When aiming for higher efficiency in your production processes, you need to utilize a critical metric: machine availability. In this article, we take a closer look at the importance of machine availability. We cover how it’s calculated, explore the benefits, and analyze ways to improve your availability score. We also compare it to another closely related metric: machine uptime.
What is Machine Availability?
Machine availability is connected to how efficient and reliable your machinery is within the manufacturing process. Specifically, machine availability is the proportion of planned running time available for production. It’s an essential component in achieving high efficiency in production.
It’s also a critical pillar of OEE (Overall Equipment Effectiveness). A high availability percentage helps provide a healthy OEE score. A clear sign of efficiency is when machines produce output for a significant amount of their planned running time.
It’s important to know that the time the machine is planned to be available is referred to with different names with the same meaning. We are using planned running time, which can also be referred to as planned operating time, planned productive time, or potential production time, or any other combination of the same words for that matter.
The other part of machine availability is downtime. Just because a machine is planned to be available doesn’t mean it will be producing. It might need repairs or cleaning. Operators may be in a meeting, or a product changeover might be required.
How to Calculate Machine Availability
As discussed above, knowing machine availability requires knowing the machine’s planned running time. In most cases, this will be the scheduled shifts, with planned maintenance shutdowns or a period with no orders (lack of demand) removed.
We also need to identify all the recorded instances of downtime. This could be unplanned downtime, like a machine breakdown. It could also be planned downtime, like cleaning or a changeover.
Calculating availability can be done in these four simple steps:
- Identify and capture planned running time. This is the sum of your scheduled shifts minus planned shutdowns and lack of demand.
- Identify and capture total downtime.
- Downtime % = Total Downtime / Planned Productive Time x 100%
- Availability % = 100% – Downtime % OR Availability % = Run Time / Planned Productive Time x 100%
In the example below, the planned running time/planned productive time is 60 minutes. In that 60 minutes, 12 minutes is assigned to cleaning and therefore captured as downtime. The remaining 48 minutes can be used to calculate availability – in this case, resulting in 80%.
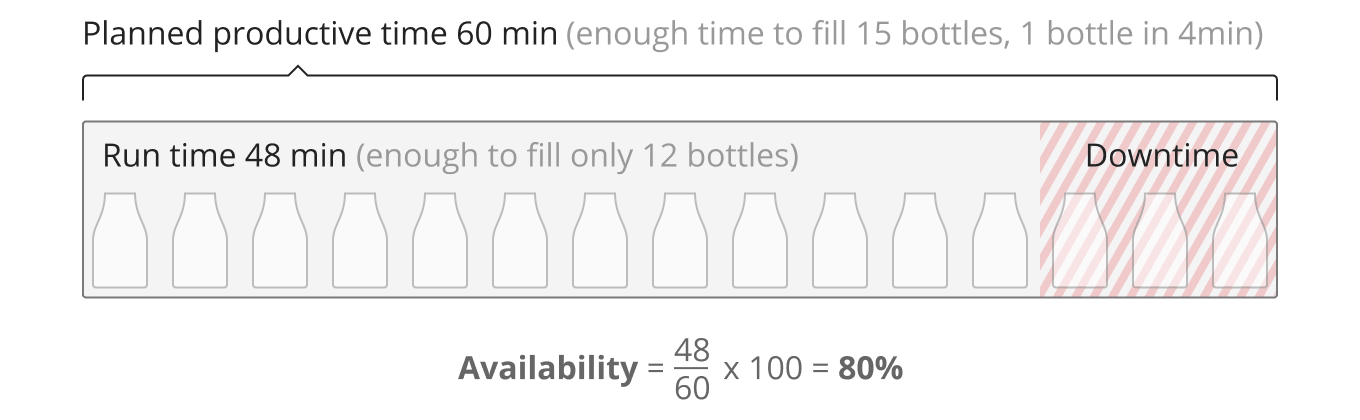
Case Study: TORM Metall
When the Estonian company TORM Metall found that one of their machines was running at only 35% capacity, they realized that change was necessary. TORM turned to production digitization to reduce machine downtime and track any inefficiencies in their production lines.
TORM used OEE software to track all their downtime and the reasons for it. With that data, they could understand the issues more clearly. From there, implementing solutions led the problematic machine to jump to 70% uptime, doubling its capacity.
“Digital technologies are advancing rapidly. If businesses do not take advantage of their opportunities and keep their finger on the pulse, then they’ll already be left behind tomorrow.”
TORM Metall
What is the Difference Between Machine Uptime and Machine Availability?
Machine uptime and availability are closely related. The terms are used interchangeably and often need to be clarified.
As mentioned, machine availability is the proportion of planned running time available for production.
On the other hand, machine uptime is simply the total time the machine is producing. In other words, uptime is a synonym for run time and is used to calculate availability.
From the calculation point of view, we can reflect the interconnectedness as follows:
Availability = Uptime/Planned running time*100%
Machine Uptime and Availability: Mr. Evocon at Work
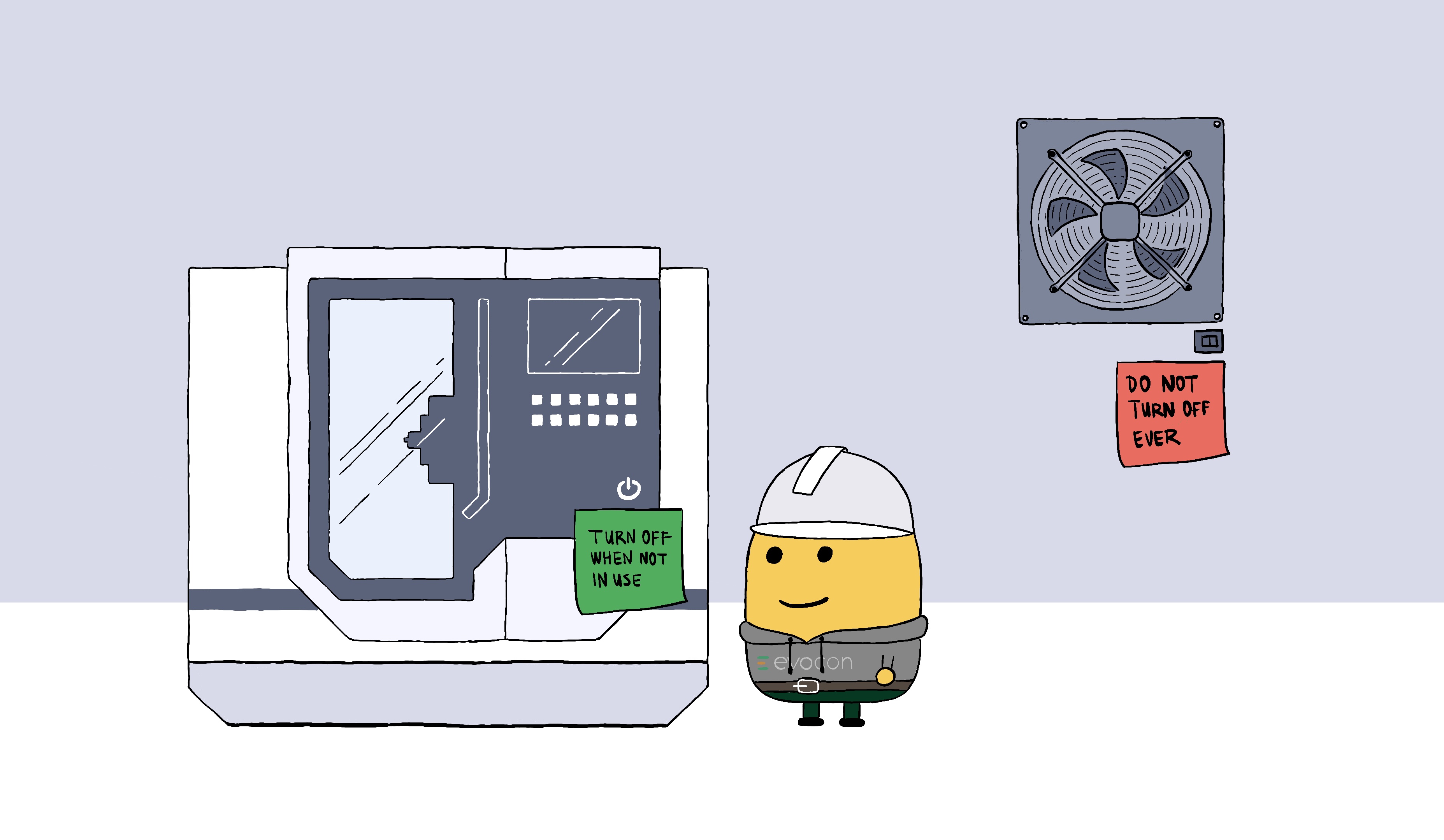
To help clarify the difference between uptime and availability further, let’s use the example of Mr. Evocon working a CNC machine. We’ll run through multiple examples, adding complexity to help understand how these metrics work together.
Example 1
In our first example, we look at the time when Mr. Evocon is actually operating the CNC machine. If Mr. Evocon were to run the machine without interruption for 1 hour, the CNC machine’s uptime would be 1 hour. In the same way, availability would be 100% as there was no downtime.
Example 2
If, for example, Mr. Evocon took a 12-minute unplanned stop for material resupply, this would be counted as downtime. Due to the break, uptime is now down to 48 minutes. And Availability = 48/60 x 100% = 80%
Example 3
If, instead, Mr. Evocon took a 12-minute paid rest break, although this is officially downtime (the machine isn’t running), the paid rest break is compulsory and is accounted for in the analysis as planned downtime (and excluded from OEE). Uptime would remain 48 minutes, but availability would be 100% because the break time is removed from the planned running time.
Let’s add more elements to this scenario to see it calculated altogether.
Example 4
This time, Mr. Evocon runs the machine for 1 hour, but he is taking a mandatory 5-minute break and spending 7 minutes getting new material.
Uptime (the time he is actually running the time machine) is still 48 minutes (60 – 7 – 5). But Availability % = [48/(60-5)] x 100% = 87%
Hopefully, these four examples illustrate how uptime and availability work together and at the same time that they are two different metrics.
When manufacturers start to monitor their production, their initial focus is on uptime, as it’s a much simpler metric to calculate. But once analysis deepens and downtime is captured, availability becomes the focus.
What’s causing the most downtime in your factory?
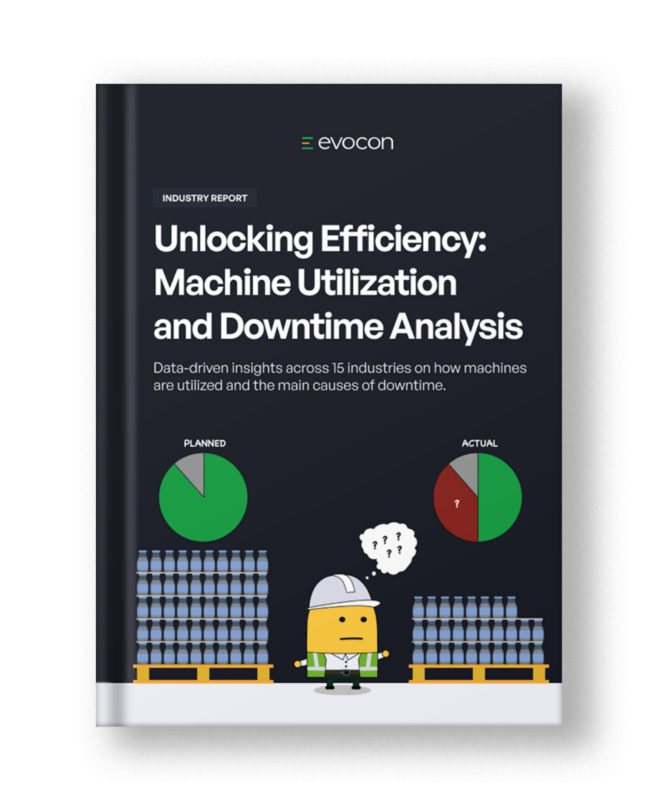
6 Factors That Affect Equipment Availability
Several factors can affect how much of a machine’s availability is spent working or producing. Issues that lower your availability score are labeled as downtime. There are two types of downtime in manufacturing. Some aspects, such as maintenance, are planned, and others are unexpected or unplanned. Below are some factors that can affect machine availability.
1. Uncommented stops
An exploration of our client’s hidden downtime factors showed that uncommented stops were one of the biggest reasons for downtime. An uncommented stop could be there for a couple of reasons: either an operator didn’t write down a reason for the stop, or the operator simply didn’t know the reason. Unfortunately, it’s impossible to make adjustments and improve when we don’t know the reason for a stop.
2. Product changeovers
While essential, changeovers lead to downtime, affecting the machine availability metric. Downtime will vary depending on the complexity of the change and the technique used by the worker performing it. Although we cannot prevent changeovers, methods can be implemented to streamline the process, increasing availability and simplifying the operator’s task. For example, analyze every operator’s methods, discover the fastest, most efficient model, and make it the standard procedure for everyone moving forward.
3. Equipment breakdown
Breakdowns cause significant reductions in machine availability. Not only do technicians have to diagnose and repair the machine, but they could experience a delay while waiting for new parts. A breakdown’s impact causes a ripple effect throughout the production environment. Firstly, the production flow is significantly hindered, but also reallocation of manpower might be required, and resource planning may be interrupted. Thus, regular maintenance and inspections are essential.
4. Unplanned maintenance/cleaning
Similar to a breakdown, unexpected maintenance can impact availability significantly. With uptime being reduced, the availability percentage will also decrease. Planning maintenance and cleaning in advance will decrease the likelihood of unplanned maintenance, therefore protecting availability.
5. Material shortage
There are a few things that can be streamlined on the shop floor to prevent waiting and delays in production, and inventory organization is one of them. Waiting for raw materials to continue production is unexpected and affects availability. Clear steps can be put in place to create a more efficient workplace, making not only raw material more accessible but also the manpower and vehicles needed to move it from point A to point B.
6. Unexpected stops
Other more exceptional factors could also lead to an unscheduled stop. For example, human errors and safety incidents can impact availability. Maintaining high levels of training alongside strict health and safety codes can go a long way in preventing too many unwanted stops. Unfortunately, even with the best planning and systems in place, some things are simply out of our control. Freak weather, power cuts, or natural disasters, although thankfully rare, can also play a role in reducing availability.
How to Improve Machine Availability
- Get rid of paper/install production monitoring software
- Implement downtime meetings (weekly/daily) strategy
- Preventative Measures (maintenance, quality checks, safety)
Get rid of paper/install production monitoring software
As you look to improve machine availability, manufacturing data collection software plays a crucial role in achieving that goal. It can empower both people and production through real-time data. Visualizing factory status means no surprises, letting you spot issues before they significantly affect machine availability.
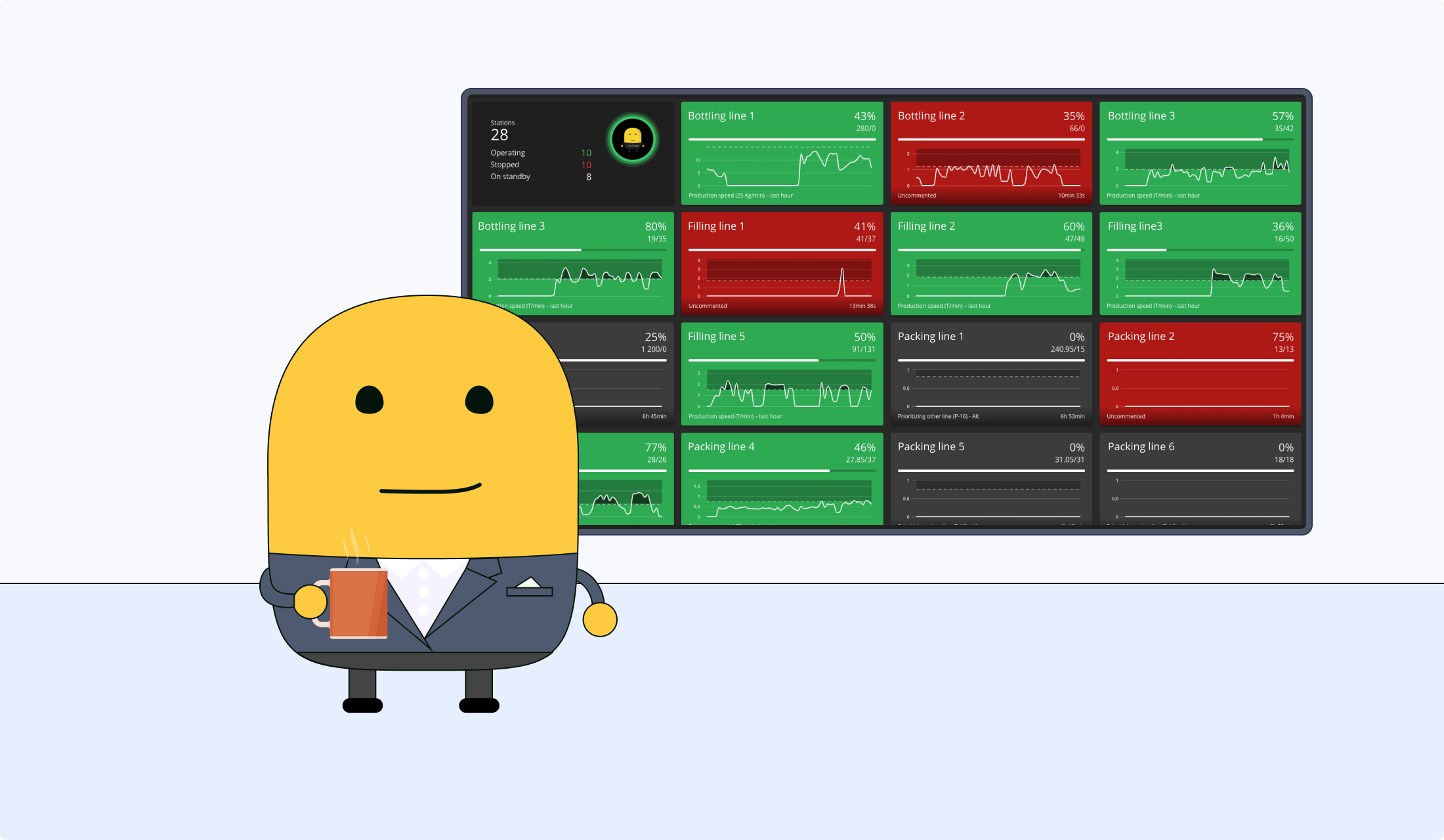
If you are still using a pen-and-paper data collection method, this is the first thing that needs to change. The method is simply too time-consuming, with too much room for error and subjectivity over what’s important to record and what’s not.
With a digital solution, the software records all downtime automatically, allowing you to categorize it. Once patterns emerge, you can act, implementing strategies to correct root causes. If the changes are successful, you should see a significant reduction in unplanned downtime and increase in availability.
Real-time OEE Software
Reduce unplanned downtime and increase machine availability with Evocon’s 30-day free trial.
Implement regular downtime meetings
Daily management is vital. Always having one eye on the floor means it’s easier to spot any new developments that can be reacted to quickly. Regular meetings (daily and/or weekly) give your team a voice and allow new information to spread clearly and quickly.
As discussed, some processes in manufacturing have an effect on planned running time, in turn limiting potential availability. Changeover, start-up, and planned maintenance times can all be reduced, bringing with it an improvement in machine availability. Setting a standard for all these processes is a great start to improving efficiency. Once you discover the optimum standard, training and enforcing that method throughout the workforce will reduce variance and consistently improve availability. Using continuous improvement techniques will help you discover how these processes can be optimized.
Preventative measures
Help the machine help you. Often, machines rely on an operator’s actions before they can do what they’ve been programmed to do. Ensuring workers are where they must be at the right time improves efficiency. How do you create greater efficiency in your teams? Creating a smarter floor layout is one way: it minimizes time spent walking and searching for materials or tools.
Ensure regular planned maintenance and equip maintenance teams with tools like Evocon’s Checklists to streamline daily routines. Regular, targeted maintenance ensures fewer breakdowns and fewer instances of unplanned maintenance.
OEE Software and Machine Availability
As we have shown, machine availability is vital to any efficient manufacturing process. At the heart of the matter, increased availability and uptime lead to increased efficiency, production, and, crucially, reduced cost.
Evocon’s production monitoring software enables you to monitor the status of your shifts in real time. Without waiting for something to go wrong before reacting, teams can handle any issues before they become problematic, increasing your machine availability metric.
With a real-time OEE dashboard, a user can create widgets to monitor the KPIs that are most important to them. In the case of machine availability, the downtime summary and production data widgets give you critical information if you’re looking to improve these metrics.
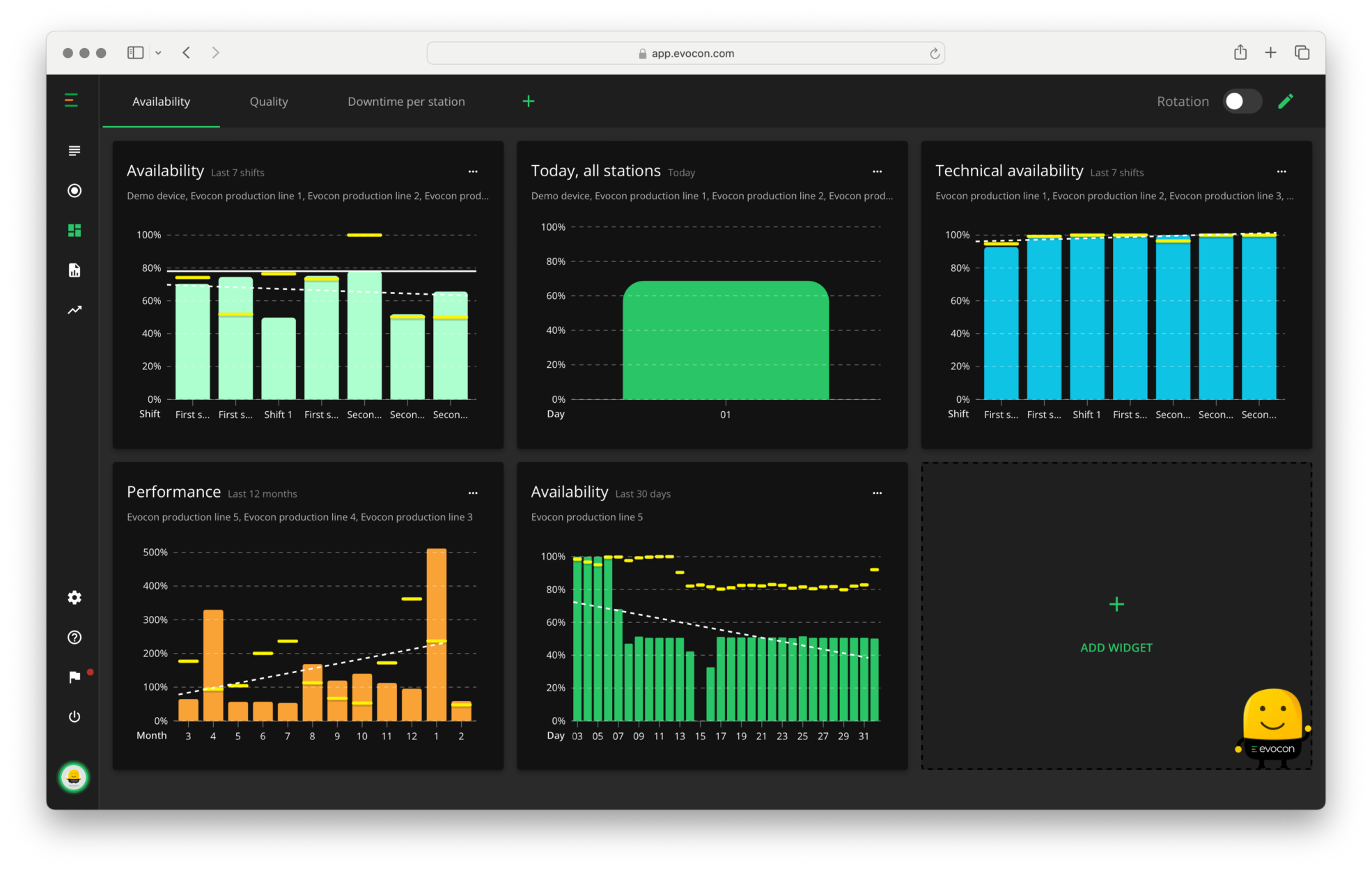
By understanding what went wrong, preventative measures become simple to execute. Spot patterns and trends with historical tracking and make better decisions about what process improvements to make.
In this time usage report, for example, production time is clearly divided between good production (green), slow production (yellow), and downtime (red). The report helps you see clearly if the changes you’re implementing are converting downtime into good production time. This is especially useful for analyzing longer time frames.
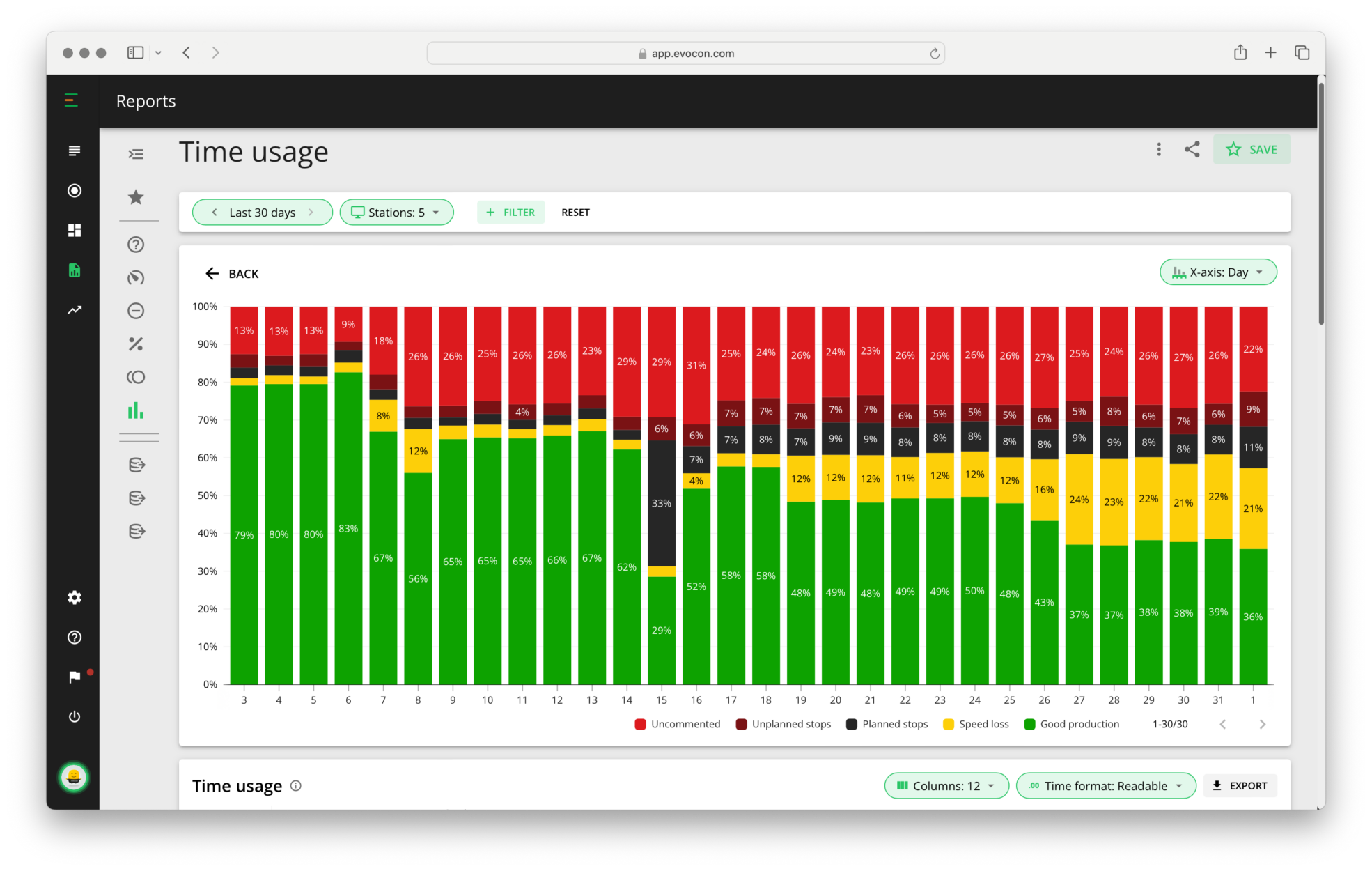
Even with the right tools, OEE software’s effectiveness relies on how it’s deployed. Creating a culture around OEE is vital for the whole team to get behind. Continuous improvement is a must. Feedback from every staff member should be encouraged. You should see failures as learning opportunities and a way of improving further. Small steps like these are vital in enhancing your machine availability score and overall equipment effectiveness.