ThaiNamthip Corporation Public Company Limited is the leading Coca-Cola bottler in Thailand and Laos, producing 400 million unit cases annually. It operates five manufacturing facilities in Thailand and one in Laos. Since late 2024, ThaiNamthip has forged a partnership with Swire Coca-Cola, the fifth-largest bottling partner of The Coca-Cola Company globally, with operations in the USA, Greater China, and Southeast Asia.
In this case study, we learn how ThaiNamthip significantly improved efficiency by rapidly implementing Evocon across three of its facilities with the support of Evocon-accredited partner Beyond 4.0.
ThaiNamthip’s Digital Evolution
ThaiNamthip ramped up digitalization in its manufacturing operations in 2021, including line efficiency monitoring. In this context, during a benchmark session with Coca-Cola bottlers, the ThaiNamthip team discovered how Evocon is used at Equatorial Coca-Cola Bottling Company (ECCBC). This led them to implement and test Evocon in 2024. The initial implementation of Evocon at ThaiNamthip started with one line in their main facility in Pathum Thani. After the first success and the quick implementation, Evocon was installed on two lines in Laos at another facility in Hatkiang, just north of the capital Vientiane.
Following the successful implementation at the Pathum Thani and Laos facilities, two more lines were installed at ThaiNamthip’s newest facility in Lampang.
The Need for a Plug ‘N’ Play Line Monitoring Solution
ThaiNamthip sought a solution to address the specific needs of its diverse operations in Thailand and Laos.
Thailand:
The ThaiNamthip Continuous Improvement Team, a highly skilled and organized group, looked for innovative ways to enhance efficiency while minimizing implementation costs. Evocon emerged as a strong contender, offering a free trial period and plug-and-play technology that further minimized implementation costs.
They recognized Evocon’s suitability for their lower-volume, lower-profit lines, where existing high-cost systems were not financially viable. Transitioning to Evocon enabled them to meet profitability thresholds without substantial investments.
Laos:
The facility in Laos, which is less mature than its Thai counterparts, lacked a history of digital solutions. This resulted in a lack of data to track and analyze efficiency. Additionally, tracking operations and obtaining accurate floor-level data proved challenging.
The Lao facility also experienced higher staff turnover. Thus, implementing an intuitive, easy-to-use tool that could boost operator engagement was instrumental in their digitization process.
Accelerated Implementation: Evocon Deployed in Less Than 7 Days
ThaiNamthip prioritized the rapid implementation of Evocon across their facilities. The initial implementation and testing of Evocon in Pathum Thani and Laos took less than one week. With the experience of their continuous improvement team and with help from Evocon partners Mohamed Taher Mouni and Mohammed Hijari, they installed Evocon in Pathum Thani in one day, followed by two days in Laos.
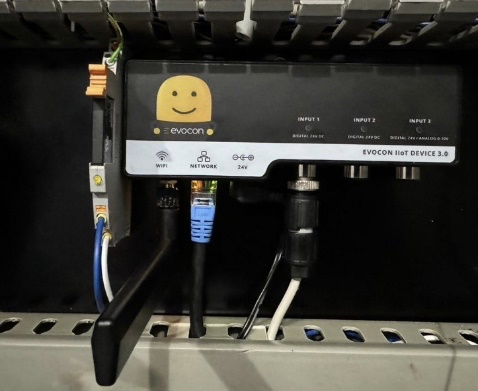
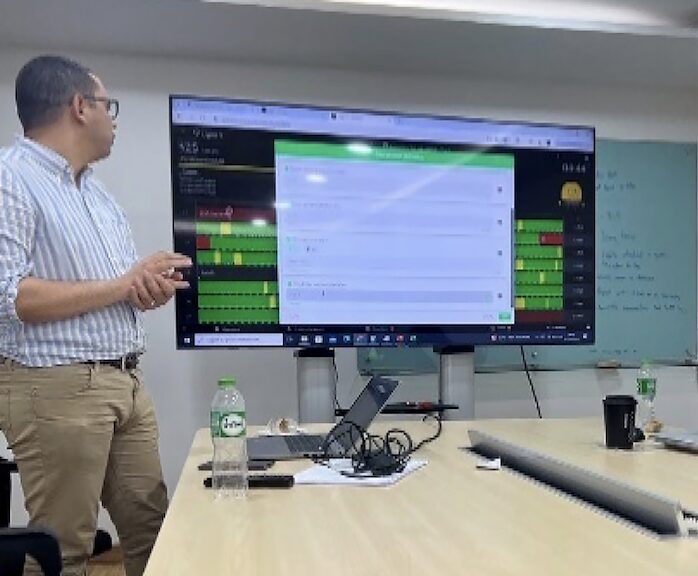
As a result of the successful and fast implementation in Pathum Thani and Laos, the ThaiNamthip team decided to install Evocon in Lampang. This was conducted in the months following the initial installation by ThaiNamthip themselves, with Evocon partners configuring the devices remotely.
They were able to get everything set up quickly thanks to a few key reasons:
Proactive Planning
The team at ThaiNamthip was highly prepared for Evocon’s arrival. The continuous improvement team worked on a plan together with the Evocon partners to prepare everything essential before their arrival. Two weeks before the partner visit and installation, they provided a comprehensive, hour-by-hour itinerary detailing the entire installation trip, including locations, machines that would have Evocon installed, and scheduled training sessions. This level of detail made the whole process run smoothly.
In Thailand, this preparation meant that when Evocon was implemented, the operators understood the system and were able to start using Evocon as soon as the training was completed.
Effective Training
With experience running technically advanced facilities, ThaiNamthip recognized the need for training for smooth implementation. They organized a one-day training program in the first factory, focusing on training the managers — they would then be responsible for training operators. Importantly, this enabled the managers to relay the training and messaging in Thai rather than English.
The Laos facility’s plan included two days of initial training. However, they could cover all the necessary training in just one day, allowing the setup to be completed the next day. Impressively, after setting up their second line in Laos, they took just 25 minutes to start using Evocon data. Along with training on Evocon, the Laos team has implemented training on efficiency and continuous improvement to further their development.
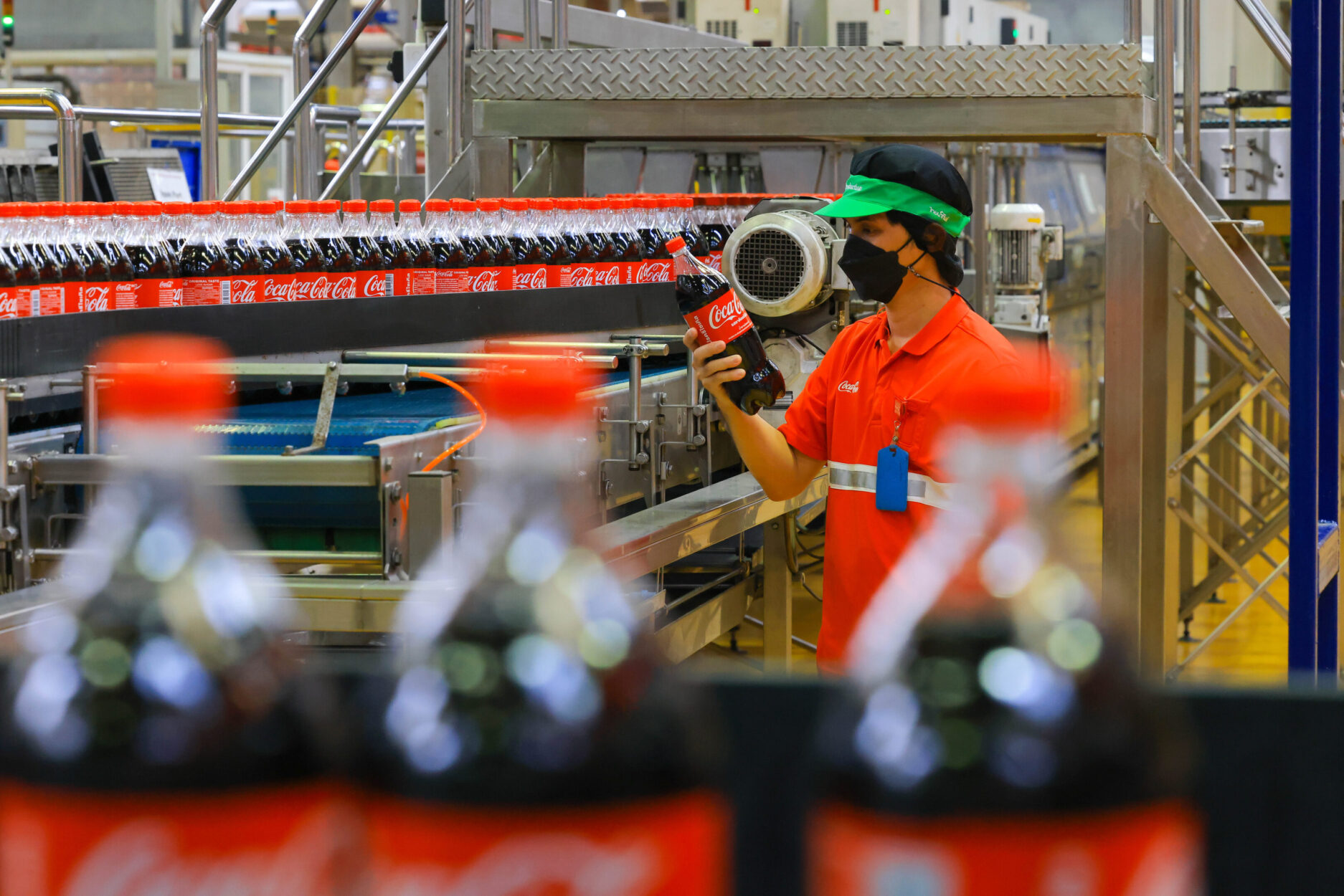
Focus on Continuous Improvement
ThaiNamthip’s proactive approach to continuous improvement was evident in their training strategy. The team used their deep understanding of operational excellence to anticipate potential operator concerns, addressing them directly during training. This ensured that operators understood how to use Evocon and why it was essential for achieving their shared efficiency goals.
Operator Adoption — The Main Implementation Challenge
Due to ThaiNamthip’s preparation, the implementation was quick and efficient, but there was a minor challenge with the adoption from the operators on the shop floor.
As Thai operations are more mature and are more used to the digitalization process, there was not much resistance from operators. With trust in their management team and training, they adapted quickly to Evocon and became actively engaged early in the process.
In Laos, however, with a less mature operation and operators less accustomed to digitalization, there was initially some resistance from the shop floor. They were concerned about the red bars in Evocon and needed to understand that they are a starting point for action, not just an alert. Through training, the team learned about the solution, the efficiency mindset, and why accurate tracking and OEE (Overall Equipment Effectiveness) can help. With the addition of Evocon to their operations and education, they saw an improvement in employee engagement within weeks.
In both Thailand and Laos, ThaiNampthip found that Evocon fosters curiosity in the operators. This encourages them to think about problems and solutions and is a key difference between just having the data and having a system that the operators want to use.
How is Evocon Used Day-To-Day?
In Thailand, operators were highly engaged with Evocon from the start. Similarly, once training was completed in Laos and operators understood the “why” behind the system, the operators began using Evocon regularly throughout their shifts.
Daily Meetings
Every day, teams across different functions gather to review production data. Evocon data is central to these meetings, providing the accurate, up-to-date information needed to assess performance and plan for the day. They have established custom dashboards, ensuring all teams have visibility into key metrics. Operators are encouraged to participate by providing valuable comments and insights. Additionally, Evocon tracks Good Manufacturing Practices (GMP) as a key performance indicator (KPI), leading to more controlled quality.
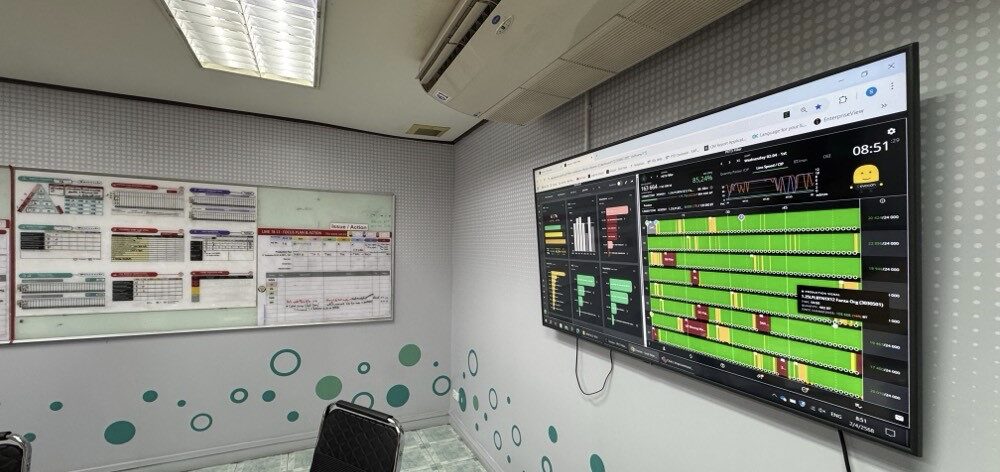
OEE Tracking
The ability to track downtime and OEE with logical and customizable operator comments has been particularly valuable to ThaiNamthip. Customizing the downtime reasons led to better-quality data and the ability to narrow down areas for improvement.
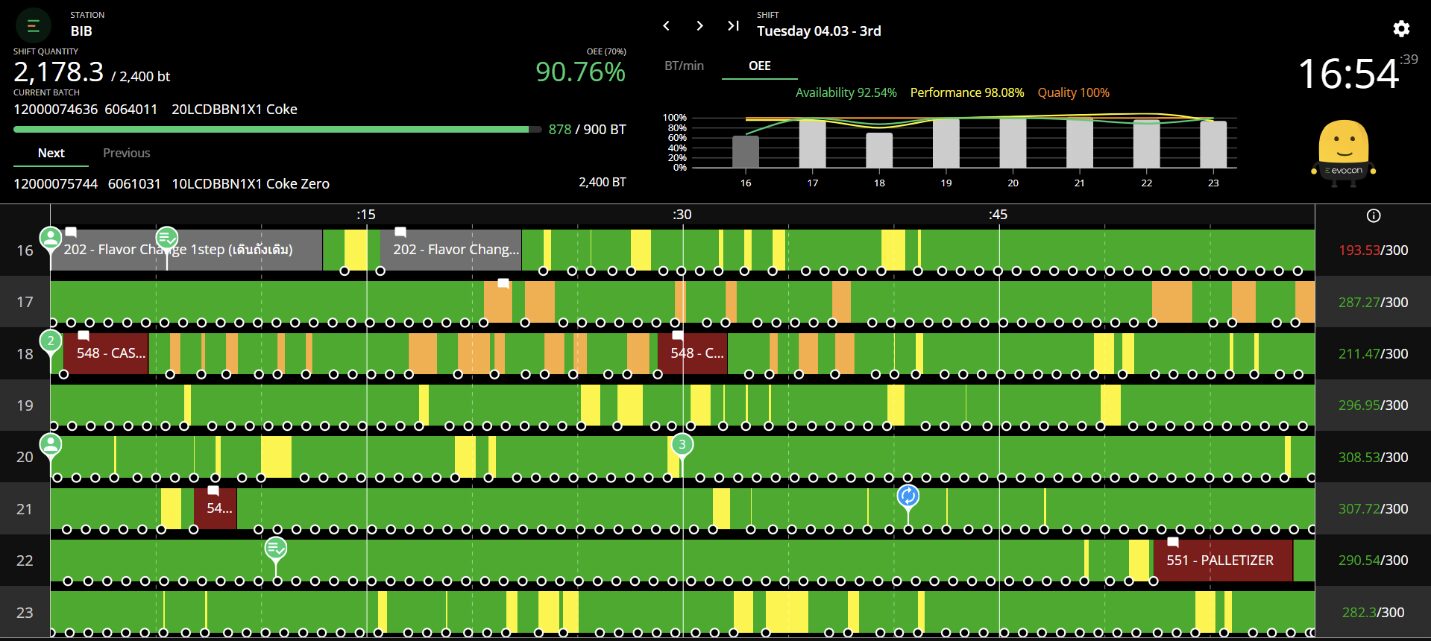
Facility Wide Displays
Throughout the facilities, there are large screens with Evocon on display. The facility-wide display of real-time data encourages continuous operator engagement and enables immediate responses to any stoppages.
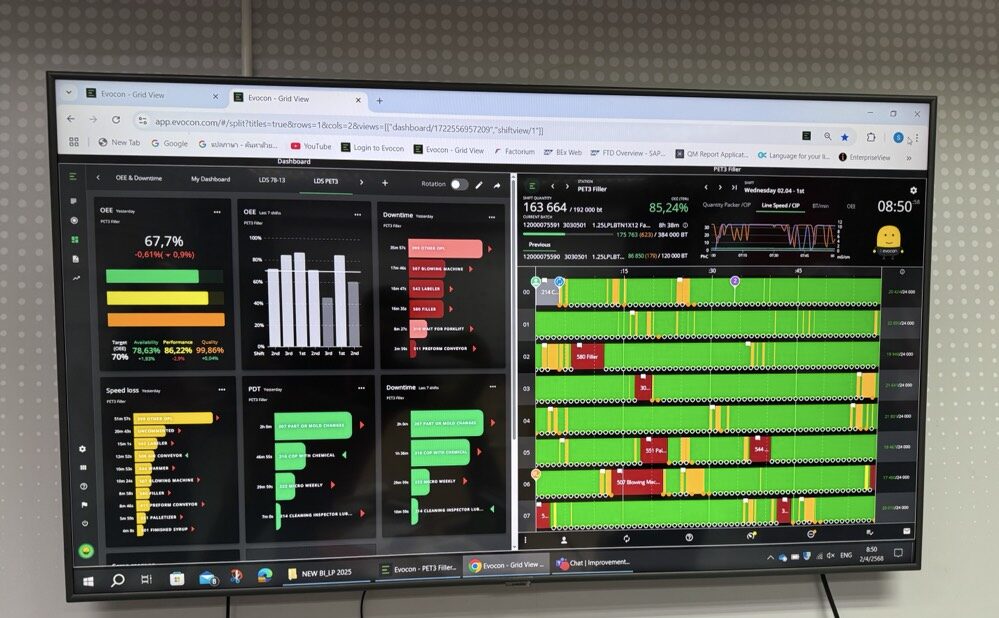
Checklists
ThaiNamThip uses Checklists to keep operations running smoothly in several areas. They are used for quality inspections, Cleaning-In-Place (CIP) operations, scrap, shift handovers, and continuous improvement projects. This active use of Checklists has led to more control over their product quality by ensuring that all quality control steps are completed.
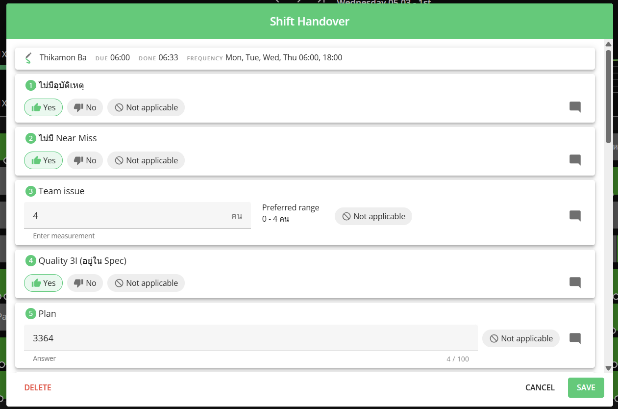
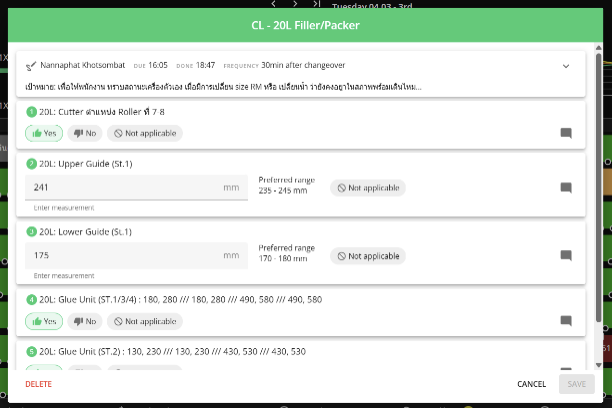
Custom Widgets
On the Evocon Shift View, they have used the option to implement custom widgets to keep track of the data they need. Specifically, they have a process parameter tracking conductivity and line speed.
ERP Integration & Custom Reports
Evocon is not used as a standalone tool at ThaiNamthip, and they are currently integrating it with their enterprise resource planning (ERP) system. The integration is set up so that the data is being sent both ways between the ERP and Evocon. Custom reports are being used to retrieve data for improved decision-making.
Partnership Impact
The collaboration between Evocon partner Beyond 4.0 and the ThaiNamthip team demonstrates an exceptionally efficient approach to implementing new software at a facility. As a result of the preparation done by the continuous improvement team at ThaiNamthip and the knowledge, skills, and experience of the Evocon partners, they were able to have Evocon up and running across the two facilities in less than a week, resulting in immediate improvements in production visibility and operator engagement.
The partners played a key role in the successful implementation of Evocon at ThaiNamthip by supporting the physical installation, training, and rollout.
After presenting the success of this implementation at events and conferences, Evocon partners have seen expansions in Saudi Arabia, Europe, and the US. This expansion directly results from the powerful impact of collaborative partnerships between knowledgeable teams.
Key Takeaways
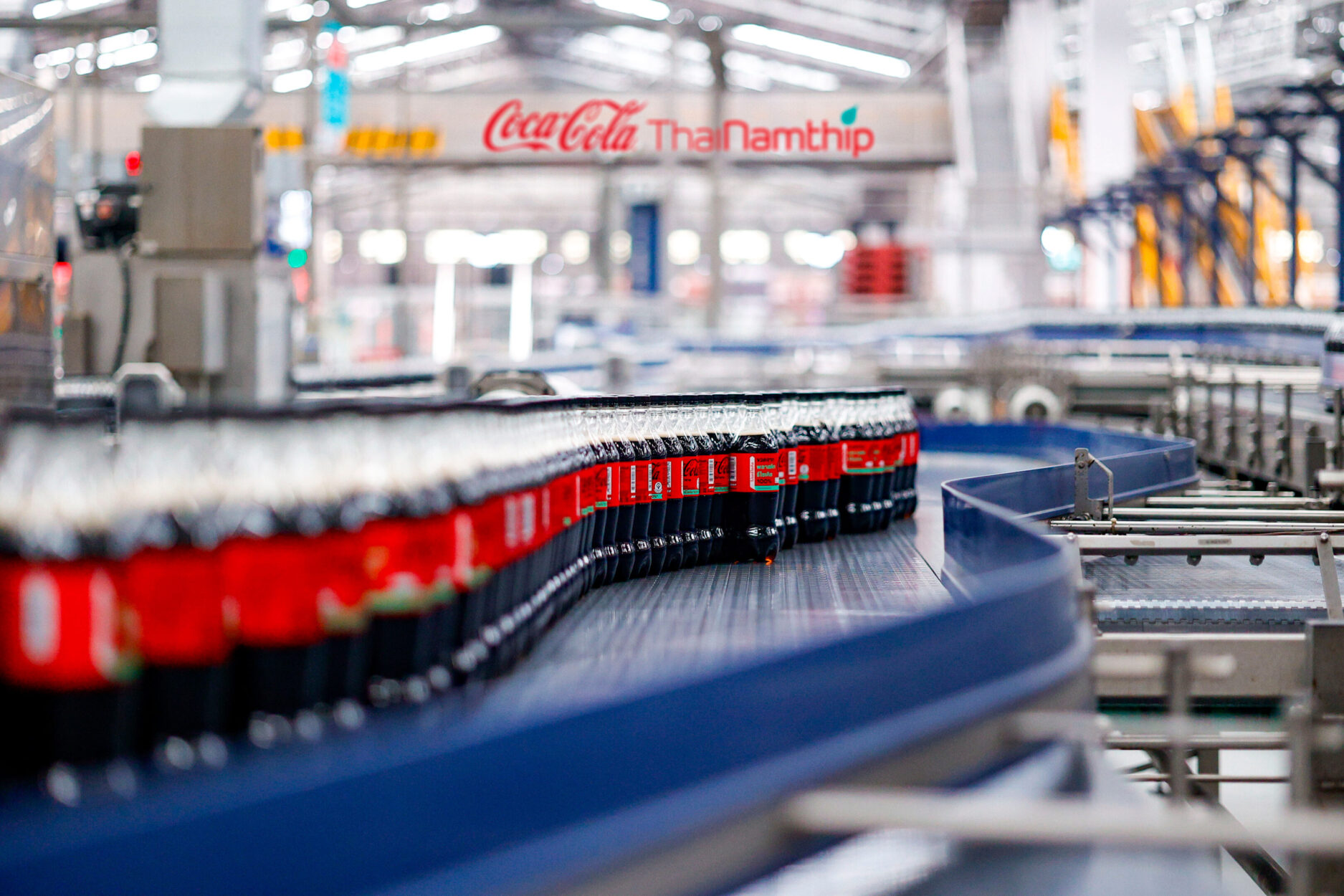
The implementation of Evocon across ThaiNamthip’s facilities in Pathum Thani, Lampang, and Laos is a model for rapid and effective digital transformation. The level of preparation done and their desire to reach operational excellence led to an exceptionally smooth roll-out, which, in a short timeframe, resulted in enhanced production visibility, boosted operator engagement, and improved daily operations. ThaiNamthip’s successful installation of Evocon in their Lampang facility without the Evocon partners on-site shows how well the team was prepared and will simplify future installations.
By ensuring accurate real-time data is available and sharing this with their team daily, they keep everyone aligned and focused on the shared goal of maximizing OEE and reducing downtime.