Faced with a growing number of challenges, from ongoing supply chain disruption and rampant inflation, to increasingly expensive and more difficult to source raw materials, most manufacturing organizations need to be more efficient, agile, and leaner than ever.
One of the ways in which manufacturers can drive tangible efficiency gains is by closely tracking production losses and accurately measuring production quality, with a view to improving both going forward.
But improvements can only be made when the current state of play is known. This can happen through digitalization and, in particular, data. That’s why effectively monitoring OEE is such a common goal among manufacturers.
Manufacturers can identify where potential improvements can be made by accurately capturing and thoroughly analyzing loss and quality data.
However, in their haste to realize data-driven benefits, some manufacturers make a common mistake: to neglect data standardization at the beginning of their production monitoring journey. While it may seem like an incidental oversight, it is a problem that is inevitably more difficult to resolve further down the line.
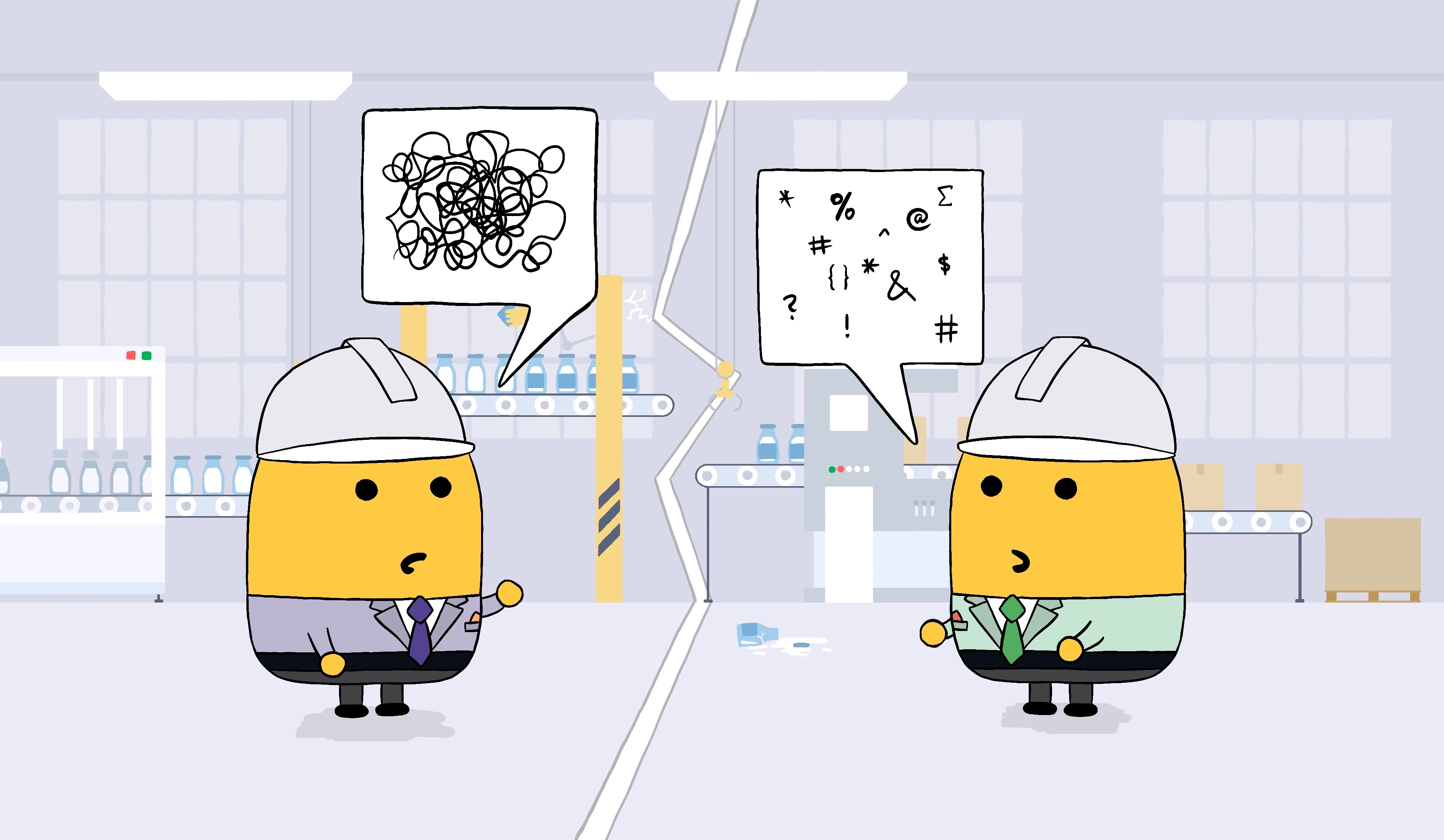
Learn more: How Digitalization Improves Quality Control in Manufacturing
What is Data Standardization?
An easy way to understand data standardization is when working with a spreadsheet containing data from different sources. Often, said data is all the same, but its formatting differs e.g. some date fields may read “November 10, 2022” while others read “11/10/2022”. When you start processing this data and making it all in the same format e.g., “MM/DD/YYYY”, then this is data standardization in action.
In brief, data standardization is the process of creating a set of standards, then transforming any data you have – regardless of its source – to adhere to those standards.
From the manufacturing perspective, imagine all the data captured from production lines and machines in a single plant. Or from multiple plants, for that matter. It’s undoubtedly going to be in different formats unless you standardize it. And if you don’t, then any analysis you want to conduct will be, at best, difficult and, at worst, fruitless.
So from the manufacturer’s perspective, data standardization, for example, means:
- Having the same loss reasons (downtime, speed, quality) used by all operators.
- Being able to localize (translate to different languages) loss reporting.
- Providing different types of access to data, depending on the role and function of employees.
In other words, data standardization helps your organization speak the same language, no matter where sites are located.
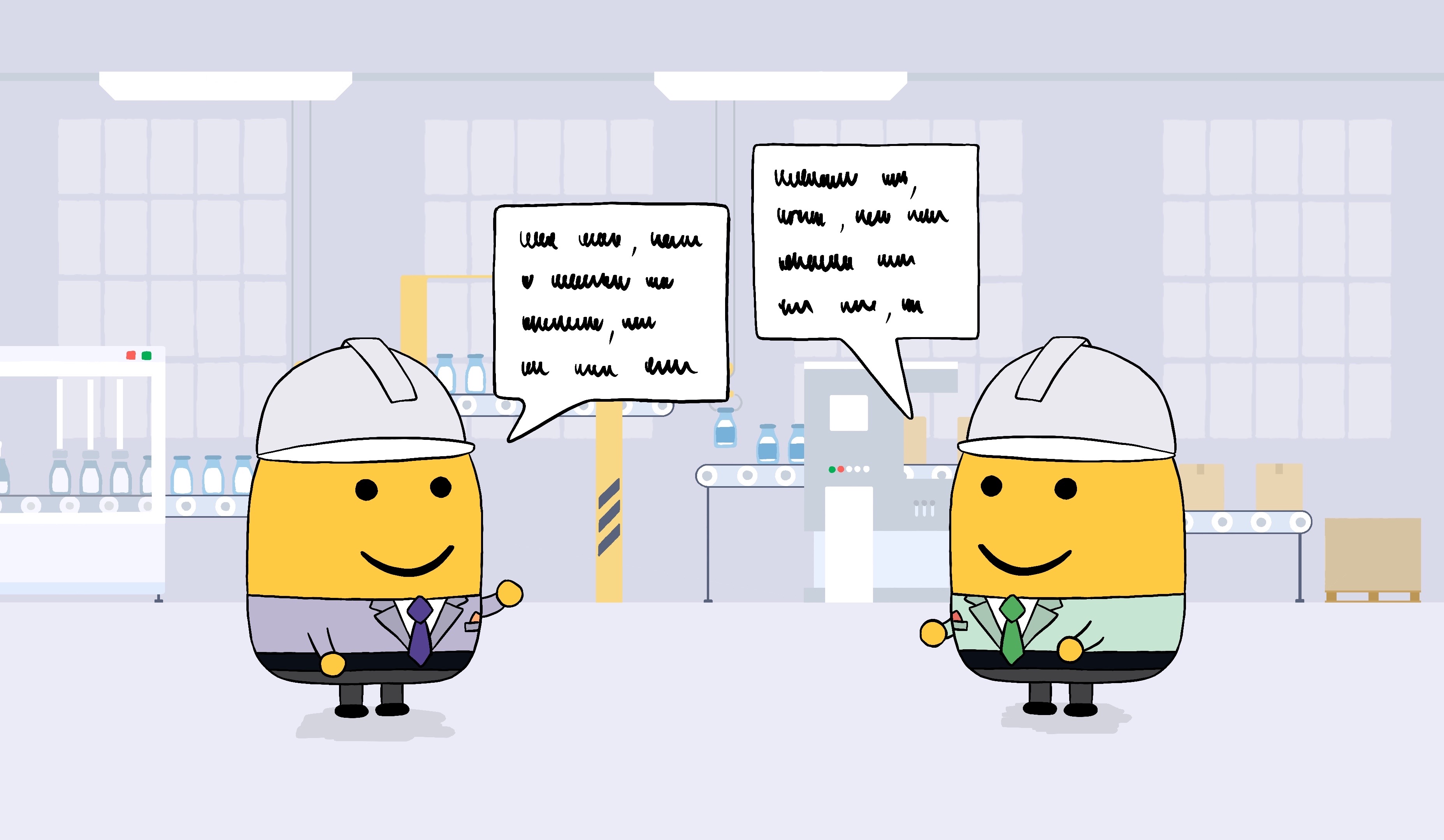
How to Know if Data Standardization Is a Challenge?
During our own conversations with manufacturers that have multiple factories, either in one country or many, there are several common challenges associated with the lack of data standardization.
You can try and answer the following questions to understand if standardization is a challenge at your organization.
- Can we compare factories, and production lines and find best practices?
- Do we benchmark our progress to see if our improvement initiatives are working?
- Are we able to update our shop floor personnel on how they are performing?
- Can we advise our stakeholders of our ongoing progress?
- Do we update our customers with loss and quality metrics?
Your entire digitalization strategy will likely be questioned if you cannot leverage data to answer these fundamental questions.
Why Focus on Data Standardization?
While achieving data standardization across your entire manufacturing estate may seem daunting, the rewards are substantial.
Improved efficiency in decision-making
With standardized data, you can electronically provide your central and regional productivity teams with a more accurate representation of the actual situation. And by having a consistent system in place, it becomes easier to identify patterns and trends in data, allowing decisions to be made quickly and efficiently.
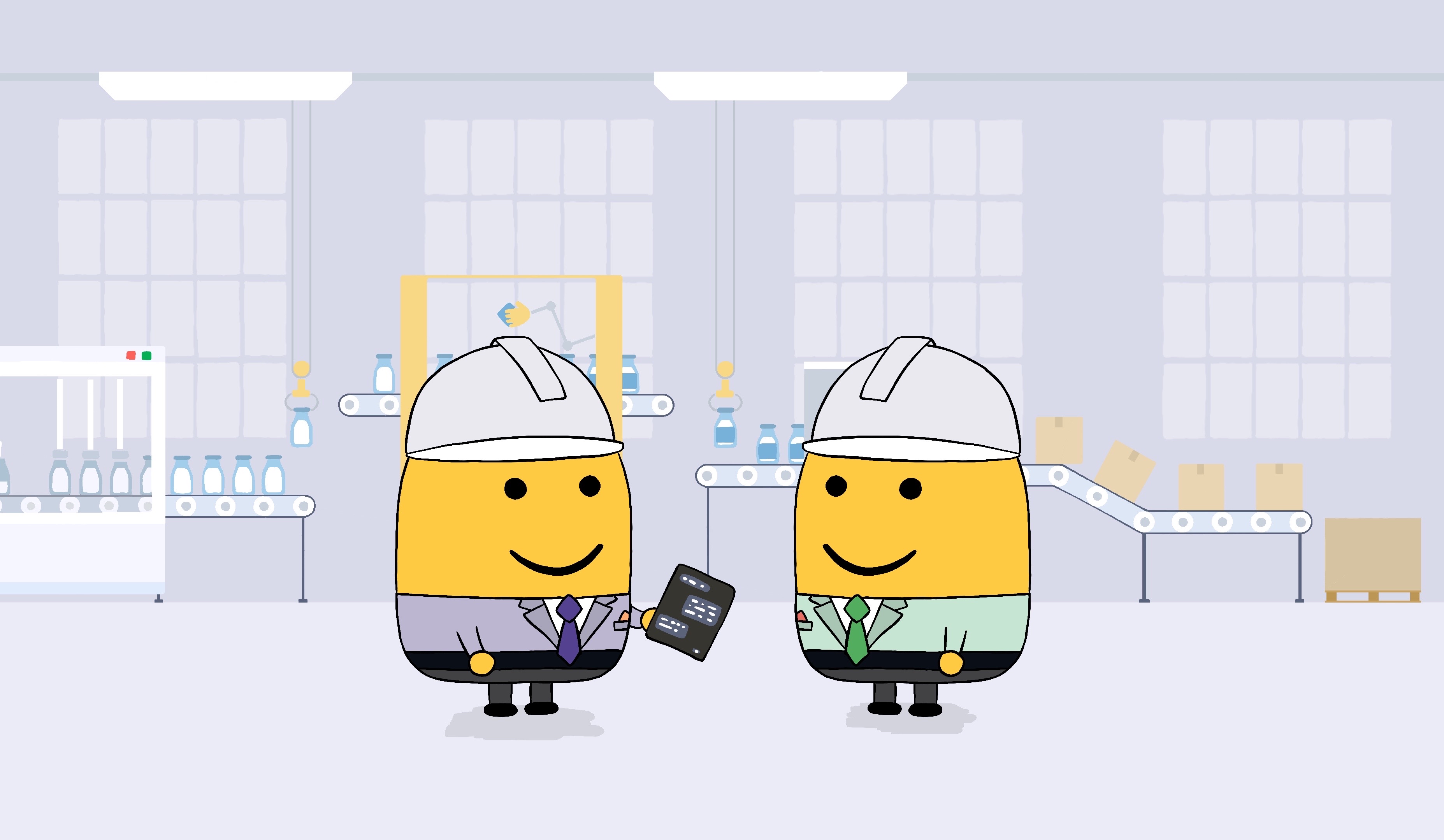
Drive cultural change
With losses accurately captured and standardized data shared among personnel, many organizations find that their culture undergoes a shift. Employees tend to proactively take ownership of their areas and strive to improve them on an ongoing basis. This is especially powerful when friendly competition occurs between sites, each trying to outdo the others in terms of performance. An added bonus here is the knowledge transfer that often occurs between factories.
Benchmark to see how you are improving
As we’ve already mentioned, you can’t benchmark your distributed factories without standardized data. Benchmarking allows you to see each facility’s baseline and identify possible areas where improvements can be made. Regular reviews can then be used to assess progress against the improvement plans you’ve made.
Identify best practices and drive cost-savings
Firsthand insights from one of our clients revealed how leveraging data uncovered quality issues which were a direct cause of downtime. The client found that one of its products sometimes ran with high availability and sometimes did not. Upon further analysis, the client discovered that some of the bags its product was placed in were liable to fail, resulting in production downtime. Bags from a different supplier did not have this problem, which is why availability varied.
With this knowledge, the client reached out to the supplier for a solution. With higher quality bags, the client no longer has the varied availability problem. The takeaway is that quality data can help uncover issues that may otherwise remain unknown.
Production Tracking Software
Start accurately capturing and analyzing loss and quality data with Evocon’s built-in features that support data standardization across different plants. Free for 30 days.
Data Standardization Benefits in Action
Leading global fertilizer company, Yara International, had already adopted lean principles to boost its competitiveness. However, the company was still struggling to roll out effective OEE monitoring across its multiple fertilizer terminals.
Among others, one of Yara’s challenges was standardizing OEE monitoring across its global network of sites, which spanned five continents.
After implementing Evocon, Yara’s operators – regardless of their geographic location – could easily record losses using a set of predefined and standardized causes.
Having standardized its loss-monitoring process and reporting for over 135 global production lines, Yara could accurately benchmark differences between countries, regions, and terminals.
Furthermore, worldwide standardization enabled Yara and its operators to speak the same language across the board. As a result, awareness, and expertise have increased; so too has Yara’s OEE, going up by 15% on average on all the production lines.
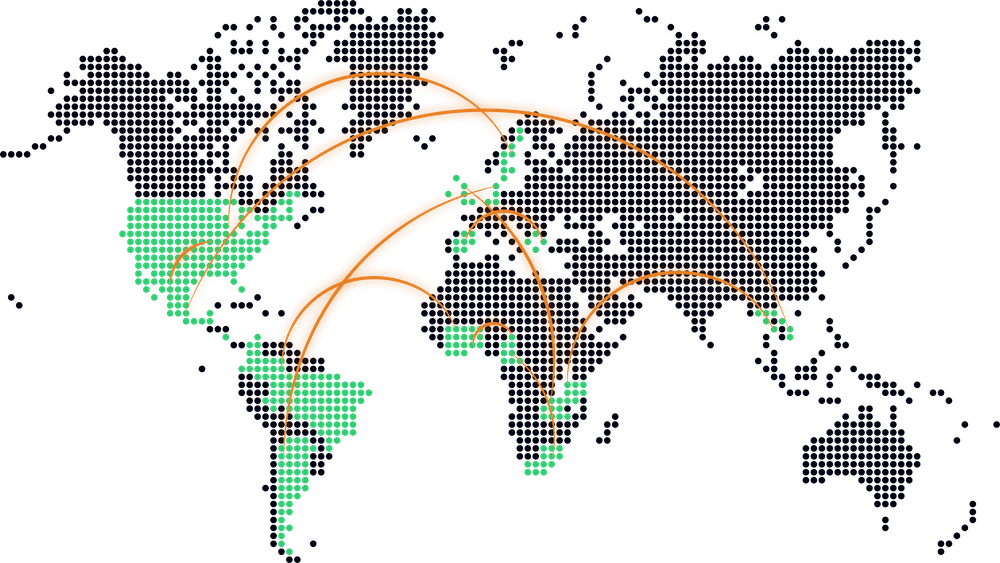
Read the full case study: Digital Transformation Helps Revitalize Yara Operations
What to Look for When Choosing a Solution
Partnering with the right solution provider for loss tracking can help you immediately stay on the right track. The following questions help you determine if the provider you are considering supports standardization in the short and long term:
- How well does the system support both local factory and multi-factory setups?
- Can the categorization of losses be localized?
- Does analytics support localization and benchmarking capabilities?
- Does integration support localization?
- Is there enough flexibility to support local loss tracking?
- Can user rights be set up so that factories can monitor each other but not change data?
- Is there global data in local language functionality, so every local user can benchmark themselves against other factories, as well as tap into global know-how?
- How well does the solution support rapid deployment with aggressive timelines? Long and resource-heavy multi-factory implementations can jeopardize the utilization and activation in the post-implementation period.
So if your organization is comparing multiple service providers for OEE and loss tracking, do not neglect the above considerations. A system that has built-in features that support data standardization will play a critical role in your digitalization strategy in the long term.