In today’s fast-paced manufacturing world, staying ahead means going digital. This article dives into the essentials of digitalizing the process of manufacturing data collection, from what it is and why it matters, to how you can make the most of it. Get ready to discover benefits, steps, tips and potential hurdles in our article, packed with useful information.
What is Data Collection in Manufacturing?
What we mean by “manufacturing data” is essentially how much you produce and at what speed, how much downtime you have and why, as well as additional helpful data around that. You need not only to know but also to find the right way to collect and analyze data in order to digitalize your production properly, reach OEE targets, and go paperless. The goal of manufacturing data collection is to monitor, measure, and optimize various aspects of the manufacturing process to improve efficiency, quality, and overall productivity.
You’ll be glad to learn that most manufacturers see significant benefits as soon as they start this journey. They mention visibility, data-driven decision-making processes, and time-savings as their biggest quick wins, followed by optimized processes, labor allocation, product quality, customer satisfaction, and informed investment decisions in the long run.
There are a few techniques you need to know as you embark on this journey, such as:
- Which lines or machines to start with
- What kind of sensors you need and where to place them
- What IIoT solutions are there on the market
- How to avoid common pitfalls (i.e. cybersecurity, data accuracy, data accessibility and usability)
What Data Can Be Collected?
Production Data
You probably landed on our article because you are most interested in production data, and yes, this is one of the less digitalized areas in the industry today. That is why we see such a push for IIoT – Industrial Internet of Things. Here is the list of what data you can collect on your shop floor:
- Machine status (on/off, running speed)
- Uptime, downtime, slow-downs, such as breakdowns, changeover duration and frequency, or other stoppages and standbys
- Products and/or parts produced
- Additional data about the context of production, like:
- Who is the person responsible
- Why is downtime happening
- What is being done on the shop floor
- What are the results of quality checks
- Notes about maintenance done (or any other helpful notes)
- Utility consumption: electricity, gas, water, compressed air, process parameters (temperature, vibration, pressure, humidity, CO2 for sustainability purposes). The latter three types of data are often captured separately from production, but we’re mentioning them here because they offer additional insights when data is connected. For example, you will know the energy consumption per product batch, the production volume per person, the impact of vibrations or temperature on your product quality, the CO2 per product, and so on.
📐 Find out what can be counted or measured with Evocon.
🔭 Learn more about full scope of production monitoring
Other Data: Inventory, Maintenance, Supply Chain Management
Other manufacturing data is typically managed in Enterprise Resource Planning (ERP) systems. ERP systems focus on businesses processes – inventory management, procurement, human resources, financial transactions. They collect and store data from the entire organization in a centralized database, provide real-time access to it and support advanced planning and forecasting. What’s more, ERP encompasses entire supply chain, including supplier inventories, lead times, logistics.
Clearly, integrating ERP and production data is a must for organizations looking to maximize digitalization.
If you are curious about how integrations work, explore our section on integrations (not just ERP but other systems as well). In the rest of the article, we will focus on production data only.
3 Reasons Why Manufacturers Double-Down on Collecting Production Data Today
The full list of why it is important to collect manufacturing data could be long, but we picked the three most frequently repeated ones.
- Drive to go paperless – the goals being increased accuracy, data granularity and time savings. So many manufacturers are still handling heaps of paper, and they are looking for ways to get rid of it. The Equatorial Coca-Cola Bottling Company is a great example of going to 0 (zero!) paper, improving the quality, accuracy, reliability, and availability of data, all with the help of the right OEE software.
[Case Study] The Recipe for Success: Operational Excellence at Equatorial Coca-Cola Bottling Company - Digitalization initiatives are typically a part of an organization’s drive toward operational excellence. The expected outcomes are quick response times, productivity improvements, full cost control, and customer satisfaction. For example, one of the largest soap manufacturers and liquid cosmetics in Europe digitalized their production and increased OEE by 30%.
[Case Study] Papoutsanis Digitalizes Production With Evocon and Increases OEE by 30% - Drive to reach certain targets is another common reason. We see a lot of interest in OEE benchmarking. If that is your interest, take a look at our study on world-class OEE, a global benchmark analysis from more than 50 countries
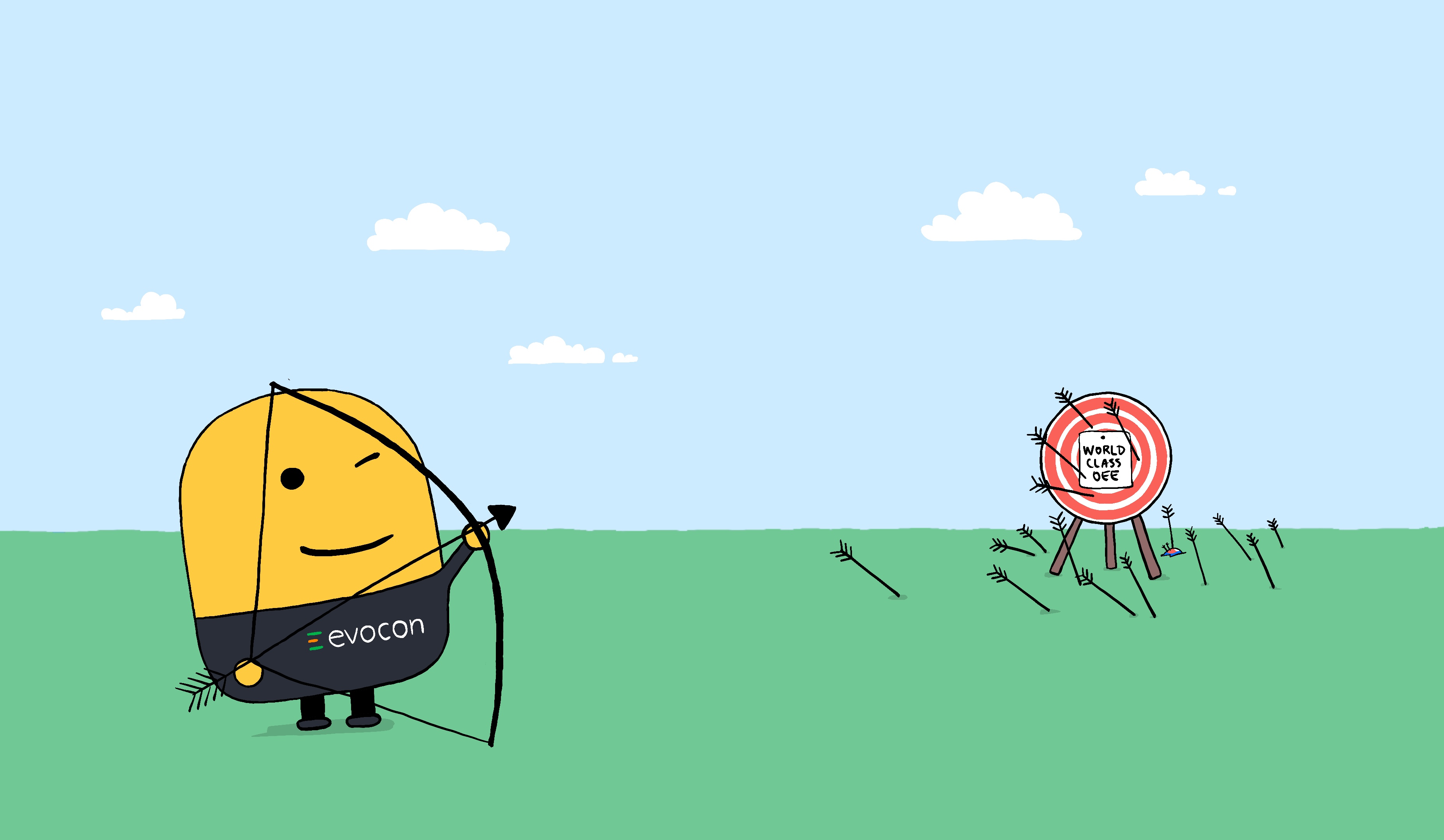
Common Benefits of Production Digitalization
Here are a few benefits brought out most frequently by the organizations we talk to.
First, the benefits that are achieved quickly – within the first few weeks:
- Visibility: everybody sees what is happening on the shop floor and why
- Better decisions: management is enabled to decide based on real-time data. For example, investment decisions, production scheduling and workforce allocation, which factories to double down on during hard times, or which factories to close down.
- Time saved: this applies to both the shop floor and office employees. If the operators have been recording data manually before, digitalization saves them time. If not, then digitalization results in smoother production, which also saves them time, albeit differently. Office workers save time handling the information needed to make analysis and decisions – now, they can get it at a glance instead of spending time trying to get it and the transform it into actionable insights.
When we catch up with our older customers, we often hear about the long-term benefits:
- Improvements to production process:
- Less downtime
- Quicker changeovers
- Better allocation of workforce
- Less scrap and/or better product quality (this one only if the organization tracks waste)
- Work satisfaction – this is an interesting one, not something that companies expect in the beginning, but something they always report afterwards. It is a direct result of transparency, everyone being on the same page, saving time due to smoother production and easy data collection.
Manufacturing Data Collection Software
Start capturing production data to improve your processes and enhance decision-making.
Strategies and Techniques for Automated Manufacturing Data Capture
In the beginning of this article you saw how long was the list of production data you could be collecting. But you don’t have to include everything at once from the get-go. So, where do you start? Here are the options:
- Choose to run a small pilot on one line with a highly motivated team – for the quickest adoption
- Choose your current bottleneck – for the biggest quick gains
- Monitor the end of your production line – for the most accurate overview of your overall productivity
The sensors are typically placed closest to the output, but this could also depend on the physical arrangement of your machines or the movement of products. Choose a place where sensors would give the most stable and reliable readings.
You do not always need new sensors, or perhaps any sensors if you have a newer machine that is capable of monitoring itself and can send the data via its PLCs.
If you are looking for specific examples, we have a few illustrated guides based on our own methods:
- Overview of sensors typically used to monitor production
- How to count products, pieces and boxes
- How to measure the weight of products
- How to measure length or volume
- How to track and monitor machine working time
- How to monitor a CNC machine
- How to monitor manual and one-off production
For collecting production data from sensors or machines and sending it over for further processing you may need an IIoT device. When choosing one, you must consider how the data will be sent: WI-FI or cables. If the data is sent via WI-FI, consider where the routers will be. If the data is sent via cables, think about how long they need to be. Finally, take into account the setup of your network: should you use your current network or create a separate one, and how will you ensure security?
Example with technical details: how to set up an internet connection for Evocon?
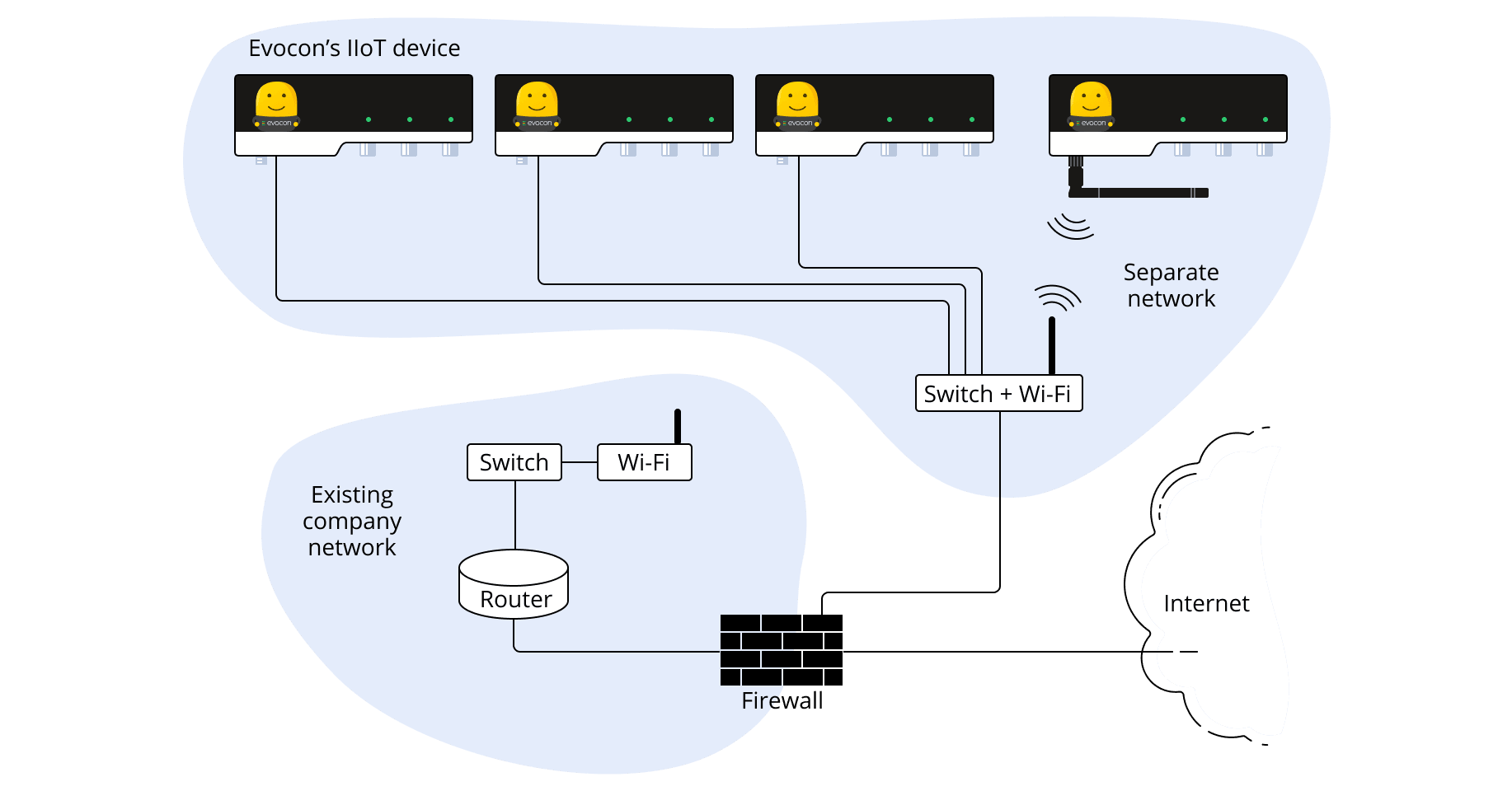
The Levels of Data Automation, Integration and Real-Time Capabilities
Where would you place your organization on the journey towards digitalization? There are a few ways to look at this.
Where you are regarding collecting and displaying data:
- Level 1: Manual. Operators take notes and enter information on paper or into Excel every hour or at the end of the shift. Someone else collects the data over a longer period of time and makes a Pareto chart or calculates OEE using Excel.
- Level 2: Automatic. Sensors on the line or PLCs send signals. Someone analyzes the data and makes reports for the management.
- Level 3: Cloud and visualization. Data is sent via cloud, processed and displayed in real-time on TV screens and accessible on phones.
Where you are regarding analyzing the data:
- Level 1: OEE or machine utilization, Pareto charts.
- Level 2: OEE per product or batch, OEE comparison between lines, manufacturing cycle time analysis, MTBF and MTTR, other advanced reports.
- Level 3: Download of detailed data, Power BI dashboards, trends and patterns.
- Level 4: Application of artificial intelligence and machine learning: predicting breakdowns, forecasting production, analyzing text input from operator notes, image recognition.
Where you are regarding integrations with other systems:
- Level 1: Production data is its own silo.
- Level 2: Production data is exported as files and imported to Excel or Power BI together with data from other departments.
- Level 3: Production data accessed via API and programmatically joined with data from other systems (ERP, CMMS), or, alternatively, an all-in-one solution that covers all the needs of the organization
Pitfalls to Avoid When Starting Digitalization
Cybersecurity
Cybersecurity is the first and most important thing to get right, especially if your organization is large. You will be dealing with internal constraints, mediating between your IT team and your providers of manufacturing data collection solutions. Here are the questions you will have to have answers to:
- Where will your production data be stored?
- How does your provider secure your production data? What encryption do they use?
- What will happen to your data after your contract termination?
- What is their data backup policy? Do they have a policy regarding how their employees are allowed to handle your data?
- Will you remain the owner of the collected production data?
- What about other entities that your provider uses in their work (sub-processors, such as AWS, Google, etc.)? Do they have a list of them?
- Is your provider certified regarding compliance with information security standards? (at Evocon, we are, by the way)
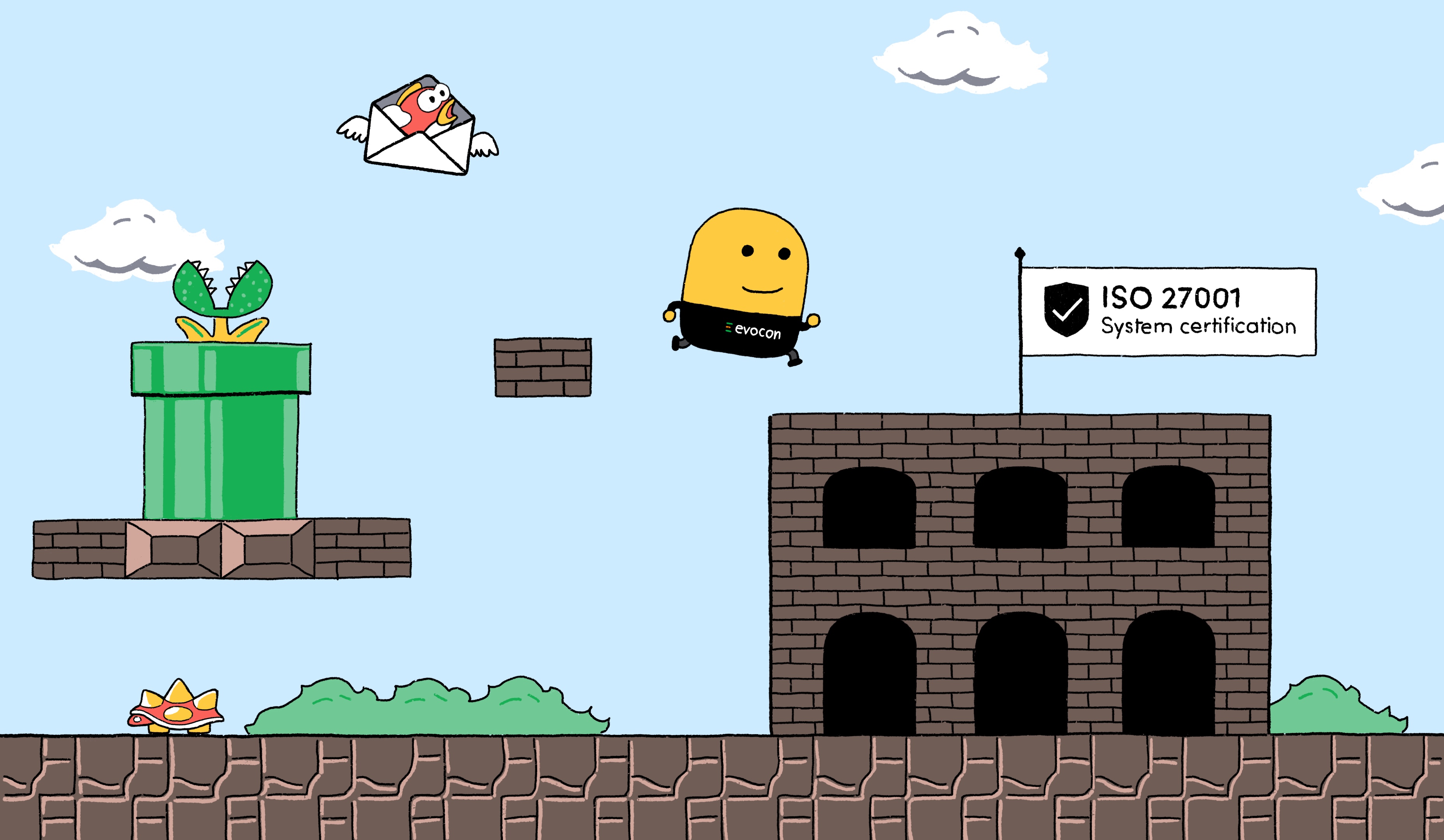
🧑💻 Tip: You need to involve your IT department early on, because misalignment with your organizational security policy can significantly slow down your implementation.
Data Accuracy
Data accuracy is very important from the very beginning, because you need to be able to fully trust the data. In the initial adjustment phase it is understandable to have inaccuracies until you get your sensors working reliably and your numbers match when you compare your production quantities from two or more different sources. If this is not ensured in the beginning, errors will accumulate, discrepancies will pop-up in your monthly, or worse, yearly reports, and the loss of trust is difficult to restore. So, invest your efforts to make sure that your hardware is set up correctly. Consider:
- Environmental conditions that could affect the readings of your sensors
- Product pile-ups or different positions that could result in mis-counting your production
- Connectivity issues – poor wi-fi, interferences, long cables
- Human factor: possibility for people to alter the data, intentionally or not
How to Overcome Resistance on the Shop Floor
This has always been an expected hurdle, as part of natural human psychology. However, things are gradually changing with the new more “digital” generation coming into manufacturing, as they do not like paper or complicated data entry systems.
And if the problem still happens, then it is easy to overcome it in three steps:
- Make it clear to operators that production data collection is about tracking production processes, and not people
- Let the operators know that automatic data collection has benefits for operators, too:
- Saves them time handling data, because they no longer need to record production quantities or downtime, and the reasons for downtime can be entered right away into the system instead of writing them down or having to remember them and then fill-out another form at the end of the shift
- Makes work less stressful, because production runs smoother, with fewer unexpected stoppages, so there is less running around fixing things
- Removes finger-pointing and blame-shifting, because of the availability of objective data
- The two steps above may be sufficient, and over time your operators will see that these benefits are real. But some manufacturers also implement additional incentives, for example, bonuses for reaching OEE targets.
How to Make Sure That Data is Not Only Collected but Also Used
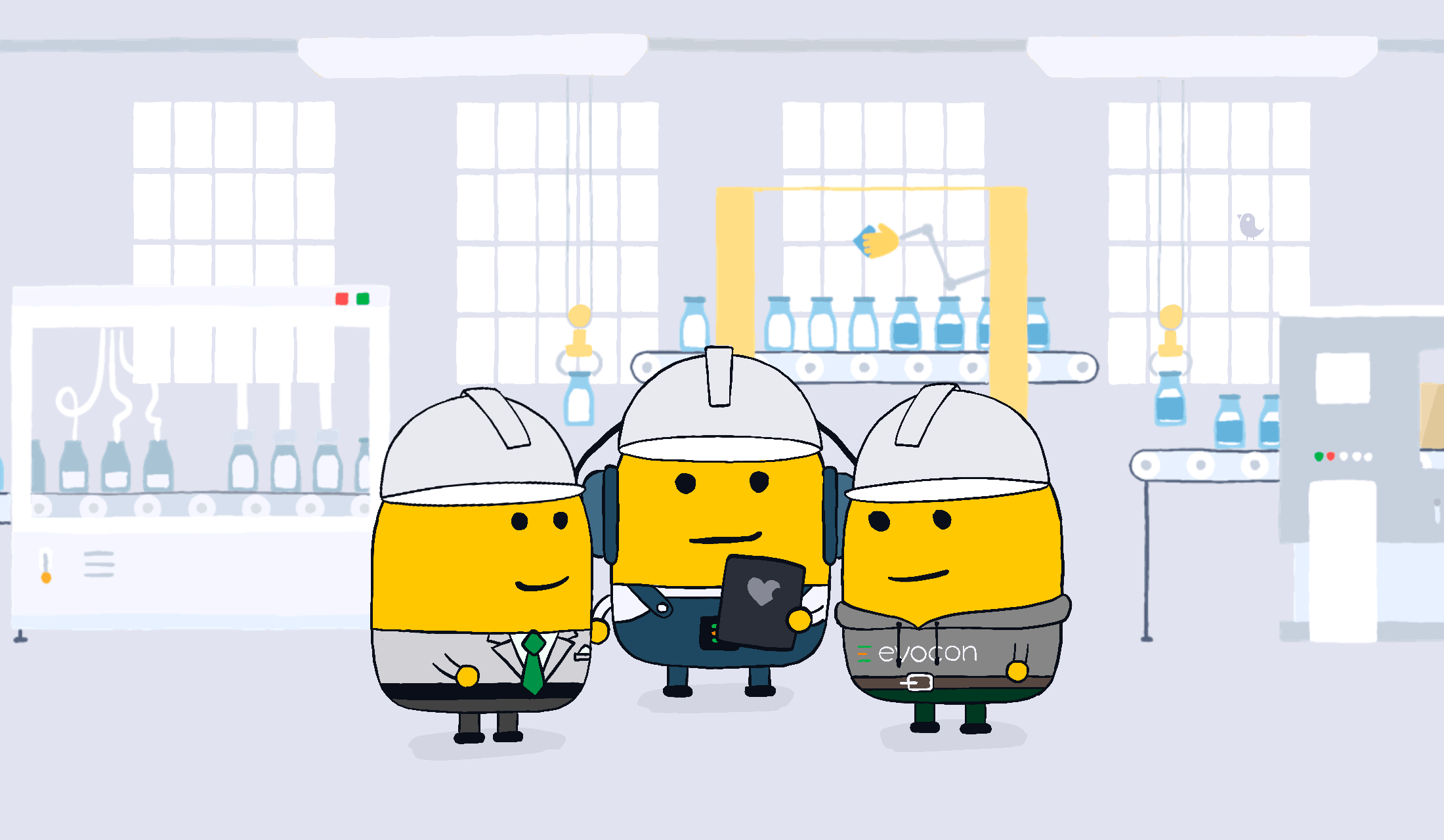
After all the effort of digitalizing your production data, it would be a shame if only a small percentage of your organization benefits from it. We know that most departments can benefit from it, not only the shop floor or the continuous improvement teams. Maintenance, quality assurance, production planning, finance, and other teams could benefit from it, too.
Here is what you need to make your production data usable.
First, you need to find a system where your colleagues can pick up their phone and with a few clicks open a page where they see what is going on on the shop floor in an easy understandable way.
A system that covers these points goes a long way to remove any friction towards data visibility across the organization.
Second, you need to build daily and/or weekly habits into the shop floor and overall operations: daily stand-ups on the shop floor, regular weekly and monthly production data reviews with managers of different departments (maintenance, quality, logistics), longer timeframe reports for the higher level management. Everyone appreciates the visibility that they get from these meetings.
Conclusion
To wrap it up, moving to digital ways of managing production data is a big step forward for manufacturers. It’s not just about keeping up with technology; it’s about making everything run smoother and smarter. From the get-go, companies see great benefits, such as clear insights, smarter choices, and time savings. Down the line, they enjoy even more significant wins like better processes, happier workers, and happier customers. This article laid out what kind of manufacturing data you can track, the results that come from doing so, and the pitfalls to avoid.
We hope this helps you on your way to hitting your goals.