Full transparency on the shop floor is two-sided: it requires addressing both the technical and human aspects of operations. The technical aspect means understanding and optimizing the performance of equipment. The human aspect requires creating an environment where people can thrive and contribute.
This already multi-layered challenge is even harder in production sites that are situated in less-developed geographic locations. Which is why this case study is interesting – it centres around Mars’ operations in South Africa, where they have a significant food manufacturing and distribution hub.
Mars’ Drive to Modernize Manufacturing Operations
A few years ago, Mars began to modernize their operations. In the US and Europe they turned to using real-time data across their whole supply chain and set ambitious goals to reduce downtime, improve quality, and achieve energy efficiency.
At the time, Jo-Ann Kitshoff was responsible for operations in Mars’ factory in Cape Town, South Africa. She recalls that downtime used to be recorded manually, by writing down notes and entering them in an Excel spreadsheet. As per her calculations, about 30% of downtime was unaccounted for – meaning, they did not know what exactly that time was spent on. Asking different people led to different answers.
This 30% gap was an “unknown unknown”. To hit the downtime reduction targets set by the company, this had to become a “known unknown”, before anything else.
Challenges of Mars’ Cape Town Site
- Firstly, there were certain financial constraints that limited access to expensive technology, which is more easily available in the US or Europe. The solution had to be both simple and effective. That was how they chose Evocon.
- Secondly, their employees (called “associates” in Mars) are often from previously disadvantaged families that had no access to digital tools, which contributes to a steep learning curve and difficulty to create a relaxed working environment. Mars does have strong employee wellness programs in place (such as their “Mars Be Well”, “Ombudsmen”, etc.), and here we will also explain how the human side of production was addressed in the Cape Town site to create more transparency.
Mars approached these challenges very methodically. Soon, they reached their first goal of zero unaccounted downtime.
“Now we have 0% unaccounted time. Every single loss is accounted for, we have a very good understanding of the downtime and therefore we can plan improvement initiatives with solid data to make decisions. That was a very big step for our business. Now we have full visibility in a live manner of what is happening on the shop floor.”
— Jo-Ann Kitshoff, Continuous Improvement Technologist
Let’s see what steps they took to achieve that.
What steps did Mars take to get to zero unaccounted downtime?
- Visibility: tablets and TV screens
After connecting a line to Evocon, the visualization of production was connected to big TV screens next to that line. This provided a real-time view of ongoing production and access to historical data for meetings that took place around these TVs.
The same visual was connected to tablets, which let associates carry them around the workplace and always be aware of the situation. - Traffic light system
The way that Evocon visualizes production fit well with the overall traffic-light system approach in the factory: green means everything is okay, red means – take action. In that regard, the newly implemented production data collection did not need any additional explanation. - In-depth training about the benefits of adding downtime reasons
The descriptions of downtime reasons added by human beings are invaluable on the shop-floor, but the resistance to do it is also often present, because someone still needs to write this down, as opposed to fault codes coming straight from the machines.
That is why the ease of entering this information is so important, and Evocon has gone through numerous usability tests and improvements over the years, so that it would be a quick and easy action for the operators. In Mars’ Cape Town site, operators learned the system quickly by themselves, very little training was needed.
From the manufacturers side, they have the responsibility to explain to their associates, why it is beneficial to do it: to remove finger-pointing and to help solve the issues in production, making the workday easier and happier for everyone. - Connection to employee promotion system
Mars uses a system where associates can use their performance metrics to apply for promotion and increase their pay. They have many ways to do that, and collected production data gives another objective way to do that. A massive performance driver was a Factory Incentive Plan (FIP), wherein the Unplanned Downtime was a clear metric that the shop floor could track and drive. Achieving this resulted in a bonus to all.
All in all, operators in Mars were eagerly waiting for Evocon to be connected to their line, asking “when can we get it?”
The Results
Let’s let the data speak for itself. Here is the all-time OEE breakdown on the line in Mars’ Cape Town factory where it was implemented first (OEE in black, its components in other colors):
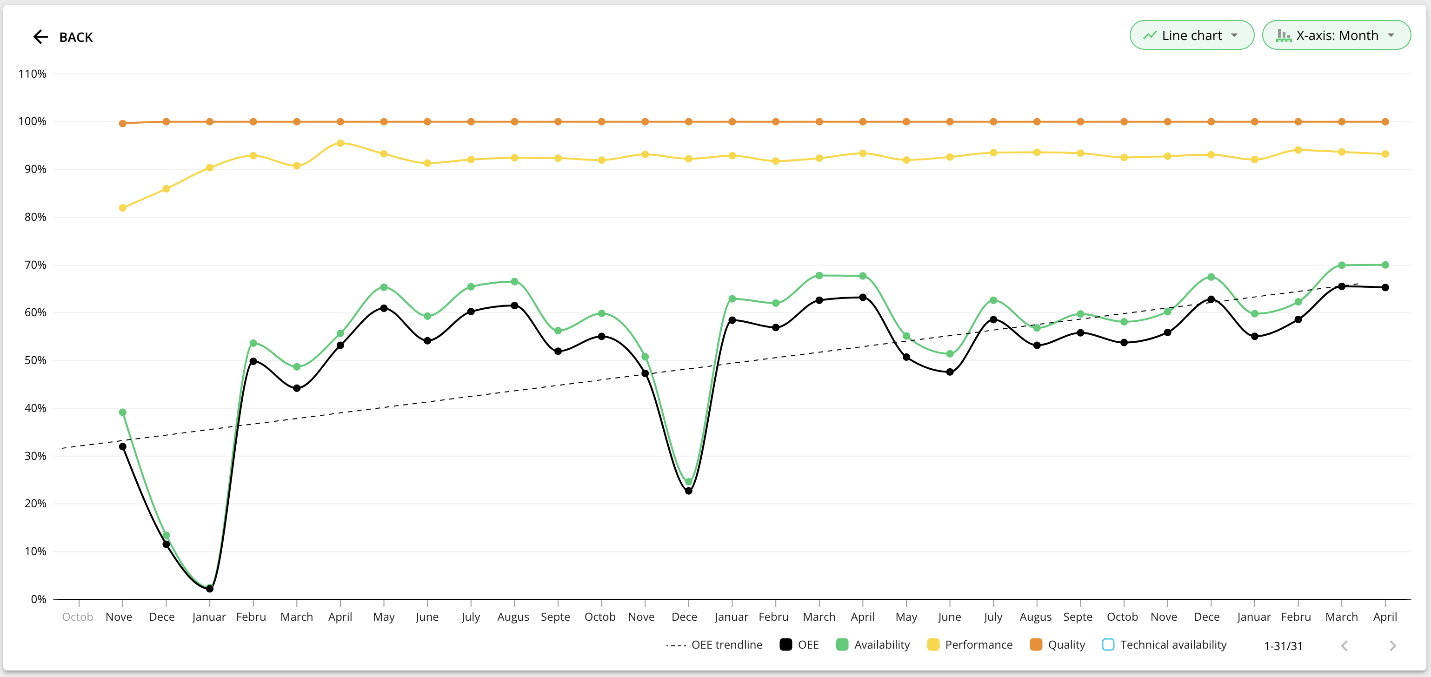
This chart shows progress from the very first day until now.
Jo-Ann remembers one specific example of an improvement that was implemented based on data they collected:
“We’ve had a couple of ongoing issues where we weren’t 100% sure what was going on. One good example – machine that puts pouches into boxes. These pouches were getting stuck. Thanks to Evocon I didn’t have to go through a lot of paper or Excel spreadsheets, all I had to do was find the issue in the data and look when it happened. It was more prevalent on one specific product on one particular shift. The reason was the setup of the machine and the flowability of the product. Since the flowability is more difficult to address, we made changes to the packaging to support this product.”
Here is the data from Evocon to illustrate this improvement between 1 Jan 2022 and 21 Dec 2023:
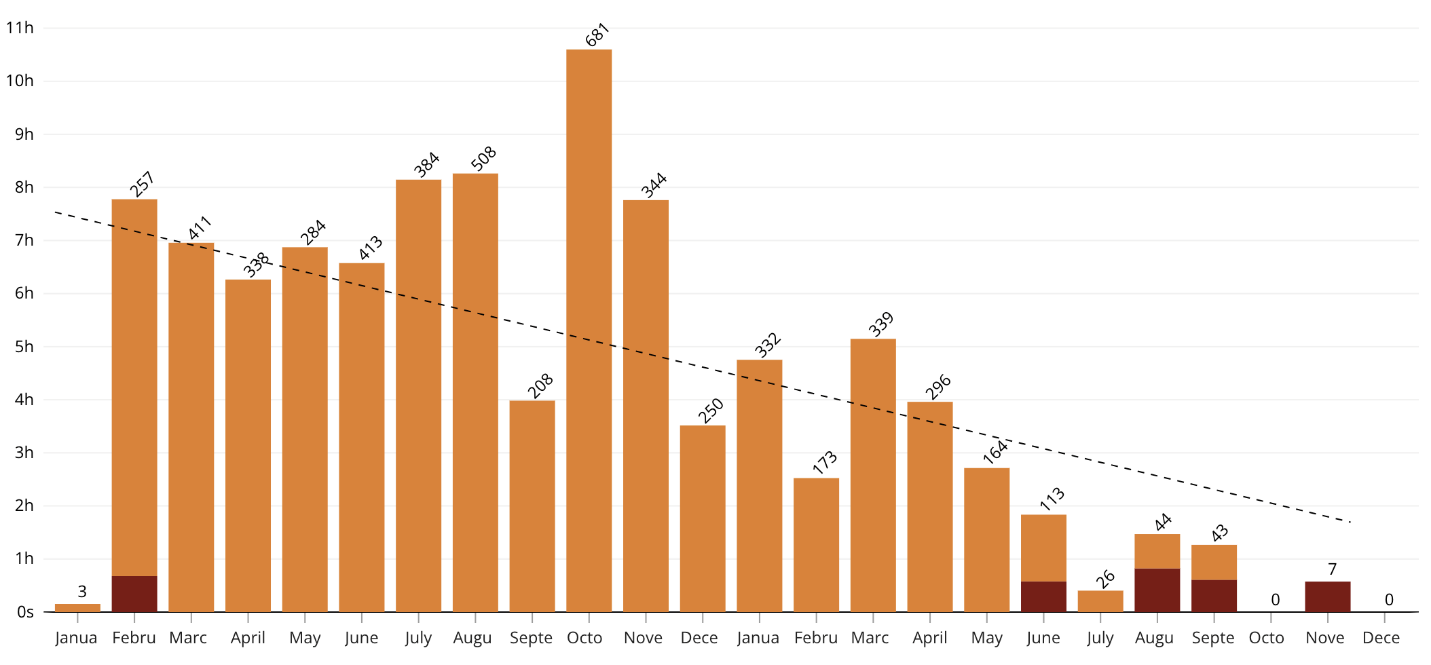
Bonus lessons from Mars
Next step after achieving transparency is to reduce downtime. Mars is doing that by integrating data from various sources, finding root causes and empowering their staff to solve them. Jo-Ann shares some lessons that Mars has learned on this journey.
- No standalone products. This point came up when we asked Jo-Ann what would be one thing we shouldn’t take away from Evocon. She replied: “Do not take away my connection to Power BI”. Jo-Ann does not approve of stand-alone tools. Business needs full connectivity to make informed decisions. At this stage in her journey, she achieves that with Power BI and appreciates it when dealing with suppliers who understand how to provide data in the right format. In the future, Mars has plans to achieve even tighter integration between their data sources.
- Cross-functional problem-solving teams. Traditionally problem solvers have been technicians, because they are the experts of the equipment. However, Mars has learned to include other stakeholders: people who know the profile of the affected product, people who know how the equipment runs, also anyone who is affected by the problem and anyone who might know the answer to it.
- Bottom-up improvement initiatives. As mentioned above, Mars puts a lot of emphasis on employee empowerment. This also applies to problem solving and generating improvement initiatives. There is a lot of value when front-line workers start thinking and looking at bigger trends. This is not an easy thing to achieve due to culture inertia. Jo-Ann mentions that operators are hesitant to come forward with their ideas. That is why Mars organizes sessions where associates are prompted to provide suggestions, which then earn them bonus points towards bonuses.
Conclusion
To wrap this up, Mars’ Cape Town factory has shown how using real-time data, modern tech and focusing on the people can make a big difference. They have eliminated unaccounted downtime, increased transparency, and are working on reducing their downtime. All the while treating their staff with empowerment and respect.
To us (Evocon) this is an inspiring client to work with – and we hope that you also find a way to apply the information above to your own business.