In the manufacturing landscape, achieving optimal efficiency through digitalization is paramount. The Overall Equipment Effectiveness (OEE) system has become a vital tool for manufacturers in this pursuit. However, the effectiveness of OEE largely depends on how it’s deployed. Transitioning from manual to automated data collection isn’t just a trend but a strategic move towards better visibility, real-time insights, and informed decision-making.
OEE Implementation Guide: Path to Manufacturing Excellence
This guide is designed to offer a clear path forward, discussing the prerequisites of OEE, the nuances of vendor selection, and the roadmap for effective implementation.
With actionable insights and practical advice, we aim to support your journey in getting OEE right for your company. And as every manufacturing environment is unique, we provide adaptable strategies to suit different needs.
Prerequisite: OEE System With Automated Data Collection
Before we get to the actual implementation and what steps you should take, we strongly suggest making sure that the system you are going to implement provides automated data collection using sensors or databases. If you are looking to implement OEE on paper or in Excel (which, in essence, is the same as paper, as you would be collecting information manually and just digitizing the values in a file), you are setting yourself up for failure. There are many pitfalls you’d be looking at, and you can read about them here if you are interested.
So this guide is really a guide on how to implement an OEE system, a digital one. And having an idea of which solution you want is a prerequisite—no matter the size of your company.
Not only will this ensure data is reliable, accurate, and consistent, but it also enables your team to track the data in real time and support informed decision-making. Furthermore, implementing a solution that automates data collection and analysis will also give you the option to integrate it with your other systems (e.g., ERP, CMMS) to drive the value of the investment further.
We also advocate trying out an OEE monitoring software that you want to go with first before making your company commit financially.
Testing different OEE vendors
Nowadays, every modern OEE solution has a free trial period, and you should take full advantage of it. If it doesn’t, we don’t recommend proceeding or explaining to the OEE provider of your choice why they should provide you with at least 30 days to try for free.
So when planning out your OEE implementation project, then, if possible, either do your research before the pilot to determine which OEE vendor you want to try first or, as part of your pilot, run multiple trials at once.
However you end up approaching this, the most important thing to consider is that you understand, before committing, what you will be getting for your money and how your team likes the OEE system of choice.
For example, one of our clients in Denmark knew they wanted to try Evocon and a local OEE provider to see which solution their team (the end-users of OEE – operators, shift leaders, production, quality, and maintenance managers) would prefer. They had Evocon running on one of their machines and the Danish provider on another. After the free trial period, they surveyed their people to make an objective decision.
They ended up presenting 11 questions for 12 people involved and asked each to be answered on a scale from 1-5, where 1 was “Very difficult,” and 5 was “Very easy.” Some of the questions included:
- What was it like becoming familiar with the system, both on tablet and PC?
- How did your colleagues think it was to use the system, to begin with?
- What was it like to change data in the system (e.g., stop reasons)?
- Did you find the information on the screen understandable/useful?
In this showdown, Evocon came on top, and the choice was made based on what the people wanted. From the questions and the answering scale, it’s easy to deduce that for our client, the most important criterion was the ease of use, and they evaluated everything through that lens before making a decision. You might have your own criteria, and whatever they are, make sure you run a test before you commit.
Now that we’ve established what is the prerequisite for this OEE guide, we can move on to the actual steps we recommend taking.
Step-by-step plan to cut downtime by 15%
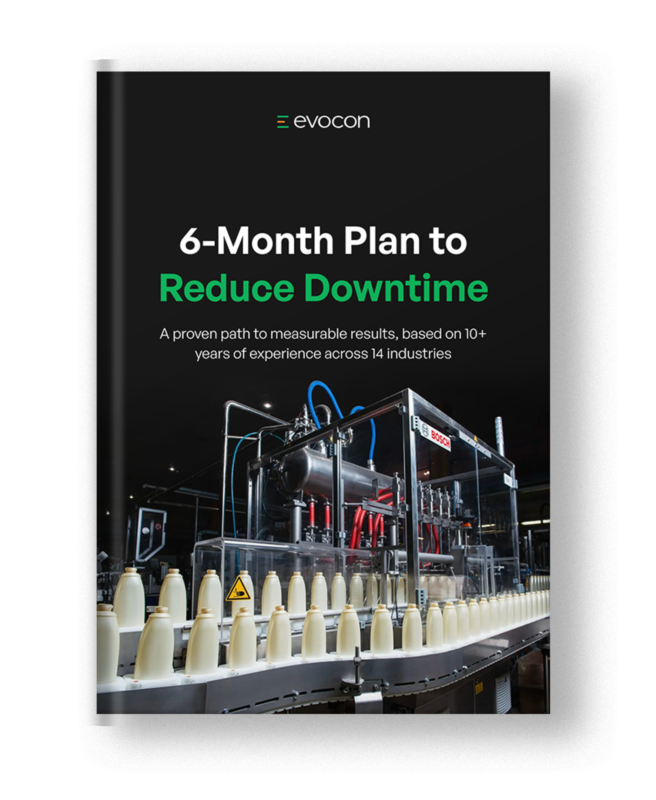
Step-by-Step OEE Implementation Guide
First, by no means is this guide exhaustive. Every journey is unique, and as such, every journey requires slight modifications here and there. What we have here are the distilled recommendations of more than 10 years of working with manufacturers of all sizes around the world.
It’s up to you to combine these steps with your process and add or remove steps depending on where your organization is on your digitalization and OEE journey.
Now that the stage is set, let’s start with the first step – understanding the “Why.”
1. Define the ‘Why’
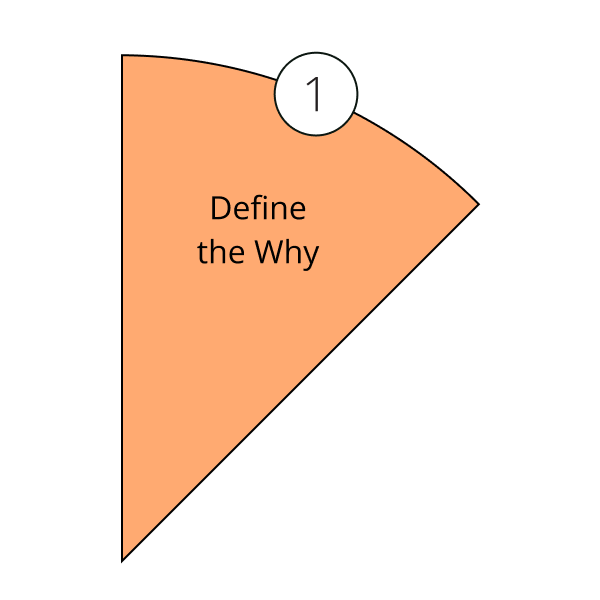
The first step in implementing an effective OEE program is defining the Why or the North Star – the core problem or objective the implementation aims to address. This could be related to improving productivity, reducing waste, or enhancing overall efficiency. By articulating the North Star clearly, organizations can align their OEE implementation with their broader goals and provide a compelling rationale for the initiative to all stakeholders.
From our experience from doing hundreds of free trials with manufacturers, the most common “Why” is usually in the form of “We want to know what is actually going on in production?”. This motivation can take different forms (e.g., “We want to know our uptime or downtime,” or “We want to know why some of our shifts are more productive than others”), but at large, it boils down to the question of transparency. The beauty of this “Why” is that you can always go deeper in your pursuit of understanding what is going on.
We recommend starting with a simple “Why” – “What are our actual top 10 downtime reasons?”
2. Assign a champion
Every successful project needs a dedicated leader or champion – someone who takes ownership of the OEE implementation from start to finish. This individual should possess a deep understanding of the OEE framework and its implications for the organization.
The role of the champion is multifaceted:
- they’ll drive the initiative,
- act as the main point of contact,
- rally teams,
- address concerns,
- communicate with the OEE vendor,
- and ensure that the project stays on course and aligned with the “Why.”
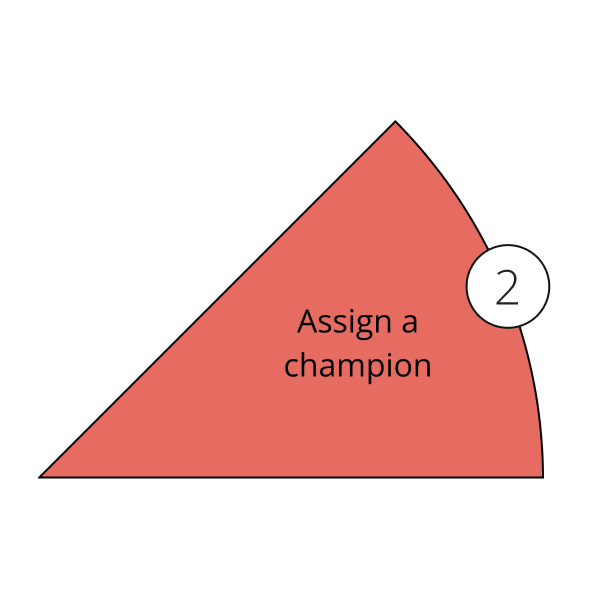
The champion should be someone who has:
- respect in the organization,
- a mandate to implement OEE,
- can motivate teams,
- and possesses the skills to communicate both the technical and business aspects of the initiative.
By having a dedicated champion, the organization ensures that there’s consistent focus, responsibility, and accountability for the OEE implementation. Their passion and commitment to the project can energize others, help them navigate challenges, and ensure the objectives are met.
As the OEE program evolves, the champion also plays a pivotal role in gathering feedback, iterating on the approach, and ensuring the continuous improvement culture is deeply embedded.
Depending on the scope of your OEE project, you might need multiple champions. If the scope is limited to one factory, then it’s a lot easier. If you are looking at several factories, you need to ensure that every factory has a champion and that there is another champion who coordinates the efforts of all. It’s very likely that you, the reader, are one of them.
3. Secure understanding and buy-in
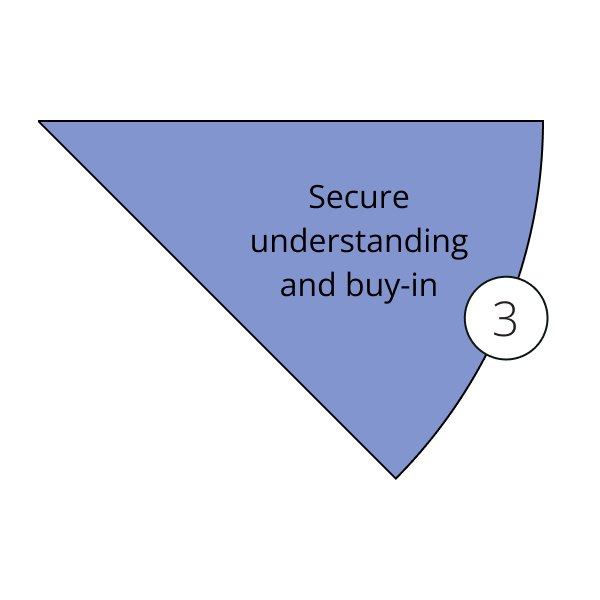
With the “Why” defined, and a champion assigned, the next step is to educate the team on what OEE is, how OEE is calculated, the importance of OEE, and how it contributes to achieving your general goal. It’s crucial to secure buy-in from top management, as their support will be key to driving the initiative forward. However, the shop floor is even more important, as they will be the ones working with OEE day-in-day-out. So make sure you educate both. And have the buy-in of both.
Another stakeholder you want to get buy-in from is your IT security. They don’t necessarily need to know the intricacies of OEE, but they do need to know how data is captured, stored, and secured. Better to have them involved sooner rather than later.
In general, the connection between OEE improvement and organizational success should be emphasized to ensure everyone is on board and committed.
We recommend using our OEE fundamentals section as a basis for educating your colleagues.
4. Choose the pilot
Depending on the scope of the OEE implementation (whether you are an enterprise manufacturer looking to roll out OEE regionally or globally or an SME wanting to track OEE in a single factory), carefully choose your pilot.
Choosing a specific machine, production line, or factory as a pilot for the initial OEE rollout is your next step. Starting with a smaller, defined scope makes the process manageable, allows for easier troubleshooting, and provides a controlled environment where initial issues can be detected and solved before scaling up.
We’ve seen enterprise clients start their pilot in one factory, where there is initial buy-in, and we’ve also seen the pilot run on a single machine in one factory. Choosing your pilot depends on your situation and how much buy-in or resistance you are facing. One machine with a change-minded operator is the way to go if your culture needs a bigger change. One factory with a proactive factory manager is the way to go if you are looking at regional OEE implementation.
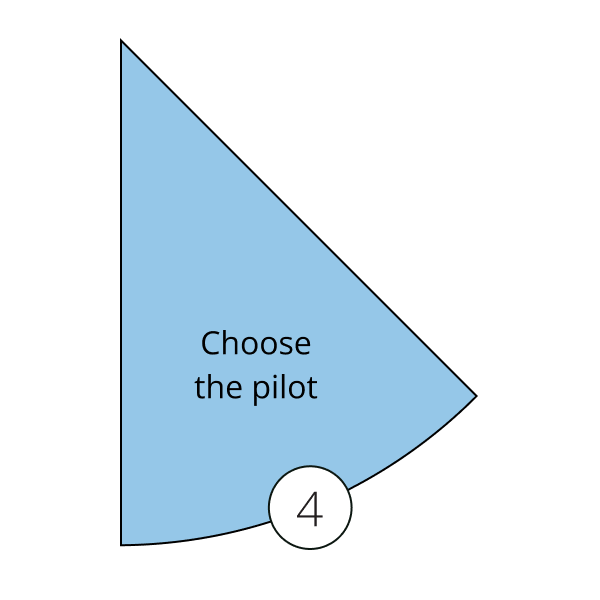
However, if there are no standout factories or machines, you might want to run pilots in multiple factories simultaneously. The reason is simple – if one pilot fails, but others succeed, then you know that the problem is local. If all fail, it might be the system itself.
As we mentioned in the prerequisite part of this guide, the pilot phase is where you also might want to try different vendors if that is your goal. E.g., if you have two vendors you want to try, run a pilot with one on one machine and with the other on another machine (extend the principle to the factory level if you are an enterprise manufacturer). Just know that this will add complexity to the whole process but will put your mind at ease when you finally make a choice.
Getting the pilot right is critical. So our general recommendation is to keep it as simple as possible but adapt the pilot as needed to ensure you are making the right vendor choice and you understand the benefits you are getting.
Start your OEE implementation journey with Evocon
Get all the tools you need to improve productivity and remove waste. Free for 30 days.
5. Set goals
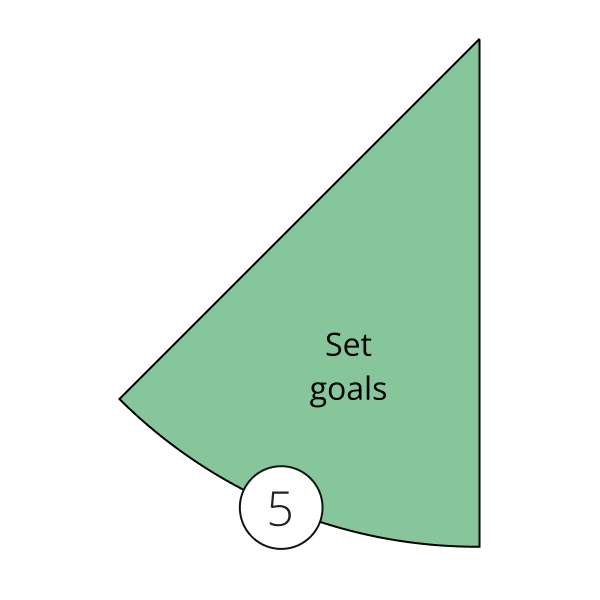
Once you have chosen your pilot, your next step is to set a goal. Your goal(s) should be realistic, achievable, and aligned with the broader objective of optimizing resources and improving the bottom line.
What we don’t recommend is having an OEE-based goal. This is a recipe for failure if your operators (or even management) don’t yet fully understand how OEE works. And even if they do understand, setting an OEE-based goal is not a good idea because you need to give people time to get used to OEE tracking in real-time and collecting data about the production process.
What we do recommend is setting a realistic goal that is a bit challenging but is not a strain. A very common goal our clients set in the pilot/free trial phase is getting all downtime events commented. That serves two purposes – building the habit of collecting information and starting to get a sense of why there are losses in the first place.
Another reason why this is a good idea is that it is simple. And what is simple, sticks. Explaining to your operators that all they have to do is make sure that all production stops have a reason attached does not require them to make a big change in their day-to-day operations, but it ensures that everyone will start getting valuable information and that everyone is involved – operators can report what the actual problems are (very common is that most of the downtime is not related to them) and management will start to understand what decisions need to be made next.
When you start collecting data, do not skip the step of clearly defining your downtime reasons. We have an article here that will help you. Standardizing loss reasons is imperative for long-term success in OEE implementation.
6. Build trust in data
As the OEE program rolls out, it’s important to build trust in the data among all stakeholders. This can be achieved through regular validation of the data, along with transparent communication of the results. The more the data is trusted, the more effective it will be in driving decision-making and improvements.
From our experience, this can go multiple ways. People, if the only benchmark they have is no data, will quickly learn to trust data coming from sensors. But, for example, in one case, we heard from our client how some of their operators kept a double system (tracking data on paper and comparing it to Evocon) to make sure our automated system was correct. If you run into a challenge like this, you can make the life of your operators easier by giving them a digital OEE calculator, instead of pen and paper.
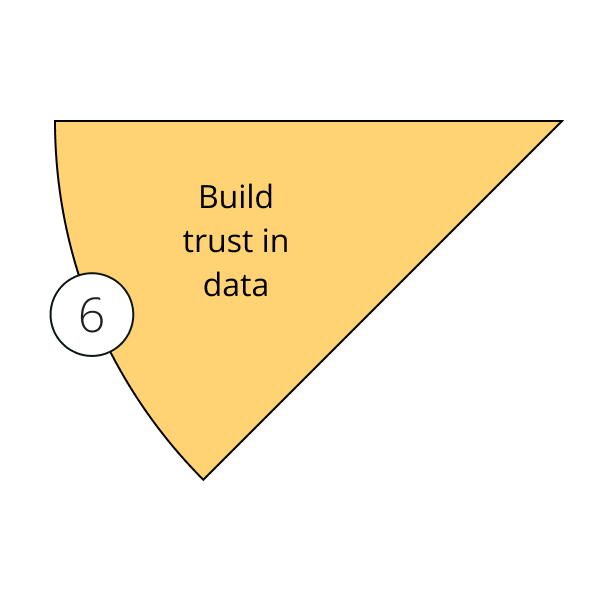
In that particular case, the bonuses of operators were dependent on data being collected and analyzed, so it was totally normal to validate the data. You’ll always have people who are against change and who are advocates of change – in order to build trust, you need to address both.
At the end of the day, your people will need to start using the OEE platform as a single source of truth. So make sure you put effort into building trust in the data that is collected by way of education and explanation.
Trust is best built through communication and transparency. In the initial stages, one of the easiest ways to do this is to have production standups after shifts end. This allows shift supervisors to review collected data with operators and analyze what happened and what can be improved.
7. Monitor, analyze, and improve, continuously
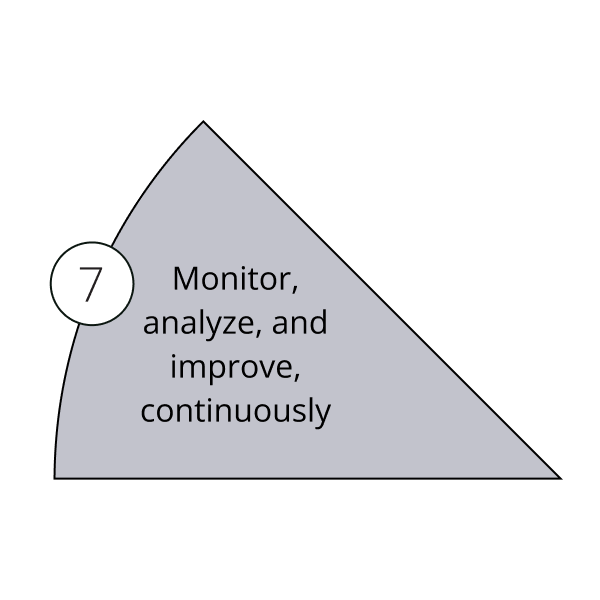
As you gradually progress in your OEE implementation, the next important step is the consistent tracking of OEE and related data over time by using an OEE dashboard. This paves the road for continual analysis of data and focus on efficiency improvement. The data collected should be analyzed to identify trends, losses, and areas of improvement. Depending on your goal, you might first focus just on downtime data to get the quick wins and main bottlenecks out of the way. But as you progress, your analysis should deepen (e.g., speed loss, quality loss, changeover time) to make sure you are improving your OEE.
As the data highlights issues, problem-solving methodologies should be applied to address them. The changes you implement must be based on the analysis of data and followed up by measuring the impact on OEE (or any other KPI that you are focusing on) to make sure that what you are doing is actually having an effect. This further enhances the cycle of continuous improvement, with each insight and action taking the organization one step closer to the “Why.”
Keep in mind that what you are doing is building a new habit and a culture. Making sure data is monitored and analyzed regularly and action taken based on found results is the best way to build a continuous improvement mindset: repetition + consistency = success.
If you are starting fresh with problem-solving methodologies, we recommend the simple 5 Why framework. As you gradually progress, take on more complex methodologies like Fishbone, ASQ, or A3.
8. Review and refine
The final step in the OEE implementation progresses is the review and refine step, which closes the loop. This means you should regularly review how closely you are hitting your targets. Based on these reviews, goals, and strategies should be adjusted as required, ensuring you remain aligned with the ultimate goal.
Also, depending on your overall implementation plan, this is the point at which you decide where to roll out OEE next – is it the next few to ten machines in the factory you ran your pilot, or is it another factory or a set of factories? Just keep in mind the rule of thumb of going small first and gradually increasing your scope.
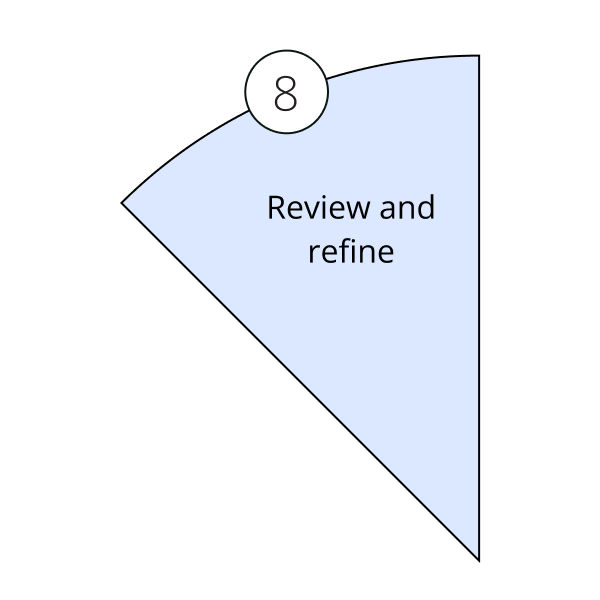
Now circle back to the beginning and review and refine your “Why” and goals, and start again.
At this stage, you can benchmark your OEE against other manufacturers and world-class OEE to see where you stand and how high to set your bar.
Final note: Creating a Culture of Continuous Improvement
This guide is meant to help you create a culture that values and encourages continuous improvement. That is the only way that you will sustain the change and improvement.
Participation and suggestions from all staff should be encouraged, and an environment should be created where failures are seen as opportunities for learning and improvement. This cultural shift, combined with the OEE initiative, will take your organization closer to your “Why” and ensure your business stays relevant and successful.
We hope this guide helps you in your OEE implementation journey. If you have any questions, don’t hesitate to contact our team, and we will do our best to help. If you are interested in trying Evocon as your OEE system, you can get started by registering for a free trial today.
And if you want to learn from the experience of others, we encourage you to explore our case studies section, where you can read about the challenges our clients have faced, how they overcome them, and what they have achieved.