In our article on the importance of lean continuous improvement (LCI), you learned the advantages of LCI success. In this one, we explain the top six most reported challenges in LCI. Then we offer insights, tips, and recommendations on how you can adapt and overcome LCI program barriers.
Top Six Challenges in Lean Continuous Improvement
The American Productivity & Quality Center (APQC) is one of the world’s foremost authorities in process and performance improvement. The chart below is the total for APQC’s Priorities, and Challenges Survey in Continuous Improvement for 2018, 2019, and 2020. The number to the left of each challenge is the sum of all responses during the past three years.

Challenge #1: Creating a lean continuous improvement culture
An effective lean continuous improvement (LCI) program requires the involvement of many stakeholders. The specific stakeholders will differ based on the size of the business. And, to some extent, it’s market (think governmental oversight in pharmaceuticals).
The most successful LCI culture insists on including everyone. From the very beginning.
Plainly stated – every person in the business needs:
- Involvement
- To understand program goals
- Know how their work contributes to the goal
- Training on CI tools
- Authority to question the status quo.
- To contribute ideas for improvement.
An ideal beginning for an LCI implementation program is with the CEO allocating resources, setting the shape of governance for the program, and defining expectations. However, success requires more than the top leaders and CEO. When it comes to LCI, a transition is required to bottom-up buy-in and, ultimately, day-to-day program ownership.
This implies that companies need to evolve from top-down administration, such as starting with the CEO, into bottom-up driven improvement. It is not an easy task because, as humans, we are hard-wired to resist change. But it is possible.
Changing your organization’s culture will take time
If you’re just getting started, an excellent first step is to create a team to manage your program at a high level. Some call this team a review board or steering committee, but regardless of name, the point is that the team meets regularly to manage the LCI program.
The review board will do the work of reviewing the company’s processes, and the regularly scheduled meeting becomes the heartbeat of the program. The information must flow from the board members down and through the continuous improvement teams.
Teams can then incorporate performance metrics and proactive tracking methods to projects, which should further instill a CI mentality in both management and line employees alike.
LCI Culture = This is how I do my job
The Economist article “From bitter to sweet” sheds light on the role continuous improvement played in the dramatic turnaround of Honeywell International. Honeywell’s CEO at the time explains that one of the most challenging obstacles to success with continual improvement was “to get to the point where people say, ‘this is how I do my job now'”.
Challenge #2: Identification and prioritization of opportunities
Identification and prioritization of opportunities require objective process data for teams to analyze. Indeed, data analysis is arguably the most useful of the three methods for project identification we cover next.
OEE as a measure of potential improvement
OEE is the ideal metric to track and understand sources of production loss. Sources of production losses are indications of potential improvement opportunities.
At Evocon, we automate the collection of your production data. Automating machine monitoring is an essential step to allow you to visualize your six big losses.
A recent research paper in the International Journal of Operations & Production Management spoke directly to our point:
“OEE provides useful benefits as a production monitor, (but) it is as a measure of improvement that the real potential of OEE can be seen.”
The paper goes on to state that “OEE provides a useful guide to aspects of the production process where inefficiencies can be targeted.”
We could not agree more.
Operator empowerment and engagement
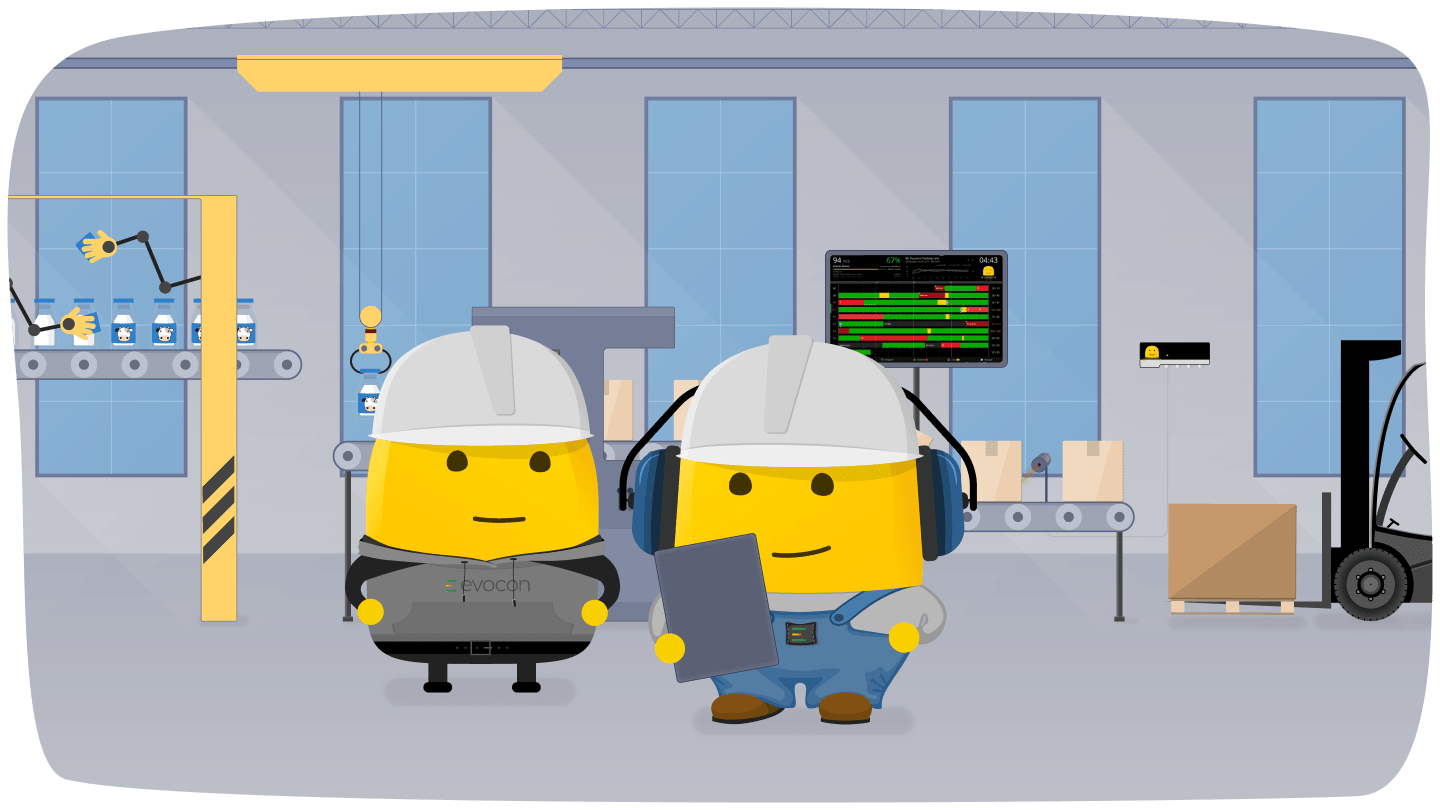
The last source of identification of opportunities may be the most important: your operations team. As mentioned before, a transition in culture needs to take place where improvement ideas are driven from the bottom up. One great way to foster and grow this habit is to empower and engage operators on the shop floor.
Here again, Evocon can help by visualizing your production data in real-time on the shop floor.
Learn more: Production Data Visualization Drives Engagement & Productivity
Continuous Improvement Software
Start visualizing your production data in real-time and boost efficiency with Evocon’s 30 day free trial.
Challenge #3 – Capturing the ROI of Improvements
Capturing the ROI of improvements is critical to the success of an LCI implementation and of individual projects.
We interpret the selection of this challenge as an indication that they (the survey respondent) do not have systematic means to manage a portfolio of CI projects. It would follow then that, here also exists a need for a real-time automated solution that can quickly provide visualization of program and project status across the entire organization.
In this case, we recommend creating a system to act as a single source-of-truth for capturing project ideas, tracking actions of process improvement teams (PIT) teams, and serving as a conduit for knowledge transfer of recorded results.
Evocon can help you by creating real-time production transparency between operators on the shop floor, managers on the top floor, and executives working from home anywhere in the world administering multi-site lean programs.
Learn more: The Importance of OEE in ROI Analysis for Manufacturers
Challenge #4 – Aligning continuous improvement efforts across an organization
Some organizations go to great lengths to define a vision and strategy for continuous improvement in manufacturing. Unfortunately, having a slide deck that layouts vision and design is not enough to ensure alignment.
The first step in reaching the alignment of efforts across the organization is to conduct meaningful conversations about CI’s role in the business. The output of these conversations builds the structure of the organizations’ vision and strategy for CI.
In the article, the key to a successful CI program, the author correctly notes that after vision and strategy are defined, a company needs to align the plan in three ways:
- Available resources
- Requirements, needs, and challenges of program leads
- Suited to the company’s ability to change
Challenge #5 – Overcoming organizational resistance to change
Perhaps no cliche is so universally associated with organizations as “The only constant is change.“
Resistance to change is an attitude or behavior that indicates an unwillingness to make or support the desired change. Leaders of organizational change tend to view resistance to change as something that must be “overcome” for change to succeed.
A more constructive approach is to view the resistance as valuable feedback that can be used to facilitate the desired change. The defining characteristic of this approach is the recognition that when people resist change, they are defending something significant that seems vulnerable.
Challenge #6 – Incorporating customer insights into the improvement process
It would seem true that if firms had customer insights, then incorporating them into the improvement process would be simple. Therefore, we have made a simplifying assumption about the data. We interpret the survey respondents who selected this challenge to be an indication that they lack customer insights.
As such, our recommendation is designed to help companies understand the importance of customer insights and to explain how other companies go about capturing this data.
Voice of the Customer
Customer insights, perceptions, and satisfaction need to be corroborated or rejected. You will need to design and implement a process to collect, analyze, and act on customer feedback.
Effective systems for utilizing customer feedback should include:
- A formal process for collecting, measuring, and analyzing customer data and for communicating results
- Feedback mechanisms determining how well customer requirements are being met
Some examples of sources of customer data that can be useful in determining customer needs and satisfaction:
Conclusion
In this article, we introduced the top six challenges in Lean Continous Improvement. Now you should be able to identify these common challenges and should also understand a few strategies to overcome these common barriers.
If you would like to continue learning, we recommend the following articles:
- Introduction to Six Sigma and Lean Six Sigma
- What is Machine Monitoring in Manufacturing?
- Introduction to Lean Six Sigma DMAIC Methodology
- DMAIC Project Example
Sources
- Diagnosing and Changing Organisational Behavior 3rd Ed, K. Cameron, and R. Quinn
- Johnston, William P., and Ray C. Oman. “Overcoming Resistance to Change.” Knowledge 11.3 (1990): 268-279.
- Dal, Bulent, Phil Tugwell, and Richard Greatbanks. “Overall equipment effectiveness as a measure of operational improvement – A practical analysis.” International Journal of Operations & Production Management 20.12 (2000): 1488-1502.
- ASQ: The Quality Improvement Handbook, 2nd Edition, pages 156 & 157
- From Bitter To Sweet. The Economist, 2012, https://www.economist.com/business/2012/04/14/from-bitter-to-sweet. Accessed 9 Oct 2020.
- Apqc.Org, 2020, https://www.apqc.org/system/files/K08591_2018_PPM_Priorities_Survey_Summary.pdf.