Thermory is an Estonian-based chemical-free wood processing company. With facilities in Estonia, Finland, and the USA, it is the world’s largest manufacturer and exporter of thermally modified wood and sauna products. Yet despite being the market leader, it faced several significant challenges that impacted its production efficiency, output, and bottom line.
The Challenge – Monitoring Production with Pen and Paper
First and foremost, they had no way of monitoring and analyzing the production process within their facilities in real-time. This meant issues where production downtime, breakdown reasons, and faults would either be under-reported or not reported at all.
“We saw that our shop floor needed a production monitoring solution to optimize the work of production machines.”
Rebeka Kütt, Production Support Team Lead at Thermory
This is a common challenge for manufacturers who use paper-based production monitoring to record data. Production downtime, breakdown reasons, and faults are not correctly recorded, and therefore their total impact on a business is vastly underestimated.
These challenges led them to partner with Evocon to gain a comprehensive view of their production efficiency and manufacturing process data. The data would allow them to optimize these processes for better overall performance.
Kütt explained that, “previously, the foreman would inform about tight spots too, but it is only natural that the major issues would remain in focus while ignoring the smaller issues. Furthermore, some small details would go completely unnoticed.”
In addition to implementing Evocon, Thermory decided to increase its production digitalization efforts by digitizing the worksheets of its forklift operators. Until then, they relied on manual inputs using pen and paper. This was unreliable and inaccurate as gaps were commonplace in the reporting from forklift operators.
Kütt explained that “In the past, the production assistant entered information regarding the movement of packages with a day’s delay and if the same package moved more than once in a day, we could never be certain where it really was and who was the last person to move it.”
Real-Time Production Monitoring with Evocon
They started by installing Evocon across Thermory’s production and manufacturing equipment. This allowed them to monitor every aspect of their production process in real-time, giving a clear overview of exactly what was happening at the workbenches. It also made them aware of their actual production efficiency.
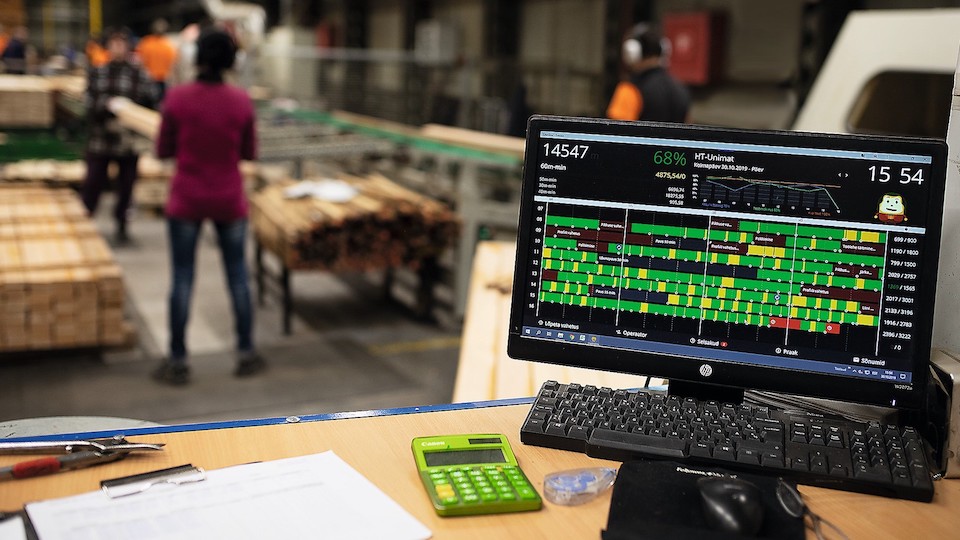
Very quickly, it became apparent that various machine breakdowns were occurring. Most importantly, though, they discovered that they had a lot of micro stops which had been too small to be noticed by a bystander. This meant that before Thermory implemented Evocon, all of these production stops went unreported.
Kütt explains, “We started to analyze the downtime of every workbench to understand better what were the main reasons for availability loss. Almost everyone in production knew, for instance, when a bench had an outage of several hours on a certain day. At the same time, nobody noticed that a bench was consistently down throughout the week for 1-2 hours due to packaging issues. Downtime due to packaging was often short, but it repeatedly occurred throughout the day.”
The benefits of a solution that gave them 100% oversight over the entire manufacturing process became evident and visible.
Overcoming the Fear of Production Monitoring
As with introducing any new system, there was initial fear among the workers. But the anxiety came from the wrong assumption that the OEE system of Evocon was there to control and monitor the performance of production operators.
Clear communication and inclusion are critical for digital transformation
However, clearly communicating the goals of production monitoring mitigated the fears. Management made it clear what data they will monitor. And how they will use collected production data to improve production efficiency.
“Clearly communicating the purpose and intent of installing an OEE system is critical to the success of the digitalization project. Without the buy-in and commitment of the machine operators themselves, there will likely be suspicion and resistance towards production monitoring.”
Rebeka Kütt, Production Support Team Lead, Thermory
Once the machine operators of Thermory realized that Evocon’s implementation improved the production process as a whole, the adoption of the system was quick and painless. Moreover, as operators saw the number of breakdowns that occurred each week, they started providing suggestions to improve the situation.
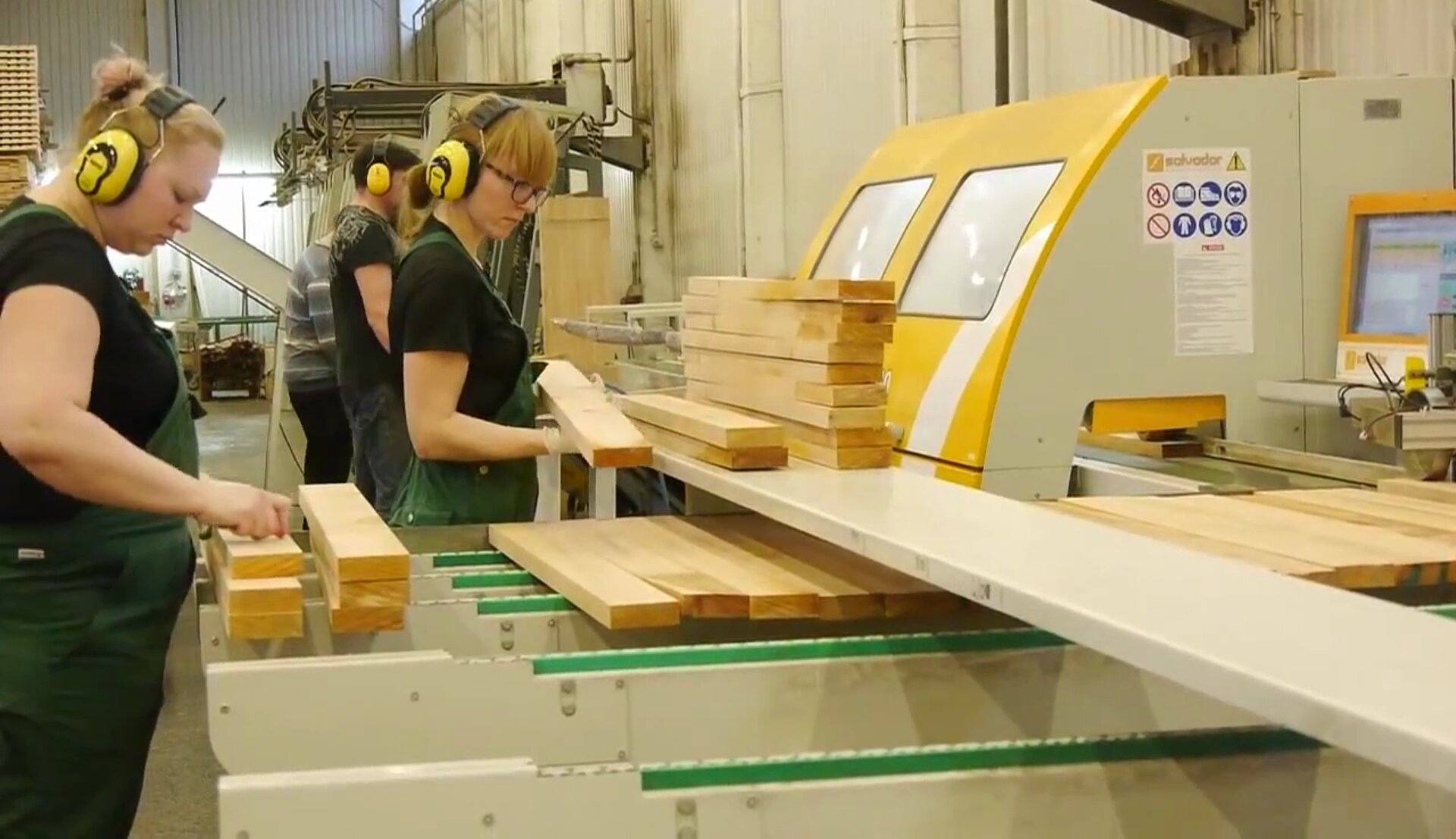
“Our experience with Evocon showed us that simply displaying real-time results gave us a really positive effect. When people could see how they worked and how many technical stops they had, some processes improved by themselves. Due to that, people started to bring out their ideas on how to make their work more effective and how to reduce technical stops.”
Concerning the digitizing of worksheets, the process went more smoothly than initially expected. At first, there were some doubts as to whether the forklift operators would cope with the tablets and digital recording. But these doubts diminished after forklift operators received training on new techniques.
“When the operators understood that a single wrong press of a button would not delete the program and nothing bad happens, excessive fear vanished.”
After digitizing different parts of the process, management understood one very important thing. Clear communication and inclusion of everyone involved are critical in making any digital transformation on the production floor a success.
Learn more: How to Effectively Communicate OEE to the Shop Floor?
Increase in Production Efficiency by 20%
Both the modernization process, as well as the implementation of Evocon, generated positive results for Thermory. The fact that every fault, breakdown, and slowdown in production was now tracked, meant that the team could quickly identify problems with the most significant losses and work to understand the root cause of the issue.
For example, by doing changes in the work process, they solved a lot of the identified issues. Such as rearranging the workspace to make mobility more convenient. Which consequently increased production efficiency.
“By starting to use Evocon, we could see our real problems. And now we deal with the problems that actually need to be solved.”
Rebeka Kütt, Production Support Team Lead, Thermory
In total, the production efficiency of the Thermory workbenches increased by 20% without any large additional expenditure.
What is more, the digitization of the forklift operators’ worksheets meant that they could track the location of packages in the program in real-time. Thus, the time spent on inventory counts took only a few days instead of a whole month.
“It is no longer necessary to check personally where a package is or who was the last person to move it. This saves valuable working hours and frees the staff up to focus on more important tasks.”
With Evocon, Thermory is now able to gain valuable insight into the performance of their production process. It has led to increased production efficiency and ultimately better profitability without threatening or upsetting the existing workforce.