Our ROI calculator shows you the value of improving OEE. But exactly what should you do to improve it? Who needs to be involved? What tools and techniques should you use? In this article, we look at the seven best practices that we’ve seen our clients use to achieve higher productivity and improve OEE.
How to Improve OEE
Overall Equipment Effectiveness (OEE) is a measure of machine potential that brings visibility to opportunities for improvement. Manufacturers implement OEE to identify, monitor, and reduce production losses. As such, it has become a universal KPI for manufacturers and a lean manufacturing best practice. This is why you should take steps to improve it.
Learn more: What is OEE and how it works & How to Calculate OEE – Formulas & Examples
1. Improve OEE by assigning a digital champion
Sometimes, a company may struggle to gain OEE improvement. Since a successful implementation is required before we can begin to improve, let’s start here.
There can be many reasons why a company might be challenged to implement OEE. Maybe they have made a mistake in calculating OEE which results in a perception that the number is wrong. Or perhaps there is a high level of resistance to change from one work cell. Regardless of the reason, we have found there is one best practice that can help: assign a digital (or project) champion.
When a company designates a digital champion for OEE implementation, they create ownership and accountability for its success. This means that as issues surface, such as those mentioned in the previous paragraph, there is someone who will work to resolve them. Not only does this go a long way to ensuring a successful implementation, but it also will ensure that changes made will be sustained.
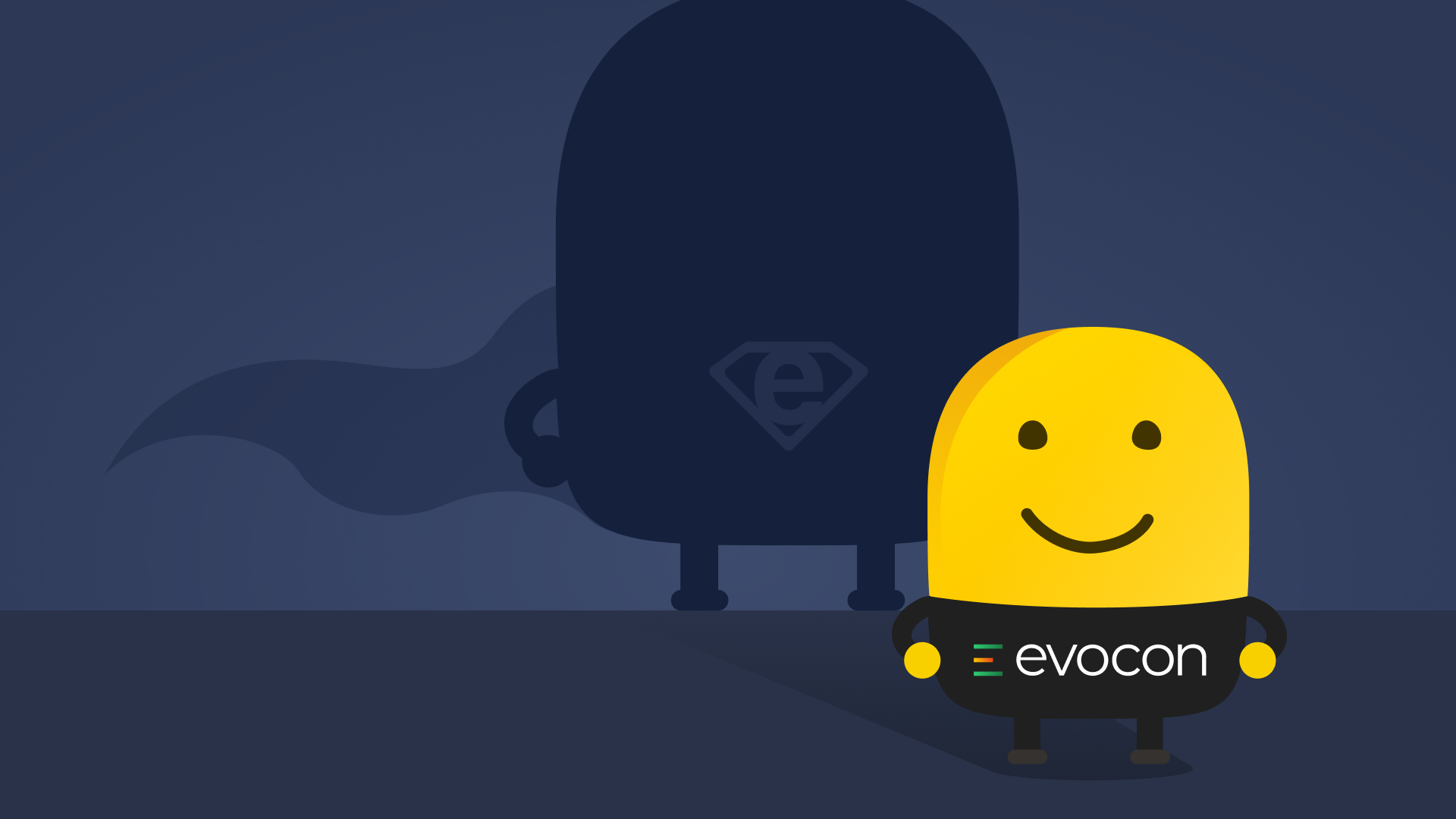
In selecting a champion for your OEE implementation, we recommend someone who is well respected by operators on the shop floor, likes to collect and analyze data, and has excellent communication skills.
Learn more: Why You Need a Digital Champion in Manufacturing
2. Automate data collection and reporting
The next best practice for improving OEE is to automate the collection and reporting of production data using overall equipment effectiveness software. Through years of working with clients in the field, we have gained an intimate understanding of the pain and shortcomings of manually collecting data. Our experience has shown us that insufficient data collection is a primary barrier to achieving higher levels of productivity and improved OEE.
It wasn’t long ago that manufacturers did not have an alternative to pen, paper, or excel for collecting OEE data. Not only was the process tedious, but it was also prone to errors. Worse, by the time reports were available, it was already too late to change the outcome. Thankfully, the rapid adoption of the IIoT has made the technology affordable. For this reason, manufacturers should not settle for manual data collection or manage the piles of paperwork or excel files that this outdated process requires.
A better option exists, and it will help with efforts to improve OEE: automate data collection and reporting on your shop floor.
Learn more from our Ultimate Guide to Production Monitoring
Automate data collection
Improve your OEE by automating data collection and reporting on your shop floor with Evocon. Free for 30 days.
3. Visualize and display real-time OEE on the shop floor
Visualization dramatically improves our ability to comprehend complex data. In visual form, we process information faster, and relationships are easier to identify. The result is higher levels of engagement by both operators and team leaders.
Evidence from the United States has shown that engaged employees lead to gains in:
- productivity (+17%),
- sales (+20%),
- and profitability (+21%).
Further, job satisfaction in factories also improves, leading to:
- fewer defects (-40%),
- lower absenteeism (-41%),
- and fewer safety accidents (-70%).
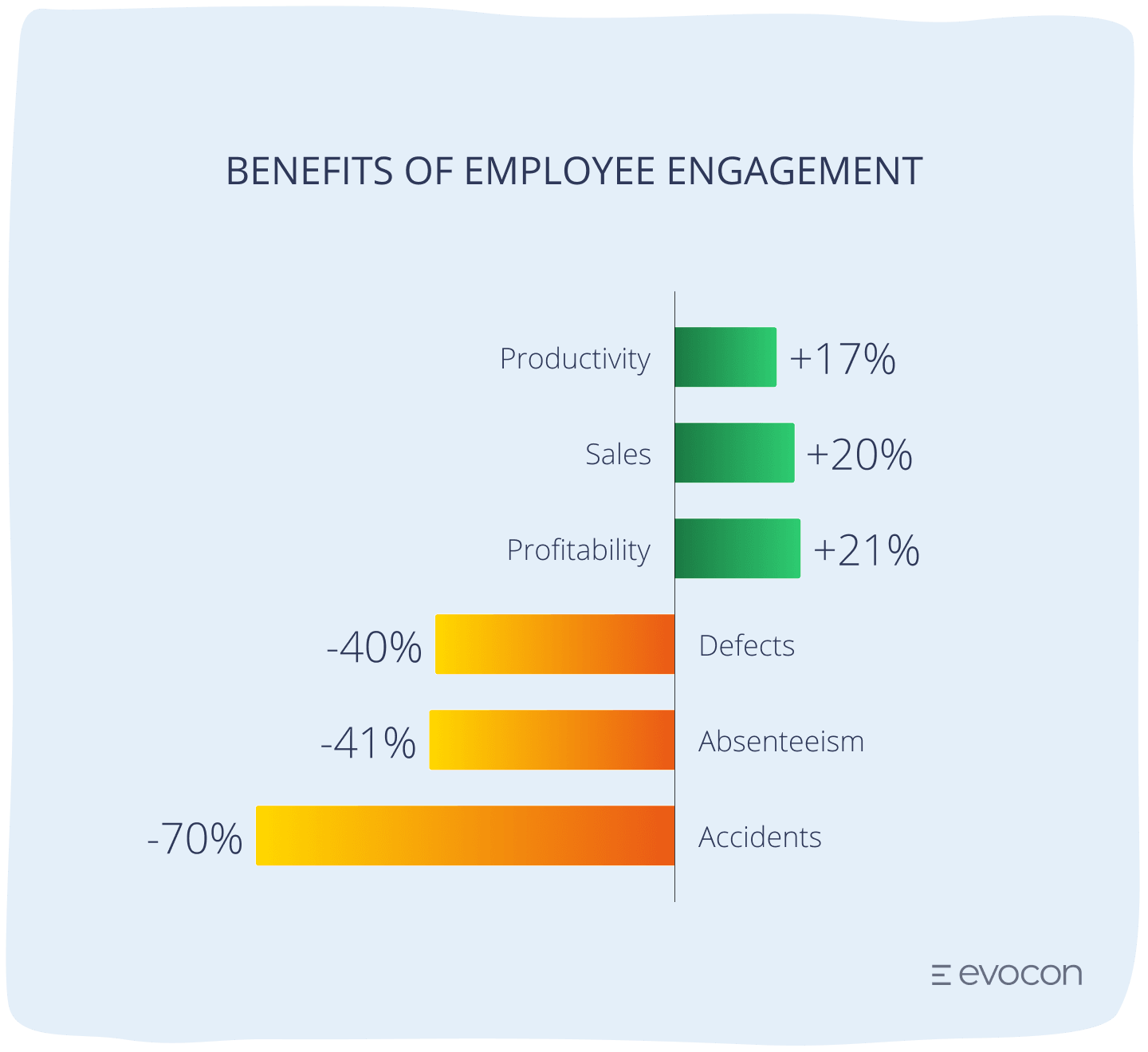
To maximize the benefits of visualizing production data, you need real-time visibility on the shop floor. For that, you can use OEE displays that display the data that is most relevant to the shop floor.
The goal is to make the information available to be acted on in the moment. This way, if a problem that affects productivity does occur, your teams are aware of it in real-time. More importantly, they have time to make adjustments that will change the results before it’s too late.
Learn more: How visualizing production data drives engagement and productivity
Learn more: What is a Visual Factory and How to Achieve It
4. Make sure all production stops are commented
Once you have OEE monitoring software in place, then another best practice that can help you improve OEE is to ensure that all production stops are commented on. A straightforward method to ensure all stops receive comments is to simply ask supervisors to check at the end of each shift. Or if you use Evocon, then operators can easily see if they forgot to comment on any of the stops.
As manufacturers, you are without question aware of what production downtime can cost your business. Indeed, creating visibility of downtime is a primary motivation for many companies implementing OEE in the first place.
However, having visibility of when production is stopped is only half the battle. To begin improving OEE, you also need to know why the stop occurred. This is where requiring comments on all stops is essential: it provides you with the “why”. And once you know the “why”, your shop floor can use the 5 Whys to look for solutions.
To fully leverage the usefulness of comments on production stops, you will want to spend some time creating a system to classify machine downtime causes.
Step-by-step plan to cut downtime by 15%
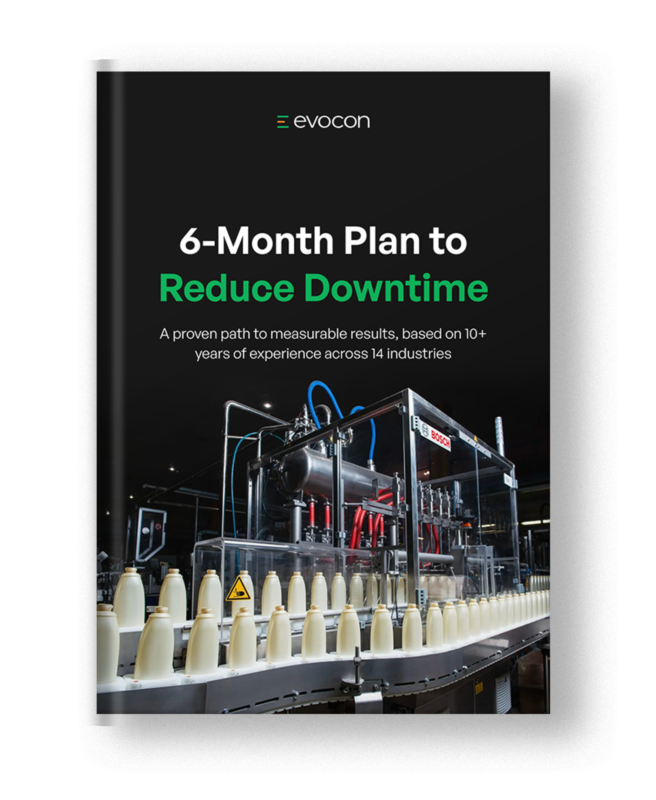
5. Implement cross-functional daily review and discussion sessions
The point of this best practice is to improve communication and engagement across all departments that touch the production process.
So, if you have a quality assurance department and maintenance team, by all means, invite a representative from each to participate in the daily sessions. The more minds you engage in problem-solving, the faster the rate of improvement, and the higher the quality of solutions that will be possible.
See how TMI used Evocon and cross-functional daily meetings to improve OEE by 30% or how Meconet’s weekly review helped increase operating time by 50%
6. Start eliminating the Six Big Losses to improve OEE
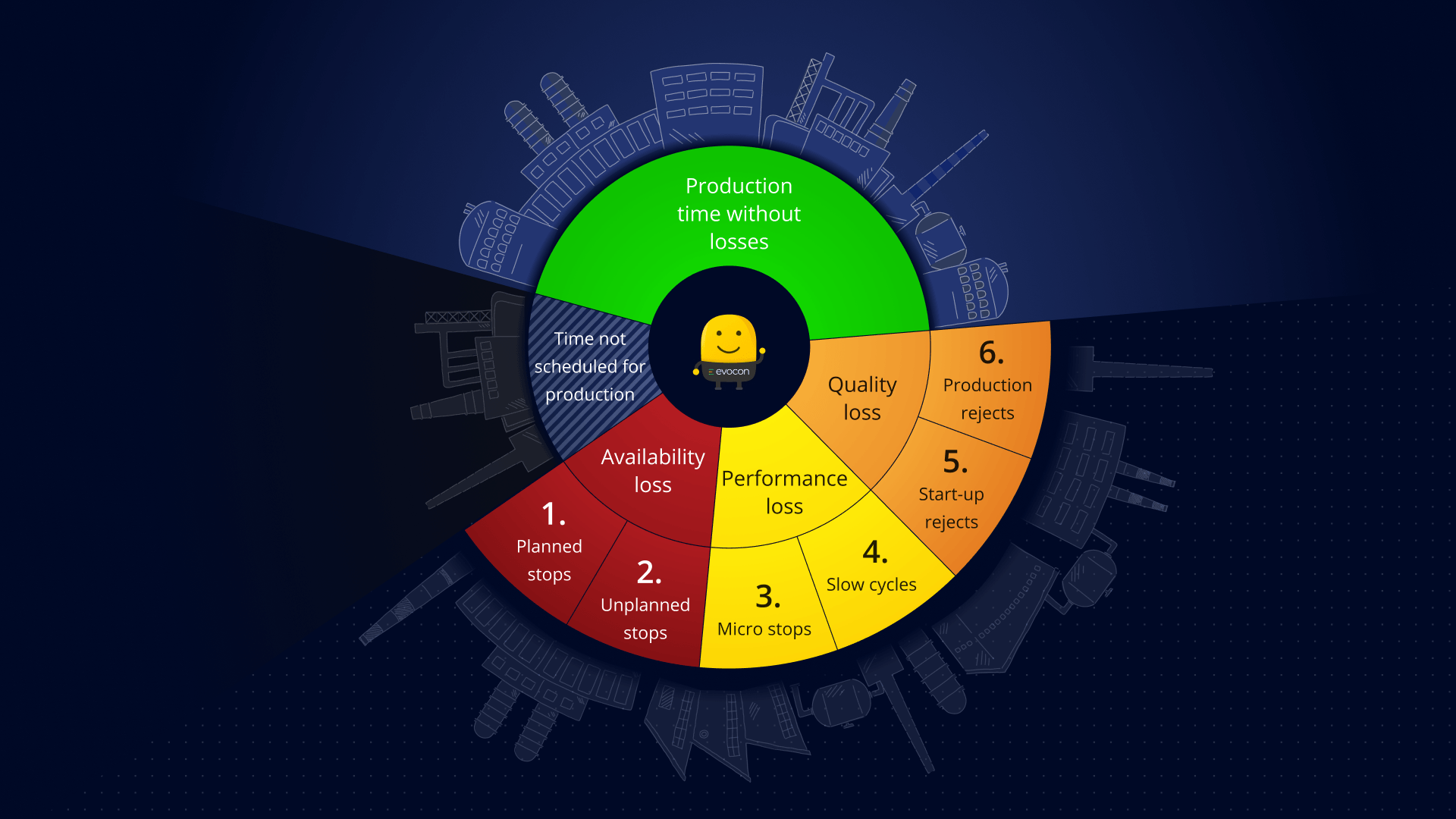
The Six Big Losses make up the basis for calculating OEE. By analyzing the causes and relative amounts of the six big losses at your plant, you can gain an understanding of where to focus your activites to achieve OEE improvement.
We recommend that the first big loss to focus on should be unplanned downtime. Unplanned downtime can result from issues such as machine breakdown, which you can track using technical availability; to poor internal logistics, for example, missing material or operator. Since having a machine down can stop the entire production process, it follows that this would be the first area to focus on.
However, there can be exceptions, as we have also seen performance loss on machines being a big contributor to losses in productivity. So you should ultimately be guided by your data.
Learn more: Six Big Losses in manufacturing
7. Utilize Root Cause Analysis
Once OEE brings visibility to your six big losses, it is time to start problem-solving. For this effort, we recommend utilizing Root Cause Analysis (RCA).
RCA is a systematic problem-solving process that helps us to understand the core cause of a problem. The idea is that by solving for the root cause, rather than symptoms, you can prevent the problems from recurring.
Learn more: Benefits of Root Cause Analysis in Manufacturing
RCA consists of six steps:
- Define the event.
- Determine the causes.
- Find the root cause.
- Find solutions.
- Take action.
- Verify solution effectiveness.
Learn more: How to Perform Root Cause Analysis in 6 Steps
Take Action
In this post, you have learned about the seven best practices for improving OEE. Now it’s time to start putting them into action on your shop floor following an OEE implementation guide that will set you up for success.
If you run into issues or have questions, reach out to us. We are always happy to help.