Machine monitoring (MM) is the application of IIoT concepts and technology to the unique challenges of the manufacturing sector, specifically to machines and shop floor production processes. This article serves as a general introduction to machine monitoring in manufacturing and in the context of OEE and improving productivity.
Origins of Machine Monitoring
The first known instance of machine monitoring was in 1991 when researchers at CERN (birthplace of the internet) connected a video feed of their coffee pot to their network. Why did they need to monitor a coffee pot?
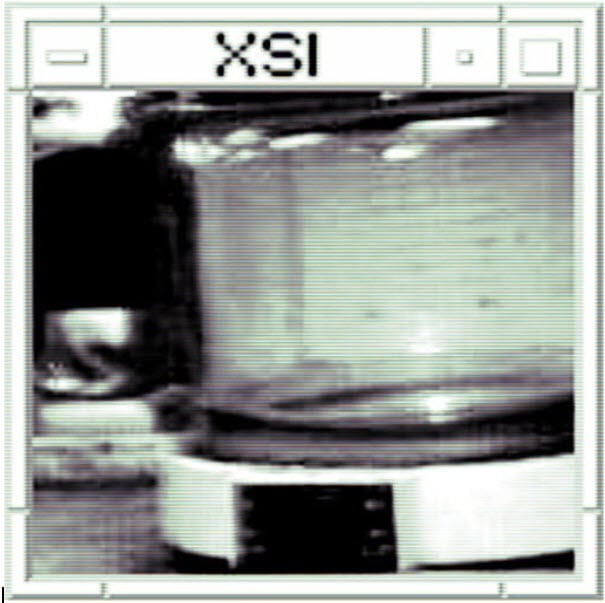
As it turns out, the engineers all required multiple cups of coffee each day, but they had a problem – their offices were a 5-10 minute walk to the coffee pot. Because several trips were made each day with an average roundtrip walk time of 7-12 minutes, the amount of time spent getting coffee was interfering with their work. Worse, often they arrived to find an empty pot of coffee. Then they had to wait to make a fresh pot.
So engineers did what engineers do in these situations, design a solution that will allow them to minimize the amount of time spent getting coffee. With a live visual of the coffee pot on everyone’s browser, they timed their trips to the break room so that they arrived at the moment the first cup would pour, and then they hurried back to work.
From this humble beginning, though, the practice grew slowly at first, then accelerated recently in connection with the introduction of the IIoT.
Today, there are many flavors of machine monitoring in use, from electric grid power stations to offshore oil wells and much more. For our purposes, though, we are going to focus on the monitoring of machines used in manufacturing.
What is Machine Monitoring?
A simple concept
Within the context of manufacturing, machine monitoring is fundamentally a simple idea.
- Collect data from machines.
- Transfer collected data to the internet.
- Monitor and analyze collected machine data.
Now that we understand what machine monitoring is, let’s look at the different types of data that manufacturers are typically interested in tracking from their machines.
Common production data to monitor
Data collected through a machine monitoring system is usually highly specific. Let’s look at a few examples of common source data that a single machine can, in theory, generate and one, several, or all, of the following.
- Machine status – On/off, run rate, speed
- Downtime & Utilization – Planned/unplanned stops
- Quality – Right part first time (RPFT), scrap rate
- Operator effectiveness – Labour productivity and efficiency
- Environmental data – Humidity, vibration, temperature
- Energy – Electricity use
If you are looking to learn about the bigger picture of production monitoring as a whole, you will find this chapter about the full scope of production monitoring useful. Otherwise, let’s move on.
Definition of machine monitoring in manufacturing
Now that we have established some context, let’s settle on a formal definition of machine monitoring. For the purpose of this article, we at Evocon define it as follows:
Machine monitoring is any means of connecting machine data feeds to the internet that enables real-time production monitoring and advanced analytics of production data.
A best practice of manufactures is to analyze production data to identify areas for improvement.
How to Get Started With Machine Monitoring?
This section will discuss how you can get started with machine monitoring, specifically what hardware you need in the context of Evocon. Please note that while we will be using specific hardware, most modern solutions are quite similar, so what you learn is generalized. So it can be applied even if you do not ultimately become an Evoncon client.
1) Hardware option
First, you need our IIoT device (or if you are considering another provider, then usually, each will have their own). The device collects production data from your process and transfers data to the cloud.
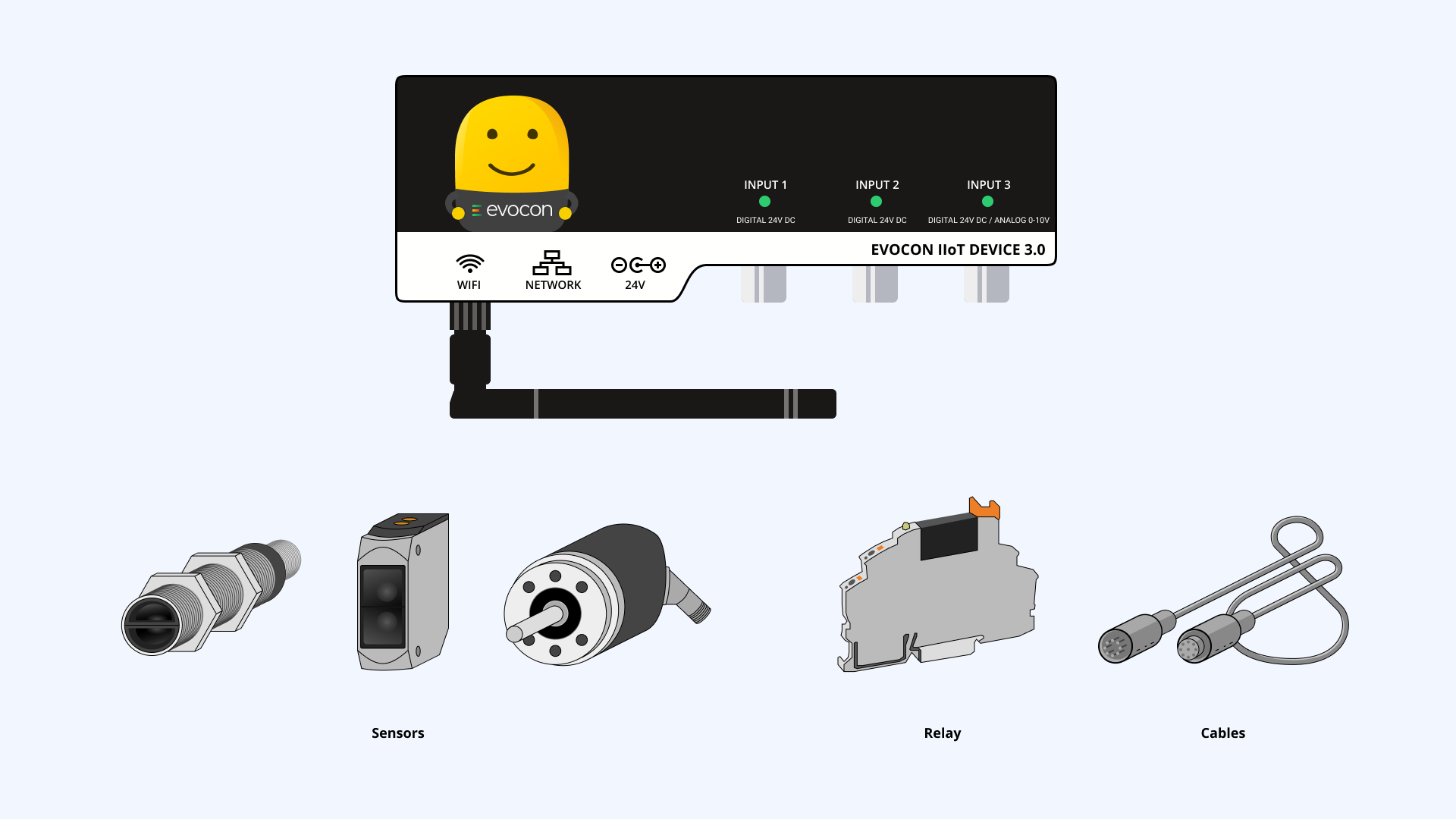
Secondly, you need hardware that enables you to get the signals you want from your machines into the device. The options here vary depending on the process you have, but generally, this includes sensors or relays and cable to connect everything. Finally, you need a tablet or computer to monitor and analyze the collected production data.
Manufacturers who have many types of older, analogue machines will most likely use this method.
Learn more: What Hardware You Need and Does Evocon Provide It?
2) Hardware-free option
Many newer machines come configured to capture production data and store it in a local database. If you know this to be true about your machines, then all you need to do is connect the database containing your production data to our software via HTTPS requests.
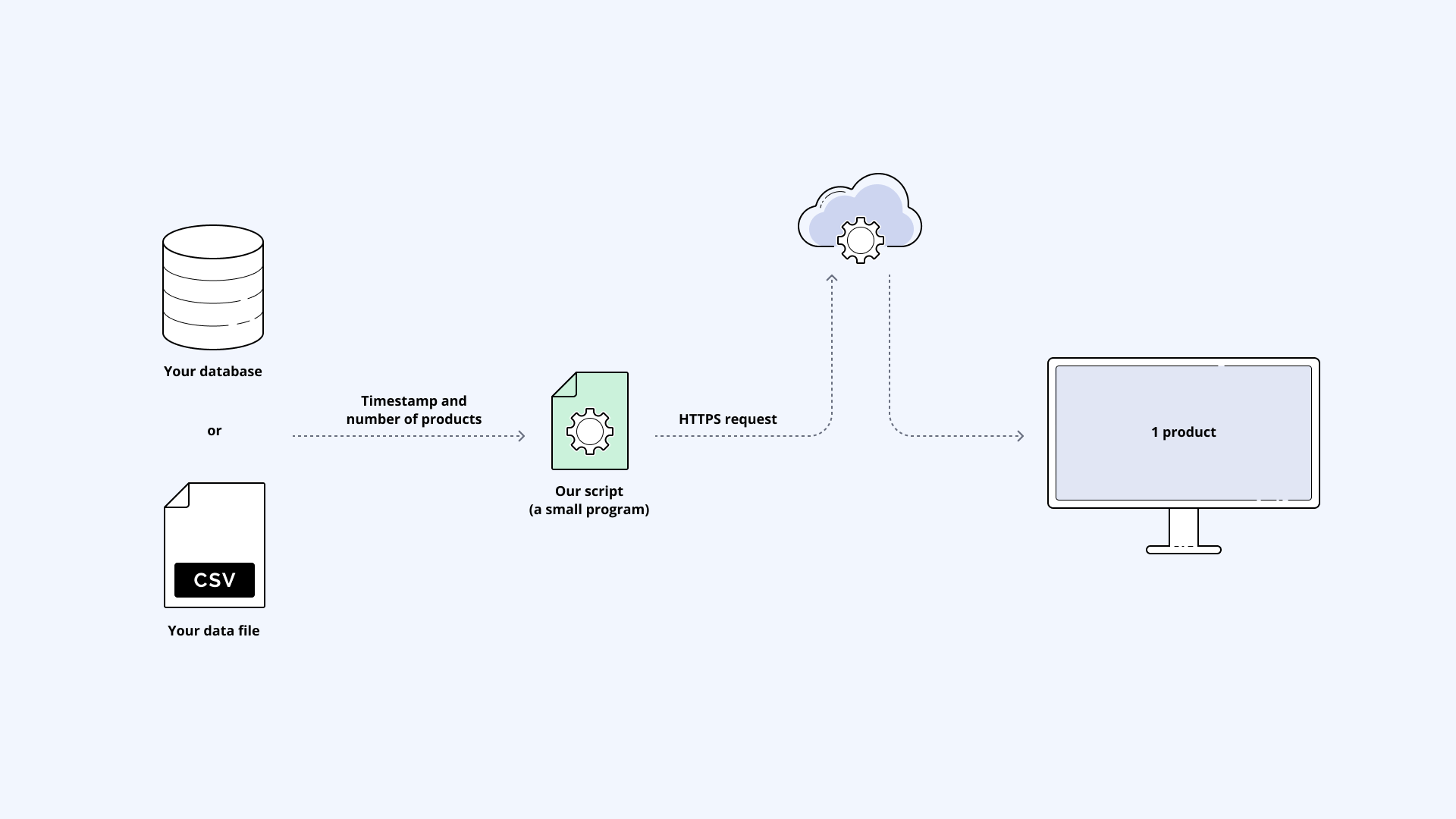
This is an excellent option for manufacturers who know that they have a lot of information about their products but have no easy way of making it visual and actionable. So if you have IT resources at your disposal, this is worth looking into. You can also get in touch with our team to learn more about this and how we can help.
Learn more: Evocon as a Hardware-Free Solution to Monitor Production
Five Advantages of Machine Monitoring
Machine monitoring converts routine manufacturing data into real-time insights and benefits. This section delves deeper into the advantages that manufacturers should aim to realize by implementing machine monitoring.
☝️ We also have another article where you can learn about the benefits of production monitoring from strategic and tactical perspectives.
Automated data collection
Manufacturers have long been interested in machine-level data. The problem was that there was just no easy way to capture it. Most plants used a manual collection of data using pen and paper. Larger firms hired a system integrator to build custom programs. These byzantine systems collected and transformed the wide variety of unstructured machine PLC data in the factory, but this was far too expensive for most.
By automating data collection, manufacturers save time and gain real-time insights into every step of the production process. Automated data collection is arguably the critical benefit of machine monitoring. This is true because data has quickly become the foundation of success in manufacturing. Moreover, without data automation, the other benefits listed below would not be possible.
Automate Your Production Data Collection
Enhance data accuracy and reliability to discover the true potential of your factory. Free for 30 days.
The first step in manufacturing digitalization
Manufacturing digitalization is the process of bringing analogue production processes into the digital era. Machine monitoring is one of the first steps manufacturers usually take in this process. This is because it enables them to build out subsequent digital initiatives.
For example, you could consider adding a machine learning solution to further leverage the production process data you collect. You could also implement an OEE dashboard which we discuss in the next section, or create a digital twin of your factory.
The main takeaway is that machine monitoring forms the core capability of manufacturing digitalization. With this capability in place, manufacturers positioned themselves to adopt several emerging smart factory initiates.
Simple OEE dashboard
While exact numbers are hard to come by, it is probably safe to assume that well over half of all manufacturing plants in operation today utilize OEE in some form. A clear conclusion we can infer is that manufacturers understand the importance of OEE to their factories. They have used OEE for years, even though it required a paper-based data collection process.
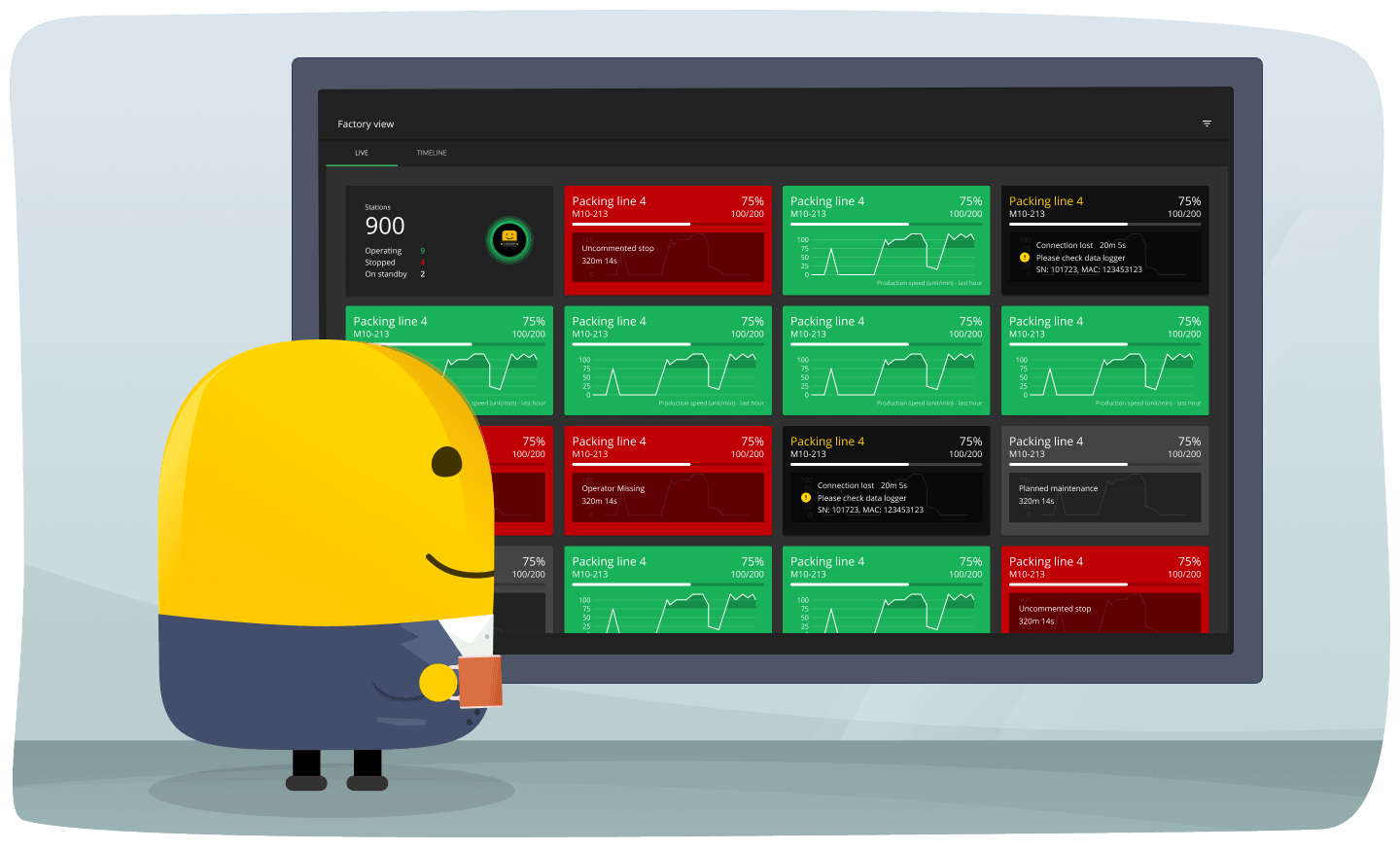
Think about that for a second. A manual collection process is labor-intensive and often has issues with data accuracy. But, because OEE is so useful to manufacturers, they prefer this problematic process with its imperfect measurement of OEE, as compared to having no OEE measurement at all.
The critical point to remember is that machine monitoring gives you reliable and actionable machine-level data. Further, machine monitoring enables live OEE data that you can use to improve productivity and reduce costs.
Production visualization
Production visualization in real-time is another game-changing benefit of MM. Your shop floor operators and supervisors will never remember how they managed before production visualization. Many on the shop floor will, for the first time, be able to see how they are doing against the plan before the shift ends. This will not only improve operator engagement but also has the power to change how you manage your manufacturing operation fundamentally.
If you want to learn more about how to use production digitalization to drive manufacturing improvement, check out our case study on TMI Automotive.
Additionally, the visual approach can go beyond just production visualization, offering simple and powerful tools to improve the overall performance of a factory – check out our comprehensive guide to visual factories.
Enhance shop floor communication
Through years of working with hundreds of manufacturers across the globe, Evocon has found that proper shop floor communication is a common trait of successful operations. By improving visibility into your production process with machine monitoring, manufacturers also create a catalyst for increased awareness and engagement by everyone on the shop floor.
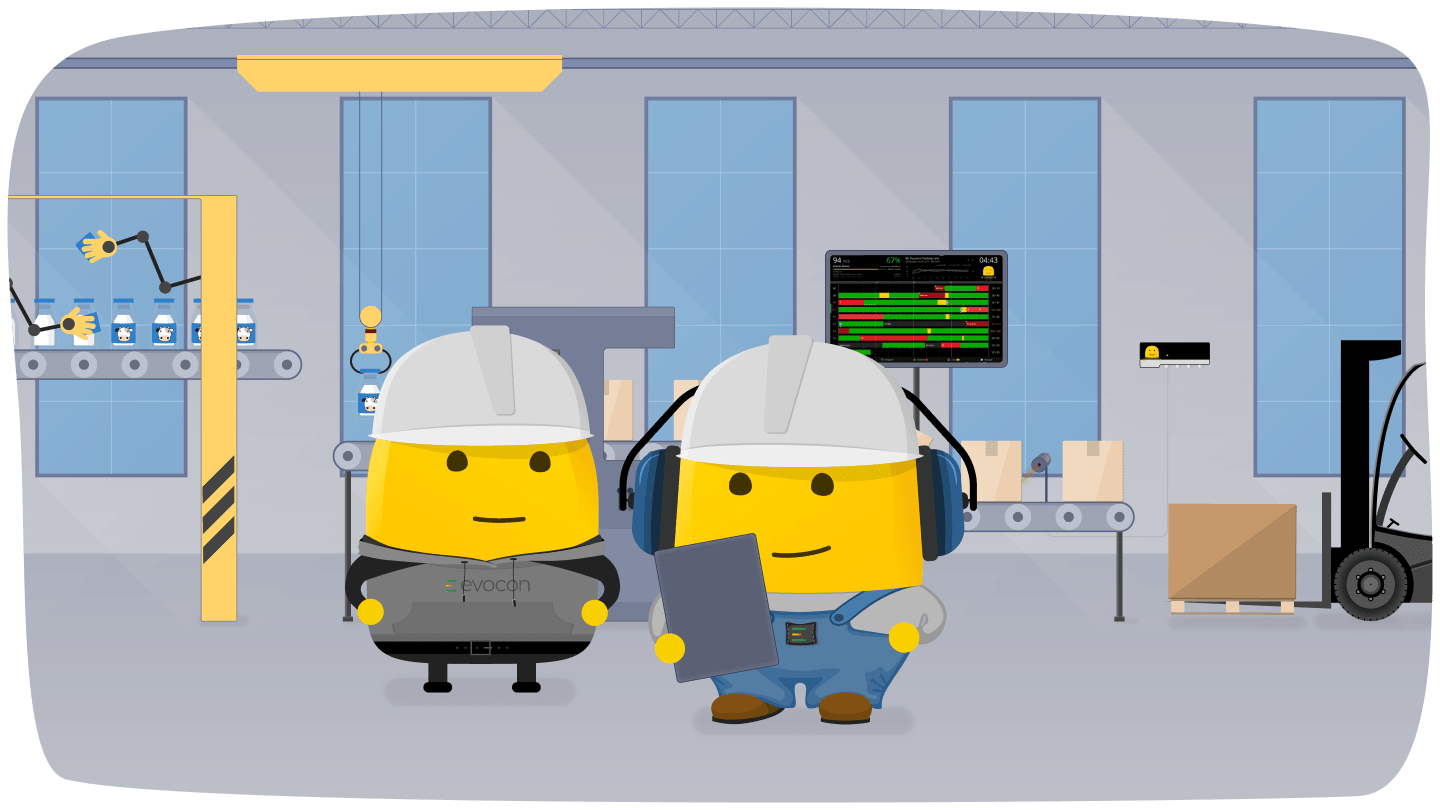
Indeed, machine monitoring provides manufacturers with an opportunity to connect individual actions on the shop floor with broader performance and process outcomes. When communicated correctly, this connection can influence your operations team to ever-higher levels of engagement and productivity.
Next Steps
In this article, we have introduced the fundamental ideas of machine monitoring. First, we looked at common machine data monitored by manufacturers. Then, we explored some of the most important advantages that a machine monitoring solution can provide.
We hope you now have a better understanding of machine monitoring. If so, perhaps you are ready to take the first step to improve your production with manufacturing digitalization. If so, we suggest starting with our free trial. As always, if you have any questions, feel free to reach out to our team.