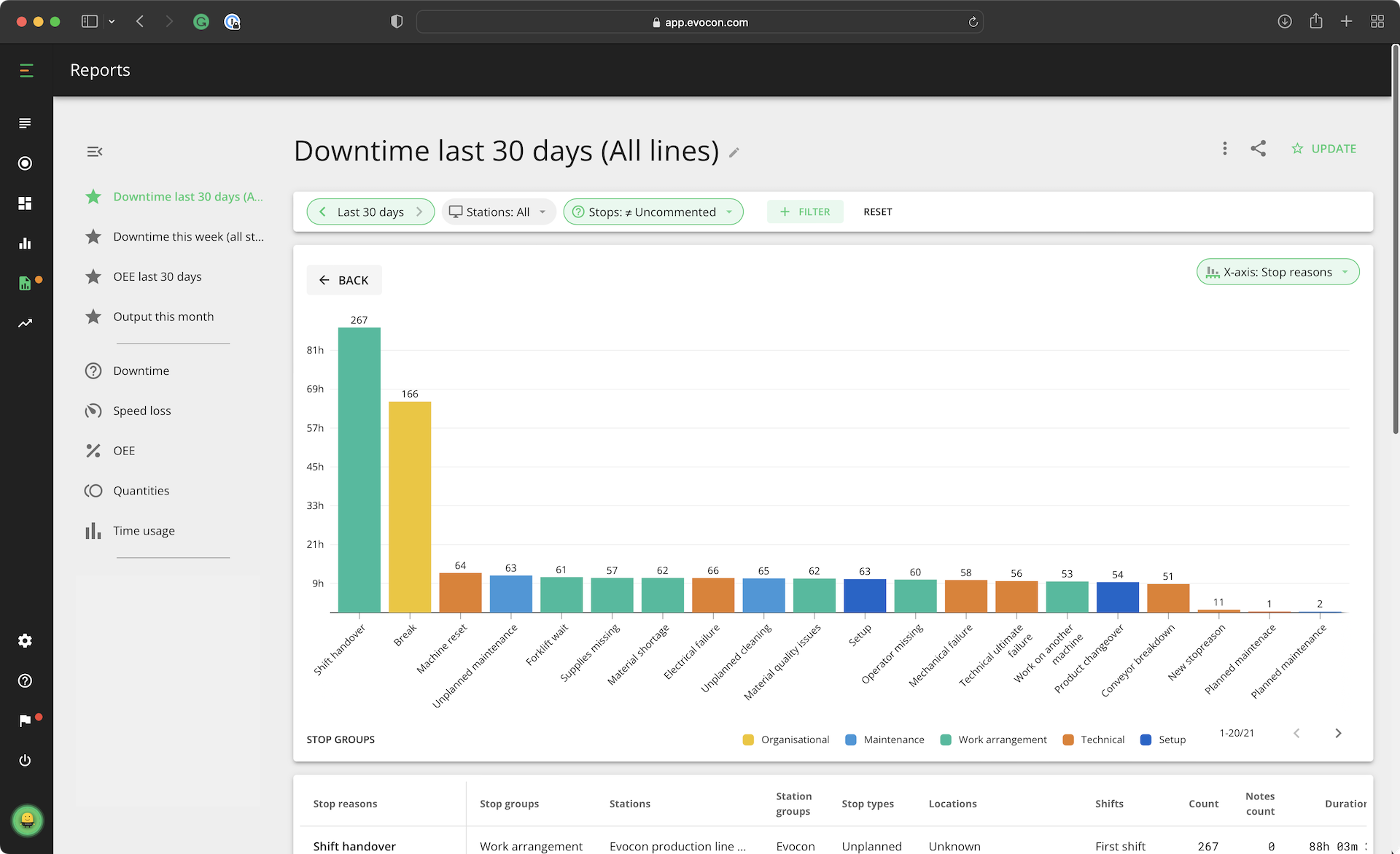
When data is collected, focus on those issues that occur most frequently or last the longest, and start by tackling the easiest ones to solve – these are your low-hanging fruits.
Consider methods such as:
- Performing a ‘5 why’ analysis on the shop floor.
- Holding short meetings with operators for brainstorming solutions.
- Regular stand-ups to share problems and align improvement efforts.
These strategies will ensure you are addressing the most impactful downtime issues first, leading to immediate improvements in OEE.
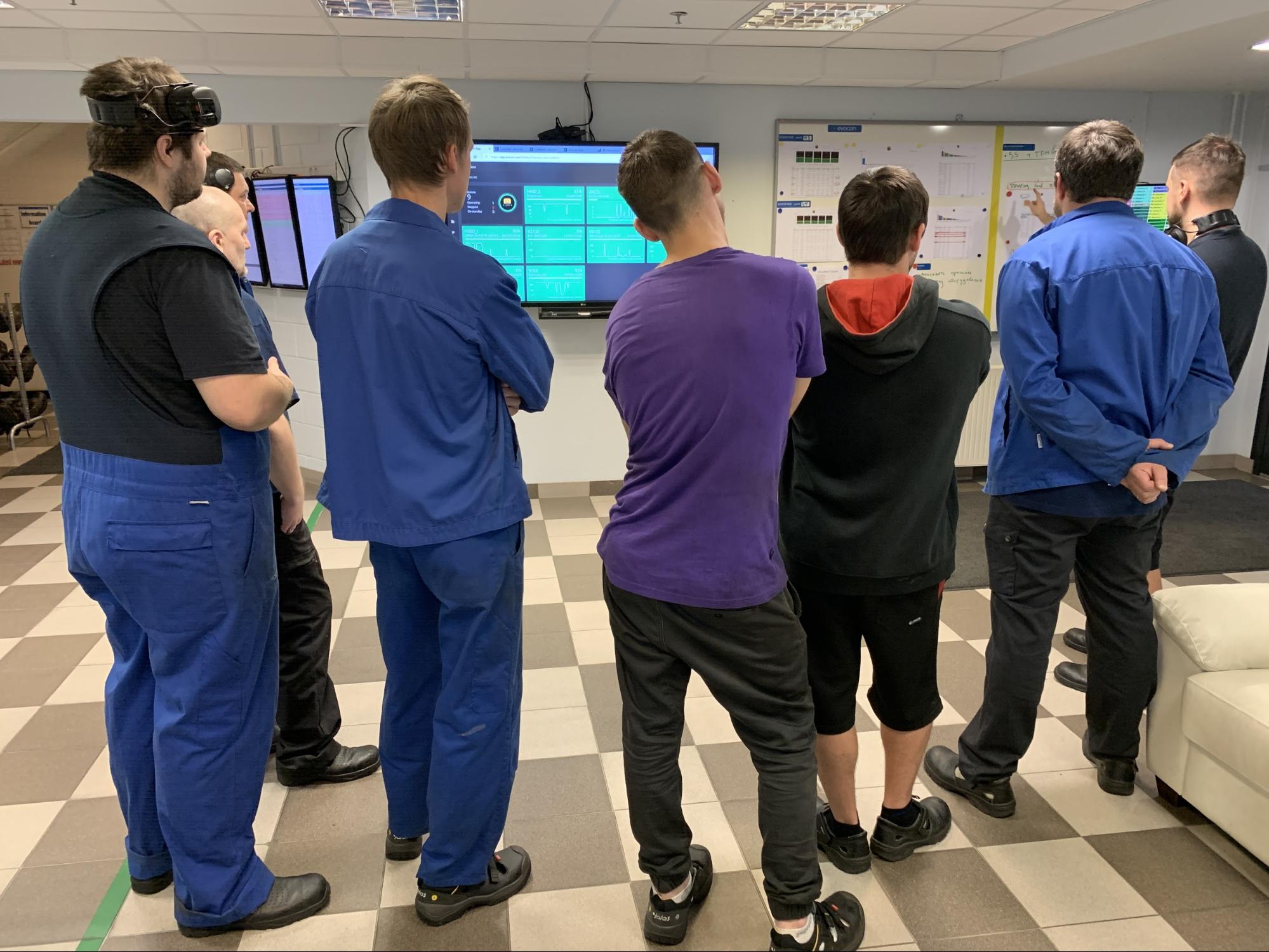
4. Solve More Complex Problems
As you advance in your downtime reduction journey, you may encounter more complex issues. Here, consider leveraging time-tested methods such as:
- Root Cause Analysis (RCA)
- A3 Problem-Solving
- Single-Minute Exchange of Die (SMED)
- Six Sigma and Lean Six Sigma methodologies
- Total Productive Maintenance (TPM)
- Gemba walks
Incorporating these strategies into your routine can lead to substantial downtime reduction. For instance, one of our clients, using our downtime tracking software coupled with the A3 process, managed to decrease their second biggest downtime from 1 hour 6 minutes per day to 41 minutes per day within three months.
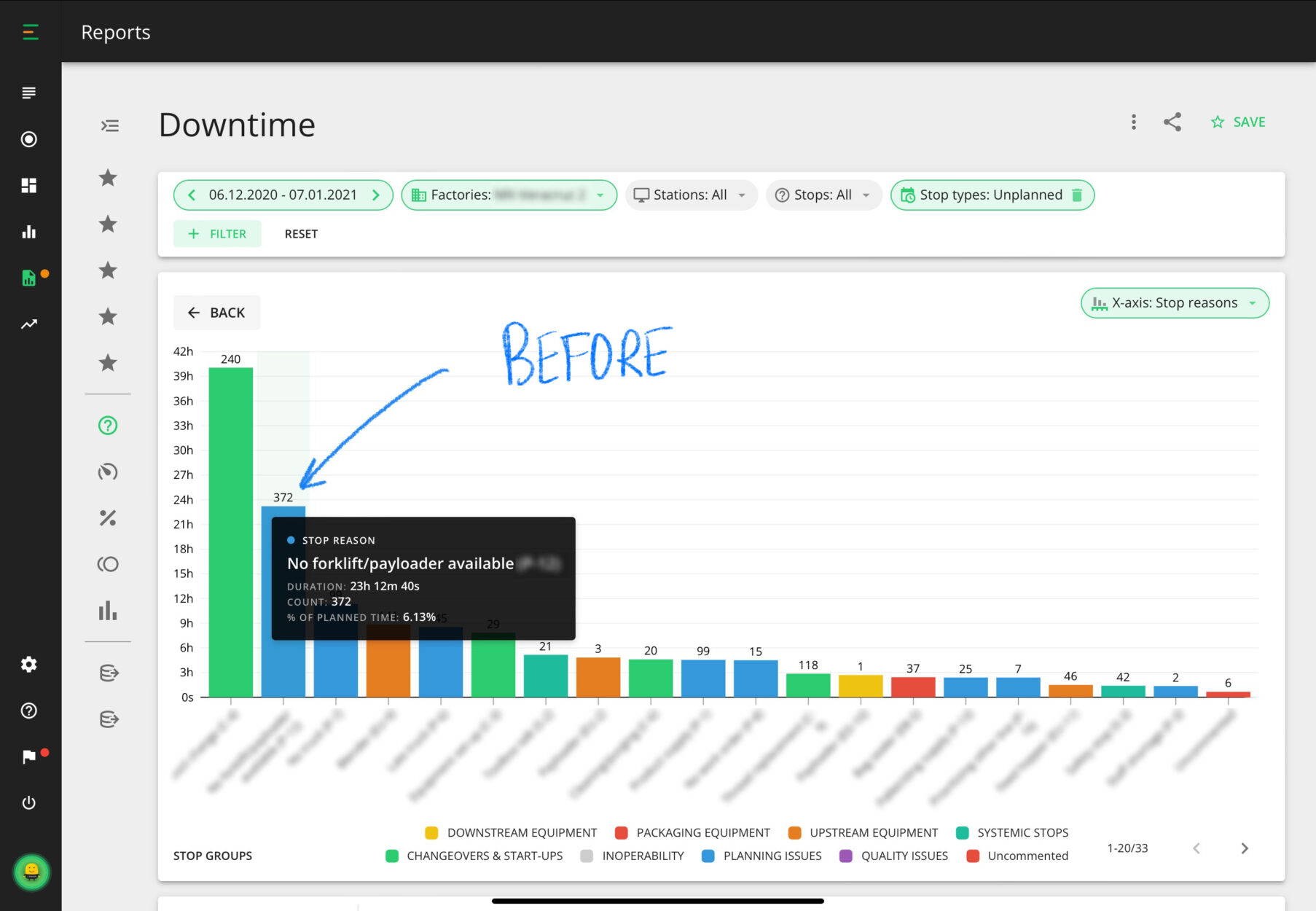
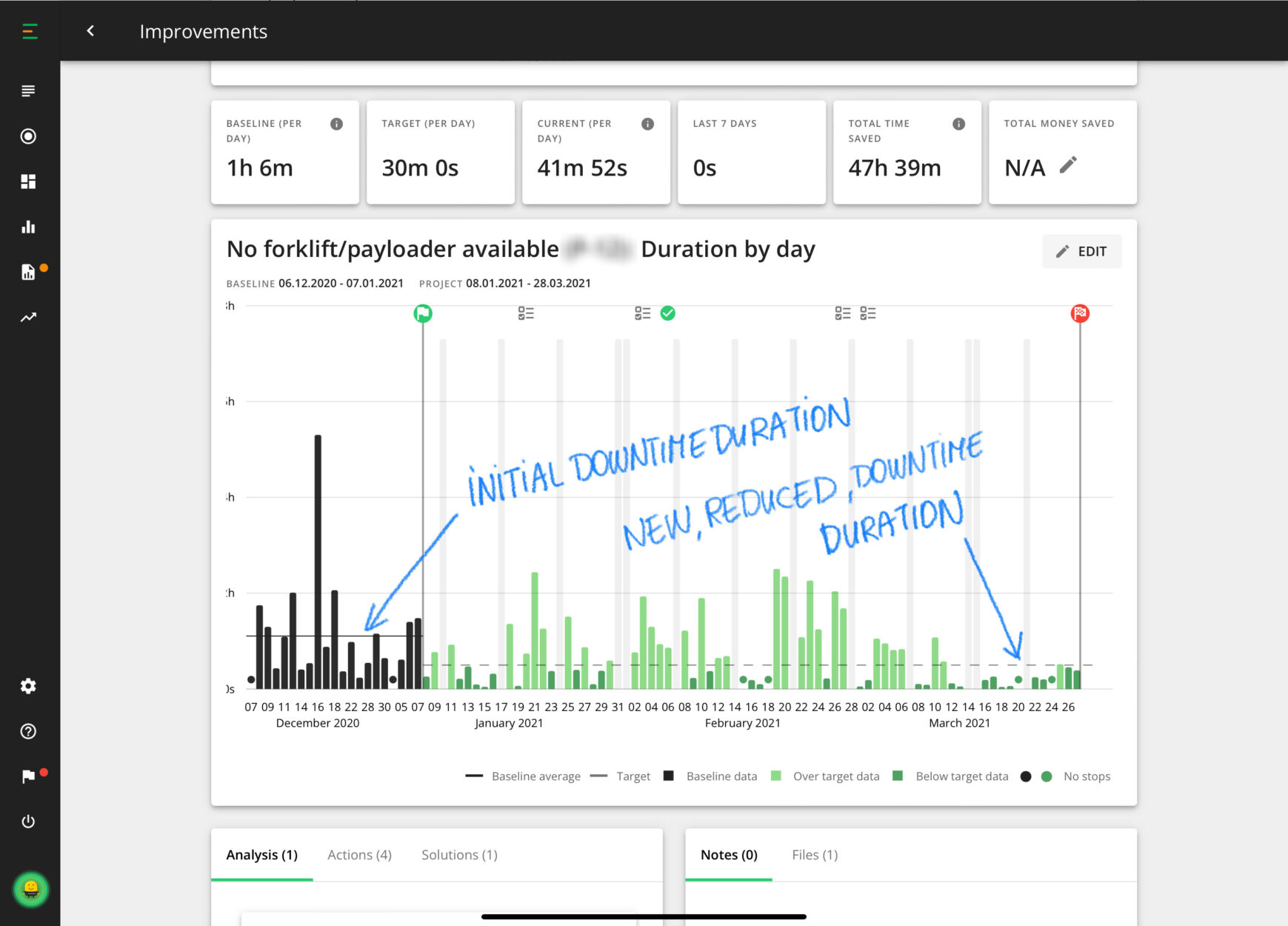
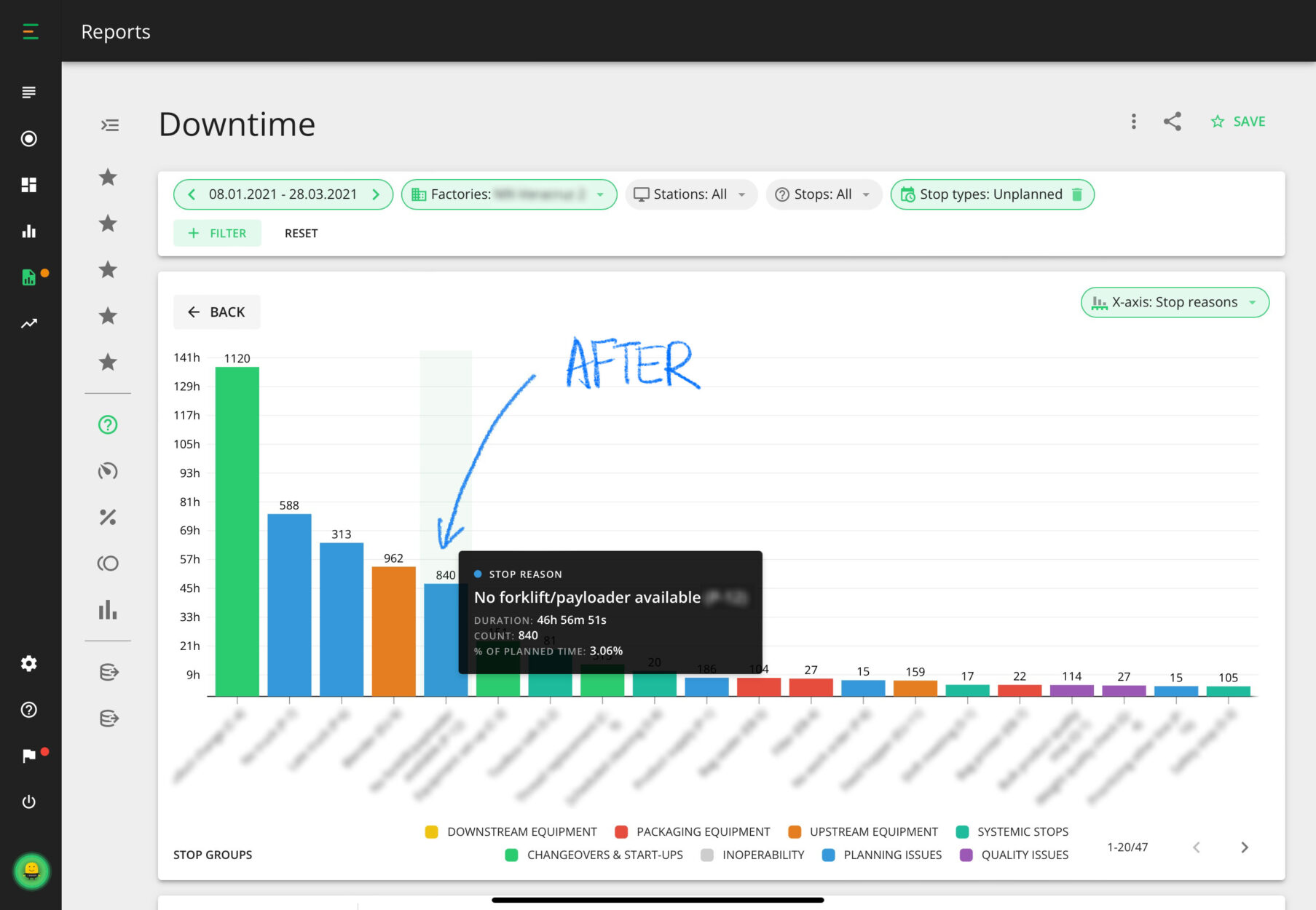
5. Be Relentless about Continuous Improvement
Continuous improvement may seem daunting as initial big leaps gradually transform into smaller, more strenuous steps. Yet, the very essence of continuous improvement is consistent progression, no matter how incremental.
Although some manufacturers might be content with achieving a ‘good enough’ level, true industry leaders continually raise their performance targets. In the context of OEE, world-class performance is typically considered to be 85% and above. Unfortunately, according to our data, only about 10% of manufacturing organizations exceed this benchmark.
The Bottom Line: Leverage Data for Continuous Improvement
Reducing machine downtime and optimizing OEE is an ongoing journey that involves making the invisible, visible; prioritizing issues and tackling them strategically; solving complex problems using robust methodologies; and persistently seeking continuous improvement.
By leveraging real-time data, engaging your team, and maintaining a relentless focus on improvement, you can significantly minimize downtime and maximize OEE. This, in turn, will drive operational excellence, leading your manufacturing facility from ‘good’ to ‘great.’