Green Manufacturing is a framework that has evolved from the Lean methodology and helps manufacturers on their journey to sustainable operations. This article will help you better understand how the framework is applied in real life and how it can benefit you.
To learn more about the Green Manufacturing framework, visit the previous article “What Is Green Manufacturing, and Why Does It Matter?”. To shortly recap:
- manufacturers use the same principles and techniques to eliminate waste in both Lean and Green,
- the main difference is what is considered “waste,”
- in Green Manufacturing, waste is viewed from the environment’s perspective (instead of the customer’s).
What Are the 7 Green Wastes?
Below you’ll find explanations of all the 7 Green wastes and examples of how different manufacturers have taken steps to reduce them. Make sure to read till the end to see the step-by-step process of eliminating Green waste.
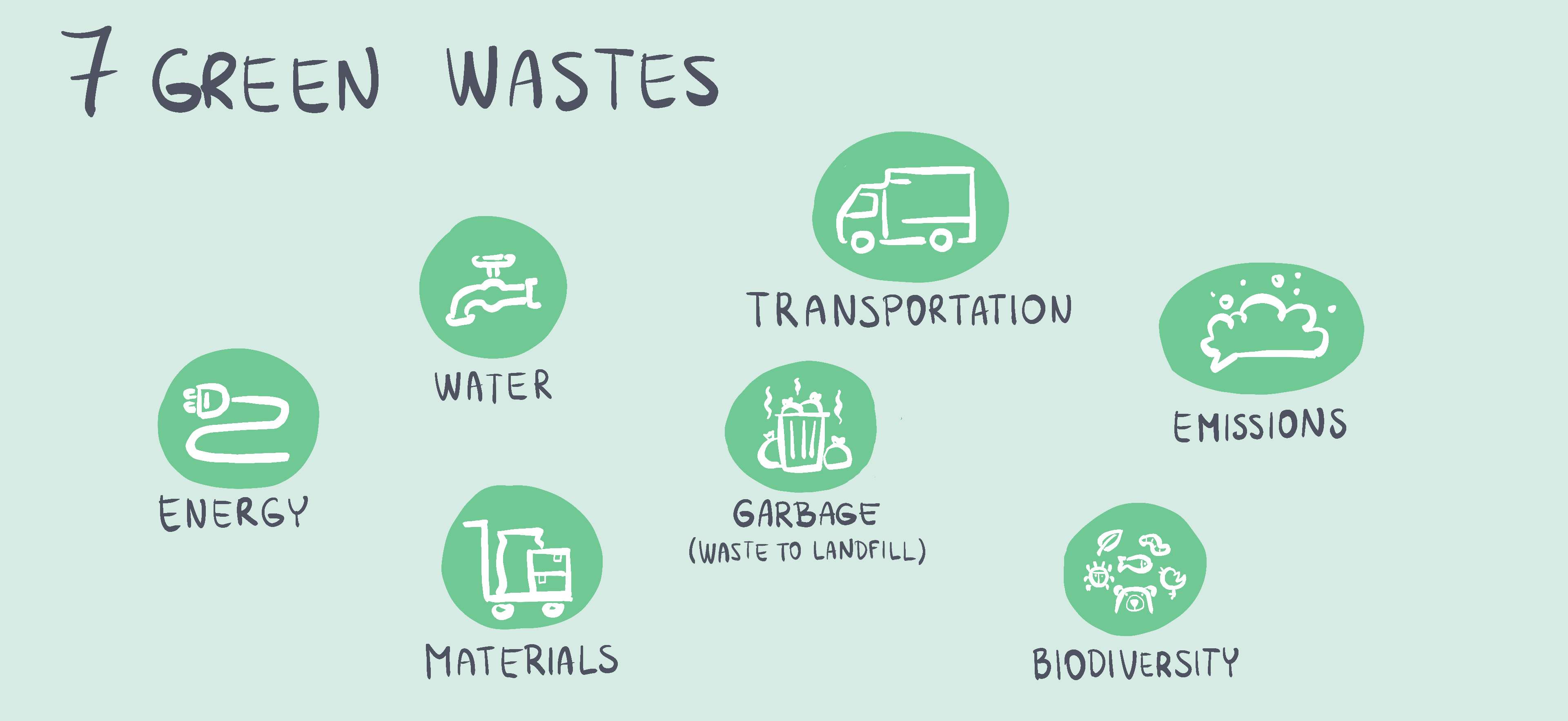
Energy
In this context, energy refers to electricity and fuels (such as natural gas) to power electrical and mechanical devices (e.g., machinery, electronics, heating, and cooling devices as well as ventilation systems).
The most common issues with the energy subject are:
- the wasteful overuse of energy;
- the source of energy (renewable vs. non-renewable);
- the fact that you have to buy the energy from someone else.
The end goal for any green manufacturer would be to have their own renewable energy power supply – from sun, wind, or biomass, for example. That’s the ultimate opportunity, and competitive advantage as that frees your company from harming the environment due to your energy needs and frees you from purchasing the energy from someone else. With the increasing energy cost and expected future increases, the direct cost savings can be significant.
We don’t have to look too far for good examples of success in this area. Our client Mid Cork Pallets uses biomass to produce 1.2 megawatts of green electricity each hour.
Water
Water, the second green waste, is essential for pretty much any company. However, manufacturers use and discharge a lot more of it than your average office building. Manufacturing industries that need a lot of water for product treatment include the garment and textile industry (for both growing cotton and dying process), industrial meat production, beverage industry (for both the water inside the drinks, but also for growing water-intense additive crops like sugar, coffee, fruit, etc), and automotive industry (for surface treatment and coating, paint spray booths, washing and rinsing, cooling and other processes).
The manufacturers have to pay for water twice – for the amount of fresh water they use from the municipality and then for the amount of water they discharge back into the system. That’s why when the price for water consumption or discharge is increased, manufacturers feel it the most.
On top of that, there is only so much water. Companies operating in water-scarce regions have to work on ensuring they will have access to it no matter what – to continue operations.
One of the leading cotton apparel manufacturers Bella+Canvas, for example, has prioritized water reduction projects for years. Now they’re saving 24 million gallons of water a week and use 7x less water than the average clothing manufacturer.
Materials
The current linear flow of materials in the manufacturing process has created two challenges, both of which are affecting manufacturer profits and sustainability – manufacturers constantly need new raw materials for production, and the product ends up in a landfill after its lifecycle.
More companies than ever before have proven – it doesn’t have to be this way. Creating a system for collecting products at the end of the lifecycle can provide valuable materials for your manufacturing plant and save a lot of money usually spent on extracting new materials. This concert of material reuse is well explained in a best-selling book globally, Cradle to Cradle by Bill McDonough and Michael Braungart.
This approach is increasingly common in the electronics industry, and we should mention HP as one of the best examples in the industry. They’re building products that are easy to repair to make them last for as long as possible, and by now, they’ve recycled 352 tonnes of supplies and hardware.
The end goal is to find ways to reuse materials and components of the product. And to achieve that, innovation at the design stage is necessary.
Using Evocon’s quality control software helps you reduce scrap and improve product quality, which contributes to eliminating Material waste and Garbage you need to have thrown out. For example, our client Chala has managed to reduce the potential scrap by 3x.
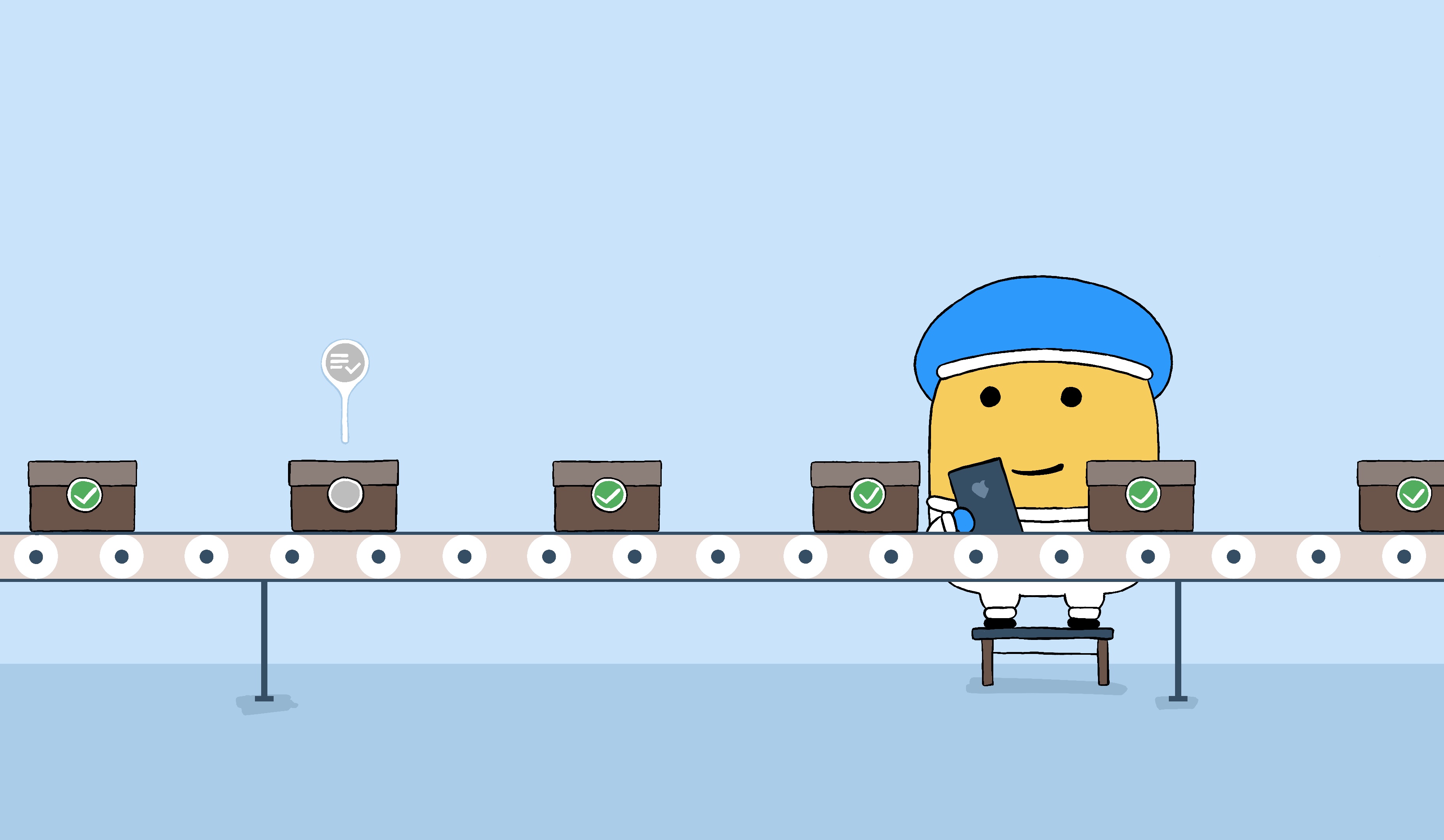
Start your sustainability journey
Get the data you need to reach your sustainability goals and remove waste. Free for 30 days.
Garbage
The environmental impact of garbage is well known. And so is the most common advice on eliminating it – reduce, reuse, recycle. But there is an aspect that’s rarely understood about this waste stream – the actual cost of throwing things away.
If you’re throwing out an item, you probably paid for it first, then you’re paying again to have someone take it away. In case the company is offsetting its emissions, it’s actually paying for it the third time as garbage contributes to the company’s GHG emissions.
Interestingly, a common thing companies discover is that the most expensive waste types in terms of cost of purchasing and disposal are also the ones to bring the most significant environmental benefit—for example, inks, paints, coatings, and oils.
For example, Subaru has been proving that zero-to-landfill manufacturing is possible for over 10 years already. As the Subaru team shares, the journey wasn’t easy as there is no one silver-bullet approach. What it takes are 1000 great ideas to get there.
Transportation
This green waste includes the transport of humans, materials, suppliers, and finished goods from one place to another. Its environmental impact is often overlooked, but in Europe alone, the transport sector represents almost a quarter of the greenhouse gas emissions and is the leading cause of air pollution in cities [Source].
The green waste stems from the fact that the current transportation system is inefficient and is run in a manner that is harmful to the environment. And as with other wastes discussed above, eliminating this one also offers cost savings.
The end goal here is to move toward 100% use of environmentally friendly modes of transport and offset what is unavoidable.
By this point, almost every company with a vehicle fleet works on reducing transportation. A good example here is a company whose whole business model is based on transporting people and items – Uber. They’re transitioning their vehicle fleet to electric vehicles (EVs) and offering alternative modes of transportation like scooters.
Emissions
We recently covered how many of our manufacturing clients are calculating their carbon footprint. To recap, many aspects contribute to the company’s total carbon footprint. The wastes mentioned above would be taken into account when calculating the company’s carbon footprint, but there are other impactful aspects to consider, for example:
- operations of an oven (baking often releases VOCs – volatile organic compounds);
- HVAC (heating, ventilation, air conditioning systems);
- emissions caused directly by your product (e.g., if your product is a car, the emissions the product generates once used and at the end of its lifecycle).
The benefit of working on eliminating this waste is twofold. It’s reducing the environmental impact of the business, but in many cases, it also helps to alleviate the financial burden of fines and fees.
The Knoll Group is a furniture manufacturer. Initially, they used spray paint that emits both VOCs and CFCs (Chlorofluorocarbons). When looking into their painting processes, they gathered that only 20% of the spray paint laid on the furniture, requiring extreme excess of material use and excess emissions. The company switched to powder-coating as 98% of the paint stuck to the furniture. Thanks to this change, Knoll group was saving $1 million a year from materials, energy, hazardous waste fees, compliance fees, and labor.
Biodiversity
This is the last, but not least important waste for Green Manufacturers to consider as it affects both the sustainability of a business and the nature it’s surrounded by. Biological diversity is the key to sustaining life on this planet. It’s encompassing all living species on earth and their relationship to each other. It’s how the trees, bees, plants, birds, and animals interact with each other, depend on each other and provide an ecosystem that can sustain life, generate oxygen, or clean water and soil.
Beyond environmental significance, biodiversity waste matters as companies have significant costs associated with clearing up trees or filling up a watershed to build a new building. The end goal here is to eliminate the destruction of biodiversity and regenerate what has already been taken.
L’Oreal, a global cosmetics brand, concluded that the lack of forest-related issue management could damage its brand value, putting more than $180 million (1% of operating expenses) at risk. Their current initiatives aim to avoid deforestation and restore marine and terrestrial ecosystems.
Steps to Eliminate Green Waste
Earlier in the article, we mentioned the end goal companies strive for in each Green Manufacturing waste area. It’s helpful to keep the end goal in mind when setting goals and throughout the journey. The general thinking and process are the same for reaching the end goal in all seven Green Wastes, so below, we’ve described it in a simplified 3-step process.
Step 1: Gather data on the current situation
By gathering data from your business, you can set a baseline. In the Energy waste context, you need to collect data on energy use and source for the whole factory and activity. In the Material waste context, you would identify the input/output of materials in each activity of the value stream. Sometimes this requires further information gathering, for example, the recyclability or material composition of materials or the type of waste.
Step 2: Increase efficiency, minimize consumption
This is a crucial step that will help you successfully reach the next steps as it ensures your operations are as lean and efficient as possible. In this step, you identify where the opportunities lie for minimizing the use of resources – e.g., switch to more efficient machinery to save energy or water, eliminate unnecessary packaging and reduce the creation of garbage. Often, this phase offers a fast (up to a year) payback period and cost savings after that.
Evocon helps reduce scrap in your production, which helps with both Material and Garbage waste. Manufacturers also use Evocon to gather data on electricity consumption (and its relation with OEE) which helps with Steps 1 & 2 of reducing Energy Waste.
Step 3: Invest in bettering your business
The last step in the process is to leap towards the end goal mentioned in each category. With the savings from Step 2, there’s at least part of the budget to invest in becoming a green manufacturer. The journey will look different for each aspect of the business and each business, but the end goal is the same – to become a truly green manufacturer.
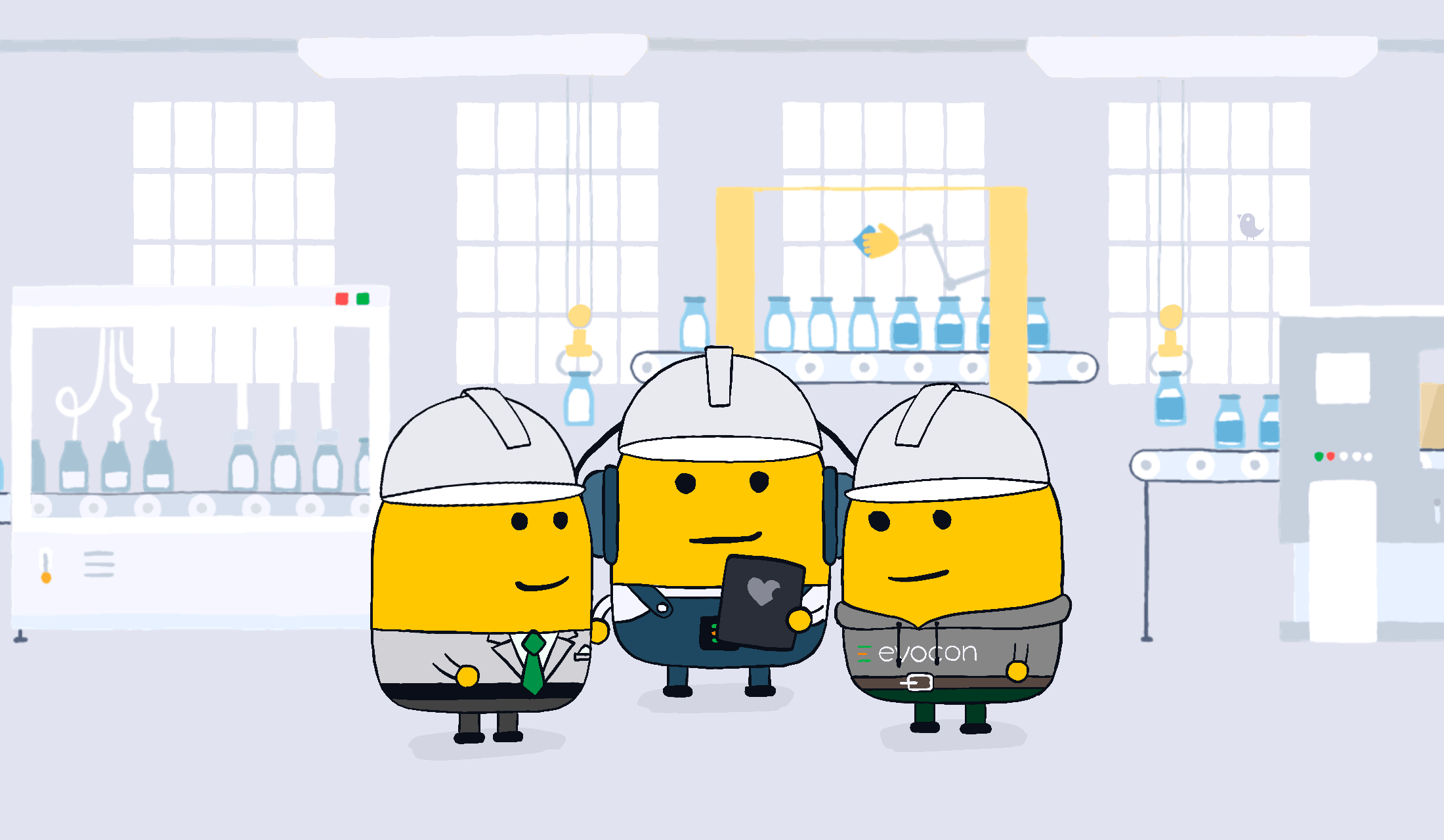
To Recap
Green Manufacturing is a framework that can come in handy in all aspects of your manufacturing process. It helps your company reduce its environmental impact and save money.
Here at Evocon, we’re helping manufacturing companies with the 1st and 2nd steps of the process. So far, our clients have found Evocon to be the most useful for combining OEE with real-time data on energy consumption and reducing material waste through improving OEE.
If you are ready to set out on this journey, visit our Green Manufacturing page to learn how we can help, or just reach out!