Investments in manufacturing are multi-faceted decisions that encompass more than just buying new machines. They can also involve increasing the Overall Equipment Effectiveness (OEE) of your existing equipment. OEE is a critical metric for productivity and process efficacy, but how does it stack up against the attraction of shiny, new machinery?
Quick Look Into Why OEE Matters
In one of our previous deep dives, we explained the financial implications of OEE and how it can help identify profitable product lines based on their respective production efficiencies. We discovered that a seemingly insignificant 1% shift in OEE could potentially affect profitability by an estimated €44,000.
Now, let’s focus on the decision between pouring funds into new equipment versus improving the efficiency (OEE) of your current machinery.
For a comprehensive understanding of Overall Equipment Effectiveness (OEE) before proceeding, consider pausing and reading our articles on what OEE is and how to calculate OEE. Already familiar with OEE? Just remember, it’s a measure of how effectively we utilize our manufacturing plant and equipment and where our efficiency gaps lie.
Decoding Investment Decisions: A Look at ROI
It’s common knowledge that an OEE of 50% outshines 40%, but how does this influence profitability per unit? How does it shape our evaluation of new investments or our strategies to boost profitability? What should be our top priority?
The answer lies in understanding Return on Investment (ROI). ROI defines the profit generated from a specific investment, providing crucial insights for assessing potential opportunities and justifying financial decisions.
By understanding ROI, manufacturers can answer critical questions, such as:
- Where should we invest our capital?
- How do we gauge the performance of an investment after its implementation?
- How can we make sure that the return on investment is optimal?
- How do we evaluate the maximization of our investment in new machinery?
Regardless of the chosen investment direction, the ultimate goal should be to enhance the production process. This essentially means accomplishing more with less, which could translate to:
- Reducing the production time per item
- Minimizing waste
- Automating routine tasks
Furthermore, investing in new machinery or improving effectiveness by minimizing downtime, facilitated by OEE software, can add significant value to the business.
Making a sound investment decision requires a holistic view that considers additional factors such as:
- Decreasing overtime work or reducing the number of shifts to meet production targets
- Lessening the need to hire and train new personnel
- Reacting swiftly to changes in demand and production schedules
- Shortening delivery timelines
A thorough understanding of these elements and a clear ROI perspective will enable businesses to make informed investment decisions that propel their growth and profitability.
OEE software
Discover the true potential of your factory. Free for 30 days.
To Invest or Not to Invest in New Machines?
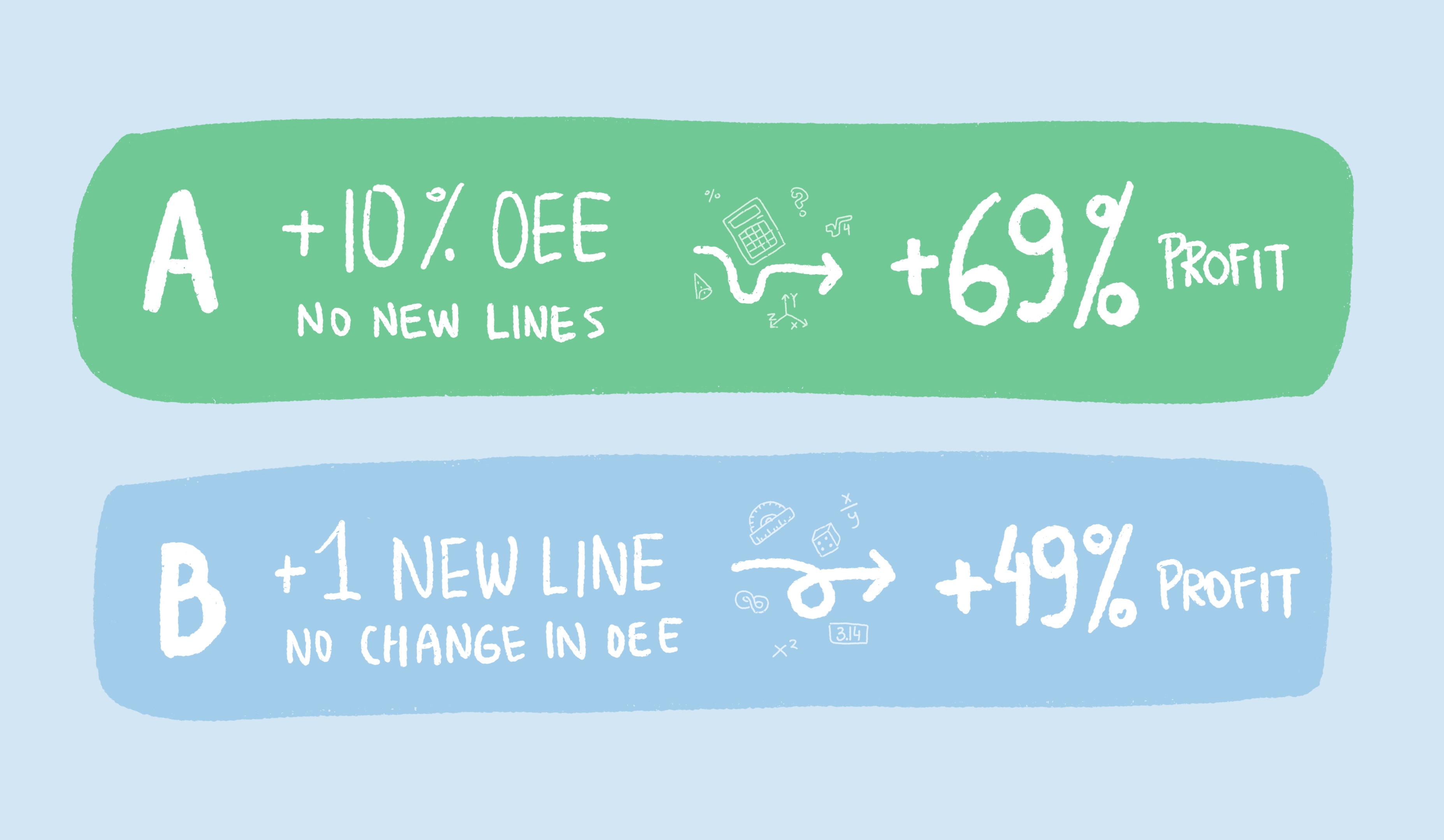
Investment decisions are a delicate balance of costs and profits. When a company contemplates buying new equipment, it’s generally to meet increased demand or optimize long-term costs. Let’s use a simple example to clarify the decision-making process.
Assume we need to boost the production capacity of our factory. We currently have three production lines and contemplate adding a fourth. Before we proceed, we must calculate the costs of operating the new line, including personnel, additional equipment, and other required resources.
Furthermore, we must reflect on our OEE and how it impacts our current output. If it’s at 40% today, and we believe we can boost it by 10 points to reach 50% on one production line, it would mean a 25% increase in output. In other words, we would produce 25% more products using the same resources.
Note on OEE: when you are doing OEE analysis and considering it in your investment decisions, it is critical that you have an objective view of it. This means not relying on what you have on paper but using accurate data collected with OEE software.
The mathematics of the investment decision
Let us assume that the OEE improvement on one line can be achieved by investing €45 000 in organization, maintenance, and staff training. However, the new line would cost us €1 000 000 and an additional €18 000 to operate.
Our decision, then, revolves around these two scenarios – enhancing the efficiency of our existing production line or buying the new line with all its associated expenses.
Scenarios | Description | Variable cost/ 1000 pcs | Fixed cost + Depreciation |
Scenario 0 | Current situation | €30 | €450 000 |
Scenario 1 | Investment in existing line | €45, €15 increase for maintenance, training, organization | €450 000 |
Scenario 2 | Investment in a new production line worth €1 000 000 | €35, €5 increase due to the staffing of the 4th line | 500 000€, due to an increase of the new line depreciation |
The above-mentioned 3 scenarios are shown in detail in the table below:
Data | Scenario 0: Current situation | Scenario 1: Investment in existing line | Scenario 2 : New production line |
Availability | 60% | 70% | 60% |
Performance | 75% | 80% | 75% |
Quality | 90% | 90% | 90% |
OEE | 40% | 50% | 40% |
Production (pcs) | 2 400 000 | 3 000 000 | 3 000 000 |
Selling price/pcs | €0.60 | €0.60 | €0.60 |
Production cost/pcs | €0.35 | €0.35 | €0.35 |
Profit (gross)/pcs | €0.25 | €0.25 | €0.25 |
Profit (gross), total | €600 000 | €750 000 | €750 000 |
Variable cost / 1000 pcs | €30 | €45 | €35 |
Variable cost, total | €72 000 | €135 000 | €105 000 |
Fixed cost + Depreciation | €450 000 | €450 000 | €500 000 |
Total cost | €522 000 | €585 000 | €605 000 |
Net profit | €78 000 | €165 000 | €145 000 |
Turnover | €1 440 000 | €1 800 000 | €1 800 000 |
% Profit | 5.4% | 9.2% | 8.1% |
Increase/decrease, % Profit | – | 69% | 49% |
Investment into improving the OEE of our current line would increase profitability +20% compared to investment into a new production line.
Your Context, Your Decision
Now, replace the above numbers with your own. You will see different numbers in the cells, but you will most likely reach the same conclusion: investing in OEE calculation and improvement costs significantly less than investing in new equipment.
Moreover, investing in improving OEE is not isolated to one production line or machine. Instead, you get the OEE improvement’s combined effect in your factory. Whereas if you buy new machines without improving your processes and effectiveness, your improved output is very isolated and does not help you maximize your resources to the fullest.
And even if your OEE is running at 80% today, the calculations and conclusions are probably the same.