As a Maintenance Manager for a manufacturing plant, your world revolves around keeping production running by overseeing the process of equipment maintenance. This post explores how Evocon’s production monitoring and OEE software helps and benefits your role in this process.
Evocon Provides Maintenance Managers with Real-Time Machine Monitoring and Live OEE Tracking
No matter the industry or the type of production process utilized, a manufacturer’s profitability is highly contingent on the reliable performance of plant equipment.
As a Maintenance Manager, you no doubt understand the importance of OEE in manufacturing. Perhaps you have even educated others about OEE being a key to optimum plant performance, continuous improvement of equipment reliability, and a universal manufacturing KPI.
Learn more: What is OEE and How Does It Work?
As we will see, Evocon’s OEE software leverages recent advances in IIoT technology into a highly intuitive and user-friendly solution that is easy to self-install and implement. Moreover, it provides the benefits you expect from OEE. Specifically, automated data collection that reduces paperwork and real-time monitoring of machine operating characteristics like downtime, speed, and quality.
Maintenance Managers Make Production Possible
Maybe your plant operates in a purely reactive mode, where equipment breakdowns create the daily schedule. Or perhaps you have adopted preventative and predictive practices, with steady progress on the road to proactive. Regardless of the current state of your department’s maintenance maturity, your role is all about effective management and continual improvement to the process that ensures all plant assets remain in good working order.
Somedays, this means you are on the shop floor working with production supervisors and machine operators to expand autonomous maintenance. Other times, you are reporting to company leadership about preventative maintenance (PM) completion trends or analyzing opportunities to reduce store inventory. The tasks are as varied as the equipment that you maintain. But one thing is certain – the modern manufacturing plant can not operate profitably without you.
Top Five Challenges of Maintenance Managers and How Evocon Helps Solve Them
Every manufacturer is different, but there are common challenges for maintenance managers, no matter what sector, product, or location. Let’s look at the top five challenges that we hear about and then show how Evocon benefits or solves the problem or challenge.
1. Insufficient Preventative, Proactive Maintenance
There is a clear need to improve the percentage of tasks completed in the category of proactive maintenance. Yet, reactive maintenance remains one of the most common approaches utilized today.
Why does this remain true? Especially in the context of widespread understanding that poor maintenance directly and significantly limits productivity. Moreover, it leads to lower product quality and increases the direct cost of production?
One reason is that we are too busy fixing things to improve processes using data and root cause analysis.
Evocon’s OEE software provides a means of communication between maintenance and the shop floor. This way, as operators register causes of machine downtime or a concern that the machine requires maintenance to prevent a failure, maintenance has a means of hearing and responding to these critical communications.
The implementation of a real-time OEE tracking solution is one-way manufacturers can enable a move from reactive to preventative maintenance.
2. Frequent Problem Solving
Frequent problem-solving only provides enough time to restore operability. Yet, lost are the learning and insight that is required to identify the root cause and prevent future occurrence. The frontline workers of the organization simply do not have enough time to learn why the equipment failed. Thus, they are stuck in a reactive mode of problem-solving.
Evocon helps by providing rich machine level process data – in real-time and with historical trends. This data creates the opportunity to quickly perform root cause analysis on the problems that create the most downtime or loss. Over time, this leads to less recurring issues, giving more time to move from reaction-based problem solving to preventative maintenance strategies.
Learn more: Benefits of Root Cause Analysis in Manufacturing & How to Perform Root Cause Analysis in 6 Steps
Moreover, Evocon is a great tool for analyzing technical availability to validate that the actions your team or your maintenance provider takes to prevent unexpected downtime have the desired effect.
3. Credible OEE Measurements
Total Productive Maintenance (TPM) has, since its inception, included OEE monitoring and measurement as the primary cornerstone of its philosophy. Furthermore, the achievement of 85% OEE was used to signify a fully functioning TPM implementation.
However, as authors, Smith and Hindcliffe point out in RCM – A Gateway to World Class Maintenance,
“The problem (with TPM/OEE) comes when you try to figure out how to establish a data system that will collect, analyze, and then produce credible OEE measurements that are actively employed in management decision making. It probably occurred, but we haven’t witnessed a truly successful working TPM program in our 20 years in the maintenance field”
Evocon is the answer to this problem. The software is designed from the ground up to collect, analyze, and visualize high-integrity OEE measurements in real-time. Our clients routinely utilize our reporting function to drive and improve not only management decision making but also as a means to engage operators on the shop floor in problem-solving.
Real-time OEE Software
Collect, analyze, and visualize high-integrity OEE measurements in real-time. Free for 30 days.
4. Meaningful Engagement with Non-Maintenance Employees
A foundational pillar of world-class maintenance is a new partnership between operations, engineering, maintenance, and technical services. It has challenged many manufacturers to implement as it requires breaking down old ways of thinking, long-entrenched silo’s, and human resistance to change. Nonetheless, the partnership must be forged and then focused on improving OEE by eliminating the six big losses.
This includes engaging operators through education about maintenance practices and enlarging the operator’s job to cover first, daily maintenance, and ultimately, autonomous maintenance.
Again, Evocon is an ideal solution to both identify and reduce six big losses and engage maintenance technicians together with machine operators.
As consultant Oskar Olofsson correctly points out, there are two ways to achieve world-class maintenance: TPM and Lean.
“Fundamental for TPM is a functioning OEE measurement. OEE gives a common measure of production and maintenance and allows common goals. The potential for improvement can be clearly defined. The choice of the available tools can be made on factual evidence.”
Oskar’s quote goes to the heart of the problem and its solution: without a common measure of production and maintenance that OEE provides, it’s difficult to align the functions with a common goal. And this goes a long way to explain why engaging operations has proved so challenging and is precisely where Evocon can help.
5. Improving Maintenance Maturity
This might be perhaps the most challenging dimension for Maintenance Managers. Simply put, organizational change, even on a small scale, can be difficult. Therefore, it is not surprising then that when a change is so significant as to be classified as transformative, the level of difficulty has most certainly increased by a level of magnitude.
This is definitely true for the transformation from reactive to knowledge-based maintenance.
Levels of Maintenance Maturity
Reactive | Preventive | Predictive | Proactive | Knowledge-Based
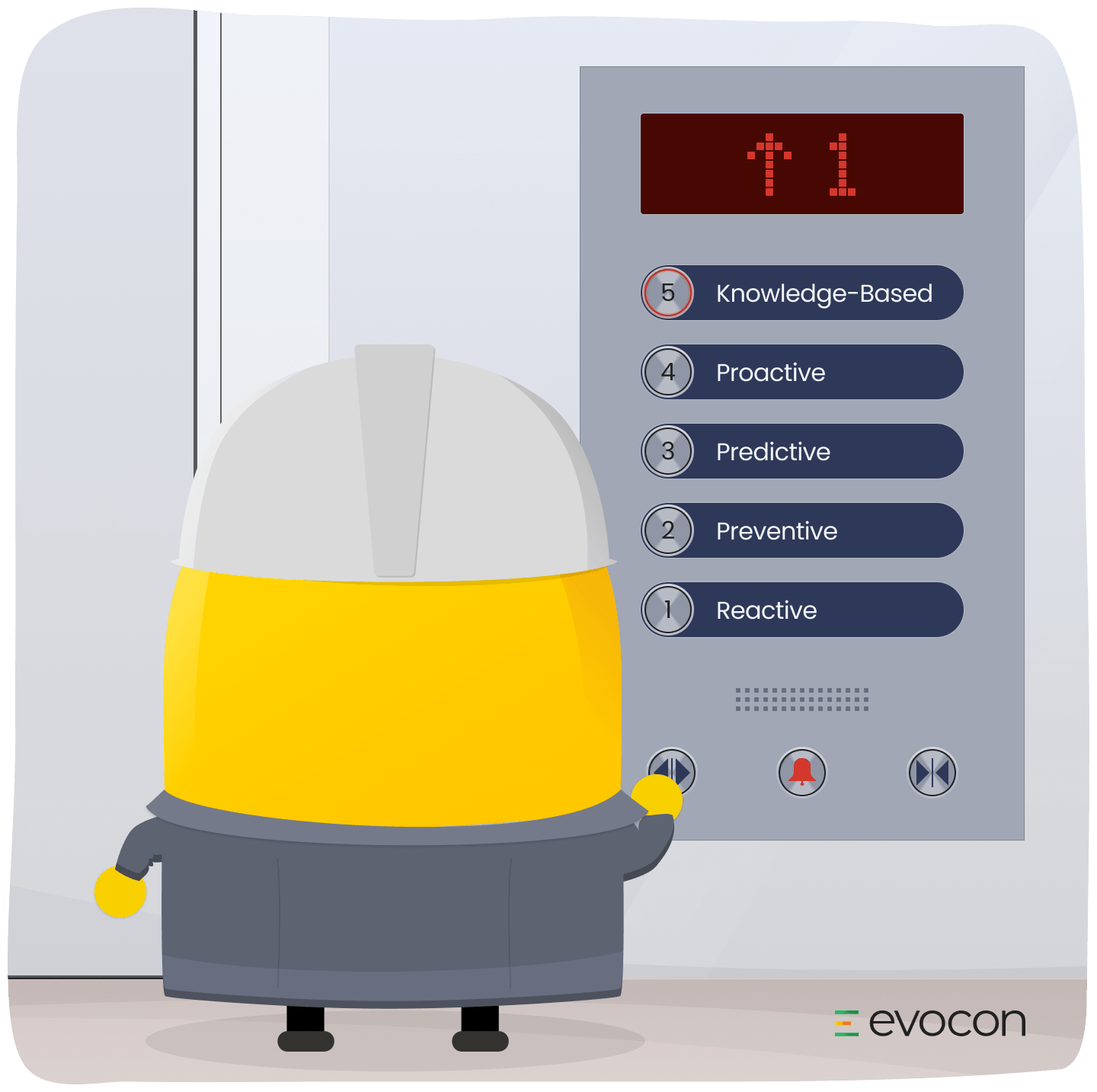
There are a number of ways that Evocon can help you in this process, and we have discussed several above. However, there is considerably more to share than can be practically covered in this post. You can continue the conversation by signing up for Evocon’s free trial.
Next Steps
To be successful, today’s Maintenance Managers in manufacturing require credible OEE measurements, automated collection of machine data. And for all of this to be accessible in real-time from anywhere in the world.
This is what Evocon is all about: empowering maintenance processes with real insights and information from the machines and operators on your shop floor.
Sources
- Fitch, E., 2014. Proactive Maintenance For Mechanical Systems. Kent: Elsevier Science, pp.1-14, 287-298, 312-315
- Stamatis, D., 2010. The OEE Primer. Florence: Productivity Press, pp.2-3, 89, 226.
- Smith, A. and Hinchcliffe, G., 2004. RCM – A Gateway to World Class Maintenance. Amsterdam: Elsevier Butterworth-Heinemann, pp.3,16.