Meconet is one of those companies whose products you use all the time without knowing it. Meconet produces demanding metal components: springs, stampings, deep drawn products, and qualified assembly works. These parts are used in electrical switches, locking devices, medicine dispensers, cars, heavy vehicles and more.
Meconet is a family-owned company that operates in four countries (Finland, Sweden, Estonia, and Russia) and is proud to have been around for three centuries, having been established in 1896.
Challenges: Machine Utilization and Reactive Maintenance
In general, Meconet’s Estonian factory was doing well. Capable equipment, skilled staff, and decades of experience ensured competitive pricing, and the orders were flowing in.
That said, success did not stop Meconet from looking for areas of improvement. One of those areas became apparent after spending time on the shop floor: machine utilization. The factory’s production engineer, whom we were interviewing, noted that some machines were scheduled to run but were sitting idle. If you asked why, you heard as many explanations as there were people. While all of them were valid, it was difficult to say which ones were the most important.
Another issue that stood out was repetitive complaints. Operators were pointing out various issues from broken equipment to missing tools but did not feel that their concerns were addressed quickly, even though the maintenance team was busy. This was due to the maintenance team not having a prioritized list of issues. They were simply solving the most recent or most urgent ones. In other words, they were doing reactive maintenance.
It was becoming clear they had to focus and solve the problems one by one, starting from those that caused the biggest losses in productivity. So, they needed to prioritize the list of problems. But how? Meconet needed to know which issues affected which machines and how significant that impact was. Meconet needed to collect production data.
The Next Challenge: Collecting Production Data
Some of Meconet’s personnel had experience in collecting production data using the classic approach: printing out a blank spreadsheet and standing next to the machine with a stopwatch, filling in information about every step. This time they videotaped the full shift of a machine and later viewed the recording and noted down every action together with its duration.
While being a sure method to learn what was happening on the shop floor, it had obvious flaws, too. The time required to collect this data was the biggest of them. It limited the amount of production data they could collect: only one machine at a time, only for one shift, and only once or twice a week.
Learn more Top 8 OEE Calculation & Monitoring Mistakes
But what if they could have the data for all the machines and all the shifts, every day? That was the promise of data automation, a popular topic among manufacturers today.
In 2019, there were already several machine downtime tracking solutions on the market. Rather than researching features and pricing of various options, Meconet tried something else.
They found another manufacturing company with similar equipment and processes. This company, Torm Metall, had a production monitoring solution in place and was happy to recommend it. Even better, that solution had a free trial.
Meconet Implements Evocon to Monitor Production
And so Meconet began the free trial of the OEE software provided by Evocon. At first, they were considering employing a person to deal with the Evocon system: installing and configuring the software, analyzing data, and extracting reports. They expected this to be a full-time job. Eventually, Meconet decided to wait and see until the end of the trial. The production engineer took on the setting up and using of Evocon. He believed he was the right person to have first-hand access to production data since he was the one in charge of making the machines run smoothly.
To their surprise, Evocon was so quick to set up and easy to use that they did not need to do any hiring.
“It’s completely hassle-free,” the production engineer told us. “I’m just doing it every morning on Monday to check data on OEE, cycle times, and machine downtime. One hour maximum”.
After studying the data, he would print out several reports from Evocon and pin them on the board for everyone to see.
That was the board we were standing in front of, next to a big TV screen, displaying Evocon’s Factory Overview screen.
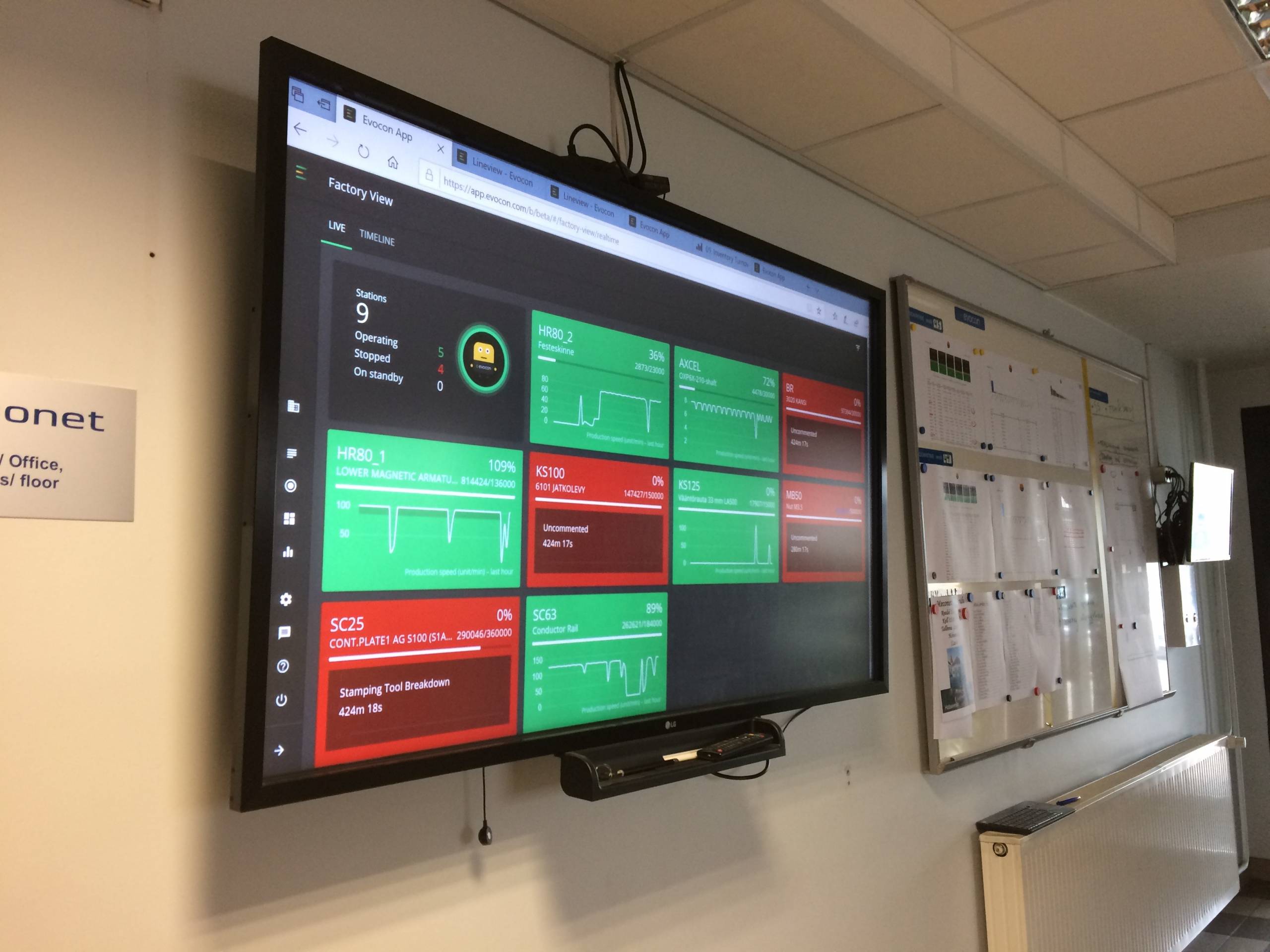
It was also where the operators met every Tuesday to discuss problems from the previous week and review goals for the current one. On the week of our visit, the focus was on making sure that operators comment on all the reasons for machine downtime.
The aim was to understand availability losses in their production process. The printouts highlighted the machines that still had some uncommented downtime.
Production Monitoring Results
The practice of a weekly review of production KPI-s was established once the trial period was over, and Meconet installed Evocon on several more machines.
The operators were skeptical of these efforts at the beginning. They were not sure how these meetings could change the reality of the shop floor.
Focusing on the top issues as a team
But it did. Production data brought out the poorest performing machines and the most common downtime reasons. Meconet prioritized them by effort and effect (for more details, read how to perform root cause analysis) and assigned them to the people responsible.
Problem-solving became a team effort, involving the shop floor, maintenance department, and the office. Limiting attention to only a few issues at a time allowed everyone to work together and fix problems rapidly.
Targeting efforts, justifying investments and sharing of best practices
Things started to change on the shop floor. The impact of the maintenance team increased because they focused their work on what was needed most. Some equipment was replaced or newly bought: the investment was easy to justify now that you could calculate exactly how much downtime it could help avoid. Operators learned from each other, borrowing techniques to increase the OEE of their machines.
Production data as an enabler of change
While the driver of the improvement was willingness and discipline, the enabler was data. With Evocon, Meconet had production data that was objective, precise, detailed, and visualized in a way that made it easy to find problems. “The main achievement of Evocon is that we finally have data that we can trust and use,” said the production engineer.
An illustration of how data helped to identify opportunities for improvement was the Raw Material Replenishment issue, which we will describe here in more detail.
“Raw Material Replenishment” Issue
As Meconet accumulated one month’s worth of production data on one of their machines, “Raw Material Replenishment” unexpectedly came up on top of the list of operational downtime.

The reason for it wasn’t clear, so they dug deeper. Root cause analysis revealed that some operators replenished material much faster than others.
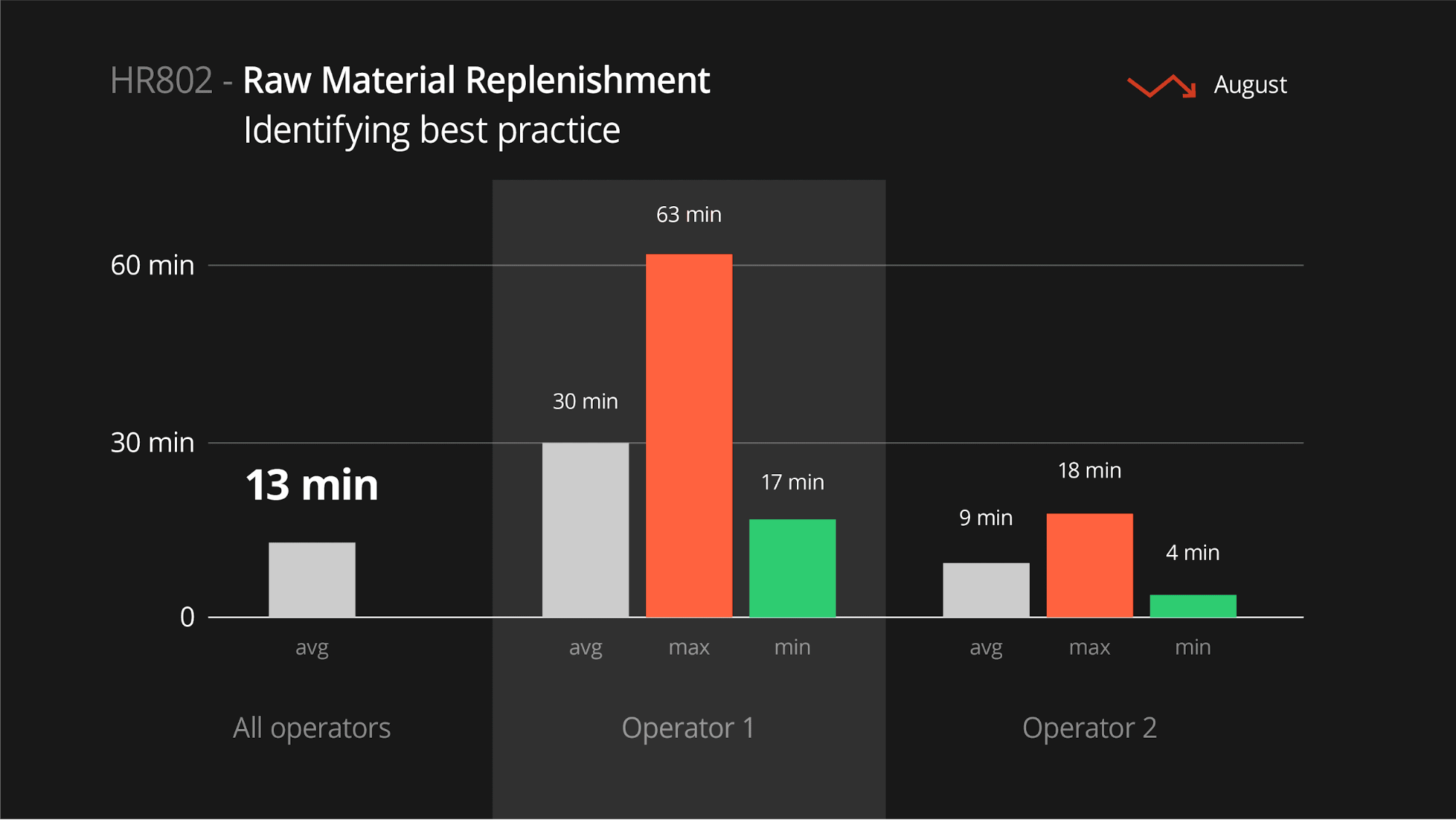
The last step was to go down to the shop floor to observe the difference. Soon after that, they had the answer. Some operators were preparing everything before the machine ran out of material, thus saving time on the replenishment procedure itself.
The solution was simple. The fastest operators introduced their way to the rest, speeding up the average replenishment time by 30%.
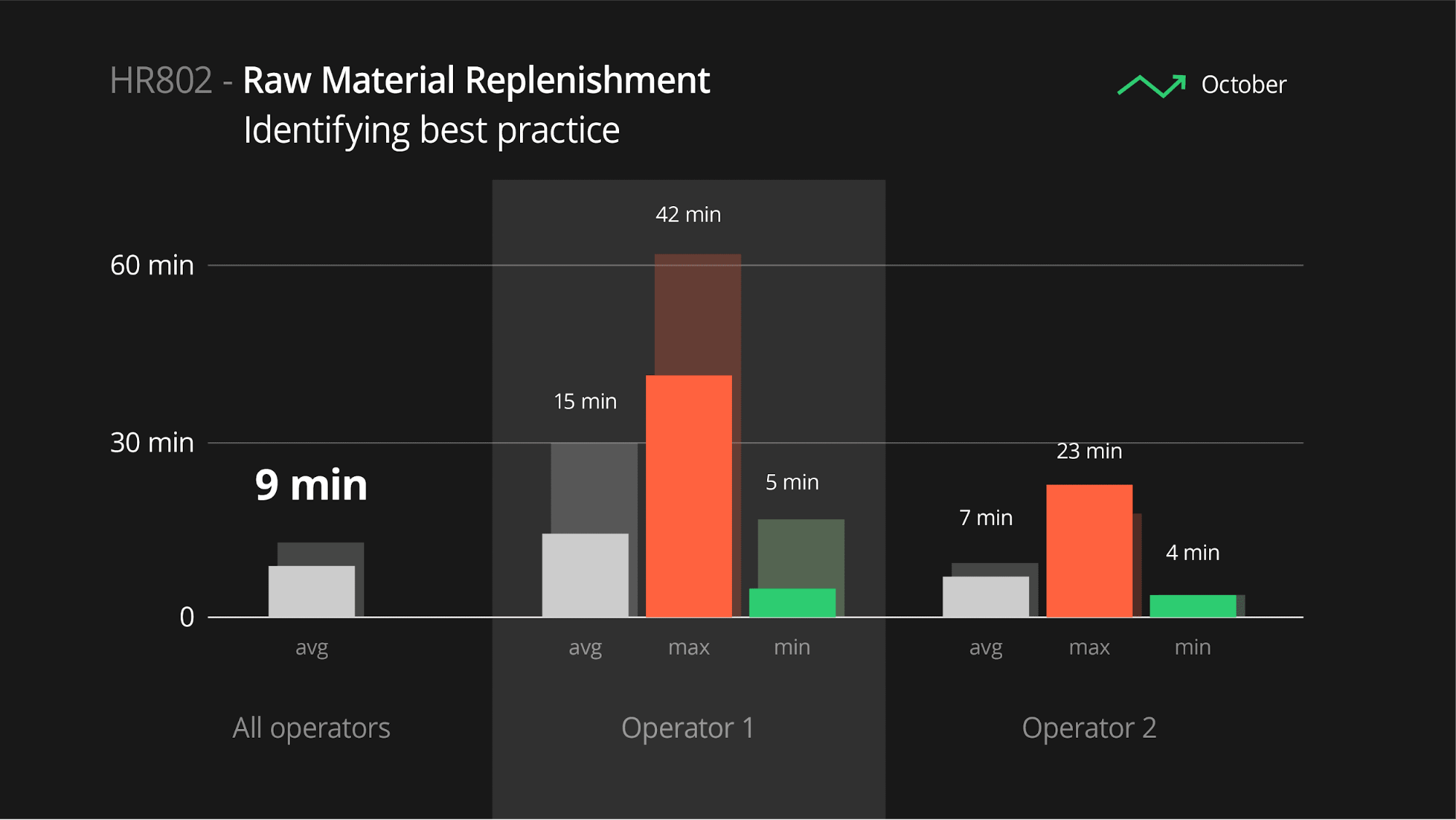
It is worth mentioning that nobody judged the operators’ performance during this (or any other) project. The real issue was communication.
Ongoing Improvements in Availability
The improvement mentioned above was only one of the many that followed. The chart of the most important downtime reasons kept evolving, new issues always climbing to the top of the list. This happened because the operators were adding comments to the machine stops more and more actively. That way, previously “uncommented stops” were becoming defined and thus actionable.
Understanding machine downtime in more detail
On the day of our interview, the biggest problems were Tool change and Machinery breakdown. To understand machinery breakdown, it was no longer enough to have stops commented. So, the Meconet team started an initiative of adding extra notes to every stop, to explain why that particular breakdown happened.
Meconet truly used the best practices of defining machine downtime reasons to the fullest.
The production engineer told us that without the data, their priority list would have been different, and some issues wouldn’t have been on the list at all. He explained how he spotted a pattern of frequently alternating yellow and green colors on Evocon’s Shift View. He wouldn’t have noticed it without Evocon’s software, because the machine wasn’t idle.
This led him to find out that much of the performance loss on that machine was due to the completed product not being taken away immediately. The solution was to buy a rotating robot to move the finished parts aside automatically.
Operating Time: +50%
As issues were tackled one by one, the overall picture kept getting better.
In just five months, Meconet increased their productive work time from 24% to 36%, which is a 50% improvement. And this is only the beginning.
When we asked the production engineer, what he would do differently, if he could do this project all over again, he didn’t need time to think.
“I would do it sooner and involve more people.”
Vadim Doman, Productioin Engineer at Meconet
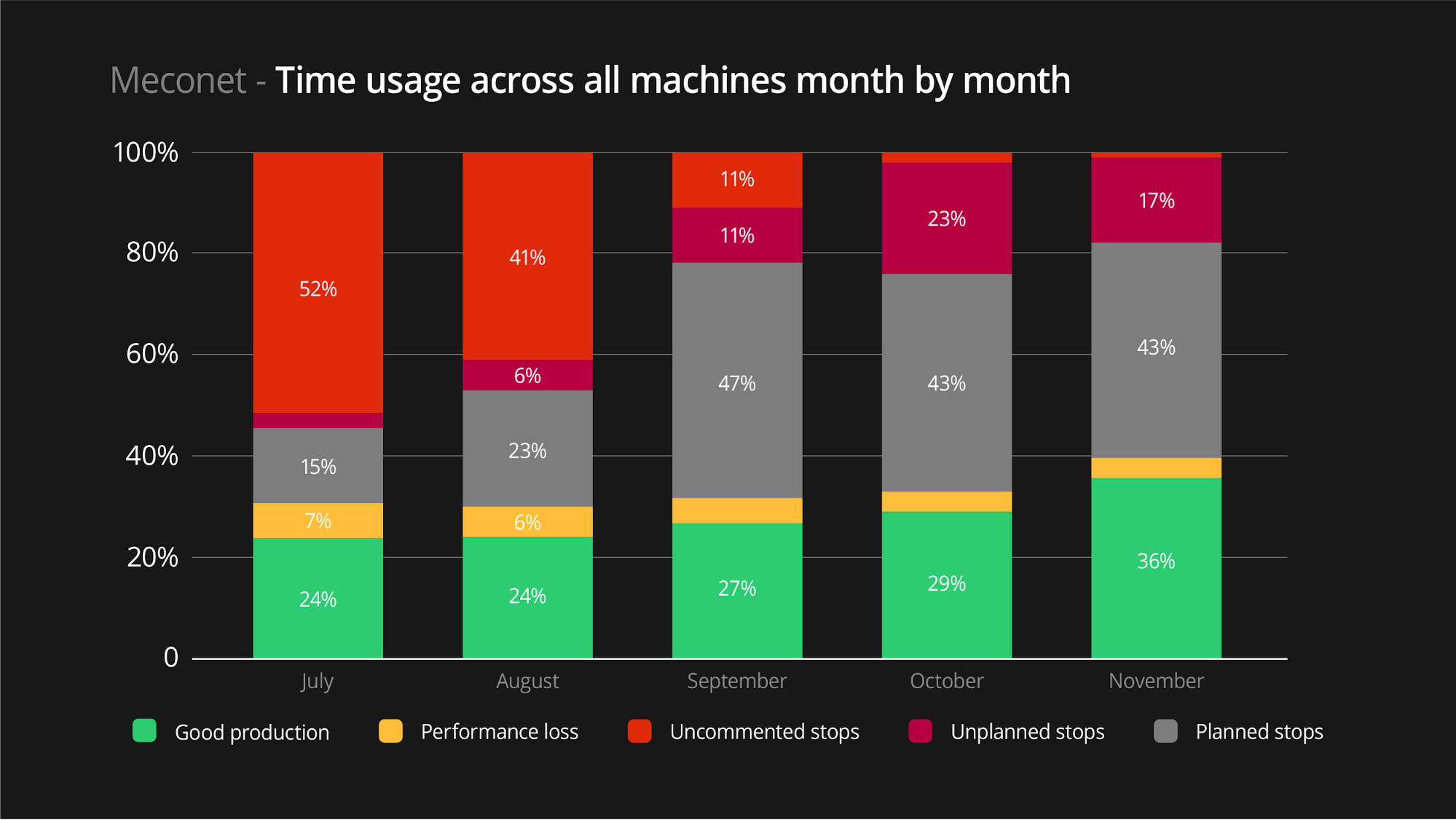
Next Steps
After the successful launch of production monitoring and live OEE data tracking in the Estonian factory, Meconet’s other factory in Vantaa, Finland, implemented Evocon as a start to their improvement journey.