Lean manufacturing, at its core, is about maximizing value while minimizing waste. By systematically identifying and eliminating inefficiencies, manufacturers can improve their processes, reduce costs, and improve overall productivity. A vital aspect of this philosophy is understanding and addressing the 8 wastes of lean manufacturing. These are the non-value-adding activities that hold back operational excellence.
What Are the 8 Wastes of Lean Manufacturing?
The 8 wastes of lean manufacturing originate from the 7 wastes developed by Taiichi Ohno, the creator of the Toyota Production System (TPS). Ohno identified seven original wastes (Muda in Japanese), which were later expanded to eight to include one additional waste — unused employee talent. These wastes represent anything that consumes resources without creating value for the customer. Recognizing and eliminating these wastes is fundamental to achieving lean manufacturing goals and lean continuous improvement.
Below are the 8 types of waste in lean manufacturing. If ignored, they can significantly impact a manufacturing operation’s efficiency and profitability. The acronym DOWNTIME is used to remember them. Here, we go through each waste and some strategies to minimize it.
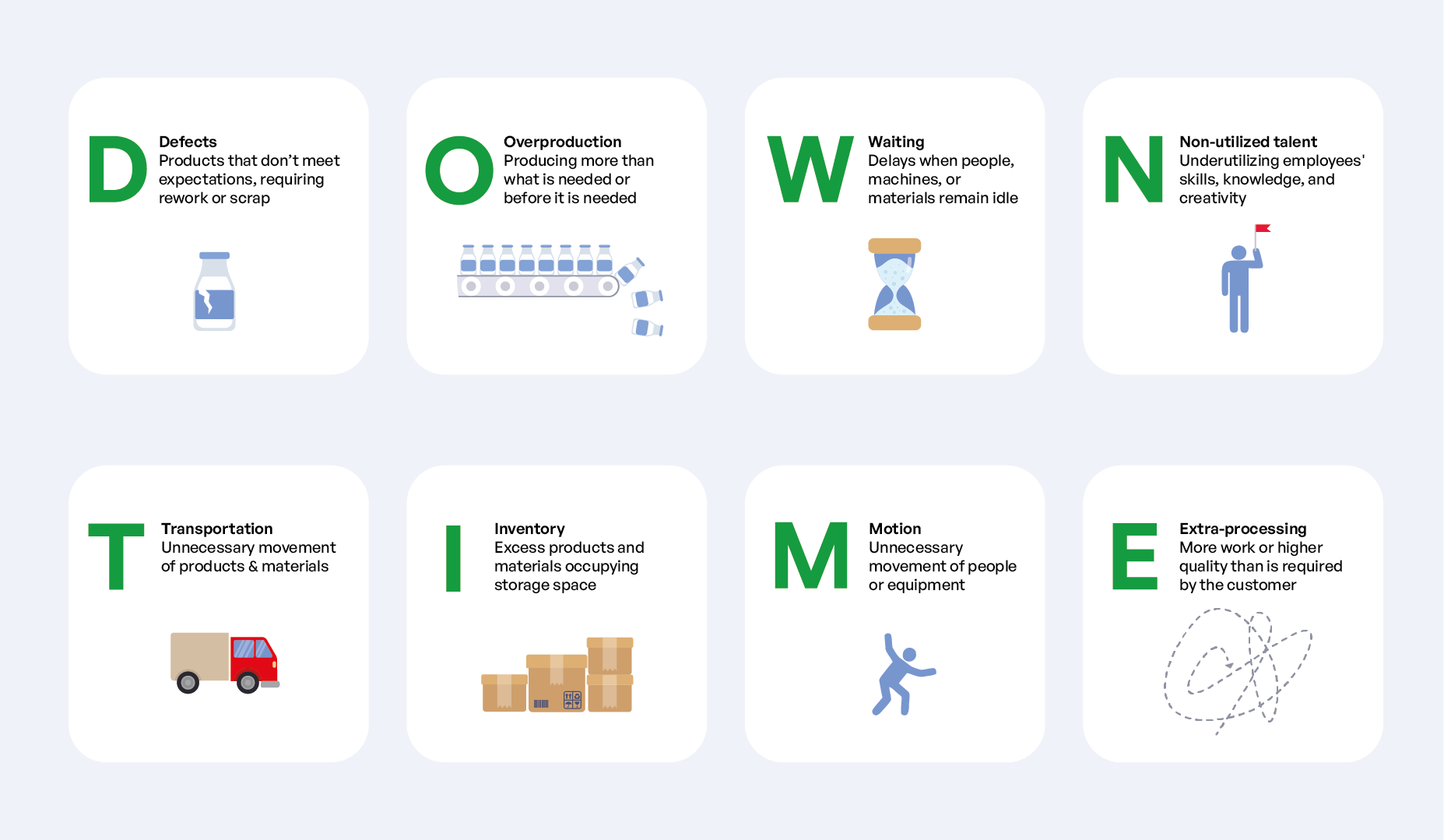
1. Defects
Defects are products or services that fail to meet customer expectations, requiring rework or scrap. Some common examples of defects in manufacturing are misaligned parts, incorrect assembly, and cosmetic issues.
One way to address defects is to implement Six Sigma — a data-driven process improvement methodology that reduces variation to improve quality. Additionally, root cause analysis is used to get to the bottom of the issues causing the defects.
Using Evocon’s Checklists, Chala SAS, a leading producer of fasteners and straps for bras, girdles, and other garments in Latin America, reduced potential scrap by 3x compared to its previous quality control process.
2. Overproduction
Overproduction is producing more than what is needed or before it is needed. This leads to excess inventory, higher storage costs, and wasted resources.
To tackle overproduction, manufacturers can implement other lean principles and methods like Just-In-Time (JIT) — a workflow methodology that aims to reduce flow times within production systems.
3. Waiting
Waiting occurs when people, machines, or materials remain idle due to delays. This leads to inefficiencies that ripple throughout the production process. Machine downtime, supply chain delays, or bottlenecks often cause these delays.
To solve waiting issues, manufacturers can use automation, improve machine utilization, implement real-time machine monitoring systems, and focus on scheduling.
Using Evocon, Torm Metall, an Estonian manufacturer specializing in creating parts and assemblies from aluminum and stainless steel, realized that their process was delayed by waiting on a worker. By adding an additional worker, uptime quickly jumped to 70%, doubling the output.
4. Non-utilized talent
The latest addition to the 8 wastes of lean, non-utilized talent refers to a manufacturer’s failure to capitalize on employees’ skills, knowledge, and creativity.
Encouraging employee creativity and innovation is crucial. To address this, employers can focus on continuous improvement programs and strive to engage employees.
Super Cerame, a producer of ceramic tiles in Morocco, has seen improved working conditions and increased motivation from its workers since implementing new software and making KPIs visible to all.
5. Transportation
This is the unnecessary movement of materials or products, increasing the risk of damage and delays.
This can be tackled using lean techniques like value stream mapping, where manufacturers create a visual guide of each step necessary to deliver a product, intending to optimize the entire process.
6. Inventory
Inventory includes excess raw materials, work in progress, or finished goods that tie up resources and require storage space.
To optimize inventory spaces, try using lean methodologies like Just-In-Time. Additionally, try using 5S methodology, a structured five-step process for sorting, organizing, and optimizing a workspace.
To optimize their inventory, Thermory, an Estonian-based chemical-free wood processing company, changed from paper worksheets to digitalized monitoring, which led to inventory counts taking only a few days instead of a whole month.
7. Motion
Not to be confused with transportation (number 5) this is the unnecessary movement of people or equipment, leading to wasted time and potential injuries.
Similarly to inventory, one way to tackle motion as a waste is to implement 5S methodology, which can organize your workspace to reduce your employees’ movement.
8. Extra-processing
Finally, we have extra-processing, which involves performing more work than the customer requires, adding cost without adding value. This includes additional work such as excessive polishing/finishing or overcomplicated designs.
Extra-processing can be addressed with value stream mapping, where you can identify and eliminate unnecessary processing.
💡Note: TIMWOODS is another acronym used to remember the 8 wastes, so if you already use TIMWOODS (Transportation, Inventory, Motion, Waiting, Overproduction, Overprocessing, Defects, and Skills), there’s no need to worry.
Now that we understand the 8 wastes, let’s move on to how modern technology helps manufacturers eliminate them.
Improve production efficiency
Evocon helps you reduce costs and improve productivity.
How Manufacturers Can Tackle the 8 Wastes With Modern Technology
Modern technology plays a key role in eliminating the 8 wastes. Below are some technologies manufacturers can use to address them.
Real-time Monitoring
Real-time machine monitoring software, such as Evocon, uses sensors and data analytics to track production processes and identify bottlenecks in real time. This enables immediate corrective actions, minimizing downtime and improving product quality.
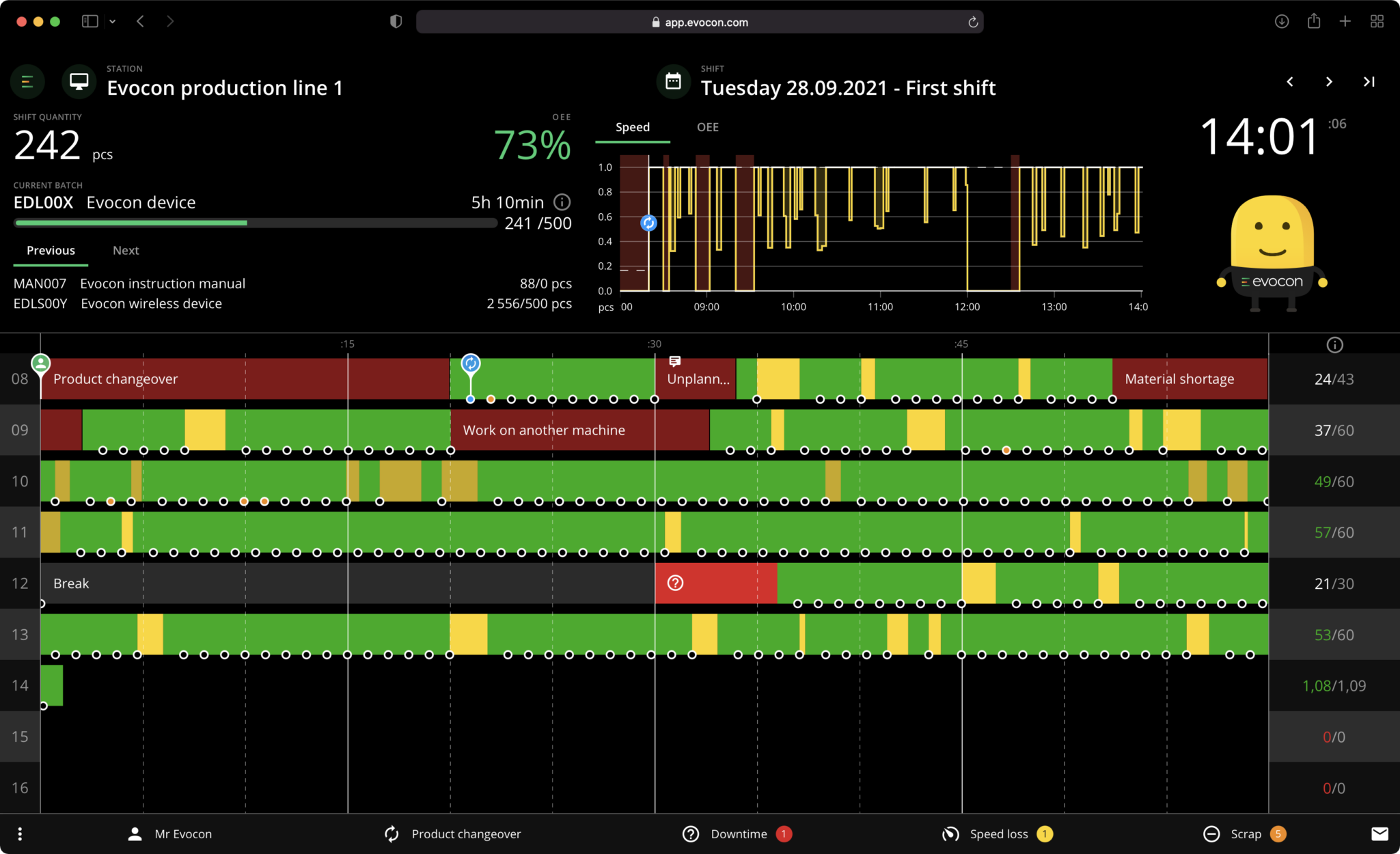
After implementing Evocon, ELBAK SA, one of the leading producers of canned fruit in Greece, started tracking the production process in real time and analyzing information every hour. Learn how they keep track of production targets, actual output, reasons for production stops, and continuous calculation of OEE.
Visual Management
Digital displays can show production data, KPIs, and waste tracking in real time. For example, digital dashboards around the shop floor can display live performance data, allowing teams to spot inefficiencies quickly and take immediate action (see more ways to utilize visual techniques in your factory).
At Tecpap, a company specializing in paper bag production in Morocco, shop floor operators use Evocon tablets to monitor machine performance in real time and capture information on losses. They also rely on the Factory Overview screen to track production and make necessary adjustments to processes.
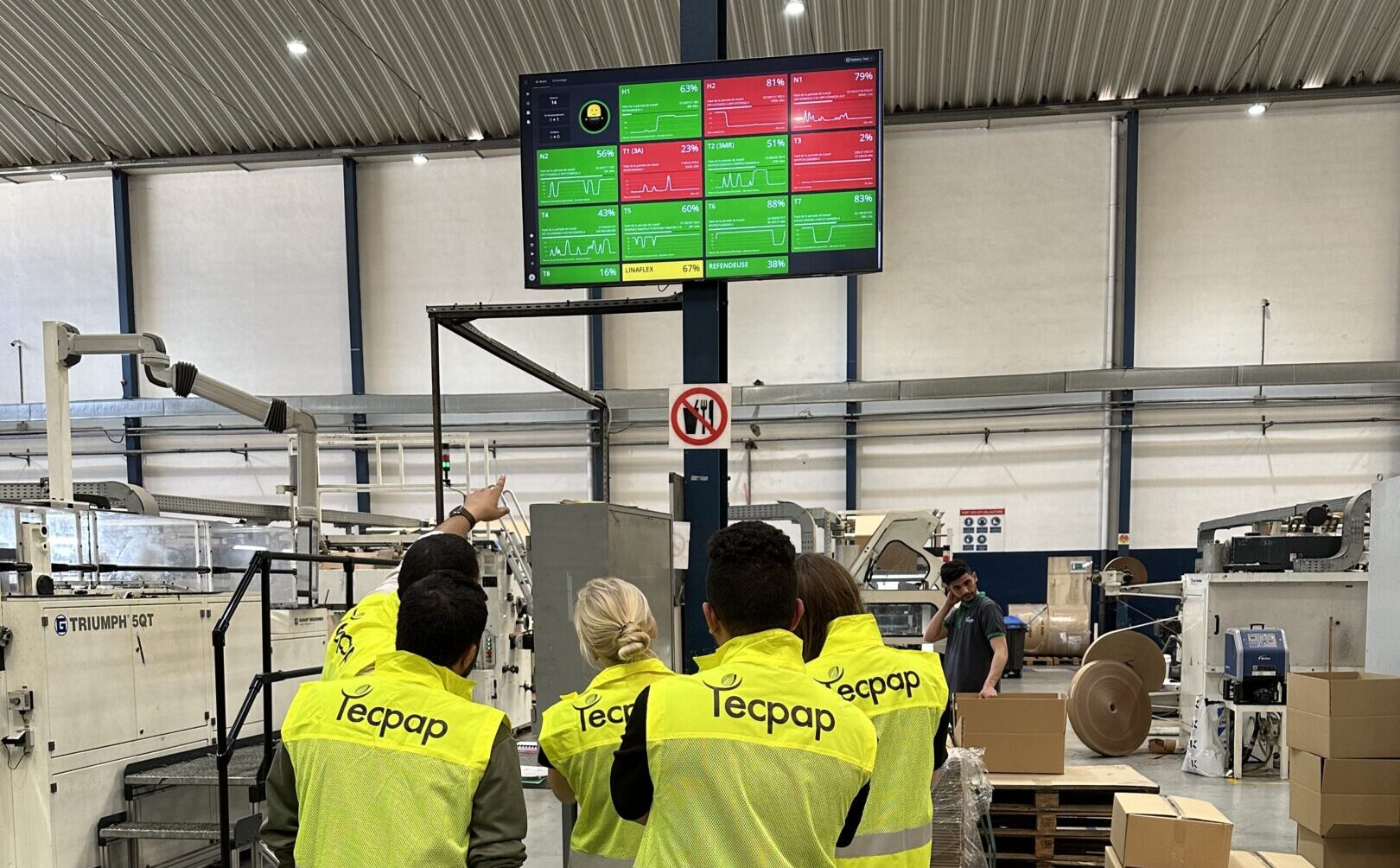
Predictive Maintenance
Implementing predictive maintenance systems can anticipate equipment failures, minimize unplanned downtime, and reduce maintenance costs. Read more on real-life applications of predictive maintenance.
Automated Inventory Management
Inventory management software and RFID technology are used to track material flow, optimize inventory levels, and prevent overproduction.
Collaborative Platforms
Using collaborative software facilitates communication and knowledge sharing among employees, maximizing the utilization of talent. This can also help lower staff turnover by increasing employee engagement and knowledge. Evocon is often used in daily cross-departmental meetings to share information between teams.
Nova Packaging is a paper packaging producer based in Thessaloniki, Greece. One of the first challenges they noticed when looking to improve efficiency was the need for a neutral reporting platform across departments. Each team presented reports with diverse data in various formats in their daily meetings, making it difficult to grasp each topic fully. This led them to seek a unified platform where every department could display standardized reports, ensuring that everyone could understand the information presented.
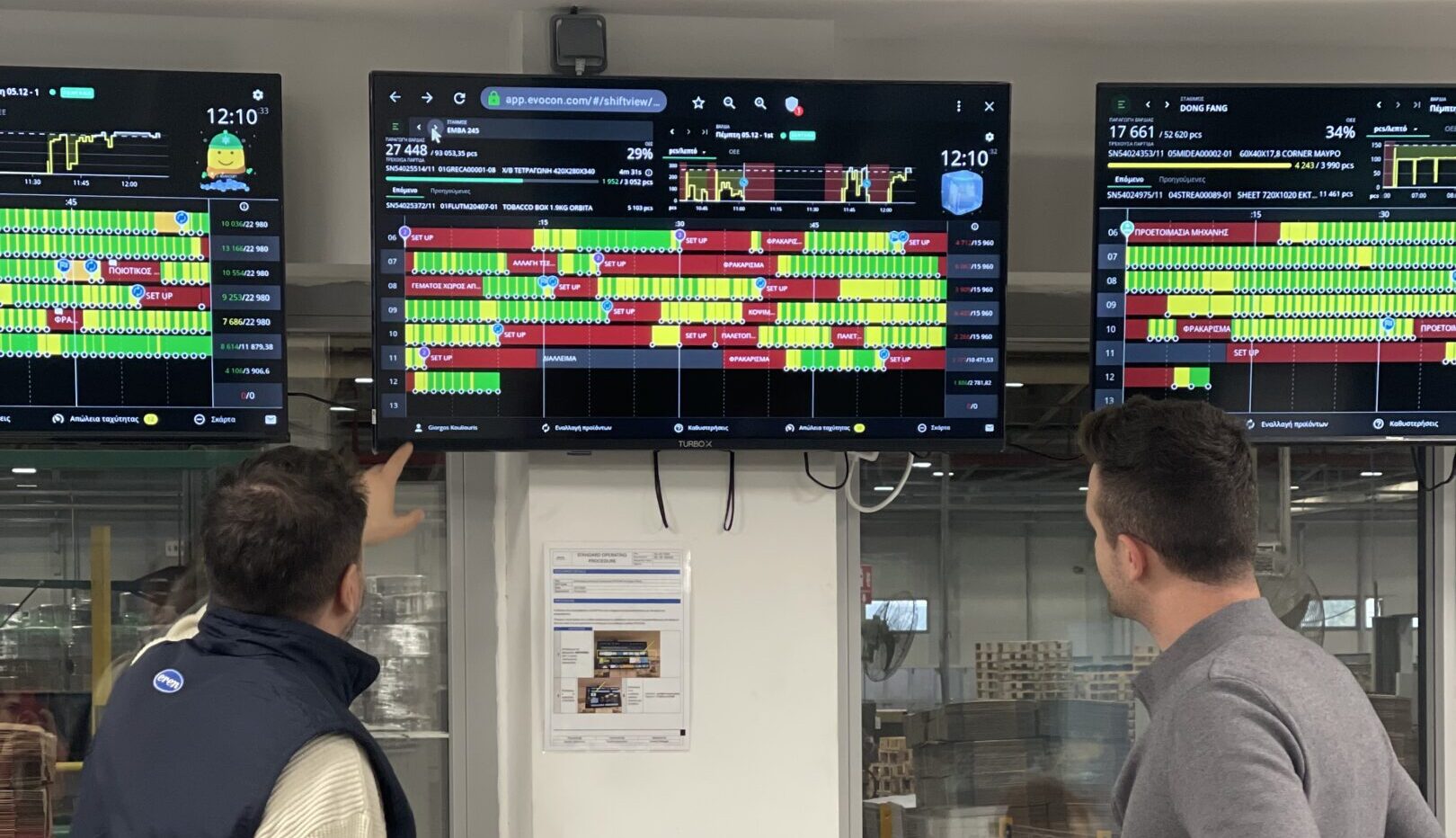
Manufacturing Execution Systems (MES)
MES systems provide a comprehensive overview of the production process, enabling manufacturers to identify and address inefficiencies across the entire value stream.
Key Takeaways
Lean manufacturing reduces waste and costs by focusing on eliminating inefficiencies to maximize value. Addressing the 8 wastes in this article is critical to improving productivity and cutting costs.
The 8 Wastes, which can be remembered using the DOWNTIME acronym, include Defects, Overproduction, Waiting, Non-utilized talent, Transportation, Inventory, Motion, and Extra-processing.
Using modern tools, such as real-time monitoring, visual management, predictive maintenance, and automated inventory systems, manufacturers can help identify and eliminate these wastes, and gain greater control over their operations.
Embracing these principles and technologies can lead to significant improvements in efficiency, profitability, and overall operational excellence.