Stopwatch, a pen, and a piece of paper. Or in the best case, an Excel spreadsheet and a videotape. Up to this day, this is the equipment for collecting production data in most factories. But notes mount up, and going through the information they contain becomes more complex. Manufacturing is efficiency-driven by definition, so does this sound like a future-proof way to gather and analyse data?
The Importance of Machine Data Collection Software
Competitive advantage stems from accurate, live information. But only automated data collection enables workers to promptly intervene on unplanned production downtime, and managers to take conscious decisions on what to improve. With Evocon, manufacturers fill this critical intelligence gap, laying the foundations of an efficient, knowledge-based factory environment.
Data automation is central to making sense of complex data
Like human labour, financial resources, and machines, data is a key asset manufacturers need in order to achieve higher productivity. Not only it is omnipresent, particularly as we see today in the information age. Taking a closer look, we would notice that it has been ever-present too.
From early craftsmen to mass production in the Industrial Revolutions, both the quality and quantity of valuable data to look through has increased dramatically. We are used to collecting figures about workers’ performance, supplies, productivity rates, as well as machines’ need for maintenance or replacement. In recent times, information systems and computers empowered industrial players to store, exchange, and analyse such data in a more comprehensive manner. However, way too often this information is still handled manually.
Some factories shifted from pen and paper to Excel sheets and video recordings, but this is not enough. IIoT and cloud-based solutions now give entrepreneurs more opportunities to increase data accuracy, availability, and insightfulness. Underlying losses negatively affect profits and OEE performance, and they stack up when managers do not have a precise idea of what is causing them. That is why Evocon advocates for a shift from manual data collection in industrial production to an automated production monitoring system.
The many ways manual data collection harms productivity
Data collection has been slower than other practices in manufacturing to reach the coming of age of technological change.
Our research and on-field experience show that insufficient data collection still dramatically troubles the industry. It is one of the most common obstacles towards achieving higher productivity and improved OEE, chiefly rooted in manual methods of data gathering. These impact not only data accuracy but also management decisions and the effective distribution of tasks among workers in the factory.
Hands-on operators and managers are aware of the huge difference between manually using computer tools and properly automating data collection. As one experienced industrial engineer told us:
“Humans should not measure machines; instead, machines should be measuring machines.”
Core procedural flaws resulting from manual data collection
When you make workers manually update an Excel sheet or use pen and paper, core procedural flaws are just one step away:
- Production downtime, breakdowns or smaller issues might go undetected, either because unseen or deemed not relevant. Subjectivity leads the assessment and, consequently, the data collection process.
- Manual data collection takes time, and workers have to devote large parts of their shift to this low-productivity function. Not only mistakes are easy to make, but why should they engage in inefficient and tedious tasks when a machine could?
- Real-time information is missing entirely, and so is a quick reaction to random stoppages. In most factories, timely detecting and fixing these problems is currently impossible due to the interval between the event occurred and its assessment.
- As a result, collected data is inconsistent, ineffective, incomplete, and inaccurate. Furthermore, OEE evaluations and improvements are based on information that impairs the achievement of higher productivity.
A practical case illustrates all these shortcomings. When an IFS customer switched from manual to automatic event recording, the number of stoppages, slowdowns, and other events reported for two production lines increased from 5 000 units per year to 200 000.
This means that the production process is often a big black box, full of information that might not yet be thoroughly accounted for and analysed. Moreover, it clearly emerges how inaccurate machinery data may lead to increased maintenance costs because problems are not dealt with in time.
Automate data collection with Evocon
Enhance data accuracy and reliability to discover the true potential of your factory. Free for 30 days.
Industry 4.0 starts from automated data collection – cases and indicators
Evocon taps into these core issues in industrial production by taking unreliability out of the equation. Machine sensors monitor equipment activity, and workers can fully deploy their time and skills to more demanding tasks. By significantly enhancing data quality, Evocon paves the way for knowledge-based decision making and higher production efficiency.
The 6 dimensions of data quality
When automated data collection is in place, data quality improves in all six dimensions fundamental to smart manufacturing.
According to the definition of the US Census Bureau, these are:
- Relevance – the extent to which the data matches the company’s needs
- Accuracy – whether the resulting values are precise and reliable
- Timeliness – how much time spans between reference period and information
- Accessibility – how easily operators can obtain and use the information
- Interpretability – the ease of understanding of the data at hand
- Transparency – objective evidence supporting data accuracy
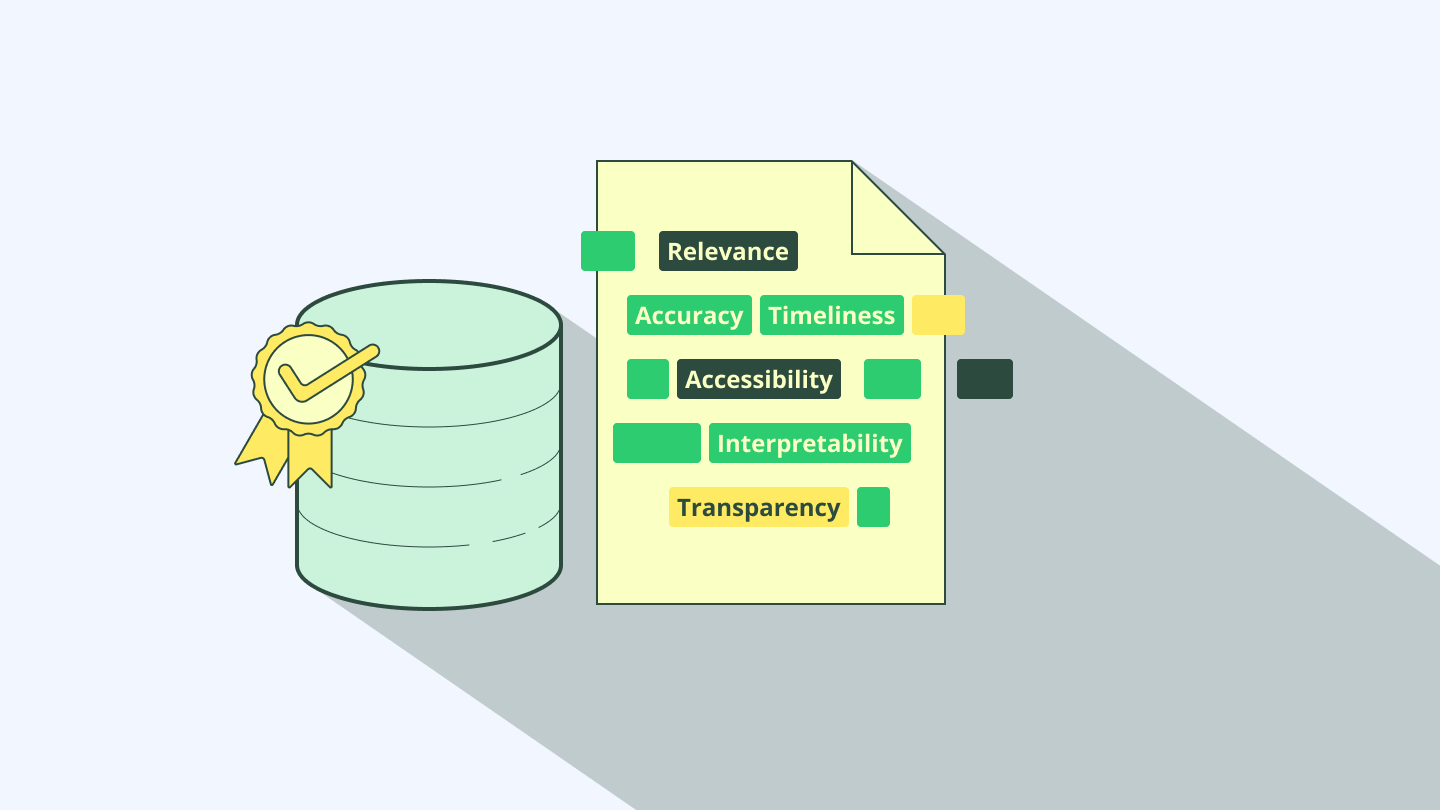
When data collection is manual, accuracy and timeliness are always out of the picture. Moreover, minor stoppages might go unnoticed, but they still cumulate in relevant losses. The example mentioned above is a perfect test case on the matter. The number of events recorded after shifting to automated data collection increased 40 times as compared to the previous figures. Evidently, a hidden factory was operating just in front of the company’s eyes, curbing profits due to massive, undetected losses.
The resulting problem is that companies take on the OEE approach, but they do it based on incorrect, unreliable information. Minimizing the role of people in data collection may enhance information accuracy, will most definitely free up the work time of operators, and improve data analysis.
For example, in a bakery of 1.8 million square feet, installing an automated data-collection system allowed for the root-cause analysis of machine downtime. This enabled subsequent improvements in equipment reliability to be carried out, boosting monthly productivity by $1 MLN.
Outstanding OEE Improvements in Smart Factories
Automated data collection allows to precisely assess the underlying losses taking place in the production process, and correctly configure a plant that enhances productivity and OEE. Quantitative and qualitative evidence makes the case for it – automating data collection leads to unidentified OEE losses becoming almost 0%.
Better data quality also means you have tools for better decision making. On top of that, the ease of understanding of Evocon’s visualisation component keeps shop floor operators in the loop, allowing them to become the first-hand source of solutions to prevent machine-related losses.
Automated data collection has enabled Evocon’s clients to achieve remarkable results and maximise their ROI. In food production, improvements of +20% in OEE performance were reached in just six months on all packaging lines. Metal components producer Meconet, by its part, recorded a +50% in productive work time.
Our OEE software has also enabled large scale projects of digital transformation in manufacturing at Yara, leading to a global average +15% of OEE performance in one year. Finally, wood processing company Thermory witnessed an increase in production efficiency of +20%.
Learn more:
- Calculate the ROI for OEE Software and Production Monitoring
- Reveal your hidden factory with our OEE calculator
Accurate Real-Time Data as the Key for Future-Proof Manufacturing
This series of customer experiences shows that data is key across industries. And automated data collection is an essential ingredient for higher returns.
We live in the information society, where accurate and complete data carries the possibility to unlock hidden potential just by shining a light on what before just remained unseen. Evocon is designed to support industrial players in their efforts to implement a paperless manufacturing system, co-creating the premises for data-driven, future-proof manufacturing.
Sources
The case studies mentioned in this article referring to the IFS customer and the bakery have been sourced, respectively, from Plant Engineering (2010, 64/8) and Food Engineering (2012, 84/2).