Production line efficiency isn’t just about output; it’s about agility, resilience, and staying ahead in a fast-moving market. Streamlined operations enable faster response to demand shifts, better resource utilization, and stronger ROI across the board. With new technologies making data more accessible than ever, manufacturers now have unprecedented opportunities to examine all aspects of production and identify improvement opportunities.
In this article, we’ll explore production line efficiency — not just for a single line, but as a general approach that can apply across different lines and facilities. This includes why it’s important, how to avoid common efficiency traps, how to calculate line efficiency, and five ways to improve it.
Understanding Production Line Efficiency
Before we explore how to improve production line efficiency, it’s important to understand what the term actually means.
Production line efficiency, the focus of this article, is about maximizing what you produce while minimizing the resources you consume. This means understanding how effectively a manufacturing line converts inputs (like time, labor, and materials) into desired outputs (finished products) with minimal waste and downtime.
Why Is Production Line Efficiency Important?
With rising costs, tighter margins, and increasing customer demands, manufacturers can’t afford inefficient operations. Improving efficiency helps manufacturers:
- Reduce operational costs by minimizing waste and idle time.
- Maximize output without increasing labor or equipment.
- Meet customer demand more reliably and on time.
- Increase profitability by doing more with existing resources.
- Maintain competitiveness in increasingly fast-paced markets.
Efficient lines also tend to be more predictable, scalable, and resilient, making them better prepared to handle production fluctuations or disruptions.
Avoiding Common Efficiency Traps
Improving efficiency isn’t always a win. You can create “efficiency traps” that hurt overall performance:
- Overproduction:
A line producing more than needed creates waste, not value. - Quality reduction:
Faster output is harmful if defect rates increase. - Operator burnout:
Unsustainable pace and insufficient training can lead to mistakes and turnover.
That’s why improving line efficiency must be based on real demand, quality goals, and broader production strategy.
To avoid these traps when monitoring your operations and identifying areas for improvement, you need to understand the difference between efficiency, productivity, and effectiveness. These terms are often used interchangeably, but they refer to distinct ideas.
Productivity measures output relative to all inputs.
Effectiveness is about achieving the right goals.
Efficiency is about maximizing output while minimizing resource consumption.
How to Calculate Production Line Efficiency
Production line efficiency can be measured in different ways. The formula below focuses on output efficiency – how effectively your line converts its maximum production capacity into actual results, which is the most relevant metric for the improvement strategies discussed in this article:
Efficiency (%) = (Actual Output / Maximum Possible Output) × 100
- Actual output:
The number of good units (products that meet quality standards) produced over a given time period. - Maximum possible output:
The highest number of good units that could be produced if the line ran at full capacity without any downtime, speed losses, or quality issues.
This efficiency calculation gives you the same basic metric as your OEE score. While efficiency offers a quick snapshot of performance, manufacturers often use OEE (Overall Equipment Effectiveness) for deeper insights into the causes of efficiency losses. We’ll explore OEE in more detail in the KPI section below.
Let’s take a look at an example. Suppose your production line can produce 1,000 units per shift at maximum capacity. However, due to minor stoppages and delays, it only produces 850 good units.
In this case: Efficiency = (850 / 1000) × 100 = 85%
This percentage shows how close your line is operating to its full potential. An efficiency below 100% reveals room for improvement due to downtime, speed losses, or quality issues.
💡 Tip: Efficiency should be tracked over time, alongside other KPIs to spot trends and prioritize improvements.
Now that you understand how to measure efficiency, let’s explore five proven strategies to improve it.
OEE Monitoring Solution
Monitor production in real time and obtain a true picture of what's happening on your shop floor. Free for 30 days.
5 Ways to Improve Production Line Efficiency
The following five strategies address the most common efficiency killers in manufacturing. Rather than generic advice, these methods focus on systematic approaches that deliver measurable results across different production environments.
1) Identify Bottlenecks

Bottlenecks are points in your production process that slow down or halt the flow of operations. They can occur anywhere along the line and are often the root cause of lost efficiency. Identifying and addressing them is crucial to improving overall performance. Some of the most common causes of bottlenecks include:
- Lack of raw materials
- Unplanned downtime
- Unavailable operators
- Poor maintenance
- Quality issues (scrap)
- Skill gaps among operators
Fortunately, there are multiple ways for you to identify bottlenecks:
- Operational data analysis:
Check through the data you have available, and look for tell-tale signs of bottlenecks, such as long wait times for materials, delayed movement between machines, missed delivery schedules, or backlogged work. - Visual inspection (Gemba walks):
Do a factory walk-through to observe processes firsthand, identify inefficiencies, and engage with operators in their actual work environment. - Value stream mapping (VSM):
VSM is a lean practice where you visually map out your entire production process, from raw materials to finished goods. This diagram identifies every step, the time each step takes, and the flow of materials and information. - Machine utilization:
This indicator is a ratio that measures the effective active time of a machine compared to the amount of time it should be working. - Operator feedback:
Your shop floor operators will know where slowdowns occur, and listening to their feedback can be invaluable when detecting bottlenecks. With Evocon, operator engagement is vital, as they can leave comments for every slowdown and stoppage, giving you the context you need.
2) Implement Lean Practices and Continuous Improvement
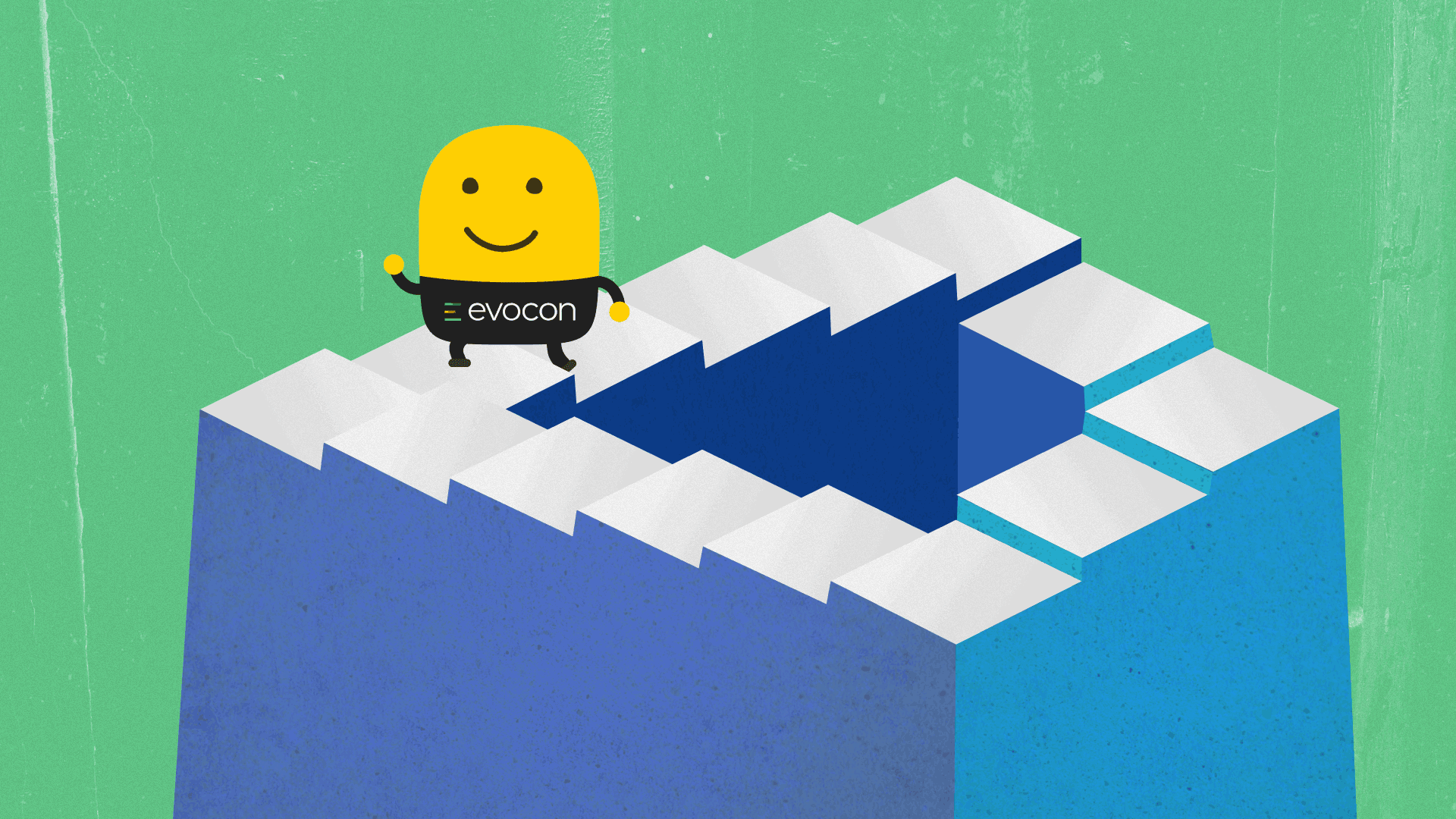
Lean continuous improvement is an umbrella term for the tools and philosophies in lean methodology that help manufacturers optimize production by making incremental improvements.
By minimizing the 8 wastes of Lean — including overproduction, waiting, motion, and defects — manufacturers can systematically identify inefficiencies and improve line performance.
In the context of improving production line efficiency, Lean methodologies can help boost efficiency, organize the workplace, and optimize workflows. Alongside Value Stream Mapping mentioned earlier, here are some of the most commonly used tools:
- 5S Methodology:
This foundational practice focuses on workplace organization — Sort, Set in Order, Shine, Standardize, and Sustain. A clean, well-organized factory reduces wasted motion, speeds up work, and makes inefficiencies easier to detect and correct. 5S helps to avoid operator burnout. - Kanban:
Kanban boards are one element of a visual factory that helps manage workflow, track inventory, and work-in-process (WIP). This helps maintain your quality standards as it prevents rushed work due to material shortages. - Six Sigma:
While distinct from Lean, Six Sigma is often combined with it to form “Lean Six Sigma.” Its methodology is more data-driven and designed to cut defects and ensure a high-quality end product. Six Sigma follows a five-step DMAIC process (Define, Measure, Analyze, Improve, and Control). - Just-In-Time (JIT) Production:
JIT aims to produce and deliver goods only when they are needed and in the exact quantities required, minimizing inventory and associated holding costs and waste. This “pull” system helps avoid overproduction, one of the major wastes that can lead to inefficiencies on the line.
💡 Tip: Don’t implement all tools simultaneously. Choose one, master it over 3-6 months, then add the next. Rushed lean implementations often fail because they overwhelm operators and create resistance to change.
3) Apply Technology and Automation

With the vast number of new tools and technologies available, there is a significant opportunity for you to improve production line efficiency, often without major investment. The key is choosing tools that reduce waste, maximize output, and enhance the precision and reliability of your operations.
- Robots and cobots:
Robots and collaborative robots (cobots) enhance line efficiency by automating repetitive, precise, or hazardous tasks. Traditional robots excel in high-volume, consistent operations, boosting speed and accuracy. Cobots, designed to work safely alongside humans, enable seamless collaboration. They allow humans to focus on complex tasks while robots handle strenuous or repetitive work.
Both significantly increase throughput, improve product quality through consistency, enhance workplace safety, and contribute to overall efficiency by optimizing labor and machine utilization. Additionally, many robots collect performance data, feeding into real-time monitoring systems.
- Sensors and the Industrial Internet of Things (IIoT):
Sensors are fundamental data collectors on a modern production line, gathering real-time data on machine status and part counts. The Industrial Internet of Things (IIoT) is the network that connects these sensors and other devices, allowing them to communicate and share this data. This continuous flow of information enables real-time monitoring of equipment performance, facilitates predictive maintenance, minimizes unplanned downtime, and enables faster, data-based decisions.
- Real-time data monitoring:
While advanced hardware like robots and sensors generate vast amounts of operational data, their real value is unlocked through real-time data monitoring and analytics.
Real-time data provides an immediate and accurate overview of your production line. Unlike historical or manually collected data, it gives us instant visibility into machine performance, production output, and potential issues as they unfold. This allows manufacturers to shift from reactive problem-solving to proactive optimization.

Using OEE software for real-time monitoring, manufacturers can:
- Pinpoint bottlenecks:
See precisely when and where slowdowns or stoppages occur. - Understand root causes:
Get detailed context, often through operator input and machine data, to determine why an issue happened. - Identify trends:
Detect recurring problems in performance that might otherwise go unnoticed. - Drive continuous improvement:
Use accurate, real-time data to measure the impact of initiatives, automation upgrades, or training programs, ensuring improvements are sustained. - Make data-driven decisions:
Replace guesswork with actionable insights, allowing for faster, more informed operational adjustments.
Real-time data is essential to improving line efficiency. It empowers teams to act on accurate, up-to-the-minute insights that help eliminate waste, reduce delays, and continuously optimize performance.
4) Employee Training and Operator Engagement

When it comes to improving line efficiency, there’s only so much you can achieve through automation or technology alone. Ultimately, it will come down to the skills, knowledge, understanding, and culture of your operators.
Operator engagement significantly impacts a factory’s day-to-day efficiency, making it essential to find different ways to engage production operators. One of the most impactful ways to boost operator engagement is through the tools they use. Clear, intuitive software that’s adaptable and easy to learn makes operators far more likely to adopt it for daily use.
Training is also essential. Without investing in your operators’ knowledge and education, they’re far less likely to be engaged in your operations, leading to multiple issues:
- Higher turnover:
More operators might leave jobs where they don’t feel valued or engaged. - Missed improvement opportunities:
You could be missing out on a “diamond in the rough”. By putting your operators through training programs, you encourage them to think outside the box. As the individuals closest to your production line, they often come up with fantastic ideas for optimizing and improving line efficiency.
To build engagement, you need to learn how to effectively communicate OEE to the shop floor.
With this knowledge, operators will understand the “why” behind their workflows, leading to greater engagement and more efficient production.
5) Utilizing Manufacturing KPIs
KPIs, or Key Performance Indicators, are measurable values that indicate how well a business is performing against its goals. While many industries use universal KPIs like profit margin, sales growth, or customer satisfaction, manufacturing requires a more specialized set of metrics focused on production efficiency, resource utilization, and output quality.
Manufacturing KPIs provide a data-driven view of production performance. They help managers by providing insights into where improvements can be made. Choosing the right KPIs ensures that your decisions are based on facts, not assumptions.
Note: The goal isn’t to track every KPI, but to focus on the few that have the biggest impact on your strategic objectives. You need to choose the right KPIs depending on your operational setup and goals.

One of the most impactful KPIs for improving production line efficiency is OEE (Overall Equipment Effectiveness). OEE is a widely used lean metric that measures how effectively a manufacturing process is running by capturing availability, performance, and quality in one number. It helps uncover the Six Big Losses in manufacturing, which are common causes of waste and inefficiency on the shop floor.
OEE is a central KPI because it directly influences productivity, downtime, cycle time, running costs, and more. As it impacts the entire company, OEE can effectively be used as a financial KPI.
You can use our OEE calculator to quickly and easily estimate your OEE, or check through our summary and examples of OEE formulas.
Case Study: At Tecpap, a company specializing in paper bag production in Morocco, shop floor operators use Evocon tablets to monitor machine performance in real time and capture information on losses. They also rely on the Factory Overview screen to track production and make necessary adjustments to processes.
They adopted Evocon to increase efficiency, reduce waste, and unlock their factories’ full potential.
Read the full case study >
Key Takeaways
Improving production line efficiency isn’t about a single fix; it’s about continuously identifying small, high-impact improvements across your operations. Start with your biggest constraints. Use data, operator feedback, and lean tools like Value Stream Mapping to identify bottlenecks and slowdowns that occur and understand why. Lean tools such as 5S, Kanban, and Just-In-Time production help you reduce waste, streamline processes, and maintain a cleaner, more organized factory.
Technology only gets you so far; your people make the difference. Robots, sensors, and IIoT devices reduce manual work and improve consistency. But the real value comes from monitoring and acting on real-time data. Provide operators with intuitive tools, ongoing training, and clear communication around your goals.
Finally, choose a few high-impact KPIs, like OEE, that reflect your efficiency goals. Use them to guide improvements, track progress, and align teams around shared performance metrics. Improving line efficiency is a continuous process, but it can become much more manageable and measurable with the right data, tools, and engagement.