Real-time production monitoring is a transformational change. It represents a breakthrough moment for many manufacturers in terms of new levels of efficiency, profitability, and transparency. Any organizational change of this magnitude deserves proper focus and resources. This is where digital champions in manufacturing play a key role in your organization.
Who Is a Digital Champion?
Digital transformation can involve the implementation of several different Industry 4.0 technologies: production monitoring, live OEE tracking, MES, demand sensing, and supply chain collaboration, to name but a few.
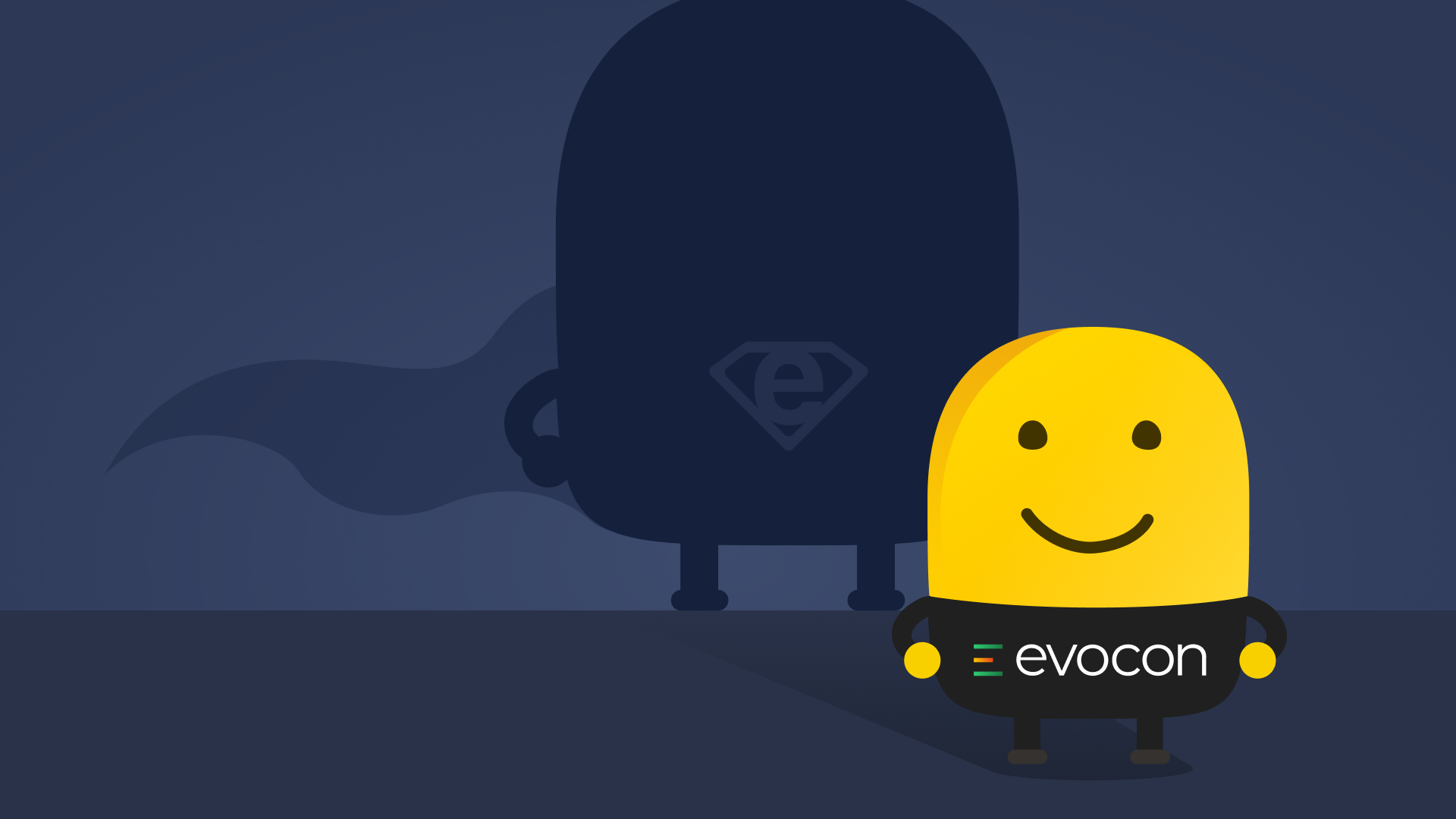
As GE, Ford, and P&G learned, the journey is challenging, and mistakes can be costly.
A digital champion owns the implementation process of IIoT-enabled technology and is accountable for delivering results in a company’s digital transformation journey. In short, they drive production digitalization efforts for the organization.
A digital champion serves as the eyes and ears of the production digitization project(s), keeping stakeholders informed and aligned to ensure the full realization of the project’s benefits.
This effort could be as simple as a single plant implementing production monitoring. Or it might be more complex. Such as the implementation of multiple projects and systems in ten plants across several countries and time zones.
While the specific production digitalization efforts pursued will be unique to each manufacturer, a core aspect of the digital champion role remains the same: ownership, accountability, and communication.
7 Responsibilities of Digital Champions in Manufacturing
Earlier, we defined the role of digital champion broadly within the digital transformation process. For the remainder of this article, we are going to narrow our focus to examples for and from manufacturers implementing live OEE tracking and production monitoring.
Our selection to narrow the focus to OEE to discuss responsibilities in no way limits their use to OEE implementation. In fact, these responsibilities can apply to a number of different digital transformation projects as well.
In this context, we believe that manufacturers who have a digital champion role position themselves for success in their efforts. Specifically, we see seven responsibilities to be of prime importance.
Learn more: What Is OEE and How Does It work?
Organizational culture
Even before you begin the journey of implementing production monitoring or live OEE tracking, your digital champion can lay the groundwork by shaping your organizational culture. This might be as fundamental as “starting with why” when they introduce production monitoring on the shop floor. Or as critical as learning how to effectively communicate OEE to the shop floor. Regardless of the specific steps that each organization may need to take, the key point is the recognition that culture change is an integral part of successful OEE implementation.
Engage and inspire employees
If this is your first time using a system to collect and monitor live OEE data, employee buy-in will be critically important. This is due to the transparency that the system itself will bring about. Transparency is certainly a positive in the long run, but at first blush to your operators on the shop floor, it can seem a bit Orwellian. Indeed, a feeling that big brother is always watching might leave some employees feeling nervous or insecure.
To counteract these effects, we suggest focusing on the communication and improvement aspects of production monitoring. Specifically, how the system helps operators to identify opportunities for improvement as well as letting them report what the real problems are that they are experiencing so that these can be fixed and their daily lives improved.
Real-time OEE software
Equip your operators with the best tools and unlock key data for increased transparency and efficiency now. Free for 30 days.
Be mindful of the change cycle
We experience an organizational change in very similar ways to how we experience change as an individual: it follows a cycle. Beginning as neutral when we are unaware and proceeding through the five stages depicted below. Without a doubt, the area of primary concern for the digital champion is the valley of despair. It is critical that you avoid getting trapped here by offering a persistent vision of positive outcomes, rewarding small wins, and nurturing fledging excitement and creativity with the system.
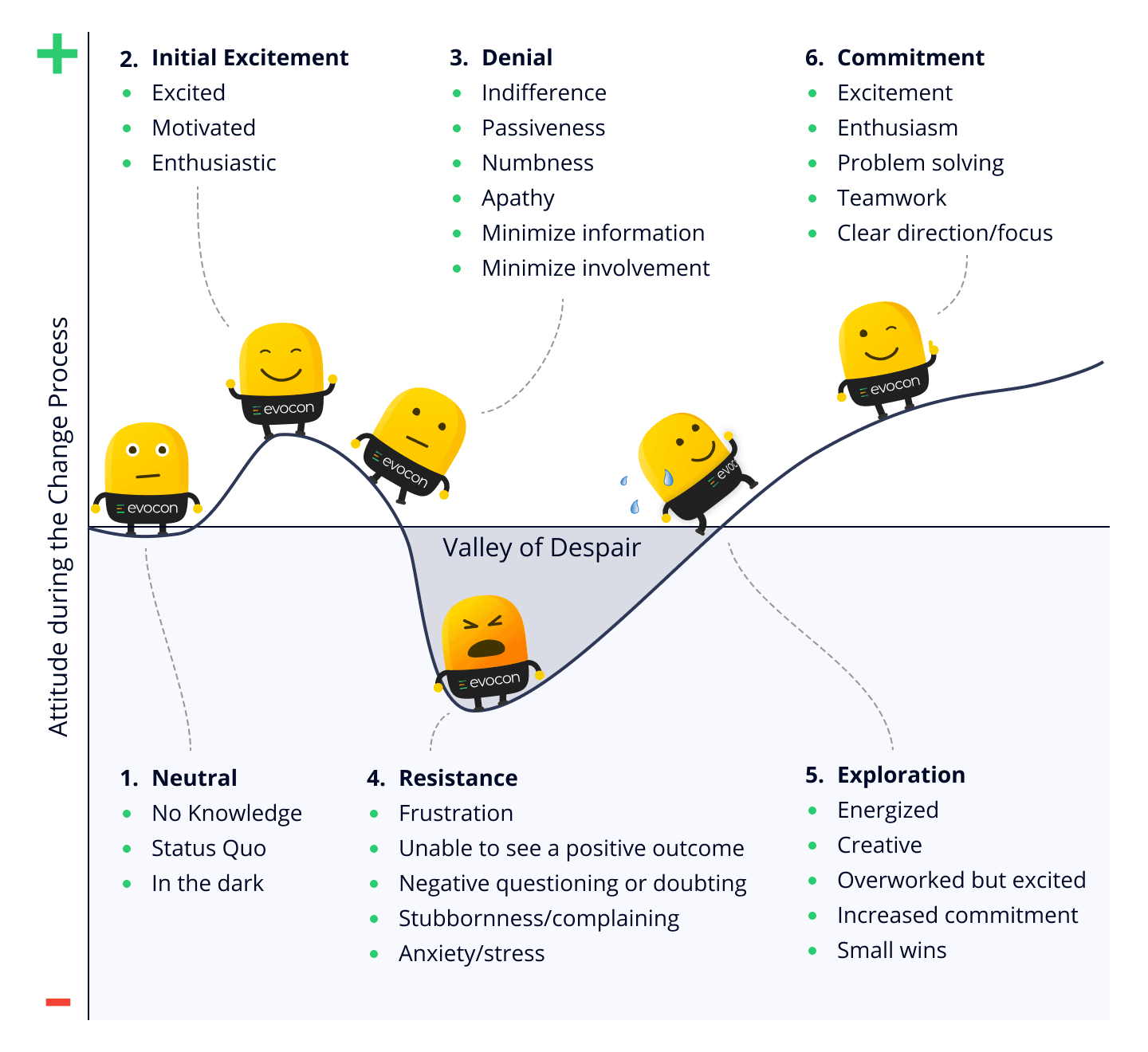
Provide training
As a digital champion, you should seek to first educate yourself in order to later act as a resident expert and superuser. A few key resources that can help you in this process are found on our website in the ‘learn’ section. Here you will find a wealth of knowledge on everything from how Evocon works, to the basics of OEE and implementation guides, and even guides to increase productivity as well as useful case studies to learn from.
Once you are up to speed and ready to launch, we suggest doing a demo with key users as part of the project’s kick-off meeting. Here you will want to explain relevant features, functions, and benefits as well as share ways to get help, such as the ‘learn’ resources previously mentioned and how to contact us directly.
Overall, the goal is straightforward. You will need to make sure that everyone who interacts with the system feels sufficiently trained.
Encourage ownership
Encouraging ownership really goes back to ensuring buy-in and securing that changes you bring about can be sustained. You lay the groundwork for encouraging ownership from the moment you introduce the project and will need to keep this in focus as you provide training. The key point is simple: you own the success of the implementation, but users of the system will need to drive this success into the future. The best way to go about this is to encourage ownership of the system and the results.
Tip: While it is true that a digital champion will need to focus primarily on machine operators in this effort, the person will also need to encourage ownership with production managers, operations managers, maintenance managers, and quality managers.
Expect questions and provide clear answers
Throughout the implementation process, you should expect a lot of questions. In fact, if you do not hear questions from users, then something may be wrong. For this reason, you should really aim to get your team asking why and asking how. Questions such as:
- Why do we classify downtime this way?
- Why is it important to add comments to downtime before the end of the shift?
- How does data collection occur?
- Why is machine availability important?
- Why is lunch no downtime?
Curiosity can be infectious. So after you get your team asking why and how questions, consider training operators in five why analysis.
Hold daily review sessions
A key learning tool and all-around best practice is the use of the daily cross-functional review sessions. The point of this exercise is to improve communications among departments by working with transparent data and open problem-solving methods.
To be clear, this is not a public “gotcha” session, which would be highly counterproductive. Instead, you are working to create a culture of collective problem-solving. In the process, you are also instilling a habit of collecting and analyzing production data each day.
Next Steps
Now you should better understand why you need a digital champion in manufacturing. You have seen what the key responsibilities of the role should be. And it’s time to take advantage of your production digitalization efforts.
As you do, keep in mind each of these seven responsibilities of digital champions in manufacturing. This will ensure your organization’s digital transformation is a successful one.