IMMA Holding SA, a Moroccan company, oversees three key subsidiaries: Tecpap, a company specializing in paper bag production; Ajdir, a producer of pharmaceutical packaging; and Dimyal, which produces high-quality notebooks specialized for education. Over the past year, each of these companies has implemented Evocon to increase efficiency, reduce waste, and understand the true potential of their factories.
In this article, we explore how these companies have used Evocon to address operational challenges and enhance their overall performance. Mohamad Azdar, Group Industrial Director at IMMA Holding SA; Ismail Mechiche Alami, Director General at Ajdir; and Mohammed Mouni, Evocon partner and founder of Beyond 4.0, shared valuable insights into the companies’ journeys with Evocon and the transformative impact it has had on their operations.
Addressing Operational Challenges with Evocon
To improve efficiency across its subsidiaries – Tecpap, Ajdir, and Dimyal – IMMA Holding sought a solution to optimize production processes company-wide. Three key areas were identified where Evocon could drive significant improvements:
- Real-time visibility into production metrics
To fully understand their factories’ potential and monitor machine performance, IMMA Holding required precise, real-time data. This information was essential not only for assessing current production efficiency but also for understanding overall capacity, guiding future expansion decisions, and identifying new business opportunities. - Reducing waste and enhancing sustainability
They needed to better understand how efficiently their machines ran and how they could reduce scrap. With a strong focus on improving sustainability, the goal was to trace the origins of scrap and address issues at every stage of the production process. - Increasing production capacity and boosting operator engagement
Assessing potential capacity and increasing output required a shift in factory workers’ behavior, presenting a new challenge. Implementing a system that was both easy to use and clearly demonstrated its benefits to shop floor operators was crucial to driving this change.
Implementing Evocon across Tecpap, Ajdir, and Dimyal
Tecpap
Mohammed Azdar, Group Industrial Director at IMMA Holding SA, had previously worked with Evocon at Lesieur Cristal in Morocco. Recognizing the potential benefits and positive impact it could bring, he implemented Evocon at Tecpap just two days after joining the company. His past experience had shown that Evocon was the optimal choice, particularly due to its ease of use and accurate real-time information.
Tecpap, found Evocon instrumental in optimizing their processes. With multiple machines requiring close monitoring — from raw material preparation to printing, folding, and gluing — Evocon provided the precise data needed to enhance efficiency.
As a result of this successful implementation, Tecpap became the first of IMMA’s companies to introduce Evocon, setting the stage for its subsequent adoption at Ajdir and Dimyal.
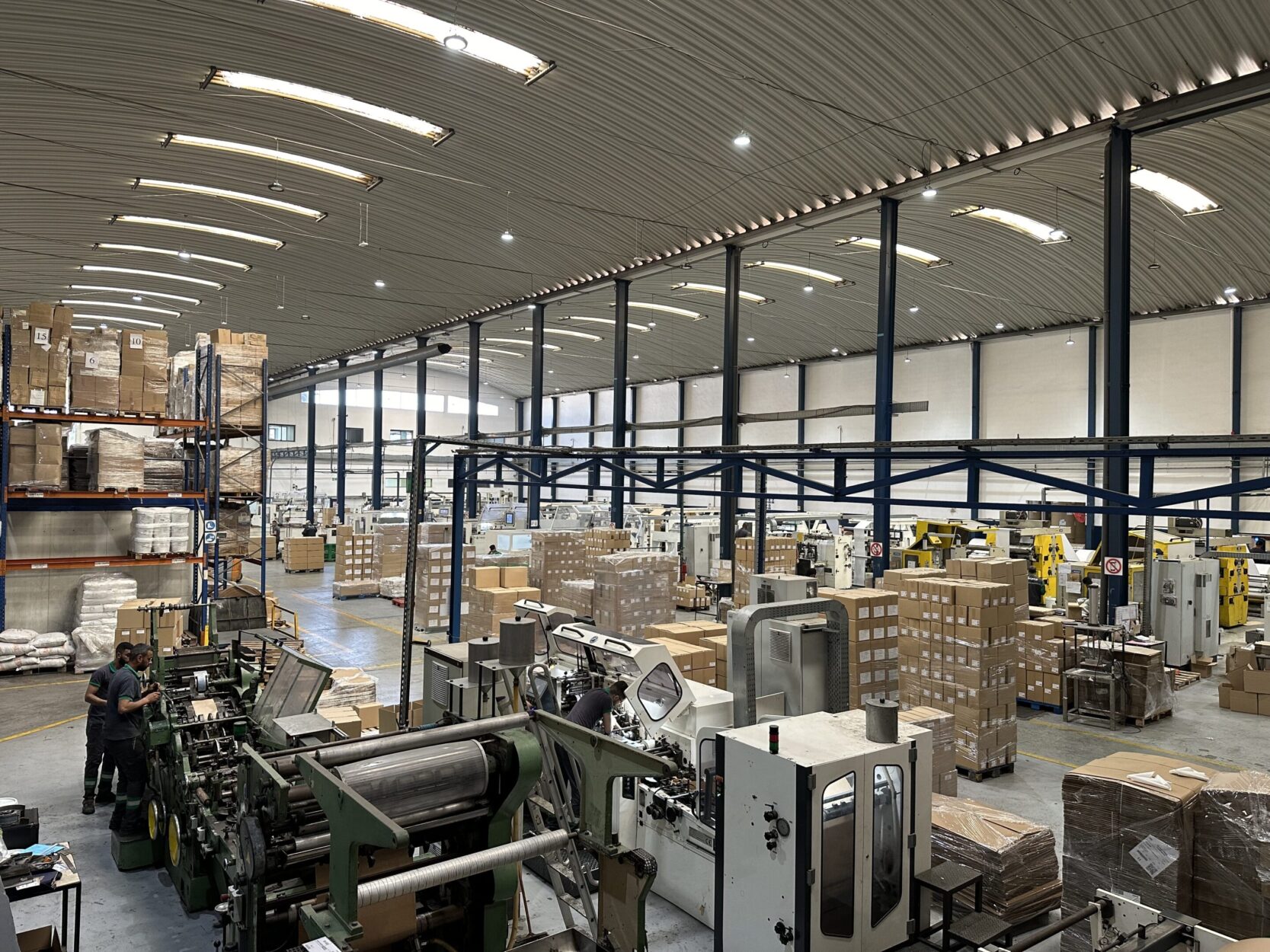
Ajdir
Ajdir, a producer of pharmaceutical packaging, followed Tecpap’s lead by implementing Evocon on a trial basis on a single production line. The success of this trial led to its rapid expansion to seven lines within just two months.
Ismail Mechiche Alami, Director General at Ajdir, recognized that Evocon could be essential not only for improving production metrics and resource management but also for future expansion planning. He is now using data from Evocon to accurately determine the factory’s true capacity to support his growth initiatives.
He further plans to use this information to secure extra funding and initiate the expansion into new markets, ultimately driving more business for Ajdir.
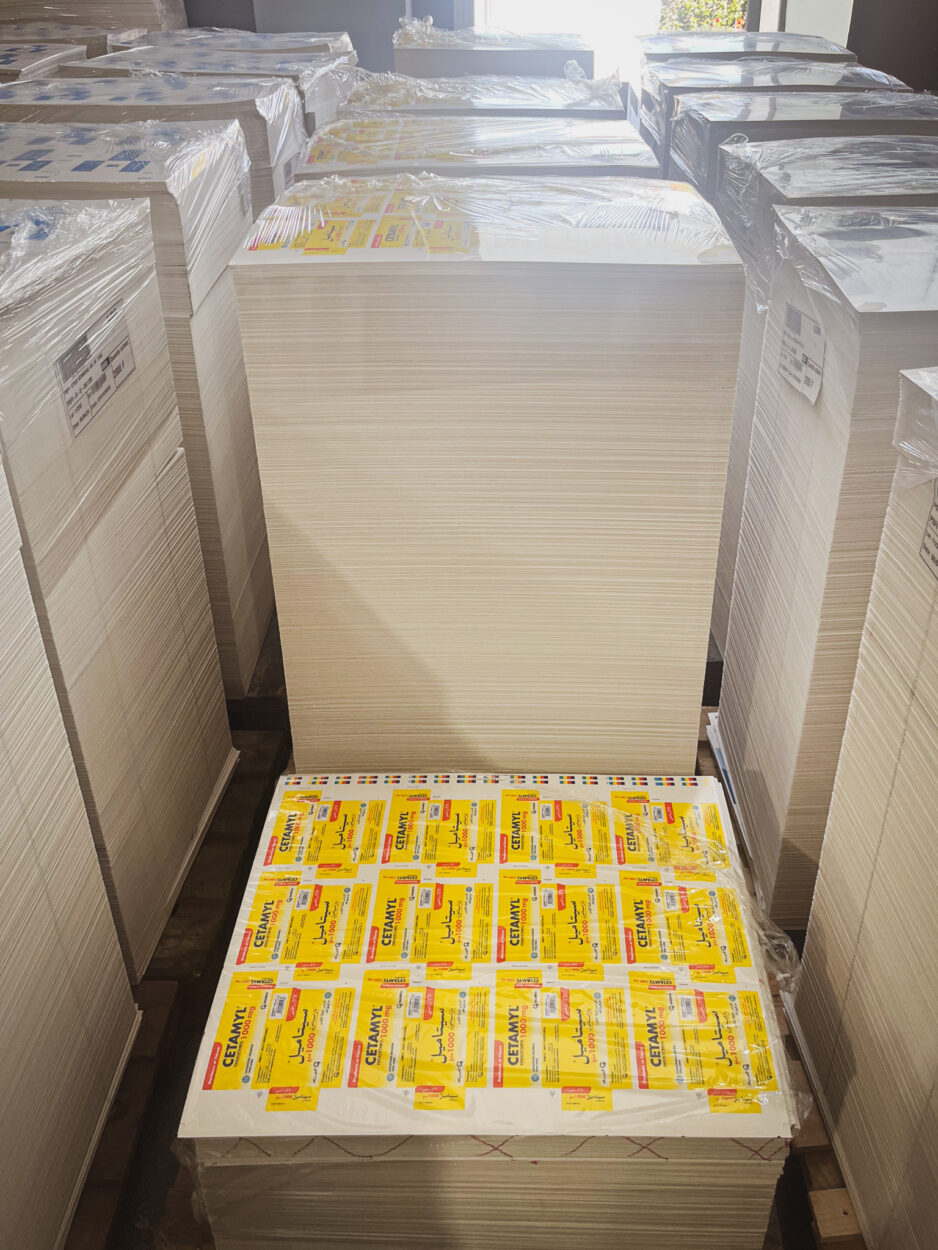
Dimyal
Dimyal, the newest addition to IMMA Holding, was founded in 2021 to produce school notebooks. Before adopting Evocon, Dimyal’s team visited Tecpap’s factory and was impressed with how effectively operators engaged with the system.
Although still in the early stages of implementing Evocon, the company has quickly recognized its value, thanks to real-time, accurate data which they are now using to improve their processes.
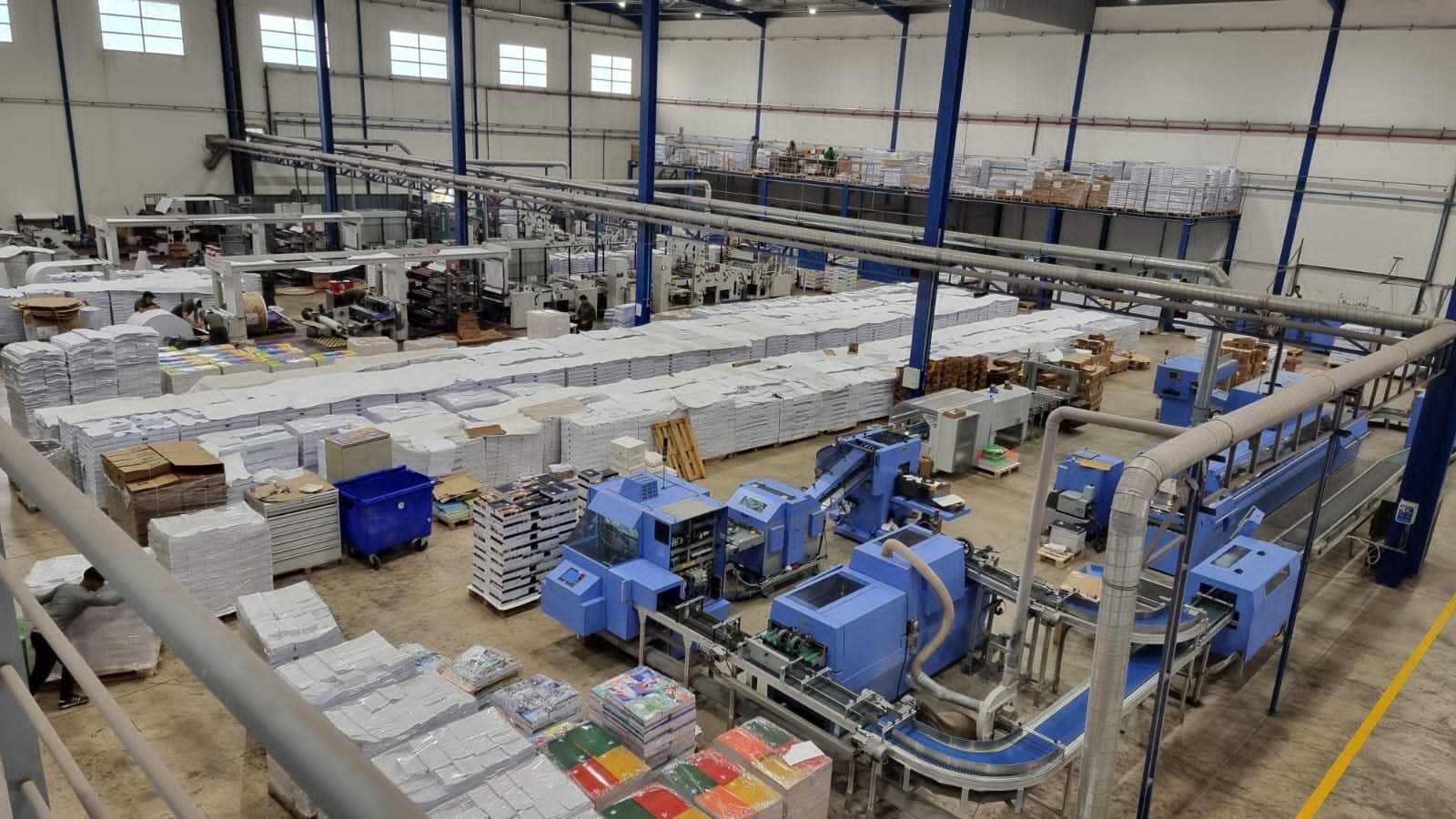
Overcoming Implementation Challenges
Tecpap
One of the major challenges at Tecpap was accurately monitoring scrap. Evocon, positioned at the end of the production line, only recorded scrap that reached that stage. However, scrap generated earlier in the process, before reaching Evocon’s sensors, was not captured, leading to discrepancies between the data from Evocon and the ERP system. The ERP system, which tracks raw materials entering the production line and finished products exiting, reflected higher scrap levels than what Evocon registered. Additionally, scrap generated during machine setup was included in the OEE calculation, resulting in a lower OEE score.
To address this challenge, Tecpap implemented Evocon’s Checklist feature as a data collection system to capture scrap occurring earlier in the process. This solution allowed them to identify precisely where and how much scrap was being generated at different stages of production. With this approach, they gained clearer insights into scrap rates at each process point, ensuring a more accurate and comprehensive understanding of overall production efficiency.
The collected data is also transferred to Power BI for further analysis, enabling Tecpap to make more informed decisions and continuously optimize their production processes.
Ajdir
Ajdir initially faced resistance from operators unfamiliar with the OEE concept and unsure of how Evocon would benefit them. To successfully implement the system, the company provided training and worked to shift the operators’ mindset. Over time, as operators became more comfortable with the system, they began to recognize its benefits, particularly in showcasing their performance and justifying bonuses.
“Evocon is not there to pressure operators to work faster or increase output at any cost. Instead, it’s there to help them become more efficient, increase productivity, and succeed together.” – (Ismail)
By linking Evocon’s results to their bonus system, Ajdir has significantly improved operator engagement. This incentive encourages operators to actively use Evocon, leading to more accurate data and greater overall efficiency, as we’ve observed with many other Evocon users. For example, read how Toftan created a bonus system around OEE.
Dimyal
As the most recent adopter of Evocon, Dimyal is still navigating the initial challenges of integrating the system into its operations. The key challenge lies in ensuring that the system is used effectively to monitor production and improve efficiency, with a focus on sustainability in their production processes.
However, with the experience of Tecpap and Adjir to rely on, they are in a good position to succeed in their implementation.
Daily Use of Evocon
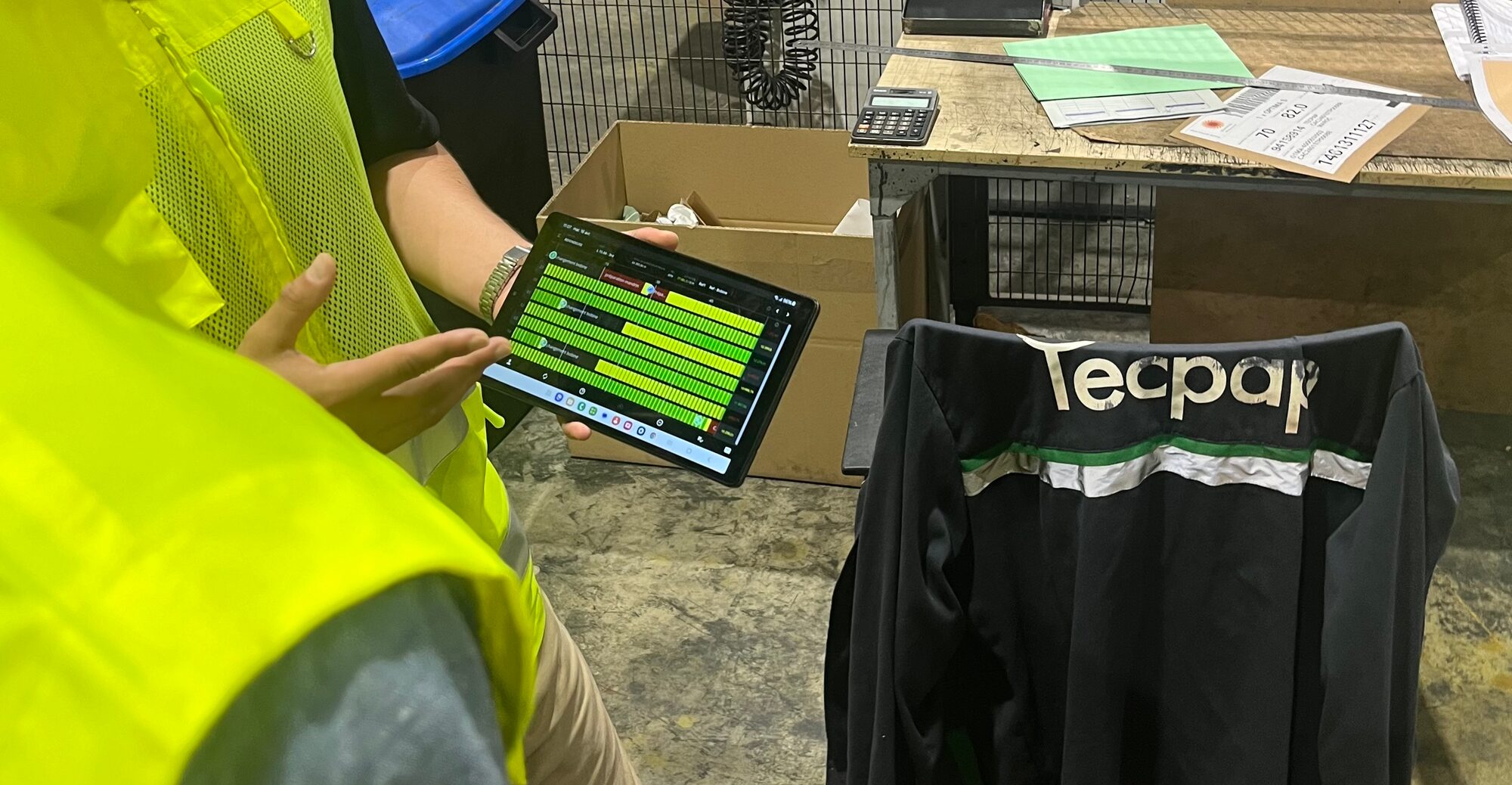
Management Usage
Management across all three companies rely on Evocon to monitor production metrics, allocate resources, and make informed decisions. But the extent to which they can do this is influenced by how far along they are in their production monitoring journey.
Nevertheless, OEE serves as the primary KPI across the board, making Evocon’s data crucial for their operational processes. This focus allows management to effectively track production efficiency, identify bottlenecks, and drive continuous improvement.
As Tecpap has been using Evocon the longest, we’ll provide a few specific examples of how they use Evocon data to make better decisions.
One of Tecpap’s focus areas is the actual production rate, with special emphasis on optimizing machine speeds. In the past, there was a lack of clarity in interpreting production data. Although production targets were met, it was unclear whether these results were truly optimal or just sufficient. Now, with accurate data to rely on, management has a much better view of their actual capabilities.
Evocon also plays a vital role in batch tracking. For example, the planning team relies on the system to determine the time needed to complete batches, such as preparing 14 pallets for shipment to a customer. The system provides visibility into how many pallets are ready, helping to schedule shipments accordingly. Furthermore, batch costs are now calculated with greater precision. By integrating production data from Evocon with existing cost information, such as operator hourly rates, Tecpap can now gain a more comprehensive understanding of their overall production costs.
Another way Tecpap leverages Evocon is by utilizing the Dashboard in daily meetings to compare the OEE of similar machines and analyze current day performance. Monthly meetings involve detailed discussions based on Evocon data, including OEE, scrap rates, and production outputs. They also integrate this data with Power BI for more custom visualization and reporting.
Evocon Usage on the Floor
On the shop floor, operators use Evocon on tablets to monitor machine performance in real time and capture information on losses. Tecpap’s operators also rely on the Factory Overview screen to track production and make necessary adjustments to processes. While Ajdir and Dimyal are still in the early stages of adopting these practices, they have already set up screens for operators to monitor the Factory Overview.
After overcoming the issues of trust and understanding why Evocon was needed, the operators have adjusted to using Evocon in their daily operations, and they now see the system’s benefits.
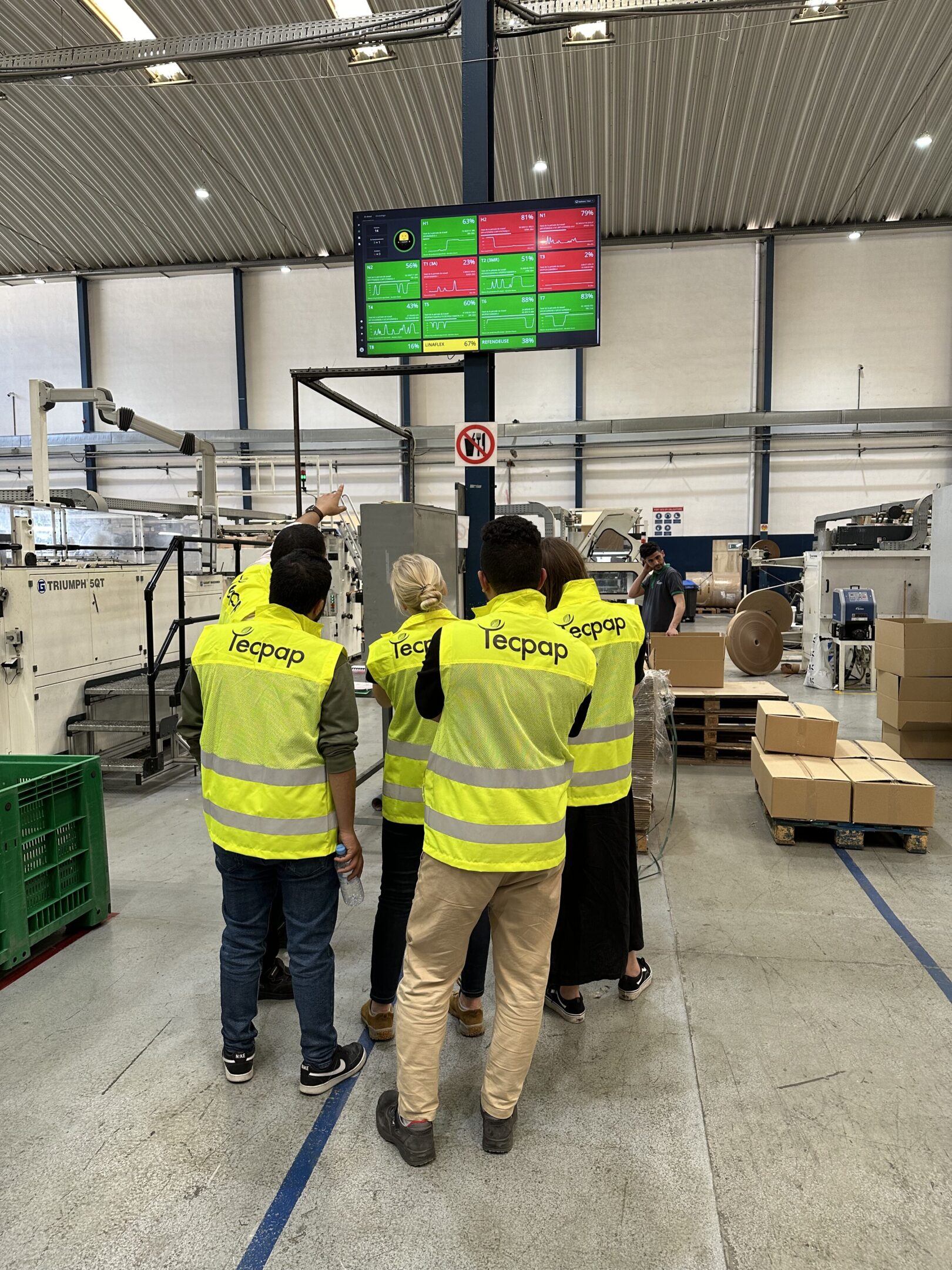
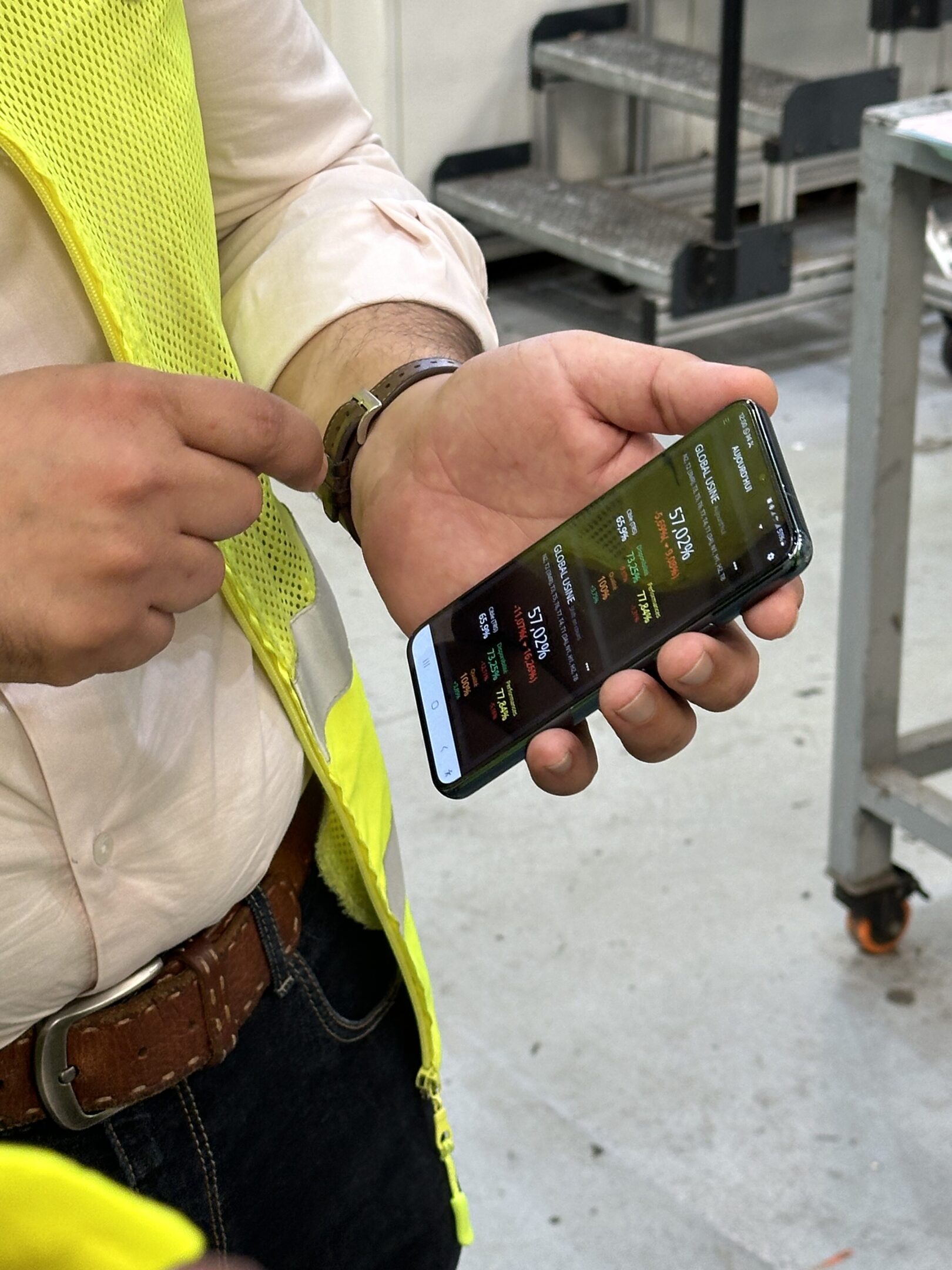
The Tecpap team has grown particularly fond of Mr. Evocon, playfully referring to him as the factory’s referee and even nicknaming him “VAR.” This lighthearted approach has helped keep operators engaged, increasing their use of Evocon and improving overall efficiency.
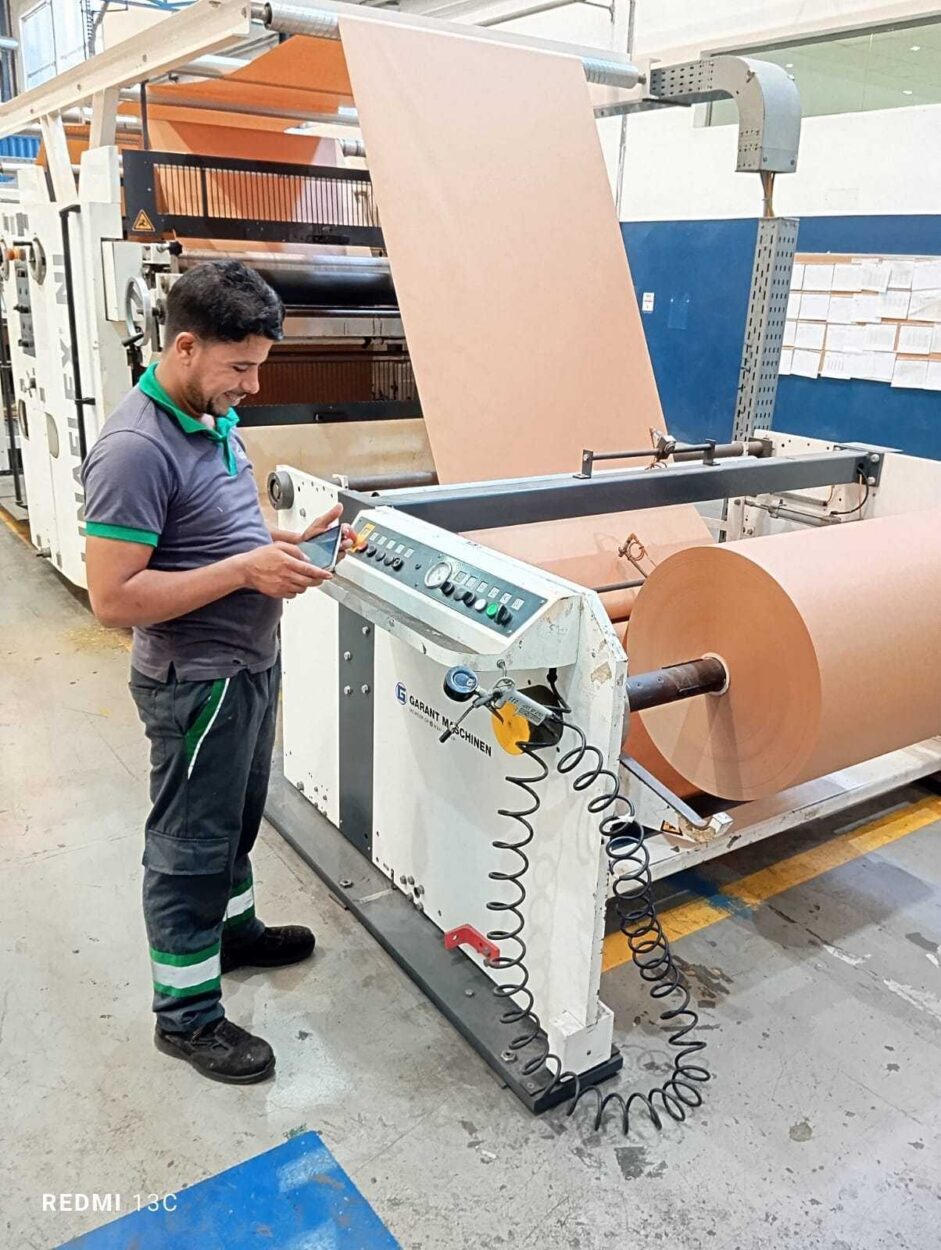
Checklists and the Removal of Paper
Checklists play a crucial role in Evocon’s functionality across all three companies, helping to digitize traditionally paper-based processes like recording product lifecycle information. This shift saves significant time and resources. At Dimyal, it took just one month to adopt Checklists, allowing them to achieve greater accuracy while also reducing their reliance on paper.
Impact of Evocon: Key Statistics and Insights
For all three companies, OEE is the main manufacturing KPI. Through the use of Evocon, they have made improvements across the board, with increased availability, performance, and quality.
Tecpap
When we look at Tecpap’s OEE score, we observe a 20% increase (+12% in absolute terms) from August 2023 to July 2024, with their OEE rising from 59% to 71%. They are determined to continue improving this figure.
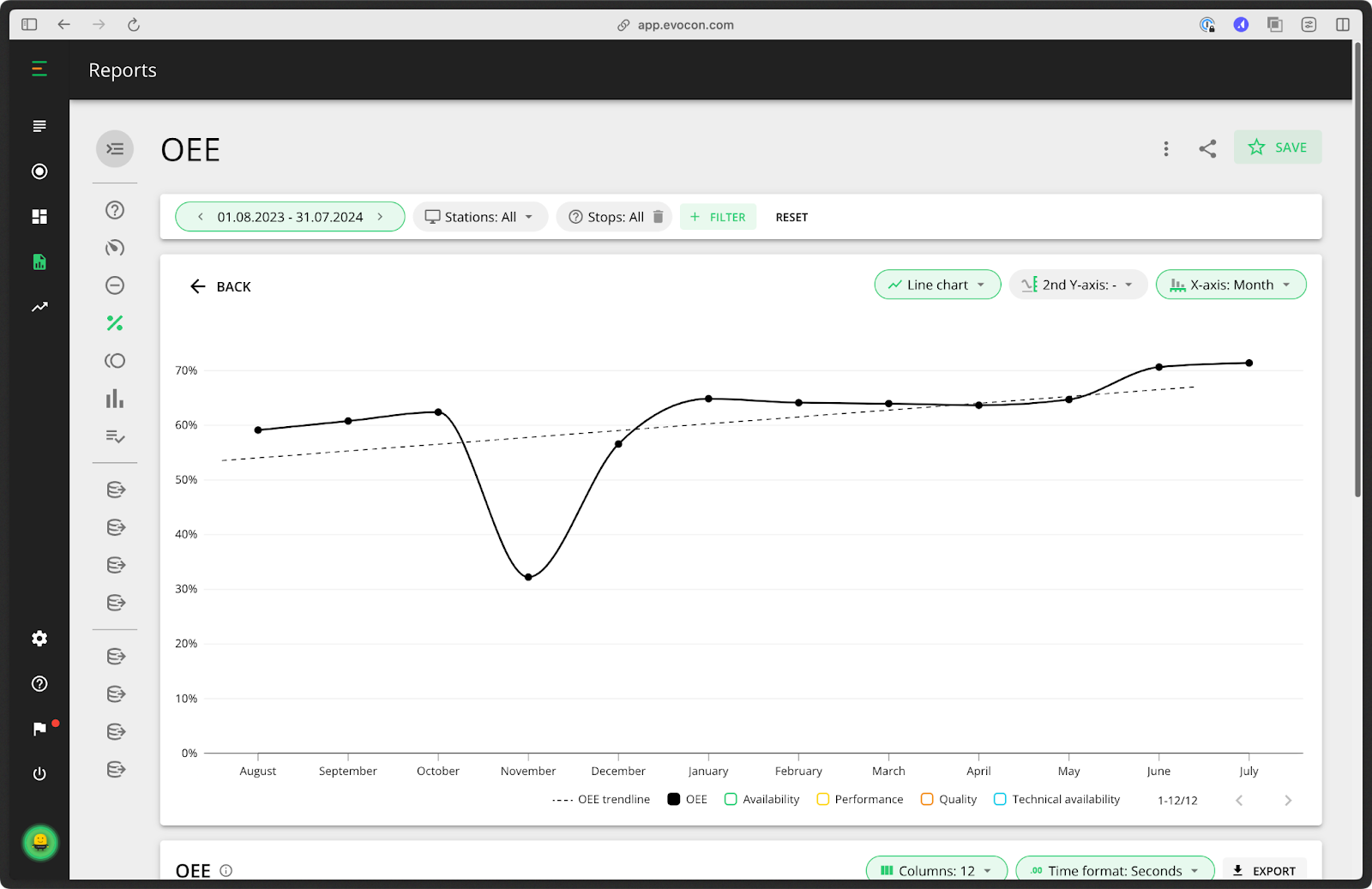
The high rate of commenting from shop floor operators has been crucial in helping Tecpap significantly improve their OEE. By effectively integrating Evocon into their daily routines, operators consistently provide reasons for machine stoppages.
This diligence is reflected in the graph below, which shows that only 0.19% of the downtime is unaccounted for. This low percentage demonstrates how operator engagement with the system has led to a more comprehensive understanding and management of production issues.
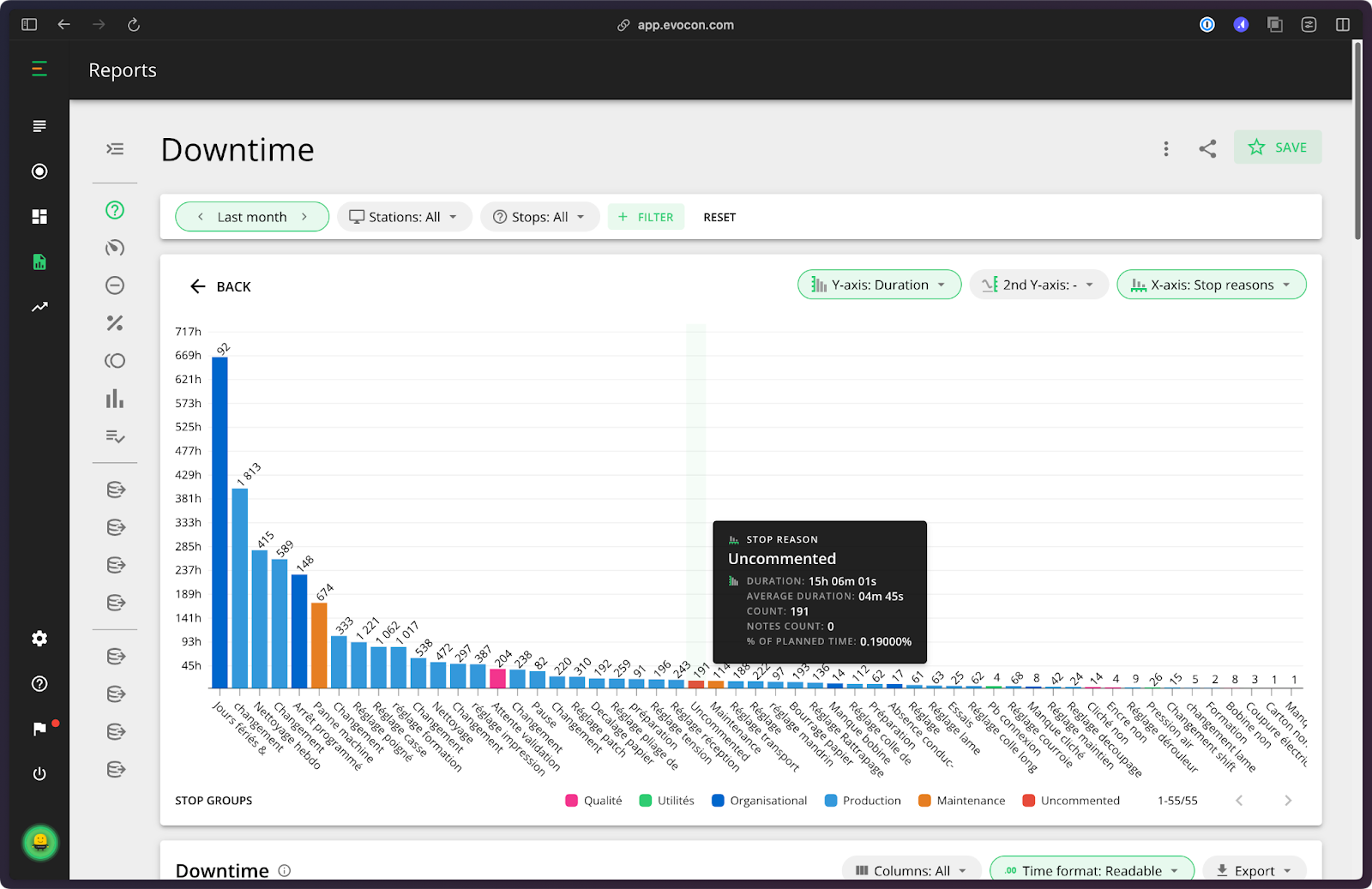
Ajdir
Ajdir’s OEE improvement is particularly noteworthy, rising by 20 percentage points, from 30% in February to 50% in July 2024, representing a 67% growth.
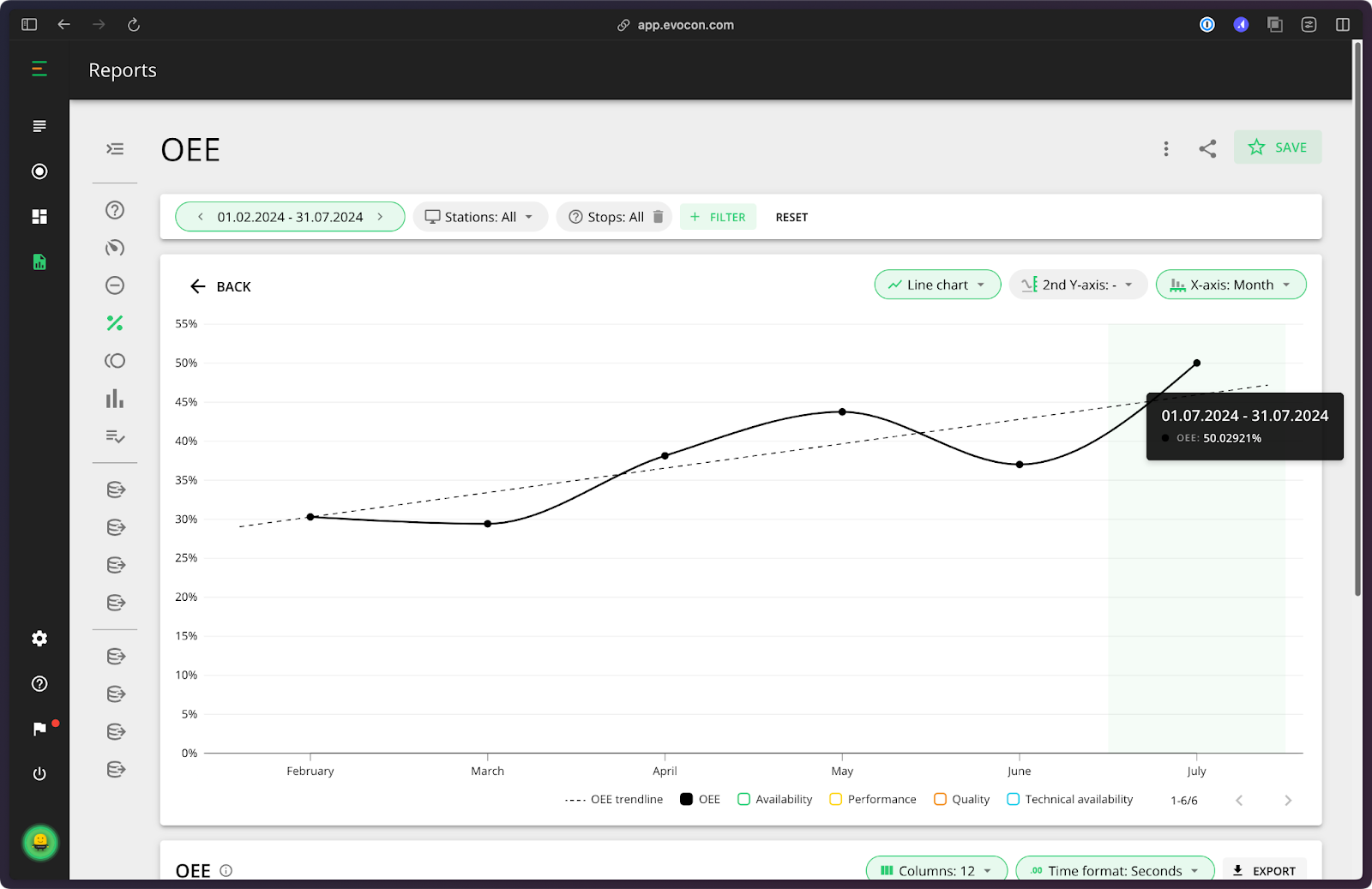
They’ve also seen their productive time increase from 25% to 40%, from February to July 2024.
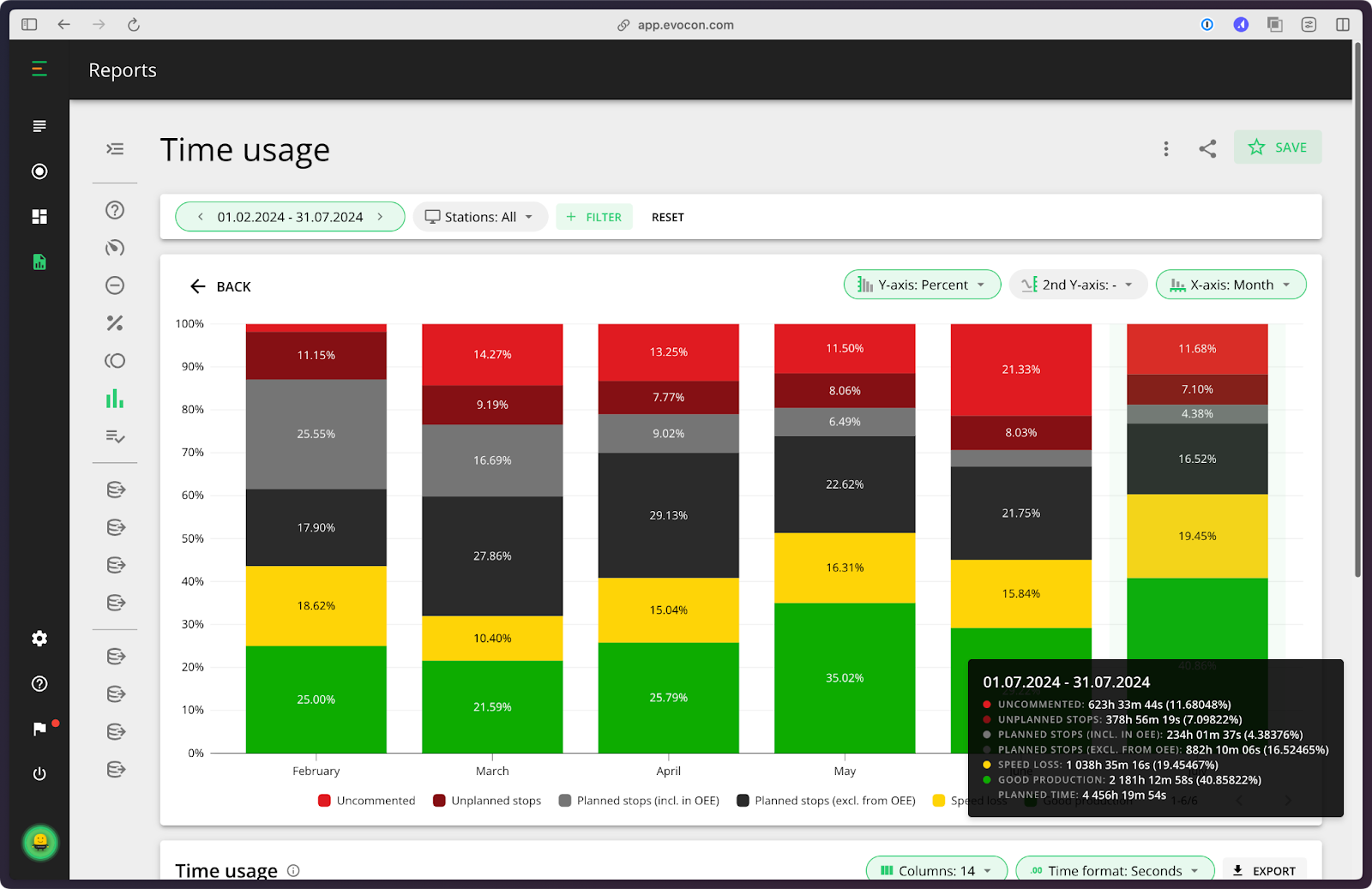
As mentioned in the section on Evocon implementation at Ajdir, a key priority for Ismail was understanding his company’s true potential. By leveraging Evocon, he was able to accurately assess actual production versus potential output, which enabled him to optimize resources and maximize factory efficiency.
For instance, in the graph below, we can see the quantity produced (in green), as well as the potential of what could have been produced when resources are fully optimized (in grey) for all station groups.
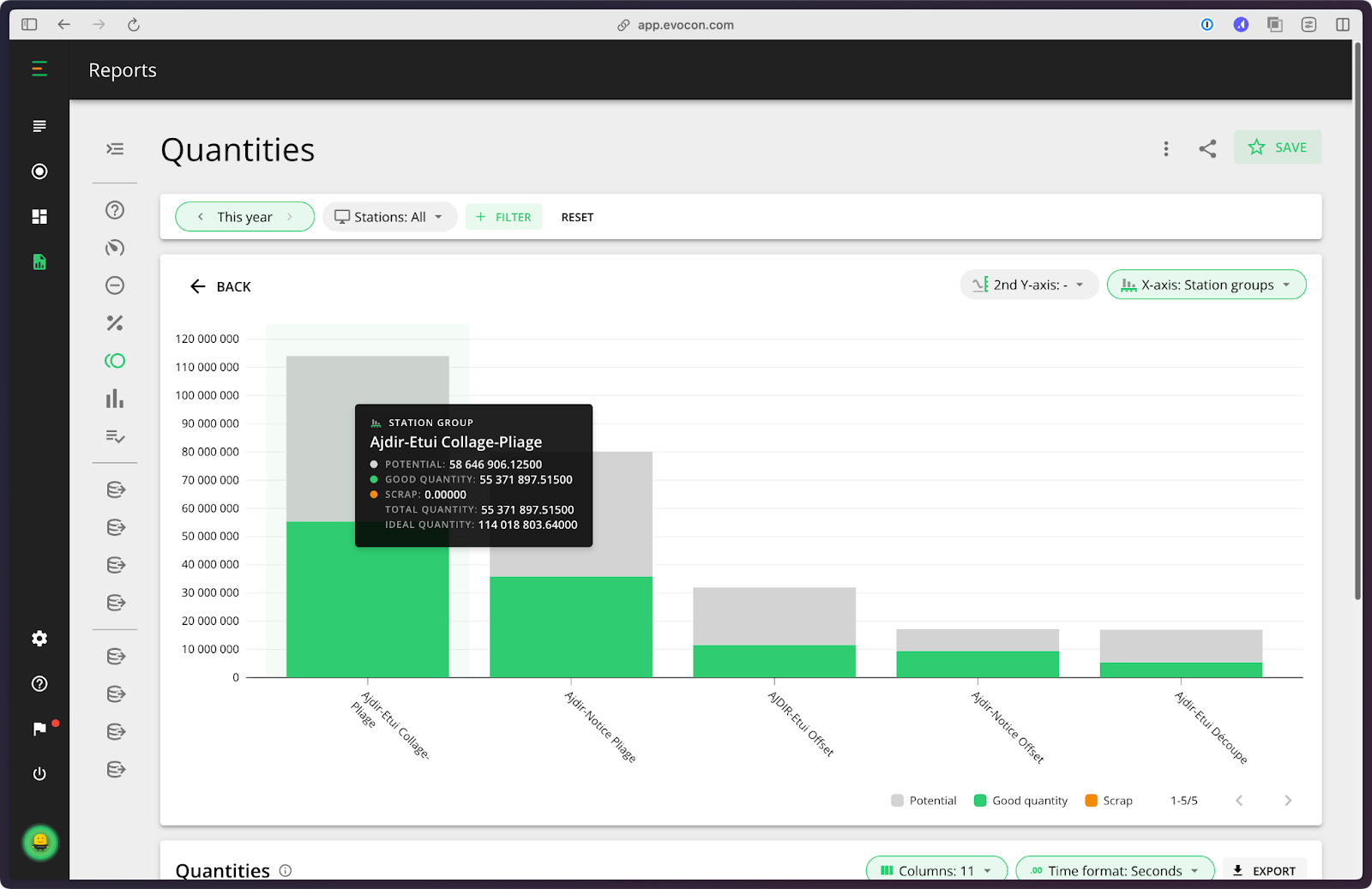
This data-driven insight will enable him to explore opportunities for expansion into new markets in the future. As an example, if Evocon data will show that Ajdir could increase production by 30% when operating at full capacity, Ismail will be able to confidently seek additional budget to expand resources — both machinery and personnel — to support further growth.
With Evocon he will be able to access the data needed to justify these investments, ensuring that any additional resources or shifts will be cost-effective and aligned with projected profits.
Dimyal
As the latest user of Evocon, Dimyal is primarily focused on gathering detailed information about their production processed and gaining a clear understanding of what is happening on the shop floor. This is the most important step that every manufacturer takes when begining to monitor production in real time.
What is more, early signs indicate that the system will be crucial in optimizing their processes further. For example, the operators are registered on the shift, they comment all stops, and complete the checklists – which are all encouraging signs of a successful adaption of the system and data gathering in full force.
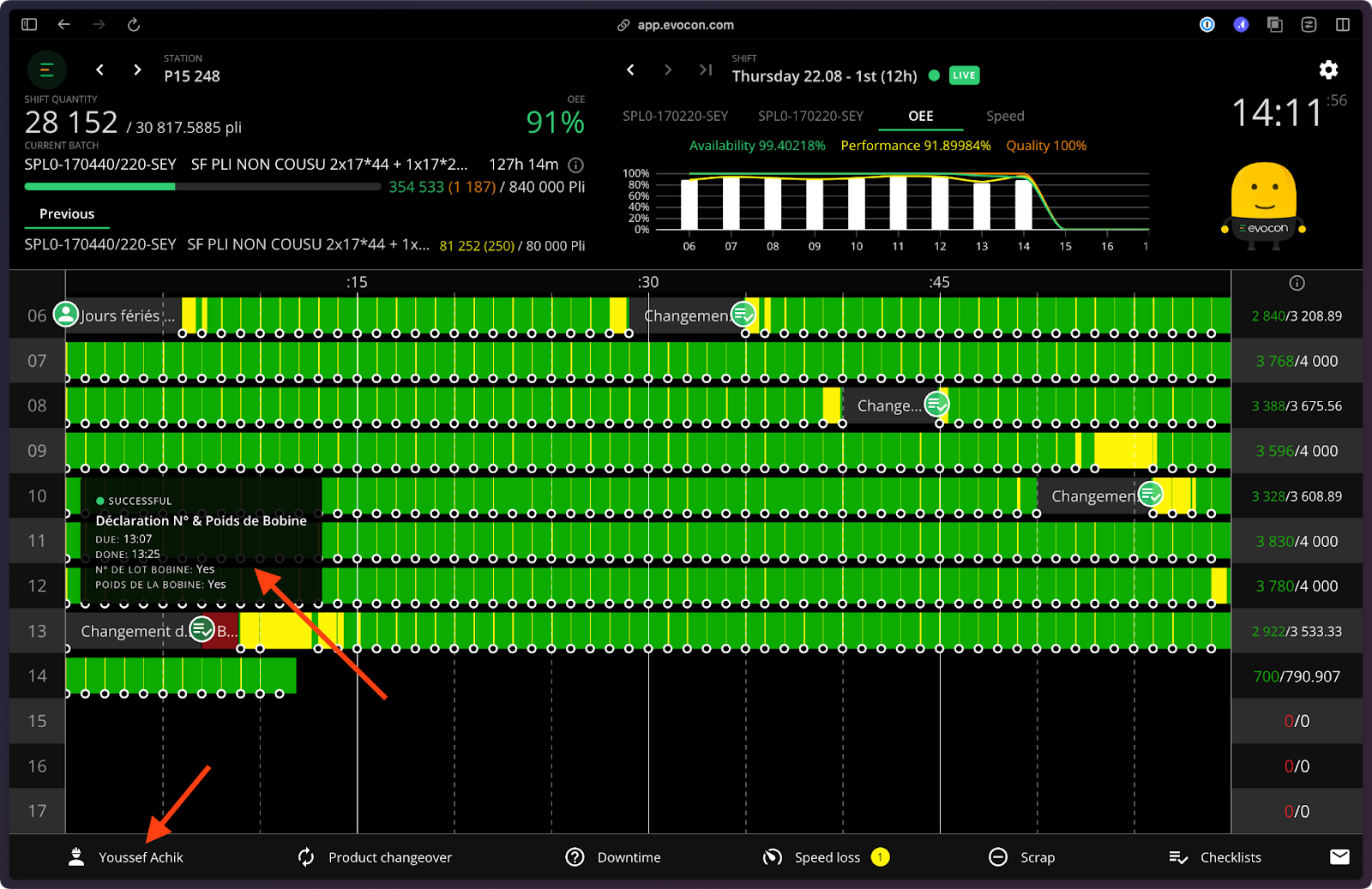
If Tecpap and Ajdir are examples to go by, we are sure Dimyal will follow through with excellent results.
Moving Forward with Evocon
IMMA Holding’s adoption of Evocon across Tecpap, Ajdir, and Dimyal shows their commitment to innovation and operational excellence. By monitoring their production lines in real time, they are all in a much better position to understand the true potential of their machines and factories. Though the operators on the floor were hesitant at first, through training and incentives, they have embraced Evocon and are now leveraging it effectively to improve processes.
With increased capacity, higher operator engagement, and consistently rising OEE scores, Tecpap, Ajdir, and Dimyal are fully committed to continuing their use of Evocon. The insights provided by Evocon data offer a clear view of their potential output, helping them determine when and where new machinery is needed. This clarity positions them to explore new markets and expand their business more rapidly.
As Evocon becomes an integral part of their daily operations, IMMA Holding is well-positioned to maintain its leadership in Morocco’s paper, packaging, and stationery industries, leveraging technology to drive growth and sustainability.